Introduction to the Plastic Injection Moulding Machine Landscape
The plastic injection moulding machine market stands at a pivotal moment, defined by technological breakthroughs, evolving end-user demands, and shifting trade environments. Over recent years, manufacturers have embraced electric, hybrid, and hydraulic platforms to balance precision, energy efficiency, and throughput. Meanwhile, industries from automotive to packaging have raised performance expectations, driving innovation in control systems, material handling, and automation. As regulatory pressures intensify and sustainability becomes a cornerstone of competitive advantage, decision-makers must navigate a complex landscape of tariffs, supply-chain disruptions, and rapid digitalization. This introduction frames the key drivers and emerging trends that are reshaping capital investment decisions, operational strategies, and product roadmaps, setting the stage for deeper analysis of market dynamics, segmentation insights, and actionable recommendations.
Transformative Shifts Reshaping the Injection Moulding Ecosystem
Over the past decade, the plastic injection moulding sector has undergone transformative shifts, fueled by advances in drive technology, automation, and materials science. Electric machines, once a niche offering, now compete head-to-head with hydraulic presses by delivering precise control of induction and servo motors that optimize cycle times and energy consumption. At the same time, hybrid platforms integrate advanced control systems-whether automatic or manual-to tailor performance across high- and low-pressure operations. Analogous breakthroughs in multi-material, thin-wall, and two-platen architectures have enabled new applications in packaging, electronics, and medical devices. Concurrently, smart sensors and Industry 4.0 connectivity have elevated predictive maintenance, real-time monitoring, and process optimization. The converging impact of these innovations is redefining productivity benchmarks, cost structures, and value propositions across all end-user segments, from aftermarket automotive suppliers to OEMs producing disposable healthcare products.
Cumulative Impact of 2025 Tariff Adjustments on Industry Dynamics
In 2025, an array of tariff adjustments on key polymer and machinery imports has delivered a cumulative impact that reverberates across supply chains and pricing models. Increased duties on electric and hybrid presses have prompted manufacturers to reassess global sourcing strategies, redirecting procurement toward domestic or low-tariff zones. Meanwhile, end users in automotive and electronics are grappling with higher component costs, leading to narrower margins and longer lead times. Regions with favorable trade agreements have captured greater share, placing pressure on players in restricted markets to innovate around cost, energy consumption, and local content. As a result, machine builders and molders alike are accelerating automation, material recycling, and process intensification initiatives to counterbalance rising input costs and maintain competitiveness.
Key Segmentation Insights into Machine Types, End-User Needs, and Technology
A granular view of market segments highlights how machine type, end-user industry, clamping force range, technology, application, and channel type each influence competitive positioning and R&D priorities. Electric machines, differentiated by induction versus servo drive systems and high-efficiency versus standard energy consumption, cater to operations that prioritize precision and sustainability. Hybrid press offerings-defined by auto or manual control systems and pressure regimes spanning high, medium, and low-address manufacturers seeking a balance of speed and flexibility. Hydraulic platforms, categorized by heavy, medium, or light clamping force and single versus dual-cylinder architectures, remain a reliable choice for high-volume, heavy-duty molding. In parallel, end users from automotive aftersales and OEMs to electronics components and systems, as well as healthcare disposables and medical devices, demand bespoke solutions that align with product complexity and regulatory standards. Clamping force bands of 0–200, 201–500, 501–1000, and above 1000 tons define capacity requirements for diverse applications, while specialized technologies such as multi-material in-mold assembly, thin-wall container or lid production, and two-platen injection and mold systems unlock performance advantages in container, lid, and part manufacturing. Beyond machine architecture and application, ancillary processes like drying via dehumidifying or desiccant systems, heating and cooling cycles, and tooling selection between metal and plastic molds further influence overall productivity and quality. Finally, channel strategies-involving direct sales or distribution networks supported by retailers and specialized distributors-shape market reach and after-sales support capabilities.
This comprehensive research report categorizes the Plastic Injection Moulding Machine market into clearly defined segments, providing a detailed analysis of emerging trends and precise revenue forecasts to support strategic decision-making.
- Machine Type
- End User Industry
- Clamping Force Range
- Technology
- Application
- Channel Type
Key Regional Insights Driving Investment and Growth Strategies
Regional dynamics underscore contrasting growth drivers and competitive pressures across the Americas, Europe, Middle East & Africa, and Asia-Pacific. In the Americas, strong demand from automotive OEMs and packaging converters fuels adoption of high-tonnage hydraulic presses and energy-efficient electric platforms. Europe, the Middle East & Africa landscape prioritizes sustainability, leading to accelerated uptake of servo-driven machines and multi-material molding solutions to support circular-economy initiatives. Asia-Pacific remains the largest volume market, driven by expansive electronics manufacturing in Southeast Asia and rising medical device production in Japan and South Korea. Here, two-platen architectures and thin-wall technologies gain traction for consumer packaging and precision components. Each region’s tariff environment, energy pricing, and labor dynamics inform capital investment strategies, while local content requirements and infrastructure investments further differentiate market opportunities.
This comprehensive research report examines key regions that drive the evolution of the Plastic Injection Moulding Machine market, offering deep insights into regional trends, growth factors, and industry developments that are influencing market performance.
- Americas
- Asia-Pacific
- Europe, Middle East & Africa
Competitive Landscape and Leading Company Strategies
Leading machine builders are fortifying their portfolios through technological differentiation, global footprint expansion, and service excellence. ARBURG GmbH + Co KG continues to set benchmarks in electric injection moulding technology with modular drive systems. Engel Austria GmbH accelerates automation integration, focusing on servo-driven hybrid platforms for high-speed packaging lines. FANUC Corporation harnesses robotics and digital twin simulations to optimize process repeatability. Husky Injection Molding Systems Ltd. specializes in turnkey solutions for thin-wall containers and high-efficiency hot-runner tooling. KraussMaffei Group GmbH leverages its broad clamping force range to serve heavy-duty automotive applications, while Milacron Holdings Corp. emphasizes rapid tool change and energy-saving controls. Nissei Plastic Industrial Co., Ltd. distinguishes itself in two-platen and multi-material processing, and Sumitomo (SHI) Demag Plastics Machinery GmbH advances in situ recycling and electric drive systems. The Japan Steel Works, Ltd. (JSW) invests in large-tonnage hydraulic press capacity, and Toshiba Machine Co., Ltd. pushes boundaries in compact hybrid and servo solutions. Collectively, these players navigate trade headwinds, sustainability mandates, and digital transformation to deliver value across diverse channels and end-use industries.
This comprehensive research report delivers an in-depth overview of the principal market players in the Plastic Injection Moulding Machine market, evaluating their market share, strategic initiatives, and competitive positioning to illuminate the factors shaping the competitive landscape.
- ARBURG GmbH + Co KG
- Engel Austria GmbH
- FANUC Corporation
- Husky Injection Molding Systems Ltd.
- KraussMaffei Group GmbH
- Milacron Holdings Corp.
- Nissei Plastic Industrial Co., Ltd.
- Sumitomo (SHI) Demag Plastics Machinery GmbH
- The Japan Steel Works, Ltd. (JSW)
- Toshiba Machine Co., Ltd.
Actionable Recommendations for Industry Leaders to Seize Growth
Industry leaders should pursue a multi-pronged approach to thrive amid evolving market conditions. First, prioritize investment in electric and servo-driven systems that deliver quantifiable energy savings and precision control, addressing both sustainability goals and quality requirements. Second, deepen end-user partnerships in automotive, electronics, healthcare, and packaging to co-innovate application-specific solutions, leveraging advanced simulation and predictive analytics to reduce time to market. Third, optimize global supply chains by balancing regional manufacturing footprint with tariff-efficient sourcing, and explore onshore assembly or joint ventures to mitigate trade risks. Fourth, expand service offerings around predictive maintenance, remote monitoring, and digital training to enhance uptime and extend machine life. Finally, cultivate an agile innovation pipeline that integrates multi-material, thin-wall, and two-platen technologies, while aligning product roadmaps with emerging materials and recycling streams.
Explore AI-driven insights for the Plastic Injection Moulding Machine market with ResearchAI on our online platform, providing deeper, data-backed market analysis.
Ask ResearchAI anything
World's First Innovative Al for Market Research
Conclusion: Balancing Innovation, Efficiency, and Market Resilience
Navigating the complex landscape of plastic injection moulding demands a strategic blend of technological innovation, market agility, and customer-centric execution. By embracing advanced drive systems, forging collaborative partnerships, and optimizing regional footprints, manufacturers can offset tariff pressures and capitalize on sustainable growth vectors. A disciplined focus on digitalization, from process simulation to predictive maintenance, will underpin operational excellence and foster resilience against supply-chain disruptions. As end users demand ever-higher performance and compliance, machine builders that deliver integrated, turnkey solutions will solidify their competitive edge. Ultimately, a forward-leaning approach that balances short-term efficiency gains with long-term R&D investments will define market leaders of tomorrow.
This section provides a structured overview of the report, outlining key chapters and topics covered for easy reference in our Plastic Injection Moulding Machine market comprehensive research report.
- Preface
- Research Methodology
- Executive Summary
- Market Overview
- Market Dynamics
- Market Insights
- Cumulative Impact of United States Tariffs 2025
- Plastic Injection Moulding Machine Market, by Machine Type
- Plastic Injection Moulding Machine Market, by End User Industry
- Plastic Injection Moulding Machine Market, by Clamping Force Range
- Plastic Injection Moulding Machine Market, by Technology
- Plastic Injection Moulding Machine Market, by Application
- Plastic Injection Moulding Machine Market, by Channel Type
- Americas Plastic Injection Moulding Machine Market
- Asia-Pacific Plastic Injection Moulding Machine Market
- Europe, Middle East & Africa Plastic Injection Moulding Machine Market
- Competitive Landscape
- ResearchAI
- ResearchStatistics
- ResearchContacts
- ResearchArticles
- Appendix
- List of Figures [Total: 28]
- List of Tables [Total: 1120 ]
Call-To-Action: Connect with Ketan Rohom to Acquire the Full Market Study
To explore in-depth analysis and strategic recommendations tailored to your business needs, contact Ketan Rohom, Associate Director, Sales & Marketing, to secure your copy of the comprehensive market research report and gain the actionable insights required to stay ahead in the transforming injection moulding landscape.
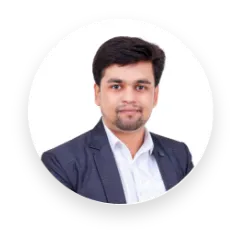
- When do I get the report?
- In what format does this report get delivered to me?
- How long has 360iResearch been around?
- What if I have a question about your reports?
- Can I share this report with my team?
- Can I use your research in my presentation?