The Physical Vapor Deposition Market size was estimated at USD 23.68 billion in 2024 and expected to reach USD 25.75 billion in 2025, at a CAGR 8.45% to reach USD 38.52 billion by 2030.

Unveiling the Strategic Importance of Physical Vapor Deposition Technologies Across High-Value Manufacturing Sectors
Physical Vapor Deposition (PVD) stands at the forefront of advanced coating technologies, offering precise control over thin-film formation and enabling high-performance materials across a multitude of industries. This process, which involves the vaporization of solid material in a vacuum environment and its subsequent condensation onto target substrates, underpins critical advancements in semiconductor fabrication, automotive component enhancement, and optical device manufacturing. As global demand intensifies for miniaturized electronics, durable tooling surfaces, and energy-efficient optics, PVD’s versatility and reliability position it as an indispensable enabler of technological progress.
Transitioning from conventional deposition methods, modern PVD has evolved to accommodate increasingly stringent performance requirements. Innovations in sputtering, magnetron technologies, and laser ablation have expanded the range of selectable materials, while enhancements in process monitoring ensure film uniformity at nanometer scales. Given its ability to deposit metals, nitrides, carbides, and oxide coatings with exceptional adhesion and compositional purity, PVD is now a linchpin in achieving wear resistance in cutting tools, anti-reflective layers on lenses, and corrosion protection on medical implants. This introduction sets the stage for an in-depth exploration of the market dynamics, technological shifts, and strategic imperatives shaping the PVD landscape.
Exploring Major Technological and Market Disruptions Reshaping Physical Vapor Deposition Applications and Value Chains Across Industries
The Physical Vapor Deposition landscape is undergoing profound transformation, driven by rapid adoption of electric vehicles, expansion of data center infrastructures, and mounting sustainability mandates. Automotive manufacturers are increasingly relying on PVD-enhanced components to extend service life and reduce friction, while semiconductor fabs demand ultra-thin, defect-free films to support sub-5-nanometer nodes. Meanwhile, the solar energy sector leverages PVD for depositing anti-reflective coatings that maximize photon absorption, underscoring the technology’s role in advancing renewable energy solutions.
In parallel, the convergence of Industry 4.0 and digital twin frameworks has introduced real-time process optimization, enabling manufacturers to monitor film growth parameters and anticipate maintenance schedules. Additive manufacturing processes are being integrated with PVD to create bespoke tooling with tailored surface properties. Furthermore, developments in green manufacturing are motivating equipment vendors to reduce chamber volumes, lower energy consumption, and substitute hazardous gases with eco-friendly alternatives. These transformative shifts illustrate a market in flux, where agility and innovation dictate competitive differentiation.
Analyzing the Compounding Economic Effects of Enhanced U.S. Tariff Measures on Physical Vapor Deposition Equipment since 2025
Since January 1, 2025, the United States Trade Representative increased Section 301 tariff rates on semiconductor products classified under HTS headings 8541 and 8542 from 25% to 50%, significantly impacting the cost structure of imported Physical Vapor Deposition equipment that contains semiconductor-grade components. This escalation has amplified capital expenditure requirements for deposition chambers, power supplies, and substrate holders sourced from overseas manufacturers, prompting project planners to reevaluate supply strategies.
Industry executives estimate that the new tariff regime could impose annual cost burdens exceeding $1 billion on leading U.S. PVD equipment suppliers such as Applied Materials, Lam Research, and KLA, each potentially absorbing up to $350 million in additional expenses per year. Smaller niche vendors, including those focused on specialized ion sources and vacuum chambers, face disproportionate risks due to limited pricing flexibility. As a result, a number of companies have begun engaging with U.S. policymakers to seek relief, while exploring tariff engineering and alternative sourcing from tariff-excluded jurisdictions.
Looking ahead, the cumulative impact of these tariff measures extends beyond immediate cost increases. Manufacturers are accelerating discussions around on-shore assembly and local component partnerships to mitigate exposure. Strategic procurement teams are negotiating longer lead times and consolidating orders to spread higher duty expenses over larger volumes. Although these adaptations introduce operational complexity, they also present an opportunity for domestic equipment assembly and R&D investment, aligning with broader national objectives to enhance supply chain resilience.
Uncovering Insights from Multi-Dimensional Segmentation Strategies Driving Physical Vapor Deposition Market Dynamics Evolution
Market segmentation for Physical Vapor Deposition reveals nuanced dynamics across technology modalities, from cathodic arc and pulsed laser deposition to electron beam and thermal evaporation. Within sputtering techniques, the evolution from ion beam to magnetron sputtering-and further into DC and RF magnetron variants-highlights divergent value propositions in deposition rate, film uniformity, and scalability. When coupled with the wide array of application domains such as architectural and jewelry decorative coatings, cutting tool and tooling hard coatings, as well as anti-reflective and filter optical layers, it becomes clear that each technology segment aligns with distinct end-use performance criteria.
Moreover, end-use industries spanning aerospace, automotive, electronics, medical devices, solar, and machinery each exhibit specific PVD requirements, driving material choices that range from carbide and diamond-like carbon to aluminum and titanium nitrides. Equipment configurations-encompassing control systems, power supplies, ion sources, and vacuum chambers-are tailored to meet source-type preferences, which include electron beam, ion beam, laser, magnetron, and thermal sources. Recognizing these interdependencies empowers stakeholders to anticipate demand shifts, optimize product portfolios, and invest in targeted process improvements that resonate with specialized market needs.
This comprehensive research report categorizes the Physical Vapor Deposition market into clearly defined segments, providing a detailed analysis of emerging trends and precise revenue forecasts to support strategic decision-making.
- Technology
- Application
- End Use Industry
- Material
- Equipment Type
- Source Type
Examining Regional Market Performance Trends and Growth Opportunities Shaping Global Adoption of Physical Vapor Deposition Solutions
Regional analysis underscores divergent growth trajectories for Physical Vapor Deposition solutions around the globe. In the Americas, established semiconductor hubs in the United States and Mexico are driving consistent demand for advanced deposition equipment, particularly as companies expand wafer fabrication capacity and automotive OEMs pursue lightweight alloy coatings. Federal initiatives promoting domestic semiconductor manufacturing and green initiatives within aerospace sectors further bolster market activity in North America.
In Europe, the Middle East, and Africa, automotive powertrain electrification and industrial machinery modernization are catalyzing interest in PVD-enhanced wear-resistant coatings, while optical coating applications benefit from robust photonics research clusters. Regulatory frameworks emphasizing carbon neutrality and circular economy principles encourage the adoption of energy-efficient vacuum systems. Across Asia-Pacific, the region’s dominance in consumer electronics production, solar panel manufacturing, and memory fabrication fosters rapid scaling of PVD equipment installations, making it the fastest-growing market for both standard and customized deposition solutions.
This comprehensive research report examines key regions that drive the evolution of the Physical Vapor Deposition market, offering deep insights into regional trends, growth factors, and industry developments that are influencing market performance.
- Americas
- Europe, Middle East & Africa
- Asia-Pacific
Highlighting Competitive Strategies and Innovations from Leading Physical Vapor Deposition Equipment Manufacturers and Suppliers
The competitive landscape of Physical Vapor Deposition is defined by a core group of equipment manufacturers and specialized suppliers innovating across system design, process control, and service offerings. Major players have accelerated their technology roadmaps, introducing modular platforms capable of handling multiple source types-such as magnetron and ion beam-in a single chamber to reduce footprint and cost of ownership. Strategic partnerships with semiconductor foundries, automotive OEMs, and optics producers are becoming increasingly prevalent, enabling co-development of next-generation coating recipes and rapid field validation.
At the same time, emerging vendors with niche expertise in areas like planar magnetron designs or advanced electron beam lithography equipment are carving out defensible market positions. Service providers offering turnkey installation, retrofit solutions, and predictive maintenance analytics are gaining traction, as customers seek end-to-end support to minimize downtime and extend equipment lifecycles. Collectively, these dynamics are intensifying the focus on innovation-driven differentiation and customer-centric business models within the broader PVD ecosystem.
This comprehensive research report delivers an in-depth overview of the principal market players in the Physical Vapor Deposition market, evaluating their market share, strategic initiatives, and competitive positioning to illuminate the factors shaping the competitive landscape.
- Applied Materials, Inc.
- Tokyo Electron Limited
- Lam Research Corporation
- Veeco Instruments Inc.
- Canon ANELVA Corporation
- Hitachi High-Tech Corporation
- AIXTRON SE
- ULVAC, Inc.
- Oerlikon Balzers Coating AG
- IHI Ionbond AG
Offering Practical Strategic Recommendations for Industry Leaders to Capitalize on Emerging Physical Vapor Deposition Market Trends
To navigate the evolving Physical Vapor Deposition landscape, industry leaders should prioritize strategic investments in localized manufacturing capabilities, collaborating with regional partners to circumvent tariff challenges and reduce supply chain complexity. Establishing assembly operations near major end-use clusters not only mitigates duty exposure but also enhances responsiveness to customer requirements and regulatory changes. Furthermore, advancing R&D investments in green PVD processes-such as low-temperature evaporation and plasma-enhanced deposition-will address sustainability mandates while differentiating offerings in competitive bidding scenarios.
In parallel, executives should strengthen cross-industry alliances, fostering joint innovation programs with semiconductor foundries and solar manufacturers to co-engineer next-generation film chemistries and deposition methodologies. Emphasizing digital transformation by integrating real-time monitoring and AI-driven process analytics can unlock higher equipment utilization and yield optimization. Finally, engaging proactively with policymakers and industry associations will ensure that tariff structures remain balanced, supporting domestic resilience without stifling access to critical global technologies.
Detailing Rigorous Research Methodology Underpinning Insights into the Physical Vapor Deposition Market Analysis Framework
This analysis is grounded in a multi-tiered research methodology combining exhaustive secondary research, primary stakeholder interviews, and quantitative data triangulation. Secondary sources encompassed peer-reviewed academic journals, patent filings, regulatory publications, and industry association reports to capture the latest technological developments and policy impacts. Primary research involved in-depth discussions with equipment manufacturers, end users across semiconductor, automotive, and solar sectors, as well as subject-matter experts in deposition process science.
Data points were validated through cross-referencing vendor financial disclosures, trade organization statistics, and USTR tariff schedules. The segmentation framework was constructed by mapping technology modalities, material classes, and end-use requirements to performance metrics and adoption rates. Finally, regional insights drew upon government incentive program analyses and import-export statistics to contextualize market momentum. This rigorous approach ensures that findings are both comprehensive and actionable for strategic decision-making.
Explore AI-driven insights for the Physical Vapor Deposition market with ResearchAI on our online platform, providing deeper, data-backed market analysis.
Ask ResearchAI anything
World's First Innovative Al for Market Research
Summarizing Key Takeaways and Future Outlook for Physical Vapor Deposition Technology and Market Evolution and Trajectories
The evolution of Physical Vapor Deposition technologies reflects an industry at the nexus of innovation, policy influence, and shifting demand patterns. As advanced materials requirements converge with sustainability imperatives, the market will increasingly reward solutions that deliver precision, scalability, and environmental stewardship. Tariff dynamics have introduced complexity, yet they also present a catalyst for reshoring and localized R&D that could fortify long-term competitiveness.
Looking forward, stakeholders should anticipate continued segmentation, with niche substrates and exotic material combinations driving specialized equipment development. Integrating digital capabilities-spanning sensor-based process control and predictive maintenance-will be paramount in unlocking operational efficiencies. By aligning strategic initiatives with industry transformation vectors and regional policy incentives, organizations can navigate uncertainties and capture growth opportunities within the vibrant Physical Vapor Deposition ecosystem.
This section provides a structured overview of the report, outlining key chapters and topics covered for easy reference in our Physical Vapor Deposition market comprehensive research report.
- Preface
- Research Methodology
- Executive Summary
- Market Overview
- Market Dynamics
- Market Insights
- Cumulative Impact of United States Tariffs 2025
- Physical Vapor Deposition Market, by Technology
- Physical Vapor Deposition Market, by Application
- Physical Vapor Deposition Market, by End Use Industry
- Physical Vapor Deposition Market, by Material
- Physical Vapor Deposition Market, by Equipment Type
- Physical Vapor Deposition Market, by Source Type
- Americas Physical Vapor Deposition Market
- Europe, Middle East & Africa Physical Vapor Deposition Market
- Asia-Pacific Physical Vapor Deposition Market
- Competitive Landscape
- ResearchAI
- ResearchStatistics
- ResearchContacts
- ResearchArticles
- Appendix
- List of Figures [Total: 30]
- List of Tables [Total: 1914 ]
Connect with Ketan Rohom to Access Comprehensive Physical Vapor Deposition Market Research Report and Tailored Strategic Support
Ready to take the next step in unlocking unparalleled insights into the Physical Vapor Deposition market? Reach out directly to Ketan Rohom, Associate Director, Sales & Marketing, to secure your comprehensive research report tailored to your strategic needs and competitive goals. Whether you are seeking in-depth data, expert recommendations, or customized scenario planning, this conversation will equip you with the foresight needed to make high-impact decisions. Engage now to gain exclusive access to actionable intelligence that will drive your organization’s next wave of innovation and growth.
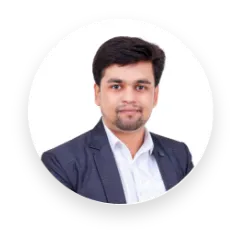
- How big is the Physical Vapor Deposition Market?
- What is the Physical Vapor Deposition Market growth?
- When do I get the report?
- In what format does this report get delivered to me?
- How long has 360iResearch been around?
- What if I have a question about your reports?
- Can I share this report with my team?
- Can I use your research in my presentation?