The Polydimethylsiloxane Market size was estimated at USD 10.46 billion in 2024 and expected to reach USD 11.64 billion in 2025, at a CAGR 10.91% to reach USD 19.48 billion by 2030.

Unlocking the Potential of Polydimethylsiloxane in a Dynamic Market
Polydimethylsiloxane has emerged as a cornerstone material across countless industries thanks to its unparalleled versatility, thermal stability, and chemical inertness. Known more commonly as PDMS, this silicone-based polymer delivers remarkable performance in applications ranging from high-precision medical devices to advanced electronics and industrial lubricants. Its unique molecular structure imparts exceptional flexibility, hydrophobicity, and dielectric properties, making it a preferred choice for formulators and engineers seeking reliability under extreme conditions.
As global demand for high-performance materials continues to accelerate, polydimethylsiloxane is poised to play an even more significant role in driving innovation. Key sectors such as automotive manufacturing and personal care are exploring novel PDMS formulations to enhance product functionality and sustainability. Meanwhile, regulatory bodies worldwide are tightening standards around chemical safety and environmental impact, underscoring the importance of materials that combine safety with superior performance.
This executive summary offers a comprehensive exploration of the current polydimethylsiloxane market. It sets the stage with core industry dynamics, examines transformative shifts, evaluates the impact of new trade measures, and delivers deep segmentation and regional insights. Ultimately, this introduction establishes the foundation for strategic action and informed decision-making in a rapidly evolving landscape.
Emerging Forces Reshaping the Polydimethylsiloxane Landscape
The polydimethylsiloxane landscape is undergoing a series of transformative shifts that are redefining competitive benchmarks and strategic priorities. Advances in green chemistry are driving formulators to develop more sustainable PDMS variants, leveraging bio-based feedstocks and waste-reduction techniques. Concurrently, regulatory agencies in North America and Europe have introduced stricter compliance requirements for volatile organic compounds and cross-border chemical shipments, compelling manufacturers to optimize their processes and supply chains.
Technological breakthroughs are also reshaping end-use applications. In the electronics sector, innovations in thermal interface materials and potting compounds are enhancing heat management in miniaturized circuit boards. In the medical arena, novel PDMS elastomers with tailored mechanical properties are enabling the next generation of implantable devices. These developments are accompanied by digital transformation within manufacturing, where predictive maintenance and real-time quality monitoring systems ensure consistent production of high-purity PDMS grades.
Taken together, these forces are converging to elevate performance standards, intensify competitive dynamics, and accelerate demand for specialized PDMS formulations. As a result, organizations that can adapt swiftly to shifting regulations, embrace sustainable practices, and invest in cutting-edge R&D will secure a decisive advantage in the evolving market.
Navigating the Wave of United States Tariffs in 2025
The introduction of new United States tariffs in 2025 has added complexity to the global polydimethylsiloxane supply chain and pricing structures. By imposing levies on key silicone raw materials and certain intermediate products, these measures have increased production costs across North American manufacturing hubs. Domestic producers have faced pressure to absorb part of these costs, while import-dependent manufacturers have encountered higher upfront expenditure for critical feedstocks.
This tariff landscape has prompted several strategic responses. Some suppliers have relocated portions of their value chains to tariff-exempt jurisdictions, redirecting production to markets with preferential trade agreements. Others have negotiated long-term contracts with raw material vendors to lock in prices and mitigate volatility. At the same time, a growing number of end users are exploring alternative sources of PDMS, including specialized regional producers in Asia-Pacific and Europe, to diversify their procurement strategies.
Despite the immediate cost implications, these tariff-induced shifts are strengthening supply chain resilience over the medium term. Companies that adapt through geographic realignment, strategic partnerships, and advanced cost management frameworks will be better positioned to navigate ongoing trade uncertainties and maintain competitive pricing for their polydimethylsiloxane-based offerings.
Decoding Market Segments for Strategic Advantage
A nuanced understanding of market segments is critical for developing targeted product and marketing strategies. The polydimethylsiloxane market is delineated by distinct product types that each present unique performance attributes and application profiles. Elastomer grades exhibit remarkable elasticity for sealing and gasket applications, while emulsion variants deliver stable colloidal dispersions ideal for coatings. Fluid grades encompass heat transfer fluids, hydraulic fluids, and vacuum pump fluids, each tailored to precise viscosity and thermal requirements. Gum forms provide high-consistency polymers for molding and extrusion processes, and resin grades serve as reactive intermediates in advanced material synthesis.
Beyond product form, application segmentation reveals opportunities across diverse industrial sectors. In automotive manufacturing, PDMS compounds enhance fuel system reliability and sensor performance. The construction sector leverages silicone-based coatings alongside sealants and adhesives to improve building envelope durability. Electronics and electrical uses span dielectric applications, potting compounds, and thermal interface materials that manage heat in high-power devices. Industrial processes incorporate PDMS as lubricants, process fluids, and release agents to optimize machinery uptime. In the medical field, polydimethylsiloxane is integral to diagnostic equipment and implantable devices, while the personal care and cosmetics markets favor formulations for color cosmetics, hair treatments, and skin-care products due to their gentle skin compatibility.
End-use industries further refine these insights by aligning PDMS properties with sector-specific demands. The automotive, construction, cosmetics, food & beverage, oil & gas, and pharmaceutical segments each require calibrated viscosity grades-ranging from low-viscosity fluids for precise dosing to high-viscosity polymers for robust sealing. Distribution channels play a pivotal role in market reach, with direct sales fostering bespoke technical support, distributors ensuring broad regional coverage, and online platforms catering to agile procurement needs.
This comprehensive research report categorizes the Polydimethylsiloxane market into clearly defined segments, providing a detailed analysis of emerging trends and precise revenue forecasts to support strategic decision-making.
- Product Type
- Application
- End Use Industry
- Viscosity Grade
- Distribution Channel
Regional Dynamics Driving Polydimethylsiloxane Demand
Regional market dynamics are shaped by local regulations, infrastructure capabilities, and end-user demand patterns. In the Americas, robust growth in automotive manufacturing and personal care products has spurred demand for specialty PDMS formulations. Leading producers have expanded capacity in the Gulf Coast region to service both domestic and export markets, aligning with North American regulatory frameworks that emphasize product safety and environmental stewardship.
The Europe, Middle East & Africa region demonstrates a strong emphasis on sustainability and low-VOC solutions. European chemical hubs are pioneering bio-derived silicone routes, and Middle Eastern producers are investing in downstream PDMS integration to capture value from their native feedstock resources. Across Africa, nascent infrastructure development is opening new avenues for silicone-based construction materials and industrial fluids, supported by regional trade agreements that facilitate cross-border chemical distribution.
Asia-Pacific remains a dynamic hotbed of innovation and production scale-up. Rapid expansion of electronics manufacturing in East Asia has driven significant uptake of high-performance thermal interface materials and dielectric compounds. At the same time, emerging markets in Southeast Asia and Oceania are witnessing increased investment in food & beverage processing and pharmaceutical packaging applications, reinforcing the strategic importance of localized PDMS supply chains.
This comprehensive research report examines key regions that drive the evolution of the Polydimethylsiloxane market, offering deep insights into regional trends, growth factors, and industry developments that are influencing market performance.
- Americas
- Europe, Middle East & Africa
- Asia-Pacific
Competitive Outlook and Leading Industry Players
The competitive landscape is dominated by a cohort of well-established chemical companies that leverage global manufacturing networks and deep technical expertise. One leading player has consolidated its position through targeted acquisitions of specialty silicone firms, augmenting its portfolio with novel high-performance grades. Another major producer has focused on capacity expansions in emerging markets while simultaneously advancing its sustainable product line through partnerships with universities and research institutes.
A different group of companies has distinguished itself by investing heavily in application-driven innovation, collaborating with end users to co-develop bespoke formulations for medical devices and advanced electronics. These producers emphasize rapid application engineering services and technical support to differentiate their offerings. Meanwhile, regional silicone manufacturers are capturing local market share by optimizing cost structures and leveraging government incentives to increase downstream integration.
Across the board, leading firms are navigating the challenges of raw material volatility and regulatory complexity by establishing strategic alliances with feedstock suppliers and logistics partners. By combining supply chain resilience with continuous product innovation, these companies are setting new benchmarks for performance, sustainability, and customer responsiveness in the polydimethylsiloxane sector.
This comprehensive research report delivers an in-depth overview of the principal market players in the Polydimethylsiloxane market, evaluating their market share, strategic initiatives, and competitive positioning to illuminate the factors shaping the competitive landscape.
- Dow Inc.
- Wacker Chemie AG
- Shin-Etsu Chemical Co., Ltd.
- Momentive Performance Materials Inc.
- Evonik Industries AG
- Elkem ASA
- Bluestar Silicones International Pte Ltd
- Gelest Inc.
- NUSIL Technology LLC
- Siltech Corporation
Strategic Actions for Industry Leaders to Thrive
Industry leaders can secure a lasting competitive edge by prioritizing targeted R&D investments that address evolving application requirements. By establishing dedicated innovation centers focused on next-generation PDMS chemistries, companies will accelerate the development of biodegradable and ultra-low volatility variants that resonate with sustainability mandates. At the same time, implementing flexible manufacturing systems will enable rapid scale-up of niche product lines in response to shifting customer demands.
To mitigate trade uncertainties and raw material cost pressures, organizations should diversify their sourcing strategies by forging partnerships with regional feedstock producers and qualifying alternative supply channels. Integrating advanced analytics into procurement and inventory management processes will further enhance visibility into cost trends and demand fluctuations, supporting more agile decision-making. In parallel, companies must strengthen their sustainability credentials through transparent life-cycle assessments and third-party certifications, thereby reinforcing their value proposition to environmentally conscious end users.
Finally, fostering collaborative relationships with key accounts-particularly in high-growth sectors like electronics and medical devices-will unlock co-development opportunities and deepen customer loyalty. By offering integrated technical services and joint innovation roadmaps, industry leaders can transform transactional supply agreements into strategic partnerships that drive both revenue growth and market leadership.
Rigorous Research Approach for Market Clarity
This research draws on a rigorous combination of primary and secondary data sources to ensure robust, actionable insights. Initially, an extensive review of industry publications, patent filings, regulatory databases, and trade statistics established the macro-level context for the polydimethylsiloxane market. These findings were then complemented by in-depth interviews with senior executives, R&D specialists, and procurement managers across key geographic regions and end-use industries.
To validate and triangulate market trends, quantitative surveys captured detailed information on product adoption rates, pricing dynamics, and supply chain configurations. Advanced statistical techniques were employed to analyze demand drivers and identify emerging growth pockets. All proprietary and third-party data underwent strict quality checks, including cross-referencing against company financial reports and customs data to confirm accuracy.
Finally, an expert panel comprising chemical engineers, market strategists, and sustainability professionals reviewed draft conclusions and recommendations. Their feedback ensured that this research framework not only reflects current market realities but also anticipates future developments, delivering a comprehensive and balanced perspective on the polydimethylsiloxane landscape.
Explore AI-driven insights for the Polydimethylsiloxane market with ResearchAI on our online platform, providing deeper, data-backed market analysis.
Ask ResearchAI anything
World's First Innovative Al for Market Research
Synthesizing Insights to Chart Future Trajectories
The insights presented in this executive summary crystallize the critical dynamics shaping the polydimethylsiloxane market and outline clear pathways for strategic action. From the accelerating push toward sustainable formulations to the recalibration of global supply chains in response to new trade measures, the industry is at an inflection point where adaptability and innovation are paramount.
Deep segmentation analysis reveals where targeted investments can yield the greatest returns, whether in specialty fluid grades for precision industries or high-viscosity polymers for robust sealing applications. Regional and tariff-related insights underscore the importance of geopolitical awareness and operational flexibility in securing reliable access to feedstocks and end markets.
Together, these findings equip decision-makers with the knowledge needed to optimize product portfolios, strengthen competitive positioning, and anticipate emerging customer requirements. By synthesizing market intelligence with actionable recommendations, this overview provides a roadmap for navigating complexity and capitalizing on the full potential of polydimethylsiloxane.
This section provides a structured overview of the report, outlining key chapters and topics covered for easy reference in our Polydimethylsiloxane market comprehensive research report.
- Preface
- Research Methodology
- Executive Summary
- Market Overview
- Market Dynamics
- Market Insights
- Cumulative Impact of United States Tariffs 2025
- Polydimethylsiloxane Market, by Product Type
- Polydimethylsiloxane Market, by Application
- Polydimethylsiloxane Market, by End Use Industry
- Polydimethylsiloxane Market, by Viscosity Grade
- Polydimethylsiloxane Market, by Distribution Channel
- Americas Polydimethylsiloxane Market
- Europe, Middle East & Africa Polydimethylsiloxane Market
- Asia-Pacific Polydimethylsiloxane Market
- Competitive Landscape
- ResearchAI
- ResearchStatistics
- ResearchContacts
- ResearchArticles
- Appendix
- List of Figures [Total: 26]
- List of Tables [Total: 512 ]
Secure Your Comprehensive Market Intelligence Today
Elevate your strategic decision-making with the most comprehensive polydimethylsiloxane market research available. Reach out to Ketan Rohom, Associate Director of Sales & Marketing, to secure your copy of the full report and gain exclusive insights that will empower your organization to stay ahead of industry shifts and capitalize on emerging opportunities
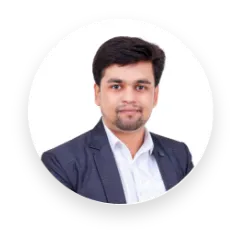
- How big is the Polydimethylsiloxane Market?
- What is the Polydimethylsiloxane Market growth?
- When do I get the report?
- In what format does this report get delivered to me?
- How long has 360iResearch been around?
- What if I have a question about your reports?
- Can I share this report with my team?
- Can I use your research in my presentation?