Introduction to the PCD Pre-Cutter Market and Its Strategic Importance
The polycrystalline diamond (PCD) pre-cutter market serves as a critical foundation for high-performance cutting applications across diverse industrial sectors. PCD pre-cutters harness the superlative hardness and wear resistance of engineered diamond composites to deliver precision material removal in demanding environments. As manufacturers prioritize throughput, surface finish, and tool longevity, PCD pre-cutters have emerged as a strategic enabler for sectors ranging from aerospace and automotive to heavy machinery and mining. Transitioning from conventional carbide tools, end users are embracing diamond-based pre-cutters to achieve tighter tolerances, minimize downtime, and reduce total cost of ownership. In parallel, advances in manufacturing techniques-such as hot pressing and brazed sintered processes-alongside novel coating technologies have elevated PCD pre-cutter performance, enabling faster feed rates and longer tool life.
This introduction outlines the strategic importance of PCD pre-cutters in meeting evolving performance requirements, setting the stage for an exploration of the transformative forces, tariff impacts, segmentation insights, regional dynamics, competitive landscape, and recommended strategies that define this dynamic market.
Transformative Shifts Reshaping the Competitive Landscape
Rapid technological progress and shifting global supply chains are redefining the competitive landscape for PCD pre-cutters. Leading manufacturers are integrating digital tool management systems and real-time condition monitoring to optimize cutting parameters and predict maintenance needs. Sustainability mandates have spurred the adoption of eco-friendly manufacturing processes and recycled diamond materials, while end users demand ultra-clean machining to meet stringent regulatory standards. The growing emphasis on reshoring and nearshoring has prompted strategic realignment of production footprints, with key players establishing localized fabrication centers to mitigate logistical risks and tariff exposures. Concurrently, the rise of mass customization has increased the need for agile tool portfolios capable of addressing a spectrum of component geometries and materials.
These transformative shifts underscore a market in flux, driven by technological innovation, regulatory pressure, and evolving customer expectations. As we move forward, it becomes essential to assess how policy changes-particularly U.S. tariff adjustments slated for 2025-will further shape supply chains and competitive dynamics.
Assessing the Cumulative Impact of US Tariffs in 2025
The scheduled expansion of U.S. tariffs in 2025 is poised to exert a cumulative impact on raw material costs, import structures, and pricing strategies within the PCD pre-cutter market. Tariff increments on imported diamond composites and related tooling components have intensified cost pressures for manufacturers reliant on cross-border supply chains. In response, many suppliers are renegotiating long-term agreements with domestic producers of CVD and HPHT diamond feedstock to circumvent escalating duties. These strategic sourcing initiatives aim to safeguard margins while ensuring uninterrupted material availability.
End users are likewise adjusting procurement practices, favoring full-service contracts that bundle tool supply with sharpening, recoating, and inventory management to stabilize delivered costs. On the manufacturing front, some OEMs are accelerating investments in local fabrication cells, thereby reducing exposure to tariff fluctuations and freight volatility. Collectively, these measures highlight a market adapting to policy-induced headwinds by reinforcing regional supply resilience, optimizing total cost of ownership, and shifting toward value-driven service models.
Key Segmentation Insights for Targeting Diverse Market Niches
A nuanced segmentation approach reveals multiple avenues for targeted growth and tailored product development. Material type analysis distinguishes between brazed diamond variants prized for robust wear resistance, carbon tool steel alternatives that offer balanced toughness and affordability, and high-performance polycrystalline diamond grades engineered for ultra-fine finish. Application area considerations range from mission-critical aerospace machining requiring micron-level precision to high-volume automotive production demanding consistent cycle times, and general manufacturing use cases where versatility and tool life are paramount.
End-user industry dynamics further stratify demand: the construction sector bifurcates into large-scale infrastructure projects and residential building applications, each with distinct cutter geometries and durability requirements; industrial consumers differentiate between healthcare equipment fabrication, which prioritizes contamination control, and heavy machinery manufacturing where sheer volume and robustness dominate; and the mining industry spans surface operations requiring large-format blades and underground extraction tolerating extreme abrasion. Tool type segmentation contrasts cutting blades-offered in mobile and stationary formats-with rotary tools encompassing specialized drilling and milling variants. Manufacturing processes such as brazed sintered assembly, advanced coating, and hot pressing underpin tool performance, while cutting direction selections (left-hand, right-hand, straight) influence chip evacuation and surface integrity.
Technology adoption trends underscore a shift toward laser cutting, plasma cutting, and water jet cutting for complementary applications, necessitating hybrid tool solutions. Tool configuration choices between multi-point and single-point cutting tools affect operational flexibility and cost per part. End-user requirements, whether targeting high-speed operations or precision cutting, drive geometry and grade customization. Finally, usage frequency and material hardness considerations-spanning multi-use and single-use scenarios as well as high-hardness versus medium-hardness options-refine product positioning and service models within this intricate market mosaic.
This comprehensive research report categorizes the PCD Pre-Cutter market into clearly defined segments, providing a detailed analysis of emerging trends and precise revenue forecasts to support strategic decision-making.
- Material Type
- Application Area
- End-User Industry
- Tool Type
- Manufacturing Process
- Cutting Direction
- Technology Adoption
- Tool Configuration
- End-User Requirement
- Usage Frequency
- Material Hardness
Key Regional Dynamics Influencing Growth Opportunities
Regional dynamics play a critical role in shaping demand patterns and competitive intensity across the PCD pre-cutter market. In the Americas, infrastructure modernization programs, a robust aerospace industry, and a revitalized automotive sector support steady uptake of high-performance cutters, while reshoring initiatives drive domestic tool production. Europe, Middle East & Africa presents a multifaceted landscape: Western European manufacturing hubs continue to demand ultra-precision tooling for medical and automotive applications, regulatory frameworks push sustainable practices, and emerging markets in the Middle East and Africa invest heavily in construction and mining, expanding the addressable base for durable cutting solutions. Asia-Pacific emerges as the fastest-evolving region, propelled by large-scale infrastructure projects in Southeast Asia, surging automotive assembly in China and India, and government incentives for localized high-value manufacturing. Varying import duties, trade agreements, and local content regulations further influence regional supply chain architectures and investment strategies.
This comprehensive research report examines key regions that drive the evolution of the PCD Pre-Cutter market, offering deep insights into regional trends, growth factors, and industry developments that are influencing market performance.
- Americas
- Asia-Pacific
- Europe, Middle East & Africa
Competitive Landscape and Leading Industry Players
The competitive arena for PCD pre-cutters is defined by innovation leadership, broad product portfolios, and integrated service capabilities. DIAEDGE by Mitsubishi Materials Corporation leads with proprietary polycrystalline formulations and automated quality inspection systems that extend tool life. Element Six Limited focuses on its core expertise in synthetic diamond substrates, enabling ultra-fine finishes in high-precision sectors. Hyperion Materials & Technologies, Inc. differentiates through advanced coating platforms that dramatically reduce wear rates in abrasive environments. Iscar Ltd. drives modular tooling concepts, simplifying changeovers in high-volume production lines, while Kennametal Inc. leverages its global footprint to offer seamless after-sales support for both cutting blades and rotary configurations. LOVEJOY Tool Company, Inc. specializes in tailored multi-point cutting solutions, and MAPAL Dr. Kress KG excels in high-speed drilling and precision milling applications. Real Diamond Coating, Inc. applies unique surface treatments to enhance both performance and corrosion resistance. Sandvik AB remains at the forefront of geometric optimization through extensive R&D investments, and Seco Tools AB partners closely with OEMs to co-develop application-specific tool sets. SHINHAN DIAMOND IND CO., LTD. targets cost-sensitive large-scale operations with competitively priced PCD inserts, while Sumitomo Electric Industries, Ltd. emphasizes sustainable manufacturing practices and next-generation diamond composite architectures.
This comprehensive research report delivers an in-depth overview of the principal market players in the PCD Pre-Cutter market, evaluating their market share, strategic initiatives, and competitive positioning to illuminate the factors shaping the competitive landscape.
- DIAEDGE by Mitsubishi Materials Corporation
- Element Six Limited
- Hyperion Materials & Technologies, Inc.
- Iscar Ltd.
- Kennametal Inc.
- LOVEJOY Tool Company, Inc.
- MAPAL Dr. Kress KG
- Real Diamond Coating, Inc.
- Sandvik AB
- Seco Tools AB
- SHINHAN DIAMOND IND CO., LTD.
- Sumitomo Electric Industries, Ltd.
Actionable Recommendations to Drive Market Leadership
To secure sustainable growth and market leadership, industry participants should adopt a multi-pronged strategy. First, broaden the product portfolio by developing tailored PCD grades and tool geometries aligned with emerging applications such as electric vehicle component machining and composite material processing. Second, invest in digital manufacturing capabilities and real-time tool condition monitoring to reduce unplanned downtime and drive predictive maintenance programs. Third, establish strategic partnerships with diamond feedstock suppliers and local manufacturing partners to mitigate tariff exposures and reinforce supply chain resilience. Fourth, deploy modular tool platforms that support rapid changeovers, minimizing setup times and inventory carrying costs. Fifth, expand regional service networks and on-site technical support to deliver end-to-end solutions, encompassing sharpening, recoating, and inventory management. Finally, collaborate with research institutions to pioneer eco-friendly coating processes and fully recyclable diamond composites, reinforcing sustainability credentials while meeting stringent regulatory requirements.
Explore AI-driven insights for the PCD Pre-Cutter market with ResearchAI on our online platform, providing deeper, data-backed market analysis.
Ask ResearchAI anything
World's First Innovative Al for Market Research
Conclusion: Positioning for Sustainable Competitive Advantage
The PCD pre-cutter market stands at a crossroads defined by technological innovation, evolving regulatory frameworks, and shifting customer expectations. By synthesizing insights on tariff impacts, segmentation dynamics, regional trends, and competitive positioning, stakeholders can formulate strategies that balance short-term resilience with long-term differentiation. Emphasizing material science advancements, digital integration, and service-oriented business models will enable companies to capture value across the tool lifecycle. Concurrently, a nuanced understanding of region-specific drivers and end-user requirements ensures that product offerings resonate with target segments, from aerospace precision machining to mining abrasion challenges. Together, these strategic imperatives establish a roadmap for securing sustained competitive advantage and maximizing the return on investment in PCD pre-cutter technologies.
This section provides a structured overview of the report, outlining key chapters and topics covered for easy reference in our PCD Pre-Cutter market comprehensive research report.
- Preface
- Research Methodology
- Executive Summary
- Market Overview
- Market Dynamics
- Market Insights
- Cumulative Impact of United States Tariffs 2025
- PCD Pre-Cutter Market, by Material Type
- PCD Pre-Cutter Market, by Application Area
- PCD Pre-Cutter Market, by End-User Industry
- PCD Pre-Cutter Market, by Tool Type
- PCD Pre-Cutter Market, by Manufacturing Process
- PCD Pre-Cutter Market, by Cutting Direction
- PCD Pre-Cutter Market, by Technology Adoption
- PCD Pre-Cutter Market, by Tool Configuration
- PCD Pre-Cutter Market, by End-User Requirement
- PCD Pre-Cutter Market, by Usage Frequency
- PCD Pre-Cutter Market, by Material Hardness
- Americas PCD Pre-Cutter Market
- Asia-Pacific PCD Pre-Cutter Market
- Europe, Middle East & Africa PCD Pre-Cutter Market
- Competitive Landscape
- ResearchAI
- ResearchStatistics
- ResearchContacts
- ResearchArticles
- Appendix
- List of Figures [Total: 38]
- List of Tables [Total: 721 ]
Contact Ketan Rohom to Secure Your In-Depth Market Research Report
To access the comprehensive analysis, detailed segmentation frameworks, and strategic recommendations presented in this executive summary, contact Ketan Rohom, Associate Director, Sales & Marketing. Engage directly to secure your copy of the full market research report and gain the insights necessary to capitalize on emerging opportunities in the PCD pre-cutter market.
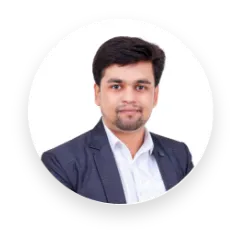
- When do I get the report?
- In what format does this report get delivered to me?
- How long has 360iResearch been around?
- What if I have a question about your reports?
- Can I share this report with my team?
- Can I use your research in my presentation?