Exploring The Strategic Importance And Technological Evolution Of Plastic Cryogenic Pulverizers In Enabling High-Quality Material Processing And Efficiency
Cryogenic pulverization represents a groundbreaking approach to size reduction in polymer processing By employing liquid nitrogen to cool thermoplastics below their embrittlement temperature materials transition from ductile to brittle states enabling precise and efficient particle size reduction This process, often referred to as freezer milling or cryomilling, incorporates high-speed rotating blades within an insulated chamber while maintaining cryogenic temperatures to prevent softening and melting Such conditions ensure uniform particle distribution and minimal thermal degradation across a variety of plastic polymers
This technique yields particles as fine as -325 mesh without compromising material integrity While traditional grinding methods can generate heat-induced damage and increased energy consumption, cryogenic milling optimizes energy usage and maintains the functional properties of heat-sensitive materials As a result, stakeholders across sectors ranging from plastics recycling to advanced composites and specialty packaging increasingly prioritize this technology to meet stringent quality criteria and regulatory mandates for material purity and performance
Uncovering How Sustainability Demands Digitalization And Automation Are Driving Transformative Shifts In The Plastic Cryogenic Pulverizer Landscape
The plastic cryogenic pulverizer landscape has shifted dramatically as manufacturers integrate sustainable practices and digital controls into their operations Driven by a global mandate for reduced carbon footprints, enterprises are embracing cryogenic grinding not only for its capacity to preserve material properties but also for its alignment with energy-efficient production protocols By leveraging liquid nitrogen cooling rails and closed-loop systems, companies have minimized nitrogen consumption by up to 32 percent in pilot implementations while enhancing throughput and lowering operational costs
In parallel, Industry 4.0 principles are taking hold within pulverization facilities Advanced automation platforms now incorporate real-time monitoring through IoT sensors and machine learning algorithms that predict maintenance needs and optimize processing parameters Such integrations have reduced unplanned downtime by as much as 15 percent in early adopters while ensuring consistent particle-size distributions across diverse polymer grades
Moreover, the drive toward eco-friendly materials is reshaping equipment design With heightened regulatory scrutiny over emissions and waste handling, manufacturers of cryogenic systems are embedding advanced filtration modules and adopting inert gas recirculation strategies These innovations align with stringent air quality standards in sectors like pharmaceuticals and food processing while also catering to brand commitments on sustainability and circular economy principles
Ultimately, the transformative shifts within this domain reflect a broader industrial evolution where technology convergence and environmental stewardship define competitive differentiation
Analysing The Cumulative Impact Of New U.S. Tariff Measures In 2025 On Cost Structures Supply Chains And Investment In Cryogenic Pulverizing Equipment
On March 3, 2025, the United States enacted an executive order raising additional tariffs on imports from mainland China to 20 percent These measures, expanding upon prior Section 301 duties, apply to nearly all covered HTS classifications used in plastic machinery and components such as electrical motors, valves and control modules Consequently, the average duty on Chinese polyolefins and related processing equipment has climbed to approximately 26.5 percent, exacerbating input cost pressures for cryogenic pulverizer manufacturers and end users alike
Shortly thereafter, a universal baseline tariff of 10 percent on virtually all imports took effect in April 2025 This across-the-board levy overlays existing duties and further elevates landed costs for critical spare parts, nitrogen injection systems, and specialized tooling vital to maintaining cryogenic temperature controls These combined tariffs have compelled procurement teams to reevaluate global sourcing strategies and in many cases delay capital investments in pulverization assets
The plastics processing sector has felt the immediate repercussions of these policy shifts In a May 2025 poll by a leading industry publication, 87 percent of plastics processors reported experiencing customer indecision or order cancellations directly attributed to tariff uncertainty Almost half of respondents characterized the impact on business as “very negative,” underscoring pervasive concerns about cost volatility and supply chain disruption
Conversely, domestic machinery builders stand to gain from renewed onshoring interest Several U.S.-based equipment suppliers have reported upticks in inquiries as processors seek to mitigate tariff exposure by favoring domestically manufactured pulverizers However, the benefits of reshoring are tempered by ongoing challenges in securing specialized components and navigating complex exclusion processes established by the USTR, which could alleviate some duties through mid-2025
Revealing Critical Market Segmentation Insights Across Machine Types Materials End Users Capacity And Automation Levels Shaping Cryogenic Pulverizer Adoption
Based on machine type, distinctions between batch and continuous pulverization systems have emerged as a foundational determinant of operational flexibility and capital allocation Batch units, favored in research and small-scale production environments, afford precise control over processing parameters and rapid changeovers for material trials Conversely, continuous systems dominate high-volume recycling and extrusion feedstock preparation due to their ability to sustain constant throughput with minimal manual intervention
Drawing upon material segmentation, cryogenic pulverizers demonstrate distinct performance characteristics when processing polyethylene, polyethylene terephthalate, polypropylene or polyvinyl chloride Each polymer’s thermal properties dictate the required liquid nitrogen consumption and cooling conveyor conveyance speed, driving equipment customization to achieve optimal embrittlement and grind efficiency
End user industry segmentation further clarifies market dynamics Automotive applications, from exterior trim coatings to interior panel compounds, increasingly depend on sub-50 micron powders that preserve polymer properties under cryogenic conditions In construction, infrastructure projects demand heavy-duty, high-capacity units for reprocessed PVC and PP materials, while residential building product manufacturers lean on medium-capacity systems for precision additives and composite blends Electronic component producers, both in consumer and industrial electronics, require ultra-fine powders to enhance thermal conductivity and dielectric properties Finally, flexible and rigid packaging converters rely on continuous cryogenic milling to ensure consistent resin properties for film extrusion and mold filling
Capacity segmentation underscores that high-capacity pulverizers supply large-scale recyclers and OEM compounders seeking economies of scale Medium-capacity equipment aligns with mid-tier processors balancing throughput demands with floor space constraints Low-capacity models predominantly serve laboratory R&D and pilot production settings where versatile testing capabilities outweigh volume requirements
Automation level segmentation reveals a spectrum of operational models Fully automatic systems integrate advanced control panels with predictive maintenance alerts, enabling lights-out operations Semi-automatic configurations provide manual adjustment points for process engineers to intervene in real time, whereas manual machines continue to support bespoke processing environments where hands-on oversight remains indispensable
This comprehensive research report categorizes the Plastic Cryogenic Pulverizer market into clearly defined segments, providing a detailed analysis of emerging trends and precise revenue forecasts to support strategic decision-making.
- Machine Type
- Material
- End User Industry
- Capacity
- Automation Level
Highlighting Key Regional Dynamics In The Americas Europe Middle East Africa And AsiaPacific That Influence Cryogenic Pulverizer Deployment Trends
In the Americas, North America stands at the forefront of cryogenic pulverizer deployment Fueled by an ecosystem of advanced manufacturing clusters and stringent regulatory frameworks, U.S. and Canadian processors prioritize equipment that delivers both high throughput and compliance with environmental mandates Government incentives for recycling innovation and robust capital expenditure cycles in automotive, packaging and electronics sectors have cemented the region’s leadership in adopting next-generation cryogenic grinding technologies
Within Europe, Middle East and Africa, regulatory rigour and sustainability goals drive investment in energy-efficient pulverization platforms The European Union’s Fit for 55 package and emerging carbon border adjustments compel manufacturers to install cryogenic systems that offer lower nitrogen consumption and embedded carbon tracking Meanwhile, Middle East oil refineries and African polymer converters are beginning to integrate cryogenic grinding solutions as part of broader circular economy initiatives supported by regional development funds
Asia-Pacific is witnessing accelerated adoption driven by rapid industrialization and growing demand for high-performance materials China, India and Japan are investing heavily in cryogenic milling for applications in pharmaceuticals, food processing and automotive lightweighting Domestic innovation ecosystems and government-led technology parks offer subsidies for advanced manufacturing equipment, further catalyzing the installation of both batch and continuous cryogenic pulverization systems across the region
This comprehensive research report examines key regions that drive the evolution of the Plastic Cryogenic Pulverizer market, offering deep insights into regional trends, growth factors, and industry developments that are influencing market performance.
- Americas
- Europe, Middle East & Africa
- Asia-Pacific
Examining Market Leadership Strategies And Innovations Of Leading Manufacturers Shaping The Competitive Landscape Of Cryogenic Pulverization Technology
Leading equipment manufacturers have distinguished themselves through deep process engineering expertise and strategic investments in cryogenic technology Scherer GmbH pioneered liquid nitrogen heat exchanger designs that maintain consistent embrittlement temperatures for a wide range of thermoplastics, driving uniform particle-size distributions critical for high-value applications Pallmann Industries has optimized grinding disk geometries and feed rate controls to minimize energy losses while maximizing throughput Linde plc, leveraging its global industrial gas network, has advanced closed-loop nitrogen systems that deliver both environmental benefits and operational economies of scale
A cohort of specialized technology providers has further refined cryogenic pulverization processes Angstrom Advanced Inc. and Cryogenic Processing Solutions, Inc. focus on turnkey systems that integrate pre-cooling conveyors with in-line classification modules, reducing footprint and nitrogen consumption Glen Mills Inc. brings decades of laboratory and pilot-scale expertise, enabling rapid scale-up for R&D initiatives Herbold Meckesheim USA and Hosokawa Micron Powder Systems excel in modular plant configurations that facilitate maintenance access and ensure GMP compliance for pharmaceutical and food-grade applications
This comprehensive research report delivers an in-depth overview of the principal market players in the Plastic Cryogenic Pulverizer market, evaluating their market share, strategic initiatives, and competitive positioning to illuminate the factors shaping the competitive landscape.
- Hosokawa Alpine AG
- Industrial Pulverizing Systems, Inc.
- SPEX SamplePrep, LLC
- Pallmann Maschinenfabrik GmbH
- Jet Pulverizer Co., Inc.
- Glen Mills, Inc.
- Nara Machinery Co., Ltd.
- Retsch GmbH
- Kreyenborg GmbH & Co. KG
- Union Process, Inc.
Formulating Actionable Strategic Recommendations To Drive Innovation Sustainability And Resilience For Industry Leaders In Plastic Cryogenic Pulverizer Markets
Invest in advanced automation and IoT integration to elevate operational efficiency across pulverization facilities By deploying sensors within insulated grinding chambers and conveyor pre-coolers, leaders can harness real-time data streams to implement predictive maintenance, optimize nitrogen flow rates, and maintain consistent particle-size distributions Embracing machine learning algorithms to analyze wear patterns and process deviations will further reduce unplanned downtime while enhancing product quality
Accelerate sustainability by adopting closed-loop cooling systems and low-embodied-carbon materials for critical components When selecting cryogenic vessels, opt for designs that maximize nitrogen recovery and leverage recyclable alloys in construction to align with corporate ESG targets Encouraging collaboration between equipment suppliers and end users to develop customized carbon accounting methodologies will solidify environmental leadership and unlock potential tax incentives and rebates
Mitigate tariff exposure through proactive engagement with USTR exclusion processes and strategic supply chain diversification Pursue targeted exclusion requests for specialized machinery classified under HTS Chapters 84 and 85 to alleviate Section 301 duties while exploring domestic partnerships for critical components such as refrigeration units, control panels and sampling valves Establish collaborative frameworks with the government-backed Exclusions Program to secure interim relief through May 2025 and beyond
Cultivate innovation ecosystems by forging strategic alliances with research institutions and polymer technology centers Prioritize joint development agreements that co-invest in next-generation cryogenic pulverization research, focusing on hybrid cooling methods and ultra-fine particle capture Encourage cross-sector consortiums to share best practices, regulatory insights and pilot data, accelerating commercialization timelines and driving continuous improvement
Outlining A Rigorous Research Methodology Combining Primary Interviews Secondary Data Validation And Expert Triangulation To Ensure Analytical Robustness
Our research methodology integrates a multi-pronged approach beginning with in-depth primary interviews conducted with key stakeholders across the value chain including equipment OEMs, polymer processors, cryogenic gas suppliers and sustainability experts Secondary data was systematically gathered from industry white papers, regulatory filings and peer-reviewed journals to build a robust knowledge base We conducted rigorous data validation through cross-referencing public financial disclosures, patent registries and trade publications to ensure factual accuracy Triangulation of insights from these diverse sources, coupled with iterative expert panel reviews, underpins the credibility of our analysis and supports the strategic recommendations provided
Explore AI-driven insights for the Plastic Cryogenic Pulverizer market with ResearchAI on our online platform, providing deeper, data-backed market analysis.
Ask ResearchAI anything
World's First Innovative Al for Market Research
Synthesizing Core Findings And Emphasizing The Strategic Value Proposition Of Cryogenic Pulverization In Modern Materials Processing Frameworks
The convergence of sustainability imperatives, digital innovation and shifting trade dynamics has propelled plastic cryogenic pulverization to the forefront of material processing strategies Organizations that deploy advanced cryogenic systems realize superior particle-size control, minimal thermal degradation and enhanced operational resilience in the face of regulatory and economic volatility By aligning machine type and capacity with material and end-user requirements, firms can tailor solutions that meet specific application demands while optimizing cost structures and resource utilization
As regions across the Americas, EMEA and Asia-Pacific continue to prioritize high-performance manufacturing and circular economy objectives, the competitive landscape for cryogenic pulverizers will intensify Leading equipment providers must therefore balance technological differentiation with strategic supply chain agility, particularly in the context of escalating tariff regimes and sustainability mandates Continued investments in automation, closed-loop systems and collaborative R&D consortiums will define the next wave of innovation, ensuring that cryogenic pulverization remains a cornerstone of modern materials processing
This section provides a structured overview of the report, outlining key chapters and topics covered for easy reference in our Plastic Cryogenic Pulverizer market comprehensive research report.
- Preface
- Research Methodology
- Executive Summary
- Market Overview
- Market Dynamics
- Market Insights
- Cumulative Impact of United States Tariffs 2025
- Plastic Cryogenic Pulverizer Market, by Machine Type
- Plastic Cryogenic Pulverizer Market, by Material
- Plastic Cryogenic Pulverizer Market, by End User Industry
- Plastic Cryogenic Pulverizer Market, by Capacity
- Plastic Cryogenic Pulverizer Market, by Automation Level
- Americas Plastic Cryogenic Pulverizer Market
- Europe, Middle East & Africa Plastic Cryogenic Pulverizer Market
- Asia-Pacific Plastic Cryogenic Pulverizer Market
- Competitive Landscape
- ResearchAI
- ResearchStatistics
- ResearchContacts
- ResearchArticles
- Appendix
- List of Figures [Total: 28]
- List of Tables [Total: 908 ]
Connect Directly With Ketan Rohom Associate Director Sales And Marketing To Secure Your Customized Market Insight Report Today
Ready to elevate your strategy with precise market intelligence on the plastic cryogenic pulverizer sector How will advanced processing technologies shape your competitive advantage Reach out to Ketan Rohom Associate Director Sales and Marketing to secure your customized market research report and gain the actionable insights you need to drive growth and innovation today
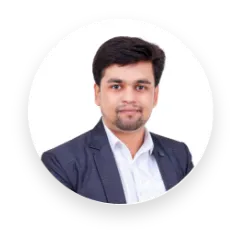
- When do I get the report?
- In what format does this report get delivered to me?
- How long has 360iResearch been around?
- What if I have a question about your reports?
- Can I share this report with my team?
- Can I use your research in my presentation?