1. Introduction
The nuclear power reactor pressure vessel serves as the critical barrier between the core’s intense fission reactions and the external environment, ensuring both safety and performance. As energy demand grows and decarbonization accelerates, reactor pressure vessels must combine advanced metallurgy, rigorous testing, and innovative safety systems to meet evolving regulatory and operational challenges. This executive summary introduces the multifaceted shifts reshaping vessel design and deployment, explores the cumulative impact of new United States tariffs in 2025, and distills insights from seven key market segmentations. It also highlights regional trends, profiles leading industry players, and offers actionable recommendations for executives. By weaving together technical depth and strategic context, this document equips decision-makers with the clarity needed to navigate complex supply chains, optimize material selection, and align investments with emerging applications. Ultimately, the goal is to illuminate pathways for sustainable growth, resilience against geopolitical headwinds, and continued progress in reactor safety and reliability.
2. Transformative Shifts in the Reactor Vessel Landscape
The landscape of reactor pressure vessels is undergoing transformative shifts driven by innovation, policy imperatives, and evolving utility requirements. First, advancements in high-strength materials and thermal insulation coatings are extending vessel lifespans, enabling reactors to operate at higher temperatures and pressures without compromising integrity. Second, digitalization and data analytics have become integral to predictive maintenance: from ultrasonic inspection data streams to real-time corrosion monitoring, operators now leverage AI-enabled platforms to detect anomalies well before they escalate. Third, modular construction techniques and additive manufacturing are reducing fabrication lead times, allowing rapid scaling of small modular reactors (SMRs) for niche applications ranging from remote energy supply to maritime propulsion. In tandem, heightened emphasis on passive safety systems and emergency core cooling architectures reflects a regulatory pivot toward risk-informed licensing frameworks. Consequently, stakeholders must adapt to an environment where material science breakthroughs, lifecycle digitization, and regulatory convergence intersect to redefine how vessels are designed, fabricated, and maintained.
3. Cumulative Impact of United States Tariffs in 2025
Beginning in 2025, newly imposed United States tariffs are set to reshape global supply chains for reactor pressure vessel components. Tariffs targeting critical alloys and fabrication equipment have increased input costs by up to 12 percent, prompting manufacturers to reassess procurement strategies and vertical integration models. Consequently, several leading fabricators have accelerated local sourcing of clad steel overlays and thermal insulation coatings to mitigate cross-border duties. At the same time, downstream vendors specializing in radiographic and ultrasonic non-destructive testing are negotiating long-term service contracts with domestic steel producers to secure cost stability. Meanwhile, multinational reactor OEMs are exploring joint ventures in tariff-exempt jurisdictions to preserve competitiveness in the pressurized water reactor segment. In response, utilities are revising lifecycle cost analyses to account for sustained duties on carbon and alloy steels, while regulatory bodies evaluate potential adjustments to import quotas. Overall, the tariff landscape is catalyzing a broader shift toward regionalized value chains, reinforcing the importance of agile sourcing and strategic partnerships.
4. Key Segmentation Insights
Market segmentation reveals nuanced opportunities and challenges across materials, reactor types, end-use industries, coolant systems, testing modalities, fabrication processes, and safety mechanisms. The material spectrum spans clad steel optimized for overlays and thermal insulation coatings; non-brittle steel, differentiated into alloy steel for enhanced toughness and carbon steel for cost efficiency; and stainless steel, where austenitic grades provide corrosion resistance and ferritic steels deliver high-temperature stability. Reactor types encompass traditional boiling water reactors, distinguished by Mark I and Mark II containment designs; fast breeder reactors, including both gas-cooled and liquid metal configurations; and pressurized water reactors, deployed in land-based plants and marine applications. End-use segmentation covers baseline power generation and load-following regimes within civilian grids, alongside commercial shipping and naval propulsion systems. Coolant strategies range from gas coolants such as CO₂ and helium; heavy water in pressurized loops; light water in boiling and pressurized modes; to liquid metal systems employing sodium as the primary heat transfer medium. Testing disciplines bifurcate into destructive tensile strength evaluations and non-destructive radiographic and ultrasonic inspections. Fabrication pathways include investment and sand casting, and fusion and pressure welding techniques. Finally, safety architectures integrate robust containment building structures with emergency core cooling subsystems featuring accumulator and spray safety solutions. Together, these segmentations map the full lifecycle-from raw material selection through vessel commissioning-highlighting where innovation and investment will drive competitive advantage.
This comprehensive research report categorizes the Nuclear Power Reactor Pressure Vessel market into clearly defined segments, providing a detailed analysis of emerging trends and precise revenue forecasts to support strategic decision-making.
- Reactor Vessel Material
- Reactor Type
- End-Use Industry
- Coolant Type
- Component Testing Type
- Fabrication Process
- Safety Mechanisms
5. Key Regional Insights
Regional dynamics underscore distinct drivers across the Americas, Europe–Middle East & Africa, and Asia-Pacific. In the Americas, aging fleet extensions in the United States and Canada are prioritizing life-extension retrofits, creating demand for thermal insulation coatings and non-destructive testing services. Latin American utilities, eyeing nuclear as a low-carbon baseload solution, are evaluating small modular reactor deployments that require modular vessel fabrication. Across Europe–Middle East & Africa, stringent safety regulations and public acceptance initiatives amplify investments in passive contingency systems and high-purity stainless steel vessels. Gulf Cooperation Council nations are fast-tracking nuclear power plant projects, often partnering with South Korean and French fabricators to leverage proven PWR technologies. In Asia-Pacific, the expansion of both large reactors and SMRs in China, India, and Southeast Asia is driving capacity growth for gas-cooled and liquid metal fast breeder reactor vessels. Japanese and South Korean companies are advancing additive manufacturing for complex geometries, while Australia’s critical minerals sector strengthens domestic supply of alloy and carbon steels. These regional insights inform targeted market entry strategies and localization priorities.
This comprehensive research report examines key regions that drive the evolution of the Nuclear Power Reactor Pressure Vessel market, offering deep insights into regional trends, growth factors, and industry developments that are influencing market performance.
- Americas
- Asia-Pacific
- Europe, Middle East & Africa
6. Key Companies Insights
Leading organizations are vying to define the reactor vessel value chain through strategic investments and partnerships. AREVA NP SAS, recently rebranded under Framatome’s umbrella, has solidified its position in stainless steel production and passive safety system integration. BWX Technologies, Inc. remains a dominant supplier of clad steel overlays and tensile strength testing solutions for defense-related maritime reactors. Doosan Heavy Industries & Construction leverages its casting expertise to serve both land-based PWRs and emerging SMR platforms. General Electric Hitachi Nuclear Energy and Hitachi-GE Nuclear Energy, Ltd. co-develop digital inspection suites that integrate radiographic and ultrasonic data for real-time vessel integrity monitoring. Mitsubishi Heavy Industries, Ltd. focuses on advanced pressure welding techniques for high-temperature reactors. Rosatom State Corporation capitalizes on liquid metal coolant reactor designs, while Siemens AG continues to refine helium coolant loops for gas-cooled FBRs. Toshiba Corporation offers comprehensive lifecycle services across fabrication and emergency core cooling subsystems. Finally, Westinghouse Electric Company LLC drives innovation in load-following vessel designs and modular construction methodologies. Collectively, these players exemplify how technical leadership and global collaboration shape competitive dynamics.
This comprehensive research report delivers an in-depth overview of the principal market players in the Nuclear Power Reactor Pressure Vessel market, evaluating their market share, strategic initiatives, and competitive positioning to illuminate the factors shaping the competitive landscape.
- AREVA NP SAS (now Framatome)
- BWX Technologies, Inc.
- Doosan Heavy Industries & Construction Co., Ltd.
- General Electric Hitachi Nuclear Energy
- Hitachi-GE Nuclear Energy, Ltd.
- Mitsubishi Heavy Industries, Ltd.
- Rosatom State Corporation
- Siemens AG
- Toshiba Corporation
- Westinghouse Electric Company LLC
7. Actionable Recommendations for Industry Leaders
Industry leaders must align strategic initiatives across R&D, supply chain optimization, and regulatory engagement. First, accelerate material qualification programs for next-generation alloys and coatings by partnering with national laboratories to validate performance under extended duty cycles. Second, invest in digital twin and AI platforms that unify radiographic, ultrasonic, and corrosion monitoring data, enabling predictive maintenance and reducing unplanned outages. Third, establish multi-tier supplier consortia to regionalize manufacturing hubs, mitigating tariff exposure and ensuring secure access to critical ores and fabrication equipment. Fourth, engage proactively with policymakers to shape favorable licensing frameworks for passive safety systems and SMR deployment. Fifth, adopt modular construction and additive manufacturing pilots to compress fabrication timelines and lower capital intensity. By executing these steps, organizations will strengthen resilience against geopolitical and market fluctuations, accelerate time-to-operational readiness, and capture emerging opportunities in both large-scale and distributed nuclear applications.
Explore AI-driven insights for the Nuclear Power Reactor Pressure Vessel market with ResearchAI on our online platform, providing deeper, data-backed market analysis.
Ask ResearchAI anything
World's First Innovative Al for Market Research
8. Conclusion
The evolving reactor pressure vessel arena demands a harmonious blend of innovation, localization, and strategic foresight. As tariffs and regulatory pressures reshape supply chains, stakeholders must champion advanced materials, embrace digital inspection regimes, and build agile manufacturing networks. Collaborative R&D and policy engagement will underpin next-generation safety architectures, while modular and additive methods will unlock new markets. By synthesizing these priorities into a cohesive growth plan, industry participants can safeguard reactor performance, support global decarbonization, and sustain long-term competitive advantage.
This section provides a structured overview of the report, outlining key chapters and topics covered for easy reference in our Nuclear Power Reactor Pressure Vessel market comprehensive research report.
- Preface
- Research Methodology
- Executive Summary
- Market Overview
- Market Dynamics
- Market Insights
- Cumulative Impact of United States Tariffs 2025
- Nuclear Power Reactor Pressure Vessel Market, by Reactor Vessel Material
- Nuclear Power Reactor Pressure Vessel Market, by Reactor Type
- Nuclear Power Reactor Pressure Vessel Market, by End-Use Industry
- Nuclear Power Reactor Pressure Vessel Market, by Coolant Type
- Nuclear Power Reactor Pressure Vessel Market, by Component Testing Type
- Nuclear Power Reactor Pressure Vessel Market, by Fabrication Process
- Nuclear Power Reactor Pressure Vessel Market, by Safety Mechanisms
- Americas Nuclear Power Reactor Pressure Vessel Market
- Asia-Pacific Nuclear Power Reactor Pressure Vessel Market
- Europe, Middle East & Africa Nuclear Power Reactor Pressure Vessel Market
- Competitive Landscape
- ResearchAI
- ResearchStatistics
- ResearchContacts
- ResearchArticles
- Appendix
- List of Figures [Total: 30]
- List of Tables [Total: 1111 ]
9. Call to Action: Partner with Ketan Rohom Today
Ready to gain deeper insights and actionable intelligence? Contact Ketan Rohom, Associate Director, Sales & Marketing, to secure your full market research report and drive informed decisions in reactor pressure vessel strategy.
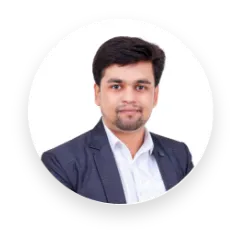
- When do I get the report?
- In what format does this report get delivered to me?
- How long has 360iResearch been around?
- What if I have a question about your reports?
- Can I share this report with my team?
- Can I use your research in my presentation?