Introduction to the Polycrystalline Diamond Cutting Tool Market
Polycrystalline diamond (PCD) cutting tools have emerged as a cornerstone of modern machining operations, delivering exceptional hardness, wear resistance, and thermal conductivity. These attributes enable manufacturers to achieve the ultra-tight tolerances and surface finishes demanded by industries such as aerospace, automotive, electronics, and oil & gas. In aerospace, PCD tools ensure the integrity of engine components and wing structures under extreme stress and temperatures. In automotive applications, they drive efficiency in braking systems, engine parts, and transmission components, reducing downtime and extending service intervals. Electronics manufacturers rely on PCD cutting edges to delicately shape microchip substrates and printed circuit boards with nanometer-level accuracy, while oil & gas operators use them for durable exploration and refining equipment. As global production cycles accelerate and materials grow more complex, the imperative for tooling solutions that balance precision with productivity intensifies. This introduction frames the strategic importance of PCD cutting tools in high-value manufacturing sectors and sets the stage for a deeper examination of the technological, economic, and regulatory forces reshaping this critical market segment.
Transformative Shifts Reshaping the PCD Cutting Tool Landscape
Over the past decade, a series of transformative shifts has upended the polycrystalline diamond cutting tool landscape. First, the rise of hybrid and composite materials-carbon-fiber-reinforced polymers, high-temperature alloys, and metal matrix composites-has driven tool designers to optimize coating chemistries and substrate architectures for unprecedented wear resistance. Concurrently, Industry 4.0 integration has introduced real-time tool monitoring, in-machine analytics, and predictive maintenance, enabling manufacturers to move from reactive change-outs to data-driven lifecycle management. Moreover, sustainability mandates and circular-economy initiatives have elevated recyclable tool substrates and environmentally friendly coatings from niche concepts to strategic imperatives. Geopolitical realignments have added another layer of complexity, prompting supply chain diversification and near-shoring strategies to mitigate tariff exposure and raw diamond sourcing risks. Finally, advancements in additive manufacturing have begun to intersect with PCD tooling, allowing for bespoke geometries and internal cooling channels that were previously unattainable. Together, these shifts demand that stakeholders adopt agile R&D programs, forge cross-sector partnerships, and continuously recalibrate their manufacturing footprints to maintain a competitive edge.
Cumulative Effects of U.S. Tariffs Post-2025 on PCD Tools
With the United States implementing new tariff structures in 2025, import duties on polycrystalline diamond cutting tools and raw diamond feedstock have risen substantially. The immediate consequence has been a marked increase in landed costs for manufacturers dependent on overseas suppliers, intensifying pressure on profit margins. In response, several tier-one tool producers have accelerated domestic capacity expansions and pursued strategic alliances with synthetic diamond manufacturers to secure duty-exempt supply channels. At the same time, pricing pressure cascades downstream; machine shops and contract manufacturers confront tighter budgets, prompting longer tool dwell times and higher demands for refurbishing services. On a global scale, these tariffs have triggered supply chain realignment, with European and Asia-Pacific producers vying to fill the gap in North American markets. Consequently, stakeholders must balance the cost advantages of alternative sourcing against potential disruptions in quality consistency and lead times. As a result, portfolio managers and procurement leaders now prioritize supplier diversification, vertical integration, and contractual safeguards to navigate the evolving tariff environment.
Key Insights from Comprehensive Market Segmentation
A granular segmentation analysis illustrates the multifaceted nature of the PCD cutting tool market. From an application standpoint, aerospace players rely heavily on engine component and wing structure machining, while automotive manufacturers focus on braking systems, engine parts and transmission components. In electronics, microchip manufacturing and printed circuit boards define precise cutting requirements, whereas oil & gas operators demand robust exploration and refining tooling solutions. By tool type, the industry divides into boring tools covering diameter and precision boring, drilling tools encompassing deep hole and high-speed drills, milling tools ranging from end mills to face mills, and turning tools spanning finishing turning and rough turning operations. End users segment into construction companies engaged in building renovation and infrastructure development, industrial equipment manufacturers producing heavy machinery and precision tools, and medical device manufacturers crafting diagnostic and surgical equipment. Material type further bifurcates into natural diamond-bort quality and gem quality-and synthetic diamond produced via chemical vapor deposition or high pressure-high temperature processes. Coating types include diamond coated with multi-layer or single layer approaches, and non-diamond coated featuring ceramic or tungsten carbide finishes. Sales channels are split between direct sales through company-owned outlets or online platforms and distributor networks comprised of global and regional partners. Finally, customer type distinguishes aftermarket services for maintenance and spare parts from OEMs serving aerospace and automotive original equipment manufacturers.
This comprehensive research report categorizes the Polycrystalline Diamond Cutting Tool market into clearly defined segments, providing a detailed analysis of emerging trends and precise revenue forecasts to support strategic decision-making.
- Application
- Tool Type
- End User
- Material Type
- Coating Type
- Sales Channel
- Customer Type
Critical Regional Dynamics Driving Market Growth
Regional dynamics underscore how geography shapes demand for PCD cutting tools. In the Americas, a mature aerospace and automotive base drives consistent investment in high-precision engine and chassis components, while robust oil & gas exploration supports heavy-duty tool applications. Meanwhile, direct sales networks and distributor partnerships ensure rapid service and localized technical support. In Europe, Middle East & Africa, the precision engineering tradition in central Europe converges with rising infrastructure projects in the Middle East and North Africa, nurturing demand for both micro-machining in electronics and large-scale boring in construction. Significant aftermarket services extend tool lifecycles, reflecting stringent sustainability goals. Across Asia-Pacific, surging consumer electronics and mobile device production fuel microchip and printed circuit board tooling needs, while rapid industrialization in China and India catalyzes growth in heavy machinery and refinery equipment. Distributor sales dominate, but online channels and direct outreach are gaining traction as manufacturers seek to optimize lead times in a high-pressure cost environment.
This comprehensive research report examines key regions that drive the evolution of the Polycrystalline Diamond Cutting Tool market, offering deep insights into regional trends, growth factors, and industry developments that are influencing market performance.
- Americas
- Asia-Pacific
- Europe, Middle East & Africa
Competitive Intelligence: Major Players and Strategic Moves
The competitive landscape features a blend of global conglomerates and specialized innovators. BIG Kaiser Precision Tooling Inc. leads in modular toolholding and highly accurate boring systems, while Element Six sets the benchmark for advanced synthetic diamond materials. Guhring Inc. commands attention in drilling solutions optimized for high-speed and deep-hole applications, and IMCO Carbide Tool Inc. balances carbide and PCD expertise for versatile milling and turning operations. ISRA VISION GmbH integrates optical inspection systems to enhance quality control across tool production lines. In Asia, Jiangsu H&Q Precision Tools delivers cost-effective solutions tailored to domestic demand, and Shenzhen Joeben Diamond Cutting Tools Co., Ltd. drives rapid innovation cycles in China’s tooling sector. Kennametal Inc. and Kyocera Corporation offer comprehensive portfolios spanning ceramic, carbide and PCD coatings, whereas Mapal Group and Mikron Tool SA Agno provide Swiss-engineered micro-machining systems. Precorp, Inc. specializes in custom PCD inserts, Sandvik AB and Seco Tools AB lead in composite and multi-layer tooling technologies, Sumitomo Electric Industries, Ltd. leverages its electrical expertise to refine PCD substrates, Union Tool Co. excels in micro end mills, and Walter AG delivers high-performance solid and indexable tool solutions. Collectively, these players define the market through continuous R&D, strategic partnerships and vertical integration.
This comprehensive research report delivers an in-depth overview of the principal market players in the Polycrystalline Diamond Cutting Tool market, evaluating their market share, strategic initiatives, and competitive positioning to illuminate the factors shaping the competitive landscape.
- BIG Kaiser Precision Tooling Inc.
- Element Six
- Guhring Inc.
- IMCO Carbide Tool Inc.
- ISRA VISION GmbH
- Jiangsu H&Q Precision Tools
- Kennametal Inc.
- Kyocera Corporation
- Mapal Group
- Mikron Tool SA Agno
- Precorp, Inc.
- Sandvik AB
- Seco Tools AB
- ShenZhen Joeben Diamond Cutting Tools Co., Ltd.
- Sumitomo Electric Industries, Ltd.
- Union Tool Co.
- Walter AG
Actionable Recommendations for Industry Leadership
Industry leaders must pursue a multi-pronged strategy to sustain growth and resilience. First, they should accelerate the development of advanced tool coatings and substrate enhancements to meet rising demands for higher feed rates and extended tool life, particularly in abrasive and high-temperature environments. Second, investing in localized manufacturing footprint expansions or joint ventures can mitigate tariff risks and reduce lead times, ensuring supply chain continuity. Third, forging collaborations with material science institutions and additive manufacturing specialists can unlock novel tool geometries and performance improvements. Fourth, integrating digital ecosystems-real-time tool monitoring, data analytics dashboards and AI-driven maintenance scheduling-will transition operations from reactive to predictive models. Fifth, embedding circular-economy principles through tool refurbishing programs, take-back schemes and recyclable substrate initiatives can align offerings with tightening environmental regulations and customer sustainability targets. By balancing technical innovation with strategic partnerships and operational agility, industry leaders can capitalize on emergent opportunities and fortify their market positions.
Explore AI-driven insights for the Polycrystalline Diamond Cutting Tool market with ResearchAI on our online platform, providing deeper, data-backed market analysis.
Ask ResearchAI anything
World's First Innovative Al for Market Research
Conclusion: Navigating Complexity and Capitalizing on Trends
In conclusion, the polycrystalline diamond cutting tool market sits at the nexus of material innovation, digital transformation and shifting global trade dynamics. The convergence of novel composite substrates, real-time data analytics and environmental mandates has elevated expectations for tool performance, lifecycle management and end-to-end sustainability. Meanwhile, tariff developments underscore the critical importance of supply chain diversification and strategic localization. As segmentation insights reveal diverse requirements across applications, tool types and end-users, stakeholders must adopt nuanced go-to-market approaches that address the unique needs of aerospace, automotive, electronics, oil & gas and medical device manufacturing. Competitive intelligence highlights the benefits of merging traditional precision engineering expertise with cutting-edge material science partnerships. Ultimately, success will favor those who marry agile R&D pipelines with robust digital platforms and environmentally conscious practices, enabling them to deliver differentiated value in an increasingly complex and dynamic marketplace.
This section provides a structured overview of the report, outlining key chapters and topics covered for easy reference in our Polycrystalline Diamond Cutting Tool market comprehensive research report.
- Preface
- Research Methodology
- Executive Summary
- Market Overview
- Market Dynamics
- Market Insights
- Cumulative Impact of United States Tariffs 2025
- Polycrystalline Diamond Cutting Tool Market, by Application
- Polycrystalline Diamond Cutting Tool Market, by Tool Type
- Polycrystalline Diamond Cutting Tool Market, by End User
- Polycrystalline Diamond Cutting Tool Market, by Material Type
- Polycrystalline Diamond Cutting Tool Market, by Coating Type
- Polycrystalline Diamond Cutting Tool Market, by Sales Channel
- Polycrystalline Diamond Cutting Tool Market, by Customer Type
- Americas Polycrystalline Diamond Cutting Tool Market
- Asia-Pacific Polycrystalline Diamond Cutting Tool Market
- Europe, Middle East & Africa Polycrystalline Diamond Cutting Tool Market
- Competitive Landscape
- ResearchAI
- ResearchStatistics
- ResearchContacts
- ResearchArticles
- Appendix
- List of Figures [Total: 30]
- List of Tables [Total: 1161 ]
Next Steps: Secure the Complete Market Research Report
To gain access to the full breadth of market intelligence, in-depth regional analysis and proprietary competitive benchmarking, reach out to Ketan Rohom, Associate Director, Sales & Marketing. Ketan will guide you through tailored research packages that align with your strategic priorities and equip you with actionable insights needed to outpace rivals. Contact him today to secure a comprehensive report and position your organization for long-term success in the polycrystalline diamond cutting tool sector.
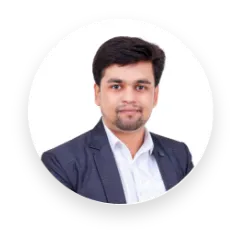
- When do I get the report?
- In what format does this report get delivered to me?
- How long has 360iResearch been around?
- What if I have a question about your reports?
- Can I share this report with my team?
- Can I use your research in my presentation?