Introduction to High-Performance Opposed-Piston Fixed Calipers
The evolution of automotive braking systems has placed opposed-piston fixed calipers at the forefront of high-performance safety and control. By integrating two pistons positioned on opposite sides of the brake rotor, these fixed calipers deliver more uniform pressure distribution, reduced flex, and heightened pedal feel compared to conventional floating-caliper designs. Their robust architecture ensures that each piston advances in perfect symmetry, squeezing the rotor evenly and transforming kinetic energy into heat with maximum efficiency.
In modern applications, opposed-piston fixed calipers have become synonymous with elite braking performance, finding homes in premium passenger vehicles, commercial fleets, sport motorcycles, and competitive racing platforms. Their rise is fueled by advancements in materials science, precision manufacturing, and real-time vehicle dynamics control. Furthermore, regulatory mandates on stopping distances and vehicle safety ratings have spurred greater adoption among original equipment manufacturers and aftermarket specialists alike.
As global mobility shifts toward electrification, autonomous driving, and lightweight construction, braking technologies must adapt to new force profiles, energy recovery needs, and system redundancies. With greater scrutiny on reliability under stress and minimal maintenance demands, opposed-piston fixed calipers are uniquely positioned to meet these rigorous standards. This executive summary examines the forces reshaping this market, dissects critical segmentation and regional trends, and offers actionable insights for stakeholders aiming to capitalize on emerging opportunities.
Transformative Shifts Reshaping the Braking Technology Landscape
The braking landscape is undergoing transformative shifts driven by technological breakthroughs, regulatory pressures, and evolving consumer expectations. First, lightweight materials such as carbon fiber composites and forged aluminum alloys are replacing traditional steel calipers, reducing unsprung mass and enhancing thermal dissipation. Simultaneously, additive manufacturing techniques permit complex internal channels and cooling fins that optimize fluid flow and heat exchange.
Moreover, integration with electronic stability systems and brake-by-wire architectures is redefining calibration strategies. These systems demand calipers with precise response characteristics and minimal hysteresis, making opposed-piston designs a natural fit. Autonomous driving initiatives further intensify braking requirements, requiring ultra-fast actuation and redundancy to safeguard passengers in unforeseen scenarios.
Environmental regulations targeting particulate emissions have also prompted the adoption of low-dust friction materials and closed-circuit brake dust capture mechanisms. These factors elevate the importance of caliper precision, seal integrity, and material compatibility. Lastly, competitive dynamics in motorsport trickle down premium performance enhancements-multi-piston monobloc designs, ceramic coatings, and hybrid material composites-into mainstream applications.
Collectively, these shifts are forging a new era in braking technology where reliability, weight savings, electronic synergy, and ecological stewardship converge.
Cumulative Impact of 2025 United States Tariffs on Brake Component Sourcing
In 2025, newly imposed tariffs on aluminum sheets, steel billets, titanium ingots, and composite fabric imports into the United States have exerted upward pressure on raw material costs. Aluminum extrusion suppliers and forged component manufacturers have adjusted pricing models to offset higher import duties, leading to a cascade effect throughout the supply chain. Fixed-caliper producers reliant on die-cast aluminum have seen their margins tighten, prompting some to reshore casting operations or source from duty-exempt trade partners.
Composite material import duties have similarly impacted carbon fiber and glass fiber caliper bodies, pushing manufacturers to explore domestic carbon reinforcement fabrication or substitute lower-cost glass fiber composites for select performance tiers. Titanium piston producers face a dual challenge: elevated tariffs and compressed inventories, which have extended lead times and disrupted just-in-time assembly lines.
These cumulative effects have driven original equipment manufacturers to renegotiate long-term contracts, seek tariff exclusions, and diversify suppliers across North America, Europe, and Asia. To manage cost volatility, several integrators are locking in hedged material agreements and investing in in-house machining capacity to reduce dependency on external cast or forged components. The net result is a reconfiguration of sourcing strategies with greater emphasis on local content and supply chain resilience.
In-Depth Segmentation Insights Across Materials, Vehicles, and Industries
Segmentation analysis reveals a multifaceted market structure. Based on material composition, aluminum remains dominant, with die-cast and forged variants each catering to different performance and cost requirements. Composite materials-encompassing carbon fiber composites for extreme heat resistance and glass fiber composites for balanced strength-are rapidly gaining share in premium applications. Steel alternatives continue to serve cost-sensitive and heavy-duty segments, especially through alloy, carbon, and stainless variants, while titanium and titanium alloy options address ultra-lightweight and high-corrosion scenarios.
Vehicle type segmentation highlights that fixed calipers serve diverse platforms. Heavy-duty trucks and light commercial vehicles demand durable steel and aluminum solutions optimized for load-bearing stability, while cruiser and sports motorcycles prioritize compact, high-precision calipers for swift engagement. Passenger vehicle applications span hatchbacks, sedans, and SUVs, each with unique design constraints influenced by wheel size, weight distribution, and thermal load profiles.
From an end-user industry perspective, aftermarket upgrades leverage specialized high-performance calipers through retail distributors and service centres, whereas automobile OEMs rely on durable economy brand systems or luxury brand custom assemblies. Racing and performance sectors, from amateur racing concerns to professional teams, push boundaries with bespoke multi-piston monobloc designs.
Technology segmentation distinguishes brake assist systems, advanced hydraulic architectures, and purely mechanical linkages, each dictating caliper integration complexity. Application type further refines this landscape into aftermarket upgrades, motorsport-grade platforms, and direct OEM installations. Caliper design choices between fixed and floating units intertwine with braking performance classifications-high-performance versus standard-while production processes including casting and forging underpin cost, tolerance, and scalability considerations. Finally, customer segments split between B2B automotive integrators and individual consumers drive customization levels and service models.
This comprehensive research report categorizes the Opposed-Piston Fixed Calipers market into clearly defined segments, providing a detailed analysis of emerging trends and precise revenue forecasts to support strategic decision-making.
- Material Composition
- Vehicle Type
- End-User Industry
- Technology
- Application Type
- Caliper Design
- Braking Performance
- Production Process
- Customer Segment
Key Regional Insights Driving Fixed Caliper Adoption
Regional dynamics underscore distinct demand drivers and adoption curves. In the Americas, robust passenger vehicle sales and a vibrant aftermarket culture fuel steady uptake of cost-efficient aluminum fixed calipers, while premium performance niches expand around motorsport and enthusiast communities. Regulatory incentives for domestic manufacturing amplify local sourcing initiatives, aligning with tariff mitigation strategies.
Europe, Middle East & Africa feature stringent safety and environmental regulations that accelerate deployment of low-emission braking systems. Premium OEMs headquartered in Germany, Italy, and the United Kingdom drive innovation through partnerships with specialized caliper manufacturers. The region’s mature racing circuits maintain high demand for carbon-ceramic rotor pairings and titanium-based calipers, while emerging markets in the Middle East embrace luxury and performance vehicles.
Asia-Pacific encapsulates a broad spectrum of market maturity, from established automotive hubs in Japan and South Korea-where leading companies invest heavily in in-house R&D-to rapidly growing manufacturing centers in China and India. Here, lightweight aluminum fixed calipers dominate OEM fitments, yet rising local motorsport scenes and aftermarket penetration encourage the adoption of composite material designs. Trade agreements within ASEAN further stimulate cross-border collaboration and supply chain diversification.
This comprehensive research report examines key regions that drive the evolution of the Opposed-Piston Fixed Calipers market, offering deep insights into regional trends, growth factors, and industry developments that are influencing market performance.
- Americas
- Asia-Pacific
- Europe, Middle East & Africa
Competitive Landscape and Leading Manufacturer Profiles
Leading players are shaping the competitive landscape through relentless innovation, strategic alliances, and integrated supply chain models. Aisin Seiki Co., Ltd. differentiates with proprietary hydraulic channel designs and tight OEM partnerships, while Akebono Brake Industry Co., Ltd. leverages advanced friction material formulations for reduced dust and noise. Alcon Components Ltd. focuses on motorsport heritage, delivering bespoke multi-piston monobloc calipers to professional racing teams.
AP Racing Ltd. continues to pioneer ceramic piston coatings that enhance thermal management, and BOSCH Mobility Solutions integrates brake-by-wire compatibility into caliper modules for next-generation autonomous platforms. Brembo S.p.A. sustains market leadership through global manufacturing footprints and lightweight forged components. Hitachi Astemo Ltd. and Mando Corporation invest in combined brake and stability control systems, elevating caliper precision through mechatronic synergy.
Nissin Kogyo Co., Ltd. targets two-wheeler markets with compact high-performance designs, while StopTech LLC emphasizes aftermarket performance upgrades with direct-fit kits. TRW Automotive Holdings Corp. offers scalable fixed caliper platforms across mass-market and luxury segments. Wilwood Engineering Inc. capitalizes on custom aluminum fabrication and rapid prototyping, and ZF Friedrichshafen AG extends its reach through integrated chassis systems that incorporate fixed calipers into holistic vehicle dynamics packages.
This comprehensive research report delivers an in-depth overview of the principal market players in the Opposed-Piston Fixed Calipers market, evaluating their market share, strategic initiatives, and competitive positioning to illuminate the factors shaping the competitive landscape.
- Aisin Seiki Co., Ltd.
- Akebono Brake Industry Co., Ltd.
- Alcon Components Ltd.
- AP Racing Ltd.
- BOSCH Mobility Solutions
- Brembo S.p.A.
- Hitachi Astemo Ltd.
- Mando Corporation
- Nissin Kogyo Co., Ltd.
- StopTech LLC
- TRW Automotive Holdings Corp.
- Wilwood Engineering Inc.
- ZF Friedrichshafen AG
Actionable Recommendations for Industry Leaders to Enhance Competitiveness
Industry leaders must act decisively to capture emerging growth opportunities. First, diversify material sourcing by establishing partnerships with domestic aluminum and composite fabricators to mitigate tariff exposure and ensure continuity of supply. Invest in additive manufacturing capabilities to accelerate prototyping and unlock complex cooling geometries that elevate caliper performance.
Second, deepen collaboration with vehicle OEMs and mobility service providers to co-develop brake-by-wire and predictive maintenance features, positioning fixed calipers as integral modules within connected vehicle architectures. Third, expand regional footprints in high-growth Asia-Pacific markets by forging joint ventures with local assemblers and leveraging trade incentives to reduce production costs.
Fourth, prioritize sustainable practices by adopting eco-friendly friction materials and recyclable caliper alloys, aligning product portfolios with evolving environmental regulations. Fifth, empower go-to-market agility through modular design platforms that address diverse vehicle types-from heavy-duty trucks to sports motorcycles-while streamlining customization processes for B2B and individual end users.
Lastly, monitor tariff developments and invest in supply chain visibility tools that enable real-time risk assessment, ensuring rapid response to policy shifts. By combining material innovation, strategic partnerships, and operational resilience, companies can strengthen competitive positioning in the dynamic fixed-caliper arena.
Explore AI-driven insights for the Opposed-Piston Fixed Calipers market with ResearchAI on our online platform, providing deeper, data-backed market analysis.
Ask ResearchAI anything
World's First Innovative Al for Market Research
Conclusion and Strategic Imperatives for Braking Technology Stakeholders
Opposed-piston fixed calipers are poised to play an increasingly critical role in next-generation braking systems, driven by the confluence of advanced materials, electronic integration, and regulatory imperatives. The shifting landscape-characterized by tariff realignments and regional growth differentials-demands a strategic approach that balances cost efficiency with cutting-edge performance enhancements.
Manufacturers that embrace diversified sourcing strategies, invest in innovative production processes, and forge deep technical collaborations with vehicle OEMs will secure long-term advantage. At the same time, a keen focus on sustainable materials and digital manufacturing practices will address the twin pressures of environmental compliance and evolving consumer preferences.
As the market continues to fragment across distinct vehicle segments and application types, companies that maintain agile modular platforms and robust supply chain visibility will be best equipped to navigate volatility. Ultimately, success will hinge on the seamless integration of opposed-piston fixed calipers into holistic vehicle dynamics ecosystems, delivering consistent, reliable braking performance under every driving condition.
This section provides a structured overview of the report, outlining key chapters and topics covered for easy reference in our Opposed-Piston Fixed Calipers market comprehensive research report.
- Preface
- Research Methodology
- Executive Summary
- Market Overview
- Market Dynamics
- Market Insights
- Cumulative Impact of United States Tariffs 2025
- Opposed-Piston Fixed Calipers Market, by Material Composition
- Opposed-Piston Fixed Calipers Market, by Vehicle Type
- Opposed-Piston Fixed Calipers Market, by End-User Industry
- Opposed-Piston Fixed Calipers Market, by Technology
- Opposed-Piston Fixed Calipers Market, by Application Type
- Opposed-Piston Fixed Calipers Market, by Caliper Design
- Opposed-Piston Fixed Calipers Market, by Braking Performance
- Opposed-Piston Fixed Calipers Market, by Production Process
- Opposed-Piston Fixed Calipers Market, by Customer Segment
- Americas Opposed-Piston Fixed Calipers Market
- Asia-Pacific Opposed-Piston Fixed Calipers Market
- Europe, Middle East & Africa Opposed-Piston Fixed Calipers Market
- Competitive Landscape
- ResearchAI
- ResearchStatistics
- ResearchContacts
- ResearchArticles
- Appendix
- List of Figures [Total: 34]
- List of Tables [Total: 855 ]
Contact Ketan Rohom for the Full Market Research Report
Unlock the full breadth of insights, data, and strategic guidance on opposed-piston fixed calipers by reaching out to Ketan Rohom, Associate Director, Sales & Marketing. Gain access to comprehensive analysis that will empower your organization to optimize sourcing strategies, capitalize on regional growth trends, and develop next-generation braking systems that meet the demands of today’s mobility revolution.
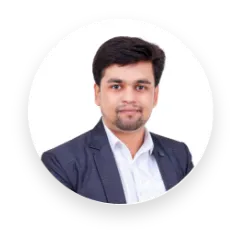
- When do I get the report?
- In what format does this report get delivered to me?
- How long has 360iResearch been around?
- What if I have a question about your reports?
- Can I share this report with my team?
- Can I use your research in my presentation?