Introduction to the Evolution of Continuous Granulation
Continuous granulation has emerged as a paradigm shift in pharmaceutical manufacturing, replacing traditional batch processes with seamless, real-time production. By integrating material handling, mixing, granulation, and drying into a continuous train, this approach enhances process control, reduces waste, and accelerates time to market. As regulatory agencies increasingly endorse Quality by Design principles and demand robust process analytical technology (PAT), manufacturers are under pressure to adopt strategies that ensure consistent product quality and scalability.
Today’s industry landscape is defined by a confluence of technological innovation, regulatory rigor, and supply chain complexity. High-value active pharmaceutical ingredients, diverse formulation requirements, and a growing emphasis on patient-centric therapies are driving manufacturers to reexamine their granulation strategies. Continuous granulation not only addresses these challenges but also aligns with sustainability goals by minimizing energy consumption and material losses.
Transitioning from batch to continuous operations requires careful assessment of equipment selection, process parameters, and in-line monitoring capabilities. Early adopters are already realizing reduced cycle times and greater agility in responding to formulation changes. In this executive summary, we explore the transformative shifts, external pressures, segmentation nuances, regional dynamics, and competitive drivers shaping the future of continuous granulation.
Transformative Shifts Reshaping Continuous Granulation
Over the last decade, continuous granulation has undergone transformative shifts, fueled by digitalization, advanced monitoring, and emerging regulatory frameworks. First, the integration of real-time analytics and PAT sensors within granulator trains has enabled predictive quality control. Inline particle size analysis, moisture monitoring, and torque measurements allow immediate adjustments, mitigating risks associated with batch variability.
Second, the adoption of Quality by Design methodologies has reshaped process development. Design of Experiments (DoE) and multivariate data analysis support the identification of critical process parameters, ensuring robust granulate attributes such as density, flowability, and compressibility. This proactive approach reduces costly reformulations and expedites regulatory submissions.
Third, Industry 4.0 concepts are gaining traction, with manufacturers leveraging digital twins and advanced process control systems. Virtual models of granulation lines facilitate seamless scale-up, while artificial intelligence algorithms optimize throughput and energy efficiency.
Finally, sustainability imperatives are driving eco-friendly process designs. Solvent-free granulation techniques and energy-efficient equipment contribute to lower carbon footprints. Taken together, these shifts have elevated continuous granulation from a novel concept to a strategic imperative, positioning manufacturers for enhanced competitiveness and resilience in a rapidly evolving environment.
Cumulative Impact of US Tariffs 2025 on Granulation Supply Chain
The introduction of new United States tariffs in 2025 has created a multilayered impact on continuous granulation supply chains. Tariffs on imported granulation equipment-spanning high shear granulators, twin screw extruders, and fluid bed units-have elevated capital expenditures, prompting companies to reevaluate vendor partnerships and consider domestic sourcing. Simultaneously, levies on key materials such as active pharmaceutical ingredients, binders, and excipients have exerted upward pressure on raw material costs, affecting formulation budgets and profit margins.
In response, leading manufacturers are exploring vertical integration strategies, negotiating long-term supply agreements, and adopting dual-sourcing models to mitigate risk. Some organizations have accelerated investment in continuous dry granulation to reduce reliance on solvent-based processes that depend on tariffed organic binder imports. Others are leveraging in-house compounding capabilities to produce critical excipients and disintegrants.
On the regulatory front, the tariff-driven shift has also spurred increased dialogue with health authorities to validate formulation changes and secure expedited reviews. As a result, companies that proactively address supply chain vulnerabilities can maintain production continuity and safeguard product quality. This cumulative tariff impact underscores the importance of agile sourcing strategies and resilient process platforms in an era of evolving trade policies.
Key Segmentation Insights Across Market Dimensions
Analyzing continuous granulation through multiple segmentation lenses reveals nuanced growth opportunities and strategic imperatives. When considering product type, the market divides into equipment and materials, with equipment platforms ranging from fluid bed granulators and high shear units to single and twin screw granulators, while materials encompass active pharmaceutical ingredients, binders-classified further into natural, organic, and synthetic-disintegrants, and excipients. In application segments, high potency drug products, immediate release formulas, modified release formulations-covering controlled, delayed, and extended release-and solvent-free systems each demand tailored process conditions and equipment features.
Examining industry verticals, biotechnology firms prioritize gentle granulation to preserve molecule integrity, contract manufacturing organizations focus on flexible, multiproduct lines, nutraceutical producers pursue scalable solvent-free processes, and traditional pharmaceutical manufacturers emphasize regulatory alignment and throughput. Process type segmentation highlights continuous dry granulation for moisture-sensitive compounds, continuous wet granulation for superior binder distribution, and direct compaction for cost-sensitive commodity products. From the end-user perspective, biotech innovators, established pharmaceutical companies, and research and development institutes each have distinct requirements for granulator customization, analytical capabilities, and scale. Finally, ingredient functionality segmentation-binders, disintegrants, fillers, and glidants-drives formulation optimization, influencing the choice of granulation technique and post-granulation processing. Together, these segmentation insights guide technology investments and market positioning strategies.
This comprehensive research report categorizes the Pharma Continuous Granulation market into clearly defined segments, providing a detailed analysis of emerging trends and precise revenue forecasts to support strategic decision-making.
- Product Type
- Application
- Industry
- Process Type
- End-User
- Ingredient Functionality
Key Regional Insights Influencing Adoption and Growth
Regional dynamics play a pivotal role in the adoption and evolution of continuous granulation technologies. In the Americas, a combination of robust pharmaceutical manufacturing hubs in North America and a growing contract development and manufacturing presence in Latin America has spurred demand for scalable continuous processes, with a focus on speed-to-market and cost efficiency. Investments in digital process control and local equipment manufacturing further strengthen the regional value chain.
Europe, the Middle East & Africa present a diverse landscape: Western Europe leads in regulatory compliance and PAT integration, while Eastern European markets are emerging as cost-effective manufacturing sites. The Middle East’s increasing focus on generic production and Africa’s nascent pharmaceutical infrastructure underscore opportunities for technology transfer and capacity building. Sustainability regulations in the EU are accelerating the shift toward solvent-free granulation.
Asia-Pacific remains the fastest growing region, driven by expanding generics and biosimilars production in China and India, coupled with governmental incentives for pharmaceutical modernization across Southeast Asia. Local equipment suppliers are enhancing their portfolios to meet regional preferences for turnkey continuous granulation lines, and strategic partnerships are flourishing to address the region’s vast patient population.
This comprehensive research report examines key regions that drive the evolution of the Pharma Continuous Granulation market, offering deep insights into regional trends, growth factors, and industry developments that are influencing market performance.
- Americas
- Asia-Pacific
- Europe, Middle East & Africa
Competitive Landscape and Leading Technology Providers
The competitive landscape of continuous granulation is shaped by a spectrum of established equipment suppliers and emerging technology specialists. ACG World and Bühler Group offer end-to-end granulation platforms integrating PAT and control software, while Alexanderwerk AG and Leistritz Extrusionstechnik GmbH specialize in twin screw solutions optimized for complex formulations. Companies such as Coperion GmbH and Glatt GmbH emphasize modular designs that facilitate rapid line changeovers across multiple product families.
On the analytical front, IKON Instruments Pvt. Ltd. and Mettler-Toledo International Inc. provide inline monitoring sensors essential for real-time quality assurance. Fitzpatrick Company and Hosokawa Micron Corporation deliver high shear and fluid bed granulators with advanced automation features. Frewitt SA and Sukhras Machines Pvt. Ltd. focus on customizable granulation trains for niche high potency and nutraceutical applications. Thermo Fisher Scientific Inc. and GEA Group Aktiengesellschaft round out the market with integrated process control systems and global service networks. Collectively, these organizations drive innovation through collaborative R&D, strategic alliances, and continuous upgrades that address evolving process demands.
This comprehensive research report delivers an in-depth overview of the principal market players in the Pharma Continuous Granulation market, evaluating their market share, strategic initiatives, and competitive positioning to illuminate the factors shaping the competitive landscape.
- ACG World
- Alexanderwerk AG
- Bühler Group
- Coperion GmbH
- Fitzpatrick Company
- Frewitt SA
- GEA Group Aktiengesellschaft
- Glatt GmbH
- Hosokawa Micron Corporation
- IKON Instruments Pvt. Ltd.
- L.B. Bohle Maschinen + Verfahren GmbH
- Leistritz Extrusionstechnik GmbH
- Mettler-Toledo International Inc.
- Sukhras Machines Pvt. Ltd.
- Thermo Fisher Scientific Inc.
Actionable Recommendations for Industry Leaders
To harness the full potential of continuous granulation, industry leaders should implement a series of targeted actions. First, establish cross-functional teams that bridge R&D, engineering, quality, and supply chain to accelerate process development and scale-up. Embedding Quality by Design principles from project inception will streamline regulatory approvals and reduce time-to-market.
Second, invest in modular, flexible equipment platforms that accommodate multiple granulation techniques-dry, wet, and direct compaction-to future-proof manufacturing lines against changing product portfolios. Leveraging digital twins and process simulation tools can further optimize equipment utilization and capacity planning.
Third, develop strategic sourcing agreements and dual-sourcing strategies for critical excipients and API precursors to mitigate tariff-induced supply risks. Engage in collaborative partnerships with local material suppliers to reduce lead times and transportation costs.
Fourth, implement advanced process control systems with integrated PAT modules for real-time monitoring and adaptive feedback loops, ensuring consistent granulate quality across high potency and modified release applications.
Finally, cultivate a culture of continuous improvement by training personnel in data analytics, process optimization, and regulatory best practices. Regularly benchmark performance against industry peers and invest in digital upskilling initiatives to maintain a competitive edge.
Explore AI-driven insights for the Pharma Continuous Granulation market with ResearchAI on our online platform, providing deeper, data-backed market analysis.
Ask ResearchAI anything
World's First Innovative Al for Market Research
Conclusion: Embracing Continuous Granulation as a Strategic Imperative
Continuous granulation stands at the forefront of pharmaceutical manufacturing innovation, offering unparalleled gains in efficiency, quality, and sustainability. By embracing digitalization, Quality by Design, and modular equipment architectures, organizations can navigate external pressures-ranging from regulatory demands to tariff disruptions-and unlock new levels of operational resilience. Strategic segmentation and regional insights guide targeted investment decisions, while collaboration with leading technology providers ensures access to cutting-edge solutions.
As the industry accelerates towards personalized therapies and complex formulations, continuous granulation will serve as a critical enabler of agile, patient-centric manufacturing. Companies that proactively adopt these methodologies and forge integrated, data-driven processes will secure a competitive advantage in both established and emerging markets.
This section provides a structured overview of the report, outlining key chapters and topics covered for easy reference in our Pharma Continuous Granulation market comprehensive research report.
- Preface
- Research Methodology
- Executive Summary
- Market Overview
- Market Dynamics
- Market Insights
- Cumulative Impact of United States Tariffs 2025
- Pharma Continuous Granulation Market, by Product Type
- Pharma Continuous Granulation Market, by Application
- Pharma Continuous Granulation Market, by Industry
- Pharma Continuous Granulation Market, by Process Type
- Pharma Continuous Granulation Market, by End-User
- Pharma Continuous Granulation Market, by Ingredient Functionality
- Americas Pharma Continuous Granulation Market
- Asia-Pacific Pharma Continuous Granulation Market
- Europe, Middle East & Africa Pharma Continuous Granulation Market
- Competitive Landscape
- ResearchAI
- ResearchStatistics
- ResearchContacts
- ResearchArticles
- Appendix
- List of Figures [Total: 28]
- List of Tables [Total: 465 ]
Contact Ketan Rohom for the Full Market Research Report
To gain comprehensive insights and actionable intelligence on continuous granulation trends, process technologies, competitive dynamics, and regulatory impacts, reach out to Ketan Rohom, Associate Director of Sales & Marketing, for detailed guidance and to purchase the full market research report. Unlock strategic advantages and position your organization at the vanguard of pharmaceutical manufacturing innovation.
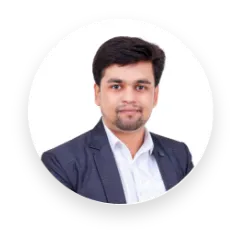
- When do I get the report?
- In what format does this report get delivered to me?
- How long has 360iResearch been around?
- What if I have a question about your reports?
- Can I share this report with my team?
- Can I use your research in my presentation?