Introduction to Plastics for Automotive Fuel Lines
Plastics have rapidly transformed the design and manufacture of automotive fuel lines by delivering exceptional weight reduction, corrosion resistance, and durability compared to traditional metal tubing. In an era defined by stringent emission regulations and the accelerating shift toward electrification, advanced polymer solutions are addressing critical performance demands while helping automakers achieve ambitious efficiency targets. Innovations in material chemistry, such as high-performance fluoropolymers and polyamides, now enable fuel line systems to withstand elevated temperatures, aggressive chemical exposure, and mechanical stress without compromising safety or reliability.
Concurrently, evolving end-user requirements and competitive pressures are driving a broader adoption of customized thermoplastic composites that balance cost-effectiveness with tailored mechanical and barrier properties. As supply chains become more complex and geopolitical factors influence raw material access, the integration of optimized manufacturing processes-ranging from precision blow molding to high-throughput extrusion-ensures consistent quality at scale. This introduction sets the stage for a deep dive into the transformative shifts shaping the plastics-for-fuel-lines landscape, the influence of emerging trade policies, and the strategic insights that industry leaders must consider to thrive in a rapidly evolving market.
Transformative Shifts Redefining the Fuel Line Landscape
The automotive fuel line segment is experiencing transformative shifts driven by a convergence of technological advancements, regulatory mandates, and evolving consumer preferences. First, the relentless push for vehicle lightweighting is propelling the development of next-generation polymers such as polyphenylene sulfide (PPS) and engineered polyoxymethylene (POM), which deliver high strength-to-weight ratios and robust chemical resistance. Second, more stringent emission norms globally-from EPA Tier 3 in North America to Euro 6 in Europe-have heightened the need for leakproof, corrosion-resistant fuel systems that minimize hydrocarbon permeation.
Additionally, the rapid ascent of electric vehicles is reshaping fuel line demand by reallocating polymer R&D toward cooling and thermal management applications, leveraging expertise in temperature-resistant and UV-tolerant materials. Supply chain dynamics are also in flux as manufacturers adopt nearshoring strategies and digital supply networks to bolster resilience against disruptions. Lastly, sustainability imperatives are steering material scientists toward bio-based and recyclable plastics, underscoring a full-circle transformation that transcends product performance to embrace environmental stewardship.
Cumulative Impact of United States Tariffs in 2025
By 2025, newly imposed tariffs on key polymer feedstocks and finished components have compounded cost pressures across the fuel line supply chain. These duties have prompted OEMs and tier suppliers to reevaluate sourcing strategies, favoring domestic manufacturers or low-tariff trade partners over previously established low-cost regions. As a result, material substitution has become a viable approach, with increased interest in locally produced fluoropolymers and polyamides that comply with tariff-inclusive landed cost targets.
Moreover, the cumulative impact of these tariffs has accelerated investments in vertical integration, enabling stakeholders to secure raw material supply and control manufacturing margins. Contract renegotiations are underway to adjust pricing formulas, passing a portion of increased landed costs downstream while preserving long-term partnership stability. Despite these headwinds, innovative process optimizations-such as waste-minimizing extrusion techniques-are helping to offset tariff-driven cost escalations, ensuring that performance standards remain uncompromised.
Key Segmentation Insights Across Multiple Dimensions
Deep market analysis reveals nuanced performance and application trends when examining plastics for automotive fuel lines across multiple segments. Material Type distinctions illuminate why fluoropolymers such as PCTFE and PTFE are prized for their exceptional barrier properties, while polyamide variants-PA 11, PA 12, and PA 6-balance flexibility and mechanical strength. Concurrently, polyoxymethylene provides dimensional stability under dynamic loads, and PPS endures high-temperature environments. Evaluating these materials by diameter size-large, medium, or small-further highlights the trade-offs between flow dynamics and pressure tolerance.
Vehicle Type segmentation uncovers differentiated demand patterns: heavy and light commercial vehicles demand robust, high-duty fuel lines, whereas passenger cars prioritize lightweight, cost-efficient solutions and electric vehicles-battery electric and plug-in hybrids-explore polymeric conduits for thermal management alongside fuel delivery. End-User analysis distinguishes aftermarket channels, where component suppliers and distributors focus on retrofit and replacement parts, from OEMs, whose collaborations with commercial and passenger vehicle manufacturers drive just-in-time production and stringent quality controls.
Manufacturing Process insights reveal that blow molding facilitates seamless, complex geometries, whereas extrusion yields continuous lengths ideal for high-volume runs; injection molding addresses intricate manifolds and connectors. Reinforcement Layer strategies contrast mono-layer constructions with multi-layer assemblies-two-layer or three-layer architectures-to optimize barrier performance and mechanical resilience. Sales Channel dynamics range from direct engagements with OEM engineering teams to indirect networks via dealers and online platforms.
Finally, Application assessments discriminate breather lines, fuel supply lines, and ventilation lines by their chemical exposure profiles and pressure regimes, while Performance Criteria segmentation-chemical and UV resistance, temperature resilience at high or low extremes-ensures regulatory compliance under EPA Tier 3, Euro 5, and Euro 6 standards. This comprehensive segmentation framework supports targeted product development and market positioning.
This comprehensive research report categorizes the Plastics for Automotive Fuel Lines market into clearly defined segments, providing a detailed analysis of emerging trends and precise revenue forecasts to support strategic decision-making.
- Material Type
- Vehicle Type
- Manufacturing Process
- Application
- End-User
- Performance Criteria
- Diameter Size
- Reinforcement Layer
- Emission Regulation Compliance
- Sales Channel
Key Regional Insights Shaping Market Dynamics
Regional variations in polymer demand and regulatory enforcement profoundly influence the automotive fuel line industry. In the Americas, stringent EPA Tier 3 mandates and a robust aftermarket infrastructure drive demand for high-barrier materials and retrofit solutions, while nearshoring initiatives boost domestic production of polyamide and fluoropolymer lines. Across Europe, the Middle East & Africa, Euro 5 and Euro 6 compliance requirements fuel adoption of advanced PPS and POM formulations, with sustainability directives prompting life-cycle assessments and recycled-content mandates.
Meanwhile, Asia-Pacific stands at the epicenter of manufacturing growth, with rapid expansion of electric vehicle platforms spurring demand for temperature-resistant plastics and multi-layer reinforcement systems. Local regulations in China and India encourage regional sourcing partnerships, further stimulating investments in blow molding and extrusion facilities. By understanding these regional nuances-regulatory landscapes, infrastructure maturity, and supply chain proximities-industry leaders can align production footprints and R&D priorities to capture growth opportunities effectively.
This comprehensive research report examines key regions that drive the evolution of the Plastics for Automotive Fuel Lines market, offering deep insights into regional trends, growth factors, and industry developments that are influencing market performance.
- Americas
- Asia-Pacific
- Europe, Middle East & Africa
Key Company Insights Driving Innovation and Growth
Market leadership is consolidated among established chemical and specialty polymer companies that continue to expand their foothold through strategic alliances and targeted R&D. Asahi Kasei Corporation leverages its proprietary polyamide technologies, while Ascend Performance Materials focuses on high-performance polyamides for demanding automotive applications. BASF SE and Covestro AG have broadened their portfolios with PPS and POM grades optimized for fuel line durability. Celanese Corporation’s collaborations on lightweight composite materials underscore a commitment to sustainable solutions.
DSM Engineering Plastics and DuPont de Nemours, Inc. remain at the forefront of fluoropolymer innovation, developing tailored PCTFE and PTFE formulations to satisfy tier-1 OEM specifications. EMS-Chemie Holding AG and Evonik Industries AG contribute niche expertise in UV and chemical resistance enhancements, whereas Lanxess AG and LyondellBasell Industries N.V. capitalize on integrated production capabilities to streamline cost structures. Mitsui Chemicals, Inc. and Radici Group are expanding capacity in Asia, and Royal DSM N.V. continues to pioneer bio-based polymer alternatives.
Complementing these efforts, RTP Company and SABIC are co-developing reinforced multilayer tubing solutions, with Solvay S.A. and Teijin Limited enhancing temperature resistance in extreme environments. Teknor Apex Company’s focus on customizable extrusion compounds and Toray Industries, Inc.’s carbon-fiber reinforced composites further diversify the competitive landscape. This constellation of players underscores a collective push toward innovation, sustainability, and global footprint optimization.
This comprehensive research report delivers an in-depth overview of the principal market players in the Plastics for Automotive Fuel Lines market, evaluating their market share, strategic initiatives, and competitive positioning to illuminate the factors shaping the competitive landscape.
- Asahi Kasei Corporation
- Ascend Performance Materials Corporate
- BASF SE
- Celanese Corporation
- Covestro AG
- DSM Engineering Plastics
- DuPont de Nemours, Inc.
- EMS-Chemie Holding AG
- Evonik Industries AG
- Lanxess AG
- LyondellBasell Industries N.V.
- Mitsui Chemicals, Inc.
- Radici Group
- Royal DSM N.V.
- RTP Company
- SABIC
- Solvay S.A.
- Teijin Limited
- Teknor Apex Company
- Toray Industries, Inc.
Actionable Recommendations for Industry Leaders
To navigate evolving market pressures and unlock growth, industry leaders should prioritize the following actions: First, accelerate development of next-generation polymers and multi-layer architectures that exceed stringent barrier and thermal standards, leveraging advanced compounding and additive technologies. Second, diversify sourcing strategies by establishing strategic partnerships with low-tariff suppliers and investing in regional manufacturing hubs to mitigate supply chain volatility.
Third, integrate digital manufacturing tools-such as process simulation and real-time quality monitoring-to reduce scrap rates and ensure consistent performance across high-volume extrusion and blow molding operations. Fourth, collaborate with regulatory bodies to shape future emission standards, ensuring new material solutions align with upcoming EPA Tier 4 and Euro 7 mandates. Fifth, embed sustainability criteria-such as bio-based content and recyclability-into product roadmaps to meet consumer and legislative expectations.
Finally, strengthen aftermarket channels through tailored service agreements and digital platforms that facilitate rapid order processing and predictive maintenance analytics. By executing these recommendations, organizations can enhance operational resilience, meet evolving performance requirements, and position themselves as trusted partners in the automotive ecosystem.
Explore AI-driven insights for the Plastics for Automotive Fuel Lines market with ResearchAI on our online platform, providing deeper, data-backed market analysis.
Ask ResearchAI anything
World's First Innovative Al for Market Research
Conclusion and Future Outlook
The automotive fuel line plastics market stands at a pivotal juncture, defined by rapid technological innovation, evolving regulatory frameworks, and shifting global trade dynamics. As demand patterns diverge across vehicle types-from heavy commercial fleets to next-generation electric platforms-material engineers and supply chain strategists must collaborate to deliver solutions that optimize performance, cost, and sustainability. By embracing advanced polymer chemistries, modernizing manufacturing processes, and adapting to regional market requirements, stakeholders will be well-positioned to capitalize on emerging opportunities.
Continued investment in R&D, coupled with proactive engagement in tariff mitigation and regulatory planning, will accelerate the deployment of high-performance, eco-efficient fuel line systems. The convergence of these efforts will not only meet current industry challenges but also pave the way for future innovations that redefine the role of plastics in automotive applications.
This section provides a structured overview of the report, outlining key chapters and topics covered for easy reference in our Plastics for Automotive Fuel Lines market comprehensive research report.
- Preface
- Research Methodology
- Executive Summary
- Market Overview
- Market Dynamics
- Market Insights
- Cumulative Impact of United States Tariffs 2025
- Plastics for Automotive Fuel Lines Market, by Material Type
- Plastics for Automotive Fuel Lines Market, by Vehicle Type
- Plastics for Automotive Fuel Lines Market, by Manufacturing Process
- Plastics for Automotive Fuel Lines Market, by Application
- Plastics for Automotive Fuel Lines Market, by End-User
- Plastics for Automotive Fuel Lines Market, by Performance Criteria
- Plastics for Automotive Fuel Lines Market, by Diameter Size
- Plastics for Automotive Fuel Lines Market, by Reinforcement Layer
- Plastics for Automotive Fuel Lines Market, by Emission Regulation Compliance
- Plastics for Automotive Fuel Lines Market, by Sales Channel
- Americas Plastics for Automotive Fuel Lines Market
- Asia-Pacific Plastics for Automotive Fuel Lines Market
- Europe, Middle East & Africa Plastics for Automotive Fuel Lines Market
- Competitive Landscape
- ResearchAI
- ResearchStatistics
- ResearchContacts
- ResearchArticles
- Appendix
- List of Figures [Total: 36]
- List of Tables [Total: 856 ]
Call-To-Action: Connect with Our Associate Director for Full Report Access
To access the comprehensive market research report and gain actionable insights tailored to your strategic objectives, reach out to Ketan Rohom, Associate Director, Sales & Marketing. Engage with an expert to explore detailed analysis, segmentation data, and growth strategies that will guide your next phase of development and investment.
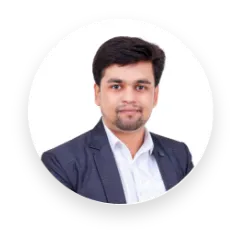
- When do I get the report?
- In what format does this report get delivered to me?
- How long has 360iResearch been around?
- What if I have a question about your reports?
- Can I share this report with my team?
- Can I use your research in my presentation?