Introduction: The Critical Role of Plastic Grease Separators
The plastic grease separator market stands at a pivotal juncture, driven by escalating environmental regulations and growing demands for efficient wastewater management. Stakeholders across commercial, industrial, and residential sectors recognize the critical role of grease separators in preventing sewer blockages, reducing maintenance costs, and ensuring compliance with health and safety standards. As regulatory bodies tighten discharge limits and municipalities invest in greener infrastructure, plastic grease separators offer a compelling combination of durability, lightweight handling, and chemical resistance.
Innovation in materials and design has accelerated performance improvements. Advances in high-density polymer formulations have enhanced structural strength while minimizing corrosion and chemical degradation. Meanwhile, modular designs facilitate rapid installation and maintenance, reducing downtime for end-users. The increasing adoption of automated cleaning mechanisms and sensor-based monitoring solutions underscores the industry’s shift toward intelligent, data-driven operations.
This report provides a comprehensive executive summary of key drivers reshaping the market landscape. By examining transformative shifts, tariff influences, segmentation dynamics, regional variations, leading players’ strategies, and actionable recommendations, decision-makers can chart a strategic path forward. The insights presented here equip industry leaders with a holistic understanding of current trends and emerging opportunities in the plastic grease separator sector.
Transformative Shifts Redefining the Market
The landscape of plastic grease separators is experiencing transformative shifts fueled by three major forces: sustainability mandates, digital integration, and cross-sector collaboration. First, stringent environmental regulations are pushing municipalities and facility operators to invest in systems that not only trap fats, oils, and grease but also ensure traceability and accountability. This regulatory pressure has accelerated the adoption of eco-friendly polymer composites and recyclable materials, aligning product lifecycles with circular economy principles.
Second, digital integration is redefining maintenance and performance monitoring. Sensor-based monitoring technologies now provide real-time data on flow rates, grease accumulation, and system health, enabling predictive maintenance and reducing unplanned downtime. The convergence of Internet of Things platforms with advanced analytics allows facility managers to optimize cleaning schedules, minimize labor costs, and extend separator life.
Finally, cross-sector collaboration between equipment manufacturers, software providers, and service firms is fostering end-to-end solutions. Partnerships are emerging that combine modular separator units with cloud-based monitoring dashboards and remote support services. As a result, end-users benefit from turnkey packages that streamline installation, compliance reporting, and in-field servicing. These shifts collectively underscore a market focused on smarter, greener, and more collaborative approaches to grease management.
Cumulative Impact of US Tariffs in 2025
The imposition of new tariffs on imported plastic components and finished separator units in 2025 has introduced both challenges and strategic realignments for manufacturers and distributors. Increased duties on key polymer resins have elevated raw material costs, compelling producers to reassess sourcing strategies and explore alternative supply chains. Some manufacturers are relocating certain production stages to domestic facilities, thereby mitigating tariff impacts while supporting regional job growth.
Meanwhile, importers have renegotiated contracts with overseas suppliers and sought tariff-exempt zones or bonded warehouses to defer or reduce duty payments. These operational adjustments have added complexity to inventory management and pricing models. To maintain competitive margins, several vendors are implementing value-added services-such as extended warranties, on-site training, and maintenance packages-that justify premium pricing without eroding demand.
Despite these headwinds, the higher cost base has incentivized investments in process efficiency. Automated production lines and advanced polymer compounding techniques are gaining traction, lowering per-unit costs over time. As the market adapts, the tariff-induced shift is likely to spur greater vertical integration and localized manufacturing networks.
Key Segmentation Insights Across Diverse Criteria
A nuanced segmentation analysis reveals distinct growth drivers and competitive dynamics across product types, capacities, materials, applications, installation modes, end-user industries, maintenance features, certification standards, and core technologies.
In terms of product type, automatic grease separators dominate high-throughput environments, while grease trap interceptors remain essential in legacy installations. Manual separators and passive units continue to serve budget-sensitive applications, though they are gradually being upgraded to automated systems to improve hygiene and reduce labor.
Capacity segmentation highlights the distinct needs of large units in industrial food processing facilities, medium units in institutional kitchens, and small units in residential or boutique restaurant settings. Material choices also influence buyer preferences: concrete separators are preferred for their robustness in heavy-duty applications, fiberglass for moderate chemical resistance, and plastic separators for corrosion resistance and ease of installation. Emerging reinforced composite materials promise to combine the best attributes of existing offerings, while stainless steel units retain a niche for extreme temperature or chemical environments.
Applications range from commercial kitchens in hotels and restaurants to specialized airport and transportation hub kitchens, which demand rapid installation and minimal maintenance disruption. Industrial facilities process high volumes of oily effluents, whereas institutional kitchens in schools and hospitals prioritize fail-safe operation. Residential installations, though smaller in scale, are witnessing rising interest in under-sink micro-separator units for home-based culinary ventures.
Above-ground separators offer straightforward servicing and are common in retrofit projects, whereas below-ground models preserve floor space in new builds. Within end-user industries, the food and beverage sector-covering bakeries, dairy processing plants, meat processing units, and restaurants-drives the bulk of demand. Renewable energy facilities are an emerging frontier, followed by oil and gas refineries, the pharmaceutical industry, and textile manufacturing, each with unique grease handling requirements.
Maintenance innovations distinguish market leaders: AI-driven predictive maintenance technologies forecast cleaning intervals; self-cleaning mechanisms automate service routines; sensor-based monitoring alerts maintenance teams to potential blockages; and manual cleaning remains relevant where capital expenditure is constrained.
Certification standards play a pivotal role in procurement decisions. CSA certification and NSF/ANSI 2 compliance govern North American markets, while EN1825 is the benchmark in Europe. International enterprises are preparing for forthcoming ISO grease separator standards. IAPMO listings further validate product safety and performance.
Finally, core technologies-centrifugal separation for high-efficiency grease removal, flotation technology for fine particle extraction, and traditional gravity-based systems-cater to different operational profiles and cost considerations. Understanding these overlapping segmentation layers allows market participants to tailor solutions and capture emerging demand pockets.
This comprehensive research report categorizes the Plastic Grease Separators market into clearly defined segments, providing a detailed analysis of emerging trends and precise revenue forecasts to support strategic decision-making.
- Product Type
- Product Capacity
- Material Type
- Application
- Installation Type
- End-User Industry
- Maintenance Features
- Certification Standard
- Technology
Key Regional Insights Shaping Demand
Regional dynamics reveal contrasting growth patterns. In the Americas, infrastructure modernization efforts and stringent municipal discharge regulations drive strong demand, particularly in urban centers. Public-private partnerships are financing wastewater upgrades, creating opportunities for turnkey grease management contracts. Meanwhile, Europe, Middle East & Africa exhibit heterogeneous trends: Western Europe’s mature markets focus on system retrofits and technology upgrades, while Gulf Cooperation Council nations invest heavily in airport and hospitality infrastructure, boosting demand for robust separators. African markets remain nascent but hold long-term potential as urban sanitation initiatives gain momentum. In the Asia-Pacific region, rapid industrialization and expanding food and beverage processing capacities in countries like China, India, and Southeast Asian nations catalyze equipment purchases. Moreover, government incentives for green infrastructure and strict coastal discharge limits underscore the urgency for advanced grease separator installations.
This comprehensive research report examines key regions that drive the evolution of the Plastic Grease Separators market, offering deep insights into regional trends, growth factors, and industry developments that are influencing market performance.
- Americas
- Asia-Pacific
- Europe, Middle East & Africa
Key Companies Insights and Competitive Strategies
Leading companies are leveraging diversified strategies to secure market share and differentiate their offerings. AC Plastics, Inc. emphasizes high-density polymer innovations, while ACO Australia tailors modular designs for local building codes. The various ACO divisions-ACO Building Drainage, ACO Building Drainage North America, Inc., ACO Building Drainage Solutions, ACO GMBH & Co KG, ACO Group, ACO Plumbing, ACO Polycrete Pty Ltd, ACO Systems Ltd, and ACO Systems USA Inc.-coordinate global R&D efforts to standardize performance benchmarks. Anderson Process focuses on customized interceptor solutions for food processing plants, and Flotronic Pumps Ltd integrates advanced pumping systems with separator units. GRAF UK Ltd capitalizes on lightweight, corrosion-resistant tanks, whereas Kingspan Group plc leverages its manufacturing scale to offer cost-competitive packages. Nemco Ltd excels in compact under-sink separators for commercial kitchens, and PREFA GmbH differentiates through patented flow control technologies. These firms are also forging strategic partnerships with service providers and software developers to create end-to-end maintenance ecosystems that enhance customer retention.
This comprehensive research report delivers an in-depth overview of the principal market players in the Plastic Grease Separators market, evaluating their market share, strategic initiatives, and competitive positioning to illuminate the factors shaping the competitive landscape.
- AC Plastics, Inc.
- ACO Australia
- ACO Building Drainage
- ACO Building Drainage North America, Inc.
- ACO Building Drainage Solutions
- ACO GMBH & Co KG
- ACO Group
- ACO Plumbing
- ACO Polycrete Pty Ltd
- ACO Systems Ltd
- ACO Systems USA Inc.
- Anderson Process
- Flotronic Pumps Ltd
- GRAF UK Ltd
- Kingspan Group plc
- Nemco Ltd
- PREFA GmbH
Actionable Recommendations for Industry Leaders
Industry leaders can capitalize on emerging opportunities and mitigate risks by pursuing the following actions:
• Integrate digital monitoring platforms. Embedding IoT sensors and analytics tools within grease separators enhances predictive maintenance, reduces downtime, and builds value-added service revenue streams.
• Diversify material sourcing. To navigate raw material cost volatility and tariff impacts, establish strategic partnerships with polymer suppliers and explore alternative composites that balance cost, durability, and environmental sustainability.
• Expand modular offerings. Designing plug-and-play separator units for both above-ground and below-ground installations streamlines project timelines, lowers installation costs, and appeals to retrofit and greenfield customers alike.
• Pursue strategic alliances. Collaborations with environmental service firms, software developers, and installation contractors create integrated solutions that differentiate brands and increase customer loyalty.
• Focus on certification readiness. Proactively obtaining relevant certifications-CSA, NSF/ANSI 2, EN1825, and forthcoming ISO-demonstrates compliance rigor and facilitates market entry across regions.
• Target high-growth segments. Prioritize product lines tailored to airport and transportation hub kitchens, renewable energy facilities, and emerging industrial zones in Asia-Pacific and the Middle East to capture early-mover advantages.
• Invest in R&D for next-gen composites. Advanced reinforced composite materials promise superior strength-to-weight ratios and recyclability, positioning innovators ahead of regulatory shifts toward circular economies.
Explore AI-driven insights for the Plastic Grease Separators market with ResearchAI on our online platform, providing deeper, data-backed market analysis.
Ask ResearchAI anything
World's First Innovative Al for Market Research
Conclusion: Navigating Complexity to Drive Growth
The plastic grease separator market is at an inflection point. Regulatory pressures, technological advances, and shifting supply chain dynamics are converging to create a landscape rich with opportunity and complexity. By embracing digital integration, optimizing segment-focused offerings, and forging collaborative ecosystems, companies can secure sustainable growth and competitive advantage. As market participants adapt to tariff implications and certification demands, those who innovate in materials science and service delivery will emerge as industry front-runners. Vigilant attention to regional nuances and end-user requirements will ensure solutions remain aligned with evolving environmental and operational imperatives.
This section provides a structured overview of the report, outlining key chapters and topics covered for easy reference in our Plastic Grease Separators market comprehensive research report.
- Preface
- Research Methodology
- Executive Summary
- Market Overview
- Market Dynamics
- Market Insights
- Cumulative Impact of United States Tariffs 2025
- Plastic Grease Separators Market, by Product Type
- Plastic Grease Separators Market, by Product Capacity
- Plastic Grease Separators Market, by Material Type
- Plastic Grease Separators Market, by Application
- Plastic Grease Separators Market, by Installation Type
- Plastic Grease Separators Market, by End-User Industry
- Plastic Grease Separators Market, by Maintenance Features
- Plastic Grease Separators Market, by Certification Standard
- Plastic Grease Separators Market, by Technology
- Americas Plastic Grease Separators Market
- Asia-Pacific Plastic Grease Separators Market
- Europe, Middle East & Africa Plastic Grease Separators Market
- Competitive Landscape
- ResearchAI
- ResearchStatistics
- ResearchContacts
- ResearchArticles
- Appendix
- List of Figures [Total: 34]
- List of Tables [Total: 471 ]
Call to Action: Secure Your Comprehensive Market Report Today
Ready to elevate your strategic outlook? Contact Ketan Rohom (Associate Director, Sales & Marketing) to acquire the full report and gain in-depth insights that will empower your next move in the plastic grease separator market.
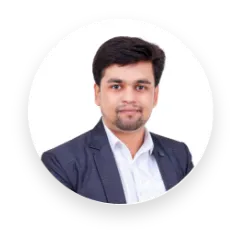
- When do I get the report?
- In what format does this report get delivered to me?
- How long has 360iResearch been around?
- What if I have a question about your reports?
- Can I share this report with my team?
- Can I use your research in my presentation?