Introduction to the Nuclear Power Castings & Forgings Market
The nuclear power castings and forgings sector lies at the heart of global energy security, delivering critical components that ensure reactor integrity, safety, and longevity. As nuclear operators pursue stringent performance criteria and life-extension programs, demand has surged for advanced alloys and precision forging techniques. Nuclear regulators worldwide enforce rigorous quality control and traceability standards, driving suppliers to adopt robust certification protocols and invest in specialized testing facilities. Meanwhile, aging reactor fleets in developed markets and the construction of new units in emerging economies are creating a dynamic environment characterized by evolving material requirements and complex project timelines. Through close collaboration with utilities and regulatory bodies, manufacturers are leveraging their metallurgical expertise to address corrosion resistance, fatigue life, and extreme temperature performance. This introduction sets the stage for an in-depth exploration of how technological advancements, policy shifts, and market segmentation are reshaping the competitive landscape for nuclear power castings and forgings.
Transformative Shifts Reshaping the Nuclear Castings & Forgings Landscape
Innovation in materials science and manufacturing processes is driving a transformation in the nuclear castings and forgings landscape. Advances in metallurgical research have yielded high-performance nickel alloys and novel titanium grades that deliver superior creep resistance and corrosion protection under harsh reactor conditions. Additive manufacturing is emerging as a complementary technique, enabling complex geometries and rapid prototyping while reducing lead times. At the same time, digital twins and Industry 4.0 platforms are enhancing predictive maintenance capabilities, allowing operators to forecast component lifespan and schedule timely replacements.
In parallel, the rise of small modular reactors and factory-built containment vessels is demanding scalable production methods and standardized components. Sustainability imperatives are steering the industry toward lower-emission manufacturing processes and circular supply chains. Regional supply chain diversification is also underway, with strategic partnerships forming across Asia, Europe, and North America to mitigate geopolitical risks and ensure continuous access to critical raw materials. Collectively, these shifts are fostering a more resilient, agile, and innovative market environment.
Cumulative Impact of United States Tariffs on 2025 Supply Chains
The introduction of United States tariffs scheduled for 2025 represents a significant inflection point for nuclear castings and forgings supply chains. The cumulative impact of these levies will drive up costs for imported nickel alloys, specialty steels, and precision forgings, prompting domestic manufacturers to scale up capacity and optimize production efficiency. As a result, utilities may face higher upfront equipment expenditures, although domestic reshoring efforts and tariff engineering could offset a portion of the added expense.
Strategic stockpiling of critical materials is becoming a priority for procurement teams, while long-term supplier agreements are being renegotiated to incorporate tariff pass-through clauses. Equally important, quality assurance processes will need to adapt to new traceability requirements, ensuring that domestically sourced forgings meet stringent regulatory benchmarks. In essence, the 2025 tariffs will accelerate the shift toward localized supply chains, incentivize capital investment in fabrication facilities, and alter global trade flows for key forging and casting materials.
Key Segmentation Insights Across Product, Material, Application and More
Segmentation analysis reveals that the market is dissected by product type into castings and forgings, reflecting differing fabrication techniques and end-use requirements. Material type segmentation encompasses nickel alloys-Hastelloy, Inconel, Monel-steel-Alloy Steel, Carbon Steel, Stainless Steel-and titanium-Pure Titanium, Titanium Alloys-underscoring the diversity of metallurgical solutions required under varying reactor conditions. Application segmentation covers heavy equipment components-Rotor Shafts, Turbine Blades-reactor vessels-Containment Vessels, Pressure Vessels-and seals and valves-Sealing Rings, Valve Bodies-each demanding precision engineering and rigorous quality control.
Further granularity emerges through manufacturing process segmentation, which includes closed die forging, die casting, open die forging, and sand casting, reflecting distinct production pathways and design constraints. End-use sector segmentation differentiates new nuclear plants from nuclear plant maintenance and nuclear plant upgrades, highlighting shifting investment focus across industry lifecycles. Component type segmentation stratifies large components like coolant pipes, medium components such as pump housings, and small components including nuts and bolts, illuminating varying logistical and technical considerations. Industry standards segmentation-ASME Standards, ASTM Standards, ISO Standards-drives compliance and interoperability, while supplier type segmentation contrasts integrated suppliers with specialized suppliers. Finally, technology integration segmentation differentiates advanced techniques-3D printing, additive manufacturing-from traditional techniques, emphasizing the role of digital and hybrid manufacturing methods.
This comprehensive research report categorizes the Nuclear Power Castings & Forgings market into clearly defined segments, providing a detailed analysis of emerging trends and precise revenue forecasts to support strategic decision-making.
- Product Type
- Material Type
- Application
- Manufacturing Process
- End-Use Sector
- Component Type
- Industry Standards
- Supplier Type
- Technology Integration
Key Regional Insights Driving Global Opportunities
Regional dynamics in the nuclear castings and forgings market vary significantly. In the Americas, strong incentives for domestic manufacturing and life-extension programs for existing reactors are bolstering demand for high-precision forgings and large-scale castings. Supply chain resilience is a focal point, with localized production capacity being expanded to counteract international tariff pressures.
In Europe, Middle East & Africa, stringent regulatory frameworks and ambitious decarbonization targets are driving investments in new reactor technologies and component upgrades. Collaborative frameworks between European fabrication specialists and emerging nuclear markets in the Middle East are fostering technology transfer and capacity building.
Asia-Pacific stands out as a high-growth region, with expanding nuclear fleets in China, India, and South Korea necessitating large-volume deliveries of both standard and custom engineered components. Investments in manufacturing automation and material innovation are creating cost efficiencies, while export strategies are aligning with broader Belt and Road Initiative objectives. Collectively, these regional insights underscore the importance of tailored supply chain strategies and adaptive manufacturing capabilities to meet diverse market requirements.
This comprehensive research report examines key regions that drive the evolution of the Nuclear Power Castings & Forgings market, offering deep insights into regional trends, growth factors, and industry developments that are influencing market performance.
- Americas
- Asia-Pacific
- Europe, Middle East & Africa
Key Company Insights and Competitive Dynamics
A review of leading players highlights a diverse competitive landscape. Alstom SA (now part of General Electric) brings extensive experience in heavy equipment components and reactor vessel design. AREVA SA (now part of Framatome) excels in advanced nickel alloy development and containment vessel fabrication. Bharat Heavy Electricals Limited (BHEL) leverages large-scale forging capabilities and deep expertise in steam generators and pressure vessels. China First Heavy Industries (CFHI) focuses on high-volume production and cost competitiveness, while Doosan Heavy Industries & Construction Co., Ltd. offers a vertically integrated model spanning casting, forging, and machining.
Electricité de France (EDF) contributes unique in-house capabilities for nuclear plant maintenance and life-extension projects, and Japan Steel Works, Ltd. is renowned for precision forgings in ultrahigh-strength steels. Larsen & Toubro Limited combines engineering, procurement, and construction services with specialized fabrication skills. Ontario Power Generation (OPG) emphasizes asset management and aftermarket support, and Rosatom State Atomic Energy Corporation provides a fully integrated end-to-end service offering from raw material sourcing to component delivery. Westinghouse Electric Company LLC rounds out the list with deep reactor technology expertise and global aftermarket solutions. Together, these companies shape market trends through continual investment in R&D, capacity expansion, and strategic partnerships.
This comprehensive research report delivers an in-depth overview of the principal market players in the Nuclear Power Castings & Forgings market, evaluating their market share, strategic initiatives, and competitive positioning to illuminate the factors shaping the competitive landscape.
- Alstom SA (now part of General Electric)
- AREVA SA (Now part of Framatome)
- Bharat Heavy Electricals Limited (BHEL)
- China First Heavy Industries (CFHI)
- Doosan Heavy Industries & Construction Co., Ltd.
- Electricité de France (EDF)
- Japan Steel Works, Ltd.
- Larsen & Toubro Limited
- Ontario Power Generation (OPG)
- Rosatom State Atomic Energy Corporation
- Westinghouse Electric Company LLC
Actionable Recommendations for Industry Leaders
Industry leaders should pursue a multi-pronged strategy to capture emerging opportunities. First, invest in advanced material research and digital manufacturing platforms to accelerate innovation cycles and reduce time-to-market. Second, establish strategic partnerships with raw material suppliers and component fabricators to diversify risk and secure preferential access to critical alloys. Third, optimize supply chain resilience by developing domestic capacity, implementing tariff engineering measures, and scouting alternative sourcing locations. Fourth, enhance workforce capabilities through targeted training programs in advanced forging techniques, quality assurance, and regulatory compliance. Fifth, adopt predictive maintenance frameworks and digital twin technologies to extend component lifecycles and drive cost efficiencies.
By executing these recommendations in concert, companies can position themselves to meet evolving performance requirements, adhere to stringent industry standards, and maintain competitive differentiation in a rapidly shifting environment.
Explore AI-driven insights for the Nuclear Power Castings & Forgings market with ResearchAI on our online platform, providing deeper, data-backed market analysis.
Ask ResearchAI anything
World's First Innovative Al for Market Research
Concluding Perspectives on Future-Ready Strategies
The nuclear power castings and forgings market stands at the intersection of technological innovation, regulatory rigor, and intricate supply chain dynamics. We have examined the drivers of material evolution, the implications of 2025 tariffs, and the nuanced segmentation that shapes demand across applications and regions. Leading companies are investing in advanced alloys, digital platforms, and localized production to stay ahead of policy shifts and quality imperatives. Ultimately, success will hinge on the ability to integrate cutting-edge manufacturing techniques with robust risk management and deep collaboration across the value chain.
This section provides a structured overview of the report, outlining key chapters and topics covered for easy reference in our Nuclear Power Castings & Forgings market comprehensive research report.
- Preface
- Research Methodology
- Executive Summary
- Market Overview
- Market Dynamics
- Market Insights
- Cumulative Impact of United States Tariffs 2025
- Nuclear Power Castings & Forgings Market, by Product Type
- Nuclear Power Castings & Forgings Market, by Material Type
- Nuclear Power Castings & Forgings Market, by Application
- Nuclear Power Castings & Forgings Market, by Manufacturing Process
- Nuclear Power Castings & Forgings Market, by End-Use Sector
- Nuclear Power Castings & Forgings Market, by Component Type
- Nuclear Power Castings & Forgings Market, by Industry Standards
- Nuclear Power Castings & Forgings Market, by Supplier Type
- Nuclear Power Castings & Forgings Market, by Technology Integration
- Americas Nuclear Power Castings & Forgings Market
- Asia-Pacific Nuclear Power Castings & Forgings Market
- Europe, Middle East & Africa Nuclear Power Castings & Forgings Market
- Competitive Landscape
- ResearchAI
- ResearchStatistics
- ResearchContacts
- ResearchArticles
- Appendix
- List of Figures [Total: 34]
- List of Tables [Total: 853 ]
Contact Ketan Rohom to Access the Full Market Research Report
To gain full access to the in-depth market research report and unlock tailored insights for strategic planning, contact Ketan Rohom, Associate Director, Sales & Marketing. Reach out today to secure your copy and drive informed decision-making in the nuclear power castings and forgings sector.
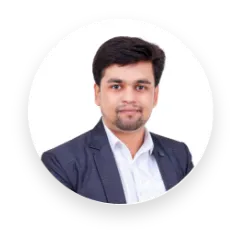
- When do I get the report?
- In what format does this report get delivered to me?
- How long has 360iResearch been around?
- What if I have a question about your reports?
- Can I share this report with my team?
- Can I use your research in my presentation?