Introduction to the Evolution and Strategic Importance of Palletizing Robot Arms
Automation has emerged as a cornerstone of modern logistics, and palletizing robot arms are at the forefront of this transformation. By automating the stacking and organizing of products on pallets, these robotic systems enhance throughput, reduce labor costs, and minimize workplace injuries. Today’s palletizing solutions blend advanced motion control, sophisticated end effectors, and intelligent vision systems to meet the varied demands of industries from food and beverage to automotive.
Market leaders are now focusing on scalable, flexible cells that can adapt to evolving production lines. Instead of rigid, high-cost installations, businesses are investing in modular units that integrate seamlessly with existing conveyors and sorting equipment. As global supply chains grow more complex, palletizing robot arms play a pivotal role in ensuring efficiency and reliability, enabling manufacturers and logistics providers to maintain competitive advantage.
This executive summary explores the driving forces shaping this sector, examines the impact of shifting trade policies, unpacks critical segmentation and regional dynamics, highlights leading companies, and outlines strategic recommendations. By understanding these factors, executives and decision-makers can chart a clear path toward optimized operations and sustainable growth in pallet automation.
Key Transformative Shifts Redefining Palletizing Robot Arm Deployment
The landscape of palletizing robot arm deployment has undergone profound shifts in recent years, fueled by rapid advancements in robotics, data analytics, and human–machine collaboration. Core innovations in articulated robots have unlocked unprecedented reach and payload capacity, while SCARA robots now deliver pinpoint accuracy for lighter loads. At the same time, the emergence of collaborative robots has democratized automation, allowing smaller operations to deploy safe, easy-to-program systems alongside human workers without extensive safety fencing.
Parallel to hardware evolution, the rise of artificial intelligence and edge computing has empowered control systems to dynamically adjust stacking patterns, detect anomalies in real time, and optimize cycle times through predictive maintenance. Where traditional deployments demanded rigid programming and lengthy downtime for changeovers, today’s platforms support rapid recipe changes, ideal for industries with high SKU variability.
Finally, supply chain resilience has become a priority. Companies are shifting away from single-source solutions and embracing distributed, modular architectures that can be rapidly reconfigured or relocated. This shift not only mitigates risk from localized disruptions but also shortens time to market for new facilities and product lines.
Assessing the Cumulative Impact of 2025 U.S. Tariffs on Palletizing Robot Arms
The United States’ tariff measures introduced in 2025 have had a cumulative impact on manufacturers and end users of palletizing robot arms. Tariffs on robotic components have driven up the landed cost of critical modules such as servo motors, gearboxes, and precision sensors. In response, many original equipment manufacturers have reevaluated their supply base, accelerating near-shoring strategies and qualifying alternative suppliers in tariff-exempt regions.
These trade policy shifts have also influenced system design priorities. Suppliers now emphasize modular subassemblies that can be sourced locally to offset tariff exposure. Some automation vendors have restructured procurement contracts to include hedging mechanisms or transferred certain manufacturing steps to regional facilities to avoid cross-border duties.
End users are feeling the pinch as well, particularly in industries with tight margins like consumer goods and food and beverage. Higher equipment acquisition costs have prompted a growing number of companies to extend capital investment cycles, negotiate extended payment terms, or pursue rental-based automation models. Despite these headwinds, strong long-term demand for throughput gains and labor optimization continues to underpin steady investment in palletizing robotics.
Key Segmentation Insights for Palletizing Robot Arm Adoption
When analyzed by type, articulated robots dominate high-payload, high-reach palletizing applications, while SCARA robots capture significant share in low-volume, high-precision scenarios; within Cartesian robots, the 2-axis variant excels in space-constrained environments but 4-axis designs are increasingly favored for complex stacking patterns. Examining end effector options reveals that custom end effectors deliver tailored solutions for unique product geometries, but grippers remain the standard, with three-finger grippers handling irregular loads and two-finger grippers optimized for uniform cartons.
Payload capacity segmentation indicates a robust appetite for 50–100 kg systems in heavy-duty warehousing, whereas 5–20 kg models are prevalent in light-assembly operations; demand for systems above 100 kg is growing in automotive and metal processing lines. Within industry verticals, automotive continues to invest heavily in fully automated palletizing lines, while food and beverage players prioritize hygienic designs with vacuum cups; the pharmaceutical sector values strict cleanroom compatibility. Looking at applications, handling tasks make up the majority of deployments, but assembly and disassembly use cases are accelerating as manufacturers seek end-to-end automation, and welding palletizer hybrids are carving out niche opportunities in metal fabrication.
This comprehensive research report categorizes the Palletizing Robot Arm market into clearly defined segments, providing a detailed analysis of emerging trends and precise revenue forecasts to support strategic decision-making.
- Type
- End Effector
- Payload Capacity
- Industry
- Application
Key Regional Insights Shaping the Palletizing Robot Arm Market
In the Americas, widespread interest in labor cost reduction and reshoring initiatives is fueling rapid adoption of palletizing robot arms across manufacturing and distribution centers. Infrastructure readiness and strong financial incentives have supported aggressive automation roadmaps. In Europe, Middle East & Africa, stringent safety regulations and energy efficiency mandates have driven innovation in collaborative and vacuum-based palletizers, while supply chain disruptions in certain regions have encouraged investments in buffer automation to smooth throughput peaks.
Across Asia-Pacific, a combination of rising wages in emerging markets and government-backed robotics programs has propelled demand for palate-level automation. China’s ‘Made in China 2025’ initiative and South Korea’s smart factory subsidies are prime examples of public-sector programs catalyzing deployments. Japan maintains leadership in high-precision, ultra-high-speed palletizing solutions, and Southeast Asian hubs like Malaysia and Thailand are establishing themselves as regional assembly centers that adopt mid-range, cost-effective robotic cells.
This comprehensive research report examines key regions that drive the evolution of the Palletizing Robot Arm market, offering deep insights into regional trends, growth factors, and industry developments that are influencing market performance.
- Americas
- Asia-Pacific
- Europe, Middle East & Africa
Key Company Profiles Driving Palletizing Robot Arm Innovation
Global progress in palletizing robot arm innovation is being driven by a diverse array of established robotics and automation companies. ABB and ABB Ltd. continue to lead with modular 4-axis Cartesian and articulated solutions, while Bosch Rexroth AG integrates smart hydraulics for heavy-payload applications. Comau’s expertise in automotive palletizing cells complements Denso’s compact, high-speed SCARA lines. FANUC and Fuji Robotics maintain broad portfolios spanning collaborative arms to high-capacity articulated systems, and Hyundai Robotics leverages its automotive heritage for robust, high-frequency stacking.
Kawasaki Robotics and Krones AG focus on turnkey beverage line solutions with hygienic stainless-steel designs, whereas KUKA and Mitsubishi Electric drive innovation in integrated vision-guided palletizing. Omron Corporation emphasizes safety-first collaborative palletizers, complemented by Schneider Electric’s IoT-enabled control ecosystems. Seiko Epson Corporation and Staubli develop compact SCARA and delta variants for light assembly and palletizing, while Techman Robot and Universal Robots pioneer user-friendly, plug-and-play cobot cells. Yaskawa’s Motoman series rounds out the landscape with proven reliability in high-throughput distribution operations.
This comprehensive research report delivers an in-depth overview of the principal market players in the Palletizing Robot Arm market, evaluating their market share, strategic initiatives, and competitive positioning to illuminate the factors shaping the competitive landscape.
- ABB
- ABB Ltd.
- Bosch Rexroth AG
- Comau
- Denso
- FANUC
- Fuji Robotics
- Hyundai Robotics
- Kawasaki Robotics
- Krones AG
- KUKA
- Mitsubishi Electric
- Omron Corporation
- Schneider Electric
- Seiko Epson Corporation
- Staubli
- Stäubli Robotics
- Techman Robot
- Universal Robots
- Yaskawa
Actionable Recommendations for Industry Leaders Embracing Automation
Industry leaders should take proactive steps to capture the full potential of palletizing robot arms:
-
Expand modularization: Standardize on modular hardware platforms and software frameworks that allow rapid reconfiguration across multiple pallet patterns and product types. This will shorten integration cycles and lower total cost of ownership.
-
Invest in edge intelligence: Deploy real-time analytics at the cell level to monitor performance, predict maintenance requirements, and adjust stacking algorithms dynamically. Edge computing reduces latency and enhances system resilience.
-
Forge strategic partnerships: Collaborate with suppliers of vision systems, end effector designers, and integrators to build ecosystem alliances. Joint R&D efforts can accelerate the development of differentiated solutions for specific industries.
-
Emphasize workforce enablement: Pair advanced human-machine interfaces with comprehensive training programs to ensure smooth adoption. Upskill technicians to manage robot deployment, troubleshooting, and continuous improvement initiatives.
-
Mitigate supply chain risks: Diversify component sourcing and qualify regional suppliers to buffer against tariff volatility and logistics disruptions. Consider dual-sourcing key modules and establishing local assembly cells where feasible.
Explore AI-driven insights for the Palletizing Robot Arm market with ResearchAI on our online platform, providing deeper, data-backed market analysis.
Ask ResearchAI anything
World's First Innovative Al for Market Research
Conclusion: Strategic Imperatives for Palletizing Robot Arm Implementation
Palletizing robot arms represent a transformative investment in operational efficiency and competitive differentiation. By embracing flexible architectures, intelligence-driven controls, and strategic sourcing approaches, organizations can achieve sustained throughput gains and accelerated return on investment. Cross-functional collaboration-aligning procurement, engineering, and operations teams-will be essential to navigate trade policy shifts and market uncertainties.
As automation continues to evolve, the integration of AI-enabled vision, collaborative human–robot workflows, and digital twin technologies will define the next frontier in palletizing performance. Companies that anticipate these trends and adjust their automation roadmaps accordingly will secure the dual advantage of optimized labor utilization and future-proofed production environments.
This section provides a structured overview of the report, outlining key chapters and topics covered for easy reference in our Palletizing Robot Arm market comprehensive research report.
- Preface
- Research Methodology
- Executive Summary
- Market Overview
- Market Dynamics
- Market Insights
- Cumulative Impact of United States Tariffs 2025
- Palletizing Robot Arm Market, by Type
- Palletizing Robot Arm Market, by End Effector
- Palletizing Robot Arm Market, by Payload Capacity
- Palletizing Robot Arm Market, by Industry
- Palletizing Robot Arm Market, by Application
- Americas Palletizing Robot Arm Market
- Asia-Pacific Palletizing Robot Arm Market
- Europe, Middle East & Africa Palletizing Robot Arm Market
- Competitive Landscape
- ResearchAI
- ResearchStatistics
- ResearchContacts
- ResearchArticles
- Appendix
- List of Figures [Total: 26]
- List of Tables [Total: 331 ]
Next Steps: Engage with Ketan Rohom for Comprehensive Market Analysis
To learn more about detailed competitive analysis, segmentation deep dives, and regional opportunities in the palletizing robot arm market, contact Ketan Rohom, Associate Director, Sales & Marketing. Engage with him to secure a comprehensive market research report that will guide your automation strategy and investment decisions.
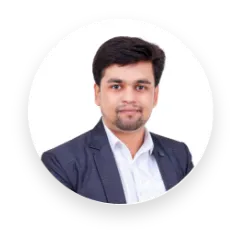
- When do I get the report?
- In what format does this report get delivered to me?
- How long has 360iResearch been around?
- What if I have a question about your reports?
- Can I share this report with my team?
- Can I use your research in my presentation?