Introduction to Polyurethane In-Mold Coating Technology
Polyurethane in-mold coatings have emerged as a pivotal innovation in advanced manufacturing, transforming the way composite and thermoplastic parts achieve superior surface quality, durability, and aesthetic appeal. By applying a liquid polyurethane formulation directly within a mold, this technique creates seamless, high-performance coatings that adhere intimately to substrates during the molding cycle. This integrated process not only streamlines production but also delivers enhanced scratch resistance, chemical resilience, and UV stability compared to post-mold coating applications.
As demand intensifies across industries for lightweight components with premium finishes, in-mold coating technology addresses critical challenges in cycle time reduction, environmental compliance, and cost optimization. Leveraging rigorous formulation science and precise process controls, manufacturers can now achieve consistent part quality at scale, while minimizing waste and energy consumption. Moreover, evolving regulatory pressures and customer expectations for eco-friendly solutions are driving the adoption of waterborne and low-VOC polyurethane systems, further solidifying in-mold coatings as a cornerstone of sustainable production practices.
In this executive summary, we explore the forces reshaping the polyurethane in-mold coating landscape, dissect the implications of recent trade policies, and provide strategic insights to help decision-makers harness emerging opportunities in this dynamic market segment.
Key Transformative Shifts Shaping the In-Mold Coating Landscape
The last few years have witnessed transformative shifts in the in-mold coating landscape, propelled by breakthroughs in resin chemistry, digital manufacturing, and sustainability mandates. Innovations in UV-curable polyurethane blends now deliver rapid cure cycles and enhanced gloss retention, enabling manufacturers to meet high-volume production demands without sacrificing surface performance. Simultaneously, the integration of Industry 4.0 analytics is optimizing process parameters in real time, reducing scrap rates and enabling predictive maintenance to maximize equipment uptime.
Sustainability has become a driving force, with the development of bio-based polyol feedstocks and waterborne systems reducing reliance on petrochemical derivatives while adhering to stringent environmental regulations. As a result, leading manufacturers are pivoting toward cradle-to-gate life cycle assessments to quantify carbon footprints and demonstrate compliance with global eco-label standards.
Furthermore, the rise of lightweight composite substrates in aerospace and automotive applications is catalyzing demand for coatings that combine flexibility with long-term durability. Advanced nanofillers and silane crosslinkers are now being incorporated to bolster adhesion and abrasion resistance, unlocking new possibilities in high-performance segments. These shifts underscore a broader evolution in which technological, operational, and regulatory dynamics converge to redefine the in-mold coating value proposition.
Assessing the Cumulative Impact of United States Tariffs in 2025
In 2025, the cumulative impact of United States tariffs on raw materials has reverberated across the polyurethane in-mold coating supply chain, exerting pressure on both resin suppliers and end-use manufacturers. Tariffs on critical intermediates such as MDI and TDI have driven up inbound costs, compelling formulators to reevaluate sourcing strategies and negotiate long-term contracts to secure stable pricing. The increased duty burden has prompted many producers to localize production or enter into joint ventures to mitigate exposure to import levies.
Consequently, these policy measures have spurred innovation in alternative chemistries, with a growing emphasis on isocyanate-free systems and reactive diluents that circumvent tariffed inputs. At the same time, downstream customers are demanding greater transparency on cost pass-through mechanisms, leading to collaborative pricing models and volume-based incentives. In an environment of heightened tariff uncertainty, supply chain resilience has become paramount, driving investments in dual sourcing, buffer inventories, and nearshoring initiatives.
Although short-term margins have been squeezed, the evolving tariff landscape has accelerated the adoption of agile manufacturing architectures and fostered closer partnerships between raw material producers, coaters, and OEMs. Market participants that proactively adapt their procurement and formulation strategies stand to emerge more competitive in the post-tariff era.
In-Depth Segmentation Insights Across Application, Finish, End-User, Components, Material, Technology, Performance, and Substrate
Analysis of the in-mold coating market across application segments reveals differentiated growth trajectories. In aerospace, exterior and interior components are both experiencing heightened demand for lightweight panels that deliver high gloss and chemical resistance; manufacturers are increasingly favoring polyurethane systems formulated for rapid demolding and minimal secondary processing. In automotive, the dynamic between exterior coating technologies and interior surface enhancements underscores the need for coherent formulations that ensure color consistency and durability across both segments. Electronics applications-from consumer devices to industrial control panels-require coatings that balance aesthetic appeal with thermal stability and dielectric performance. Turning to furniture, the distinction between commercial and residential products highlights divergent finishing priorities, where high-durability gloss coatings serve office environments, and softer satin matte finishes address home décor trends. Similarly, the sports equipment segment is bifurcated into fitness equipment, which demands high abrasion resistance, and protective gear requiring impact-resistant topcoats.
When examining finish types, high gloss and medium gloss variants continue to dominate markets that prioritize visual impact, whereas flat matte and satin matte systems are gaining ground in segments driven by contemporary design aesthetics. Pearlescent and textured metallic finishes represent a specialized niche, appealing to premium applications that seek distinctive visual effects and tactile depth.
From an end-user perspective, DIY enthusiasts and professional designers are fueling demand for user-friendly waterborne in-mold kits, while retail and wholesale distributors are optimizing inventory management to cater to volatile seasonal demand. Contract manufacturers and OEMs are investing in high-volume, automated coating lines equipped with advanced process controls to ensure reproducibility and throughput.
Component type segmentation underscores the diversity of formulation requirements. Antifoaming agents and UV stabilizers are critical additives that enhance coating performance under challenging environmental exposures. Both solvent-based and water-based basecoats remain prevalent, with waterborne variants gaining market share due to regulatory pressures. Single-component primers offer ease of application, whereas two-component systems deliver superior adhesion and chemical resistance. Topcoat choices between high-solids and low-solids formulations reflect a trade-off between film build and dry time.
Material type considerations split between thermoplastics, such as polycarbonate and polystyrene, and thermosetting substrates, including acrylic-based and epoxy-based composites, each demanding tailored adhesion promoters and flexibilizers. In the realm of coating technologies, automated dipping and multi-pass flow coating systems are favored for high consistency, while manual dipping and single-pass flow coating remain essential for low-volume, customized production. Forward and reverse roll coating techniques enable precise thickness control on flat substrates, and electrostatic spraying is often employed for complex geometries requiring uniform coverage.
Finally, performance attributes such as abrasion resistance, chemical resistance, corrosion resistance, and temperature stability drive formulation complexity. High-abrasion and long-term corrosion resistance are particularly critical in industrial settings, whereas acid and alkaline chemical resistance are prioritized in segments exposed to harsh cleaning protocols. Temperature stability, whether at extreme high or low ends, ensures coating integrity across diverse operating environments. Substrate compatibility further subdivides the market between aluminum and steel surfaces, which require robust metallic adhesion promoters, and composite materials and plastics, which necessitate specialized primers to mitigate differential thermal expansion.
This comprehensive research report categorizes the Polyurethane In-Mold Coating market into clearly defined segments, providing a detailed analysis of emerging trends and precise revenue forecasts to support strategic decision-making.
- Application
- Finish Type
- End-User
- Component Type
- Material Types
- Coating Technology
- Performance Attributes
- Substrate Compatibility
Key Regional Dynamics Influencing Market Adoption and Growth
Regionally, the Americas market continues to lead in innovation adoption, with North America’s automotive and aerospace industries driving demand for advanced polyurethane in-mold coatings that meet stringent safety and environmental standards. South American markets, particularly Brazil, are embracing waterborne technologies to comply with evolving VOC regulations and capitalize on burgeoning infrastructure investments.
In Europe, Middle East & Africa, regulatory frameworks such as REACH and GHS have accelerated the phase-out of high-VOC solvent-based coatings, prompting manufacturers to pivot toward eco-friendly alternatives. Germany, France, and the UK remain hotspots for advanced coating developments, while the Gulf Cooperation Council countries are leveraging growth in construction and automotive manufacturing to expand in-mold coating capacity.
Asia-Pacific markets exhibit the highest overall growth trajectory, driven by rapid industrialization, automotive assembly expansions, and consumer electronics manufacturing hubs in China, Japan, South Korea, and India. Local producers are scaling up capacity for waterborne and UV-curable polyurethane systems to meet both domestic and export demand. Southeast Asian nations are also rising as strategic manufacturing bases, offering cost advantages and supportive government incentives for chemical industry investments.
This comprehensive research report examines key regions that drive the evolution of the Polyurethane In-Mold Coating market, offering deep insights into regional trends, growth factors, and industry developments that are influencing market performance.
- Americas
- Asia-Pacific
- Europe, Middle East & Africa
Competitive Landscape and Leading Industry Players
The competitive landscape is defined by a mix of global chemical giants and specialized coating formulators, each leveraging unique capabilities to capture market share. Akzo Nobel N.V. and BASF SE have expanded their in-mold coating portfolios through targeted R&D investments in bio-based polyols and high-performance additives. Axalta Coating Systems and PPG Industries, Inc. emphasize integrated solutions, combining primers, basecoats, and topcoats to simplify procurement and streamline application processes. Bayer AG and Covestro AG are collaborating with OEMs to develop application-specific formulations for automotive lightweight composites.
Specialist manufacturers such as Coventya International GmbH and Lubrizol Corporation focus on performance additives, offering tailored antifoaming agents and UV stabilizers that enhance durability under extreme conditions. DAW SE and Tikkurila Oyj are leveraging their deep regional presence in Europe to provide rapid technical support and color matching services. Huntsman Corporation and KCC Corporation are investing in isocyanate-free technologies to address emerging regulatory constraints, while Nippon Paint Holdings Co., Ltd. and The Sherwin-Williams Company emphasize digital color management tools to reduce time-to-market.
Meanwhile, Hempel A/S, RPM International Inc., and Valspar Corporation are differentiating through service excellence, offering end-to-end project management and on-site training programs. Collectively, these players are fostering collaboration across the value chain, forging partnerships with resin producers, molders, and end users to co-develop next-generation in-mold coating systems and accelerate adoption in high-growth segments.
This comprehensive research report delivers an in-depth overview of the principal market players in the Polyurethane In-Mold Coating market, evaluating their market share, strategic initiatives, and competitive positioning to illuminate the factors shaping the competitive landscape.
- Akzo Nobel N.V.
- Axalta Coating Systems
- BASF SE
- Bayer AG
- Beckers Group
- Coventya International GmbH
- Covestro AG
- DAW SE
- Hempel A/S
- Huntsman Corporation
- KCC Corporation
- Lubrizol Corporation
- Nippon Paint Holdings Co., Ltd.
- PPG Industries, Inc.
- RPM International Inc.
- The Sherwin-Williams Company
- Tikkurila Oyj
- Valspar Corporation
Actionable Recommendations for Industry Leadership and Growth
To thrive in the evolving in-mold coating market, industry leaders should prioritize the integration of sustainable chemistries by accelerating development of bio-based and low-VOC polyurethane formulations. This strategic pivot will not only ensure regulatory compliance but also resonate with end users demanding greener solutions. Additionally, investing in digital process controls and predictive analytics platforms will optimize cure parameters, reduce defects, and enhance throughput, delivering tangible ROI through reduced rework and downtime.
Strengthening supply chain resilience is equally critical. Leaders should secure diversified sourcing agreements, consider nearshoring critical intermediates, and establish collaborative forecasting mechanisms with suppliers to mitigate tariff volatility and raw material shortages. Forming strategic alliances with OEMs and contract coaters to co-innovate application-specific solutions can unlock new revenue streams and deepen customer engagement.
Moreover, expanding technical service offerings-such as on-site training, color matching laboratories, and virtual reality–enabled process simulations-can differentiate product portfolios and foster long-term customer loyalty. Finally, accelerating pilot projects for emerging technologies, including isocyanate-free chemistries and advanced nanocomposite coatings, will position companies at the forefront of next-generation performance requirements, ensuring competitive advantage as market demands evolve.
Explore AI-driven insights for the Polyurethane In-Mold Coating market with ResearchAI on our online platform, providing deeper, data-backed market analysis.
Ask ResearchAI anything
World's First Innovative Al for Market Research
Conclusion: Seizing the Future of Polyurethane In-Mold Coatings
The polyurethane in-mold coating sector stands at an inflection point, shaped by technological breakthroughs, sustainability imperatives, and shifting trade policies. Manufacturers that embrace digitalization, invest in green chemistries, and cultivate agile supply chains will be best positioned to capture growth and lead market transformation. By fostering strategic partnerships across the value chain, prioritizing customer-centric innovation, and deploying advanced service offerings, companies can differentiate their offerings and drive lasting competitive advantage.
As the regulatory landscape tightens and end users demand higher performance and environmental stewardship, the opportunity to redefine surface finishing standards through in-mold coating technology has never been greater. Organizations that align their R&D roadmaps with market needs and operationalize continuous improvement practices will unlock value, mitigate risk, and establish themselves as trusted partners in delivering high-quality, sustainable solutions.
This section provides a structured overview of the report, outlining key chapters and topics covered for easy reference in our Polyurethane In-Mold Coating market comprehensive research report.
- Preface
- Research Methodology
- Executive Summary
- Market Overview
- Market Dynamics
- Market Insights
- Cumulative Impact of United States Tariffs 2025
- Polyurethane In-Mold Coating Market, by Application
- Polyurethane In-Mold Coating Market, by Finish Type
- Polyurethane In-Mold Coating Market, by End-User
- Polyurethane In-Mold Coating Market, by Component Type
- Polyurethane In-Mold Coating Market, by Material Types
- Polyurethane In-Mold Coating Market, by Coating Technology
- Polyurethane In-Mold Coating Market, by Performance Attributes
- Polyurethane In-Mold Coating Market, by Substrate Compatibility
- Americas Polyurethane In-Mold Coating Market
- Asia-Pacific Polyurethane In-Mold Coating Market
- Europe, Middle East & Africa Polyurethane In-Mold Coating Market
- Competitive Landscape
- ResearchAI
- ResearchStatistics
- ResearchContacts
- ResearchArticles
- Appendix
- List of Figures [Total: 32]
- List of Tables [Total: 1562 ]
Call-to-Action: Connect with Ketan Rohom for the Full Market Research Report
To explore comprehensive market insights and gain a competitive edge, reach out to Ketan Rohom, Associate Director, Sales & Marketing, for tailored access to the full in-mold coating research report. Harness this intelligence to inform strategic decisions and accelerate your market leadership journey.
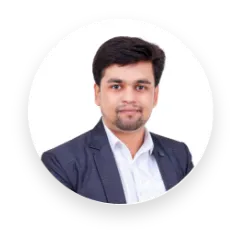
- When do I get the report?
- In what format does this report get delivered to me?
- How long has 360iResearch been around?
- What if I have a question about your reports?
- Can I share this report with my team?
- Can I use your research in my presentation?