Introduction: Evolution and Strategic Importance of Optical Wafer Inspection Systems
Optical wafer inspection systems have become indispensable as semiconductor manufacturing advances into ever-smaller nodes and higher complexity architectures. These systems underpin quality assurance by detecting submicron defects on 100 mm through 300 mm or larger wafers with unparalleled precision. As demand for smaller geometries and tighter tolerances intensifies, manufacturers require inspection solutions that marry speed with sensitivity to safeguard yield and reliability.
The increasing prevalence of advanced packaging, 3D integration, and heterogeneous materials has driven a shift from manual inspection toward automated optical platforms. Modern brightfield and darkfield techniques work in concert with laser scanning, electron-beam, and photoelectron emission microscopy to deliver comprehensive coverage. Consequently, inspection capabilities now extend beyond mere defect detection to enable root-cause identification and in-line process optimization.
Transformative Shifts Reshaping the Optical Wafer Inspection Landscape
Recent years have witnessed transformative shifts as integration of AI-driven diagnostics and IoT connectivity accelerates real-time analysis and predictive maintenance. Automated optical inspection platforms leveraging machine learning algorithms can now classify edge, pattern, and surface defects-whether scratches or microscopic contaminants-with greater accuracy than legacy systems.
At the same time, the move toward high-throughput, low-volume production for advanced logic and specialized memory applications has compelled vendors to innovate modular inspection architectures. The emergence of in-situ metrology tools supports seamless data exchange between fab equipment, shortening cycle times and improving yield improvement initiatives. Moreover, strategic partnerships between equipment suppliers and integrated device manufacturers have fostered joint development of next-generation solutions tailored for 300 mm and larger wafer formats.
Cumulative Impact of U.S. Tariffs on Optical Wafer Inspection in 2025
The introduction of U.S. tariffs on foreign-manufactured inspection equipment in 2025 is reshaping global supply chains and cost structures. Manufacturers who rely on imported analyzers, lens systems, and sensor modules face increased landed costs, prompting many to reevaluate sourcing strategies. Some are accelerating investments in domestic production lines for light source components-both lamp and laser-while others negotiate long-term component agreements to mitigate price volatility.
Consequently, inspection suppliers are diversifying their manufacturing footprints across Asia-Pacific and the Americas, reducing dependency on single-region production. The tariff landscape has also catalyzed innovation in production versus prototype automated optical inspection platforms, driving demand for configurable, software-centric systems that can be updated remotely to address evolving compliance requirements. In parallel, end-user industries are adjusting failure analysis and defect detection protocols to optimize throughput under new cost constraints.
Key Segmentation Insights Driving Market Dynamics
An in-depth analysis of market segmentation by technology type reveals the critical roles of E-Beam inspection, laser scanning methodologies, optical brightfield and darkfield systems, and emerging photoelectron emission microscopy in addressing diverse defect detection challenges. While optical approaches dominate high-speed wafer scanning, electron-beam and photoelectron technologies provide complementary insights for circuit pattern defect analysis and root cause identification during failure analysis.
When considering applications, defect detection workflows focusing on circuit pattern defects and particle identification coexist alongside specialized failure analysis processes for fault localization and comprehensive root cause reporting, all driving yield improvement goals. Wafer size segmentation underscores the continued predominance of 300 mm or larger wafers in advanced fabs, even as 200 mm and 150 mm tools maintain relevance for legacy processes and niche applications below 100 mm.
End users span electronics manufacturing entities striving for maximal throughput and semiconductor industry players prioritizing process control. Component type segmentation highlights that analyzer performance hinges on precision lens systems, robust light source modules-whether conventional lamps or laser emitters-and sensitive sensor arrays ranging from color and monochrome CCD cameras to advanced photodetectors. Insights from inspection type analysis demonstrate growing adoption of automated optical inspection in both production and prototype environments, though manual inspection retains a role in specialized quality audits.
Defect type segmentation clarifies the distribution between edge, pattern, and surface defects-with contaminants and scratches representing key surface challenges-while system type analysis contrasts high-throughput architectures optimized for mass production against low-volume platforms designed for R&D and pilot runs. Probe equipment categories reveal complementary electrical probing and optical probing techniques, and current innovation segmentation underscores the rising influence of AI-driven diagnostics and IoT integration in delivering actionable intelligence.
This comprehensive research report categorizes the Optical Wafer Inspection System market into clearly defined segments, providing a detailed analysis of emerging trends and precise revenue forecasts to support strategic decision-making.
- Technology Type
- Application
- Wafer Size
- End User Industry
- Component Type
- Inspection Type
- Defect Types
- System Type
- Probe Equipment
- Current Innovation
Key Regional Insights Across Major Markets
The Americas region continues to lead in inspection equipment adoption, driven by robust semiconductor manufacturing hubs in the United States and Canada focused on logic and advanced packaging. Investments in domestic tool development have spurred innovation in high-throughput systems, complementing efforts to localize critical component assembly.
Europe, Middle East & Africa reflect a balanced mix of mature consumer electronics manufacturing centers and emerging fab initiatives in automotive and power electronics sectors. Here, regulatory standards for failure analysis and yield improvement foster collaborations between equipment vendors and research institutions, elevating the sophistication of both production and prototype inspection methodologies.
Asia-Pacific remains the fastest-growing market for optical wafer inspection systems, supported by substantial capacity expansions across China, South Korea, Taiwan, and Japan. With wafer sizes predominantly at 300 mm or larger and aggressive roadmaps for next-generation nodes, manufacturers in this region emphasize AI-integrated diagnostics and high-precision darkfield inspection to maintain competitive edge.
This comprehensive research report examines key regions that drive the evolution of the Optical Wafer Inspection System market, offering deep insights into regional trends, growth factors, and industry developments that are influencing market performance.
- Americas
- Asia-Pacific
- Europe, Middle East & Africa
Key Company Profiles Influencing Industry Trends
Several global equipment suppliers are shaping the optical wafer inspection ecosystem through continuous R&D and strategic partnerships. Applied Materials, Inc. and KLA Corporation drive advancements in automated optical and electron-beam inspection, while ASML Holding N.V. and Tokyo Electron Limited deliver critical lithography-inspection synergies. Lam Research Corporation and Hitachi High-Technologies Corporation focus on lens system and analyzer innovations, enabling fine-tuned defect detection across diverse wafer sizes.
Memory and logic device manufacturers also influence inspection technology roadmaps. Micron Technology, Inc., Samsung Electronics Co., Ltd., and Taiwan Semiconductor Manufacturing Company collaborate with tool vendors to tailor solutions for high-volume memory production, whereas Infineon Technologies AG and NXP Semiconductors N.V. prioritize yield improvement in automotive and IoT device fabs.
Specialized inspection companies bring niche expertise to the market. Hermes Microvision, Inc. and Rudolph Technologies, Inc. are recognized for cutting-edge sensor modules and photodetector integration, Nova Measuring Instruments Ltd. advances metrology-aligned inspection approaches, and Teradyne, Inc. contributes robust test-and-probe solutions integrating electrical and optical probing capabilities.
This comprehensive research report delivers an in-depth overview of the principal market players in the Optical Wafer Inspection System market, evaluating their market share, strategic initiatives, and competitive positioning to illuminate the factors shaping the competitive landscape.
- Applied Materials, Inc.
- ASML Holding N.V.
- Hermes Microvision, Inc.
- Hitachi High-Technologies Corporation
- Infineon Technologies AG
- KLA Corporation
- Lam Research Corporation
- Micron Technology, Inc.
- Nova Measuring Instruments Ltd.
- NXP Semiconductors N.V.
- Rudolph Technologies, Inc.
- Samsung Electronics Co., Ltd.
- Taiwan Semiconductor Manufacturing Company (TSMC)
- Teradyne, Inc.
- Tokyo Electron Limited (TEL)
Actionable Recommendations for Industry Leaders
Industry leaders should prioritize integration of AI-driven diagnostics and IoT connectivity to enable predictive maintenance and real-time defect classification. By adopting modular architectures, they can swiftly update inspection platforms to address tariff-related component shortages and evolving defect typologies.
Supply chain resilience is critical. Establishing multi-regional manufacturing lines for analyzers, sensor modules, and light sources will mitigate geopolitical risks. Partnering with local component suppliers for lamps, lasers, and CCD camera assemblies can reduce exposure to import tariffs and shipping delays.
Fostering collaborative R&D alliances with wafer fabs and university research centers will accelerate development of next-generation brightfield, darkfield, and photoelectron emission inspection techniques. Additionally, upskilling technical teams in advanced analytics and machine learning will ensure rapid deployment of novel defect detection algorithms.
Finally, engaging proactively with industry consortia on standards for automated optical inspection and failure analysis will shape regulatory frameworks in favor of innovative, software-centric inspection solutions.
Explore AI-driven insights for the Optical Wafer Inspection System market with ResearchAI on our online platform, providing deeper, data-backed market analysis.
Ask ResearchAI anything
World's First Innovative Al for Market Research
Conclusion: Navigating the Future of Wafer Inspection
Optical wafer inspection stands at the nexus of semiconductor quality assurance and process innovation. As the landscape evolves under technological, regulatory, and economic pressures, a strategic approach that balances automation, segmentation insights, and regional adaptability will define success. Leaders who align supply chains with localized manufacturing, embrace AI-powered diagnostics, and cultivate collaborative development ecosystems will effectively navigate tariff challenges and emerging defect detection demands.
This section provides a structured overview of the report, outlining key chapters and topics covered for easy reference in our Optical Wafer Inspection System market comprehensive research report.
- Preface
- Research Methodology
- Executive Summary
- Market Overview
- Market Dynamics
- Market Insights
- Cumulative Impact of United States Tariffs 2025
- Optical Wafer Inspection System Market, by Technology Type
- Optical Wafer Inspection System Market, by Application
- Optical Wafer Inspection System Market, by Wafer Size
- Optical Wafer Inspection System Market, by End User Industry
- Optical Wafer Inspection System Market, by Component Type
- Optical Wafer Inspection System Market, by Inspection Type
- Optical Wafer Inspection System Market, by Defect Types
- Optical Wafer Inspection System Market, by System Type
- Optical Wafer Inspection System Market, by Probe Equipment
- Optical Wafer Inspection System Market, by Current Innovation
- Americas Optical Wafer Inspection System Market
- Asia-Pacific Optical Wafer Inspection System Market
- Europe, Middle East & Africa Optical Wafer Inspection System Market
- Competitive Landscape
- ResearchAI
- ResearchStatistics
- ResearchContacts
- ResearchArticles
- Appendix
- List of Figures [Total: 36]
- List of Tables [Total: 811 ]
Call to Action: Connect with Ketan Rohom for In-Depth Insights
Unlock the full potential of wafer inspection intelligence. Contact Ketan Rohom (Associate Director, Sales & Marketing) to secure the comprehensive market research report and gain actionable insights tailored to your strategic objectives.
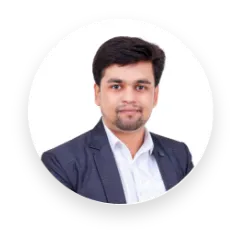
- When do I get the report?
- In what format does this report get delivered to me?
- How long has 360iResearch been around?
- What if I have a question about your reports?
- Can I share this report with my team?
- Can I use your research in my presentation?