Unveiling the Critical Role of Powder Metal Components in Modern Manufacturing Ecosystems Fueled by Precision, Efficiency, and Innovation
Powder metallurgy deploys an innovative manufacturing approach that compresses fine metal powders into precise shapes before sintering them under controlled temperatures. This process yields dense, high-performance components that meet stringent specifications for mechanical strength, dimensional accuracy, and material integrity. By harnessing advanced compaction and sintering techniques, manufacturers can optimize every stage from powder production to final part finishing, ensuring consistent quality and reliability across diverse applications.
Across industries, powder metal components underpin critical functionality in automotive powertrains, aerospace structural assemblies, medical implants, industrial machinery, and consumer electronics. In automotive, near-net-shape gears and bearings enhance fuel efficiency and reduce emissions, while in aerospace, sintered parts contribute to weight reduction and operational safety. Similarly, in medical devices and electronics, powder metallurgy’s precision enables miniaturized components with exceptional performance characteristics.
Moreover, powder metallurgy’s inherent efficiency delivers significant benefits in material utilization, cost containment, and sustainability. By achieving near-net-shape geometries, the process minimizes post-machining operations and scrap generation, often realizing scrap rates below 3%. This near-total powder usage reduces energy consumption, aligns with circular economy goals, and supports stringent environmental mandates while preserving competitive manufacturing economics.
Exploring the Technological, Regulatory, and Sustainability-Driven Transformations Reshaping the Powder Metal Components Industry
The powder metal components industry is undergoing a digital metamorphosis driven by the rapid integration of additive manufacturing and simulation-driven design tools. Emerging technologies such as 3D printing enable engineers to create complex lattice structures and internal channels that were previously infeasible, unlocking new performance and weight-reduction opportunities across sectors such as aerospace and medical devices. These advancements are catalyzing product differentiation and accelerating time-to-market for high-value components.
Concurrently, the regulatory and quality landscape is evolving to ensure consistency and safety in increasingly sophisticated applications. Standards including ISO 3252:2023, defining powder metallurgy terminology, and ISO 5755:2022, governing sintered metal material specifications, are enhancing nomenclature, testing protocols, and acceptance criteria for critical parts. In parallel, ASTM B925 outlines best practices for PM test specimens, ensuring that material and mechanical property data remain comparable and compliant across global supply chains.
Sustainability imperatives are further reshaping material strategies, as companies exploit powder metallurgy’s green credentials to meet ESG targets. By leveraging near-net-shape near-zero scrap processes and recycling metal powders in closed loops, manufacturers are cutting energy usage by up to 15% compared to traditional routes and reducing carbon footprints. The drive to adopt eco-friendly composite powders and low-alloy substitutes reflects a broader commitment to circular production models and resource stewardship across the industry.
Analyzing How 2025 United States Tariffs on Steel and Aluminum Imports Transform Cost Structures and Supply Chain Strategies in Powder Metal Components
New tariff measures implemented in 2025 have imposed higher duties on essential feedstocks such as iron and aluminum powders, compelling component manufacturers to recalibrate cost structures and supply strategies. With steel and aluminum import duties doubled in many categories, input costs for powder metal operations have surged, prompting firms to negotiate long-term contracts and diversify supplier portfolios to stabilize raw-material access and pricing.
Under tariff-induced cost pressures, several manufacturers are reshoring production facilities closer to domestic powder producers or near primary raw-material reserves. This geographic realignment fosters strategic alliances between component fabricators and powder suppliers, enabling co-location of sintering and finishing operations. Such partnerships support integrated quality control, logistics efficiencies, and capital investment in advanced processing equipment, mitigating exposure to import volatility.
Beyond immediate cost hikes, the tariff regime has accelerated innovation in material selection, as firms explore composite powders and low-alloy alternatives that escape the steepest duties. These material-substitution strategies, coupled with strengthened supplier relationships and vertical integration, are proving critical for maintaining margins and operational agility in a shifting trade environment. As a result, the powder metal sector is emerging more resilient and strategically oriented toward domestic supply continuity.
Revealing How End Use and Component Type, Material, Process, and Geometry Segments Unlock Strategic Opportunities in Powder Metal Components Market
In examining end use industries, automotive applications dominate demand for powder metal components due to the need for lightweight, high-precision gears and bearings in electric and conventional vehicles, with two-wheelers and commercial fleets also adopting PM parts for durability and cost-efficiency. Aerospace and defense sectors likewise leverage sintered structural components for weight-critical airframes and engine parts, while consumer electronics and industrial machinery benefit from filters, connectors, and wear-resistant parts that maximize performance under harsh operating conditions.
Component type segmentation reveals that bearings and bushings remain the largest categories, driven by the requirement for low-friction, high-load components in automotive transmissions and industrial equipment. Within bearings, plain and roller variants each address unique operational profiles, and roller bearings, especially deep-groove ball and cylindrical designs, deliver superior stability and speed in precision machinery. Structural parts and gear wheels further capture market share by enabling complex assemblies with minimal secondary processing.
Material type insights highlight the prevalence of iron-based powders, subdivided into high-alloy grades for demanding mechanical performance and low-alloy grades for cost-sensitive applications, accounting for over half of global PM consumption. Aluminum-based powders support lightweight structural solutions, while copper and nickel-based systems cater to electrical conductivity, corrosion resistance, and high-temperature stability in diverse environments.
The manufacturing process landscape spans traditional press sintering and metal injection molding to advanced routes such as hot isostatic pressing and additive manufacturing. Within AM, binder jetting, directed energy deposition, and powder bed fusion techniques are unlocking unprecedented design freedom and customization for low-volume, high-complexity parts. Concurrently, conventional sintering and molding remain essential for high-volume, cost-efficient mass production.
Finally, geometry segmentation underscores growing demand for complex shapes, including internal channels for fluid flow, lattice structures for optimized strength-to-weight ratios, and thin-walled components for heat exchangers. These intricate designs capitalize on powder metallurgy’s net-shape capabilities, while simpler geometries continue to support high-throughput production of standardized parts.
This comprehensive research report categorizes the Powder Metal Components market into clearly defined segments, providing a detailed analysis of emerging trends and precise revenue forecasts to support strategic decision-making.
- End Use Industry
- Component Type
- Material Type
- Manufacturing Process
- Geometry
Highlighting Regional Market Dynamics in the Americas, EMEA, and Asia-Pacific to Uncover Unique Growth Drivers and Competitive Advantages
In the Americas, robust demand in automotive powertrain and transmission sectors continues to drive powder metallurgy adoption. The United States and Mexico, with their established vehicle manufacturing bases, rely heavily on sintered gears, bearings, and structural parts to achieve fuel efficiency targets and emissions standards. Meanwhile, the medical device industry in North America is increasingly leveraging PM techniques for custom titanium and stainless-steel implants, underscoring the region’s emphasis on precision and biocompatibility. This synergy of automotive and medical applications has been bolstered by ongoing R&D investments and advanced manufacturing deployments across the continent.
Europe, Middle East & Africa (EMEA) markets are characterized by strong aerospace and defense requirements, prompting significant uptake of PM processes such as hot isostatic pressing for critical turbine and structural components. In Western Europe, additive manufacturing hubs in Germany, France, and the United Kingdom are pioneering metal 3D printing for low-volume, high-value parts, driven by rigorous quality and environmental regulations. Simultaneously, Gulf Cooperation Council countries are investing in industrial diversification programs that incentivize cost-effective, high-precision manufacturing, creating emerging opportunities in sectors like oil & gas, automotive, and medical devices across the region.
Asia-Pacific stands out for its rapid industrialization and infrastructure expansion, particularly in China and India. The automotive sector’s pivot toward electric vehicles has spurred demand for lightweight, high-strength PM parts, while the electronics industry in South Korea and Taiwan intensifies use of PM for precision connectors and magnetic components. Government initiatives such as China’s Industrial Upgrade Plan and India’s Make in India campaign have catalyzed investments in powder production and sintering facilities, positioning the region as the fastest-growing global market for powder metal components.
This comprehensive research report examines key regions that drive the evolution of the Powder Metal Components market, offering deep insights into regional trends, growth factors, and industry developments that are influencing market performance.
- Americas
- Europe, Middle East & Africa
- Asia-Pacific
Profiling Leading Powder Metal Components Manufacturers Driving Innovation Efficiency and Sustainability Through Advanced Materials and Processes
GKN Powder Metallurgy leads the sector with its integrated global network of 27 facilities and over 5,000 employees, delivering 10 million precision parts daily across automotive, aerospace, and industrial applications. The company’s robust additive manufacturing division and proprietary sintering technologies underline its commitment to innovation and operational excellence.
Sumitomo Electric Industries distinguishes itself through vertical integration, producing high-performance PM components for automotive systems using proprietary surface-treatment processes. Its scalable production lines and extensive alloy portfolio support critical powertrain and sensor applications where precision and reliability are paramount.
Höganäs AB, the world’s largest metal-powder producer, benefits from a diverse materials portfolio spanning iron, steel, and copper-based powders. The company’s sustainability initiatives, including energy-efficient gas-atomization techniques and closed-loop recycling, have positioned it as an environmental leader in powder metallurgy.
Sandvik Powder Solutions excels in aerospace, energy, and medical sectors through its Osprey brand of gas-atomized superalloy and titanium powders. Rigorous quality control and certification protocols enable the production of mission-critical components that withstand extreme conditions and regulatory scrutiny.
Other notable players include Fine Sinter Co., Ltd., renowned for ultra-precise engine and transmission components; PMG Holding GmbH, which supplies European automotive OEMs with lightweight structural parts; Schunk Group, recognized for wear-resistant industrial components; Porite Group, a high-volume supplier to Asian automakers; and Hitachi Chemical, innovating specialty PM materials for electronics and transportation markets.
This comprehensive research report delivers an in-depth overview of the principal market players in the Powder Metal Components market, evaluating their market share, strategic initiatives, and competitive positioning to illuminate the factors shaping the competitive landscape.
- GKN Powder Metallurgy Limited
- Sumitomo Electric Industries, Ltd.
- Miba AG
- FORWARD Metall GmbH
- Epson Atmix Corporation
- Hitachi Metals, Ltd.
- F.C.C. Co., Ltd.
- Ferro PM Inc.
- Feintool International Holding AG
- American Axle & Manufacturing, Inc.
Implementing Strategic Pathways for Sustained Growth Through Diversification Resilience and Innovation in the Powder Metal Components Industry
Industry leaders should diversify supply chains by engaging multiple powder suppliers across tariffelevated jurisdictions, thereby reducing dependency risks and ensuring continuity of feedstocks. Structuring flexible long-term agreements with duty-inclusive terms can safeguard against abrupt cost escalations and enable transparent price sharing among stakeholders. These measures will bolster resilience against ongoing trade policy fluctuations.
Investing in advanced additive manufacturing infrastructure offers a dual advantage of design freedom and operational agility. Deploying binder jetting or powder bed fusion systems can accelerate prototyping and low-volume production while enhancing complex geometry capabilities. Concurrently, integrating digital twins and process monitoring tools will optimize sintering cycles and reduce defect rates, elevating overall throughput and cost efficiency.
Sustainability commitments should be amplified through closed-loop powder recycling programs and the adoption of low-alloy or composite powders with reduced carbon footprints. Aligning material strategies with global ESG targets and leveraging recycled feedstocks can unlock both regulatory incentives and brand differentiation in environmentally conscious markets. Furthermore, participatory partnerships with upstream powder producers to co-invest in green atomization technologies will foster shared progress toward decarbonization goals.
Collaboration models with OEMs, research institutes, and standards bodies can expedite the development of new alloys and process benchmarks. Establishing consortiums for cross-industry R&D-focused on emerging applications such as electric motor magnets, medical implants, and heat-exchanger components-will drive shared innovation, reduce time-to-market, and strengthen competitive positioning in high-growth niches.
Demystifying Robust Primary and Secondary Research Frameworks Underpinning the Powder Metal Components Market Analysis
Our analysis combined extensive secondary research with primary interviews to ensure a robust, multidimensional perspective on the powder metal components market. Secondary research encompassed corporate filings, technical standards, trade publications, and government databases, enabling the identification of macroeconomic drivers and regulatory frameworks. Primary research involved in-depth interviews with industry leaders, procurement heads, and R&D specialists, validating trends and uncovering real-time market dynamics.
Data triangulation formed the cornerstone of our methodology, integrating multiple data sources and research methods to minimize biases and enhance the credibility of findings. Quantitative insights derived from historical trends and industry reports were cross-verified through qualitative feedback from key opinion leaders, ensuring alignment between numerical projections and operational realities. This iterative validation process strengthened our confidence in market segmentation, regional analyses, and competitive benchmarking.
Segmentation analyses leveraged detailed end-use, material, component type, process, and geometry frameworks, facilitating targeted insights for each sub-market. Regional dynamics were evaluated through localized expert discussions and government policy reviews, capturing nuanced growth drivers and logistical considerations. Company profiles were constructed from primary engagements with C-level executives and technical leads, corroborated by publicly available corporate disclosures and patent filings to assess innovation pipelines and strategic priorities.
Explore AI-driven insights for the Powder Metal Components market with ResearchAI on our online platform, providing deeper, data-backed market analysis.
Ask ResearchAI anything
World's First Innovative Al for Market Research
Synthesizing Industry Insights to Chart the Future Growth Trajectory and Competitive Landscape of Powder Metal Components
The powder metal components industry is poised for continued evolution as market participants embrace digitalization, sustainability, and strategic supply-chain realignment. Additive manufacturing and advanced sintering approaches will unlock new design possibilities, while evolving standards and circular-material initiatives will reinforce quality and environmental stewardship. Competitive differentiation will hinge on effective segmentation strategies, regional agility, and robust partnerships across the value chain.
As tariff dynamics reshape cost models, companies that proactively diversify sourcing, co-locate with powder producers, and adopt material-substitution strategies will secure stronger margins and operational resilience. Moreover, targeted investments in green atomization, digital twins, and collaborative R&D consortiums are essential for capitalizing on high-growth applications in aerospace, electric vehicles, and medical implants. By aligning strategic actions with evolving market drivers, industry leaders can chart a sustainable, innovation-led trajectory in the powder metal components sector.
This section provides a structured overview of the report, outlining key chapters and topics covered for easy reference in our Powder Metal Components market comprehensive research report.
- Preface
- Research Methodology
- Executive Summary
- Market Overview
- Market Dynamics
- Market Insights
- Cumulative Impact of United States Tariffs 2025
- Powder Metal Components Market, by End Use Industry
- Powder Metal Components Market, by Component Type
- Powder Metal Components Market, by Material Type
- Powder Metal Components Market, by Manufacturing Process
- Powder Metal Components Market, by Geometry
- Americas Powder Metal Components Market
- Europe, Middle East & Africa Powder Metal Components Market
- Asia-Pacific Powder Metal Components Market
- Competitive Landscape
- ResearchAI
- ResearchStatistics
- ResearchContacts
- ResearchArticles
- Appendix
- List of Figures [Total: 28]
- List of Tables [Total: 1014 ]
Engage Directly with Ketan Rohom to Secure Exclusive Industry Insights and Propel Your Strategic Decisions in Powder Metal Components Market
Don’t miss the opportunity to leverage comprehensive market intelligence tailored to your strategic priorities. Ketan Rohom, Associate Director of Sales & Marketing, stands ready to guide you through the report’s key insights and demonstrate how they align with your business objectives. Reach out to explore customized data extracts, discuss bespoke analysis, or secure immediate access to the full market research report. Engage with Ketan to elevate your competitive positioning and accelerate decision-making in the powder metal components arena.
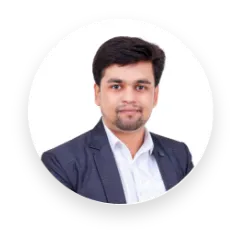
- When do I get the report?
- In what format does this report get delivered to me?
- How long has 360iResearch been around?
- What if I have a question about your reports?
- Can I share this report with my team?
- Can I use your research in my presentation?