The Polyolefin Powder Market size was estimated at USD 10.49 billion in 2024 and expected to reach USD 11.50 billion in 2025, at a CAGR 9.17% to reach USD 17.77 billion by 2030.

Unveiling the Polyolefin Powder Market Dynamics
The polyolefin powder market has emerged as a cornerstone of innovation across diverse industries, propelled by its versatile performance characteristics, cost-effectiveness, and environmental advantages. In recent years, powder forms of polyethylene and polypropylene have transcended traditional molding and coating applications, finding new relevance in cutting-edge manufacturing processes such as additive manufacturing and advanced surface treatments. This executive summary delves into the underlying drivers elevating polyolefin powders from a niche offering to a strategic enabler for manufacturers, OEMs, and material scientists seeking sustainable, high-performance solutions.
Understanding the evolving landscape requires a nuanced appreciation of both macroeconomic factors and micro-level technological advancements. Trade policies, regulatory pressures, and raw material dynamics converge to influence supply chains, point to shifting cost structures, and create both obstacles and opportunities for market participants. At the same time, continuous research in catalytic processes and polymer chemistry has unlocked powders with tailored particle sizes, narrow molecular weight distributions, and enhanced functionalization potentials. The integration of these powders into diverse systems-from architectural coatings to rotational molding of complex components-underscores their adaptive scope.
As decision-makers navigate rapid industrial transformations, the capacity to anticipate and respond to market inflection points becomes paramount. This introduction provides a foundation for exploring the current state of polyolefin powders, examining policy impacts, dissecting customer segments, and identifying regional and competitive dynamics that collectively shape future trajectories. By situating the discussion within a holistic framework, stakeholders gain clarity on where the market stands today and where strategic investments can yield the greatest returns.
Defining Transformative Shifts Reshaping the Industry Landscape
Transformative forces are redefining the polyolefin powder landscape, driven by the convergence of material innovation, digital manufacturing, and heightened performance demands. Additive manufacturing has disrupted traditional production paradigms, transitioning polyolefin powders from passive feedstocks to critical inputs for rapid prototyping and low-volume, customized part fabrication. Advances in binder jetting and selective laser sintering techniques now accommodate high-density and linear low-density polyethylene variants, opening doors for design complexities previously unattainable with thermoplastic resins.
Simultaneously, the coatings sector has experienced a paradigm shift as powder coatings-once dominated by epoxy and polyester chemistries-embrace polyolefins for their superior chemical resistance, flexibility, and recyclability. The proliferation of automotive and architectural coating applications demanding lower VOC emissions and enhanced surface durability has accelerated adoption of specialized polyethylene powders. Moreover, the rotational molding industry leverages powders to manufacture robust storage tanks, industrial equipment casings, and recreational products, optimizing wall thickness and material distribution for superior mechanical performance.
In addition, sustainability initiatives are propelling the development of bio-based polyolefin powders and closed-loop recycling solutions. Stakeholders are investing in catalytic depolymerization and molecular reprocessing techniques to reclaim polyethylene and polypropylene streams. This emphasis on circularity not only addresses regulatory pressures but also positions polyolefin powders as a scalable solution for reducing plastic waste. Collectively, these trends signal a fundamental shift in how these materials are formulated, processed, and integrated into evolving manufacturing ecosystems.
Assessing the Cumulative Impact of US Tariffs in 2025
The imposition of new United States tariffs in 2025 has introduced significant complexities into the polyolefin powder supply chain. Increased duties on imported resins and catalysts have elevated upstream costs, prompting domestic manufacturers to reassess sourcing strategies and renegotiate supplier contracts. As a result, companies have accelerated the development of local production capacities, investing in retrofit projects for existing polymerization units and securing long-term agreements with domestic petrochemical operators to mitigate exposure to fluctuating import levies.
Furthermore, the tariff landscape has spurred consolidation among key players, as scale becomes a critical defense against rising expenses. Several mid-sized processors have explored joint ventures and strategic alliances to pool resources for capital-intensive plant expansions. At the same time, downstream converters are redesigning product portfolios to emphasize higher-value, specialty powders with differentiated performance attributes, thereby justifying premium pricing that absorbs a portion of the tariff impact.
From a logistical standpoint, the tariffs have prompted shifts in trade routes and inventory management practices. Supply chain leaders have diversified transshipment hubs and instituted risk-mitigation protocols to ensure continuity of critical raw materials. While these interventions have tempered immediate disruptions, they underscore the importance of agility and proactive policy analysis. Looking ahead, companies that invest in tariff-resilient strategies and foster collaborative relationships across the value chain are better positioned to maintain operational stability and competitive positioning under this new regulatory regime.
Uncovering Key Segmentation Insights Across Product, Application, and End Use
A granular examination of the polyolefin powder market reveals distinct patterns when dissecting product types, application segments, and end-use industries. On the product front, polyethylene variants are differentiated by density and molecular architecture, spanning high-density grades prized for stiffness and chemical resistance, low-density grades valued for flexibility and impact resilience, and linear low-density grades that balance both attributes. Concurrently, polypropylene powders-whether homopolymers with high crystallinity, impact copolymers blending ethylene for toughness, or random copolymers offering enhanced clarity-address diverse performance criteria in molding, extrusion coatings, and composite formulations.
Within application spheres, 3D printing technologies rely on finely milled powders that exhibit narrow particle size distributions and thermal stability under selective laser sintering or binder jetting processes. Powder coating formulations leverage functionalized polyethylene and polypropylene powders tailored for architectural finishes, automotive protective layers, and industrial machinery coatings requiring exceptional abrasion and corrosion resistance. Rotational molding products encompass a spectrum of industries, where powders engineered to deliver uniform material flow and low shrinkage produce automotive components, industrial equipment housings, storage tanks, and recreational goods with consistent wall thickness and robust mechanical properties.
End-use industries form the final axis of segmentation, as automotive manufacturers integrate polyolefin powders into under-the-hood components and interior trim to reduce vehicle weight and enhance fuel efficiency. Consumer goods companies deploy these powders for customized household items and sporting goods, while healthcare suppliers utilize medically compatible grades for sterilizable housings and device prototypes. Industrial sectors adopt powder-based coatings for machinery protection and chemical handling infrastructure, and packaging converters explore powder coatings and molded parts that combine aesthetic appeal with functional barriers.
This comprehensive research report categorizes the Polyolefin Powder market into clearly defined segments, providing a detailed analysis of emerging trends and precise revenue forecasts to support strategic decision-making.
- Type
- Application
- End Use Industry
Illuminating Regional Trends Driving Market Evolution
Regional dynamics in the polyolefin powder market reflect disparate growth drivers, regulatory environments, and supply chain configurations. In the Americas, the presence of integrated petrochemical complexes, abundant feedstock supplies, and established downstream processing capabilities underpin robust domestic capacity. This region’s emphasis on lightweight automotive components and sustainable packaging solutions has catalyzed demand for both commodity and specialty powders. Stakeholders in North and South America benefit from streamlined logistics corridors and a mature regulatory framework that supports trade in advanced polymer forms.
Across Europe, Middle East & Africa, the landscape is characterized by stringent environmental regulations, rising labor costs, and shifting energy supplies. European manufacturers have responded by investing in energy-efficient polymerization processes and exploring bio-based feedstocks to align with decarbonization targets. Meanwhile, the Middle East’s strategic position as a low-cost feedstock producer makes it a critical exporter of base resins, although downstream powder processing remains nascent. In Africa, burgeoning infrastructure projects and urbanization trends are gradually elevating demand for durable, weather-resistant rotationally molded products and protective coatings.
The Asia-Pacific region stands out as a rapidly evolving hotspot, driven by expansive automotive production, consumer electronics innovation, and a vibrant construction industry. Local players are scaling up capacity for polymer powder manufacturing, supported by government incentives for advanced materials and additive manufacturing initiatives. China, Japan, South Korea, and India are focal points for R&D collaborations that seek to refine catalyst systems and particle engineering techniques. This region’s dynamic market conditions underscore both the opportunities and competitive pressures facing global participants.
This comprehensive research report examines key regions that drive the evolution of the Polyolefin Powder market, offering deep insights into regional trends, growth factors, and industry developments that are influencing market performance.
- Americas
- Europe, Middle East & Africa
- Asia-Pacific
Profiling Leading Players and Competitive Forces
The competitive landscape of polyolefin powders features a spectrum of global and regional manufacturers, catalyst innovators, and composite suppliers jockeying for strategic advantage. Legacy chemical companies have leveraged their upstream integration to offer comprehensive resin and powder solutions, bundling catalysts, polymerization technology licenses, and technical support services. At the same time, specialty material houses have carved niches with tailored particle morphologies, proprietary functionalization chemistries, and enhanced performance warranties geared toward demanding applications in automotive, healthcare, and industrial coatings.
In recent years, technology collaborations and licensing agreements have proliferated, enabling smaller firms to access cutting-edge polymerization processes without incurring full capital expenditure. This has democratized entry into the powder market, spurring innovation in areas such as controlled radical polymerization and advanced metallocene catalysts. Contract manufacturers and toll processors also play a critical role, supporting brand owners who prefer to outsource powder production while retaining formulation and quality control.
Moreover, sustainable and circular economy considerations have prompted alliances between resin producers and recycling specialists. These partnerships focus on chemical recycling of polyolefin scrap and the incorporation of post-consumer recycled content into powder products. As environmental pressures intensify, companies that transparently communicate green credentials and demonstrate traceability across the value chain will likely gain preference among environmentally conscious OEMs and regulatory bodies.
This comprehensive research report delivers an in-depth overview of the principal market players in the Polyolefin Powder market, evaluating their market share, strategic initiatives, and competitive positioning to illuminate the factors shaping the competitive landscape.
- China Petroleum & Chemical Corporation
- Saudi Basic Industries Corporation
- LyondellBasell Industries Holdings B.V.
- INEOS Group AG
- Exxon Mobil Corporation
- Dow Inc.
- Braskem S.A.
- Borealis AG
- Formosa Plastics Corporation
- TotalEnergies SE
Actionable Strategies for Industry Leadership
Industry leaders must adopt a multifaceted strategic approach to thrive in the evolving polyolefin powder market. First, investments in R&D should prioritize advanced catalyst systems and downstream process optimization to yield powders with narrower particle distributions, improved thermal stability, and targeted functionality. By collaborating with academic institutions and specialized research centers, companies can accelerate innovation cycles and translate laboratory breakthroughs into commercial offerings.
Second, supply chain resilience must be reinforced through geographic diversification and flexible sourcing arrangements. Establishing alternative feedstock channels, forging strategic alliances with regional resin producers, and developing in-house recycling capabilities can mitigate the impact of prolonged tariff regimes and raw material shortages. Supply chain mapping tools and scenario planning exercises will further enable preemptive risk identification and response.
Third, product portfolio differentiation through application-specific formulations will unlock premium margins. Crafting specialty powders for high-performance 3D printing, corrosion-resistant coatings, or UV-stabilized rotational molding requires cross-functional collaboration among R&D, marketing, and field application engineers. Piloting customer co-creation programs can refine product attributes in real-world environments and foster brand loyalty.
Lastly, sustainability credentials should be embedded across the value chain. Transparent reporting on recycled content, energy-efficient manufacturing metrics, and end-of-life recyclability will resonate with end users and regulators alike. Companies that proactively engage with industry consortia and standards bodies can shape emerging circular economy frameworks and secure first-mover advantages in green procurement initiatives.
Robust Research Methodology Behind the Analysis
This analysis draws on a rigorous, multi-tiered research methodology that integrates qualitative expert insights with comprehensive secondary data review. The process commenced with an extensive literature survey encompassing peer-reviewed journals, industry white papers, regulatory publications, and patent filings to establish the foundational understanding of polyolefin powder technologies and market forces. Concurrently, proprietary databases and trade association records were mined to compile historic trade flows, tariff schedules, and capacity data, ensuring a robust macroeconomic context.
Subsequently, in-depth interviews were conducted with material scientists, process engineers, supply chain executives, and senior operations managers across the value chain. These discussions provided real-time perspectives on emerging processing techniques, product performance metrics, and strategic imperatives under evolving regulatory regimes. Qualitative findings were triangulated with quantitative data points through cross-validation techniques, enhancing both accuracy and reliability.
Competitive benchmarking involved profiling leading resin producers, catalyst developers, and powder processors to map capabilities, product portfolios, and strategic partnerships. Regional analyses synthesized economic indicators, manufacturing output statistics, and end-use demand drivers to delineate unique growth patterns. Throughout the research process, rigorous editorial review and data validation protocols ensured integrity, while periodic stakeholder feedback loops refined the study’s scope and depth.
Explore AI-driven insights for the Polyolefin Powder market with ResearchAI on our online platform, providing deeper, data-backed market analysis.
Ask ResearchAI anything
World's First Innovative Al for Market Research
Concluding Insights on Market Growth and Resilience
In conclusion, the polyolefin powder market stands at the nexus of material innovation, regulatory change, and shifting end-use demands. The maturation of additive manufacturing techniques, renewed focus on sustainability, and evolving tariff landscapes collectively shape a dynamic competitive arena. Stakeholders who embrace advanced R&D, strategic supply chain realignment, portfolio differentiation, and transparent sustainability practices will secure a leadership position in this transformative phase.
The convergence of high-performance powder innovations with circular economy principles offers a compelling pathway to both commercial growth and environmental stewardship. By navigating policy headwinds and forging collaborative ecosystems, market participants can harness the full potential of polyolefin powders across a broad spectrum of industrial applications. As this sector continues to evolve, the capacity to anticipate disruptions, pivot strategies, and deliver tailored value propositions will determine long-term success.
This executive summary provides a strategic compass for guiding investments, forging partnerships, and driving operational excellence. It underscores the importance of a holistic perspective that aligns technical capabilities with market realities, ensuring that polyolefin powder solutions remain at the forefront of manufacturing innovation and sustainable development.
This section provides a structured overview of the report, outlining key chapters and topics covered for easy reference in our Polyolefin Powder market comprehensive research report.
- Preface
- Research Methodology
- Executive Summary
- Market Overview
- Market Dynamics
- Market Insights
- Cumulative Impact of United States Tariffs 2025
- Polyolefin Powder Market, by Type
- Polyolefin Powder Market, by Application
- Polyolefin Powder Market, by End Use Industry
- Americas Polyolefin Powder Market
- Europe, Middle East & Africa Polyolefin Powder Market
- Asia-Pacific Polyolefin Powder Market
- Competitive Landscape
- ResearchAI
- ResearchStatistics
- ResearchContacts
- ResearchArticles
- Appendix
- List of Figures [Total: 22]
- List of Tables [Total: 372 ]
Secure Your Access to the Full Market Research Insights
Connect with Ketan Rohom, Associate Director of Sales & Marketing, to secure a copy of this comprehensive market research report. He will guide you through the purchase process, tailor the report’s applications to your strategic objectives, and ensure timely delivery of actionable insights. Don’t miss the opportunity to leverage in-depth analysis and expert recommendations to drive competitive advantage in the polyolefin powder sector.
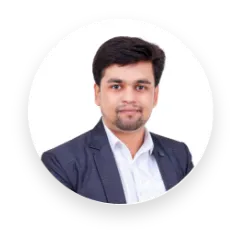
- How big is the Polyolefin Powder Market?
- What is the Polyolefin Powder Market growth?
- When do I get the report?
- In what format does this report get delivered to me?
- How long has 360iResearch been around?
- What if I have a question about your reports?
- Can I share this report with my team?
- Can I use your research in my presentation?