Introduction to the Pre-sintering Furnace Market Landscape
Pre-sintering furnaces serve as critical enablers in advanced materials processing, providing precise thermal control to transform green or shaped powder compacts into dimensionally stable, high-performance components. By carefully regulating temperature profiles, heating mechanisms, and reactive atmospheres, these furnaces ensure uniform densification and microstructural integrity prior to final sintering stages. As industries demand parts with complex geometries, tighter tolerances, and enhanced material properties, pre-sintering technologies have evolved to support emerging manufacturing paradigms such as 4D printing, additive manufacturing hybridization, and energy-efficient production.
Leading sectors-ranging from aerospace and defense to healthcare-rely on pre-sintering furnaces to deliver components that withstand extreme conditions, resist corrosion, and maintain biocompatibility. Moreover, the push toward sustainability has driven furnace makers to integrate eco-friendly heating mechanisms, optimize energy consumption, and incorporate advanced materials capable of rapid thermal cycling. Consequently, procurement strategies and engineering specifications now emphasize not only throughput and reliability but also lifecycle costs and carbon footprints.
This executive summary examines the shifting market dynamics, regulatory developments, and strategic imperatives shaping the pre-sintering furnace landscape. It offers insights into tariff impacts, segmentation trends, regional variations, competitive positioning, and recommended actions for decision-makers seeking to capitalize on growth opportunities while mitigating supply-chain and policy risks.
Transformative Shifts Redefining Pre-sintering Furnace Applications
Over the past few years, the pre-sintering furnace market has undergone transformative shifts driven by technological innovation and shifting customer expectations. Digitalization has enabled real-time process monitoring and closed-loop control, facilitating consistent quality across batch and continuous operations. Simultaneously, advances in 4D printing techniques-particularly electroactive polymers and shape-memory alloys-are extending the capabilities of pre-sintering furnaces to handle smart materials with complex reaction kinetics.
In parallel, heating mechanisms have diversified beyond conventional electrical resistance systems to include induction and microwave approaches, each offering distinct advantages in heating speed, penetration depth, and energy efficiency. As a result, manufacturers can tailor furnace configurations to specific material types-whether refractory ceramics, bio-ceramics, aluminum alloys, or thermosetting plastics-and achieve superior densification outcomes.
Moreover, the growing emphasis on sustainability has catalyzed the adoption of high-energy efficiency designs and low-consumption models, prompting original equipment manufacturers to optimize chamber insulation, waste heat recovery, and advanced sensor integration. Finally, the convergence of additive manufacturing and traditional sintering processes is unlocking new application domains-ranging from rocket components and defense equipment to dental implants and custom tooling. These transformative trends are redefining competitive advantage and setting new benchmarks for performance, cost, and environmental stewardship.
Cumulative Impact of United States Tariffs Effective 2025
With the implementation of new tariff measures effective in 2025, manufacturers and end users of pre-sintering furnaces face a recalibrated cost structure. Duties on imported furnace components, specialized alloys, and high-purity refractory materials have led to incremental price increases, affecting both capital expenditures and operating budgets. In response, many stakeholders are reevaluating sourcing strategies to strike a balance between cost containment and supply-chain resilience.
Tariffs have also spurred a renaissance in domestic production, incentivizing furnace makers to localize critical component manufacturing and invest in advanced fabrication facilities. While this shift enhances security of supply, it may introduce lead-time variations and require collaborations with new vendors to maintain technical standards. Additionally, foreign suppliers are offering bundled value propositions-such as extended service contracts and technology transfer-to mitigate the impact of U.S. trade barriers.
In parallel, end users in aerospace, automotive, and electronics sectors are adjusting procurement cycles and inventory policies to hedge against price volatility. By leveraging predictive analytics and strategic stockpiling, some organizations aim to smooth cost fluctuations and maintain production continuity. Looking ahead, the cumulative tariff impact will continue to shape competitive dynamics, driving both consolidation among suppliers and tier-one partnerships focused on integrated thermal solutions.
Key Market Segmentation Insights and Technology Preferences
An in-depth analysis of market segmentation reveals differentiated growth trajectories and technology preferences across various axes. When categorized by technology, four-dimensional printing techniques are gaining traction, with electroactive polymers and shape-memory alloys driving demand for furnaces capable of precise thermal ramp rates. Meanwhile, electrical resistance heating remains a workhorse for standard applications, but induction and microwave heating mechanisms are preferred for rapid throughput and uniform energy distribution. Reaction kinetics segmentation highlights the importance of both gaseous-phase reactivity-essential for controlled atmosphere sintering-and solid-state reactivity, which underpins densification of high-temperature ceramics.
Application segmentation underscores aerospace and defense requirements for defense equipment and rocket components with rigorous quality standards, while the automotive sector focuses on engine components and exhaust systems that must endure cyclic thermal stresses. Consumer electronics applications, including smartphone components and wearables, demand compact furnace footprints and rapid cycle times. In healthcare, dental implants and prosthetics necessitate biocompatible materials processed with strict contamination controls.
Material type segmentation spans ceramics-encompassing bio-ceramics and refractory variants-metals such as aluminum alloys and stainless steel, and polymers ranging from thermoplastics to thermosetting plastics. Furnace design insights reveal a split between horizontal configurations, which offer multi-chamber and single-chamber layouts for batch flexibility, and vertical designs, where bottom-loading and top-loading options optimize floor space and ergonomic handling. End-user industry segmentation highlights chemical processing, with catalyst material production and specialty chemicals driving demand, and manufacturing sectors focused on component manufacturing and tool production. Research institutions and laboratories prioritize materials research and testing facilities. Production volume stratification differentiates high-volume batch manufacturing and mass production from low-volume custom units and prototyping. Market size segmentation distinguishes large enterprises from small and medium enterprises, while energy consumption segmentation separates high-energy efficiency systems from low-consumption models.
This comprehensive research report categorizes the Pre-sintering Furnace market into clearly defined segments, providing a detailed analysis of emerging trends and precise revenue forecasts to support strategic decision-making.
- Technology
- Application
- Material Type
- Furnace Design
- End-User Industry
- Production Volume
- Market Size
- Energy Consumption
Key Regional Insights Shaping Market Dynamics
Regional analysis uncovers distinct drivers and barriers across the Americas, EMEA, and Asia-Pacific markets. In the Americas, robust aerospace, automotive, and medical device industries underpin sustained investment in pre-sintering furnaces, with strong R&D ecosystems supporting material innovation and process optimization. North American manufacturers benefit from proximity to critical end users and streamlined logistics, though they must contend with local content requirements tied to tariff regulations.
Europe, Middle East & Africa presents a diversified opportunity set, where stringent environmental regulations and incentives for energy-efficient solutions propel adoption of high-efficiency furnace designs. The region’s established industrial clusters in Germany, France, and the UK are complemented by growing manufacturing hubs in the Middle East, which leverage lower energy costs and strategic trade corridors. However, volatility in raw material prices and regulatory heterogeneity across markets pose challenges.
Asia-Pacific remains the fastest-growing region, led by China, Japan, and South Korea’s aggressive investments in advanced manufacturing and additive production capabilities. Government initiatives promoting domestic equipment development and export-oriented policies have accelerated capacity expansion. At the same time, emerging economies in Southeast Asia are beginning to adopt pre-sintering technologies for local automotive, electronics, and medical applications, signaling a broadening addressable market.
This comprehensive research report examines key regions that drive the evolution of the Pre-sintering Furnace market, offering deep insights into regional trends, growth factors, and industry developments that are influencing market performance.
- Americas
- Asia-Pacific
- Europe, Middle East & Africa
Key Company Profiles and Competitive Positioning
Competitive intensity is driven by a mix of global incumbents and specialized regional players, each leveraging unique strengths. Carbolite Gero Ltd. and Harper International have distinguished themselves through modular furnace platforms that support rapid retrofits and digital integration. CM Furnaces, Inc., and Deltech Furnaces emphasize customization, offering tailored chamber configurations and proprietary control software. Meanwhile, Harrop Industries, Inc., and Serena Engineering focus on niche applications, delivering ultra-high-temperature capabilities for specialty ceramics.
Heraeus Holding and Ipsen USA capitalize on material science expertise, providing integrated solutions that pair furnace hardware with advanced sensor technologies. Keith Company and Metech Inc. excel in maintenance and service networks, ensuring minimal downtime for critical operations. Linn High Therm GmbH and Nabertherm GmbH are renowned for energy-efficient designs that align with stringent environmental regulations, while MTI Corporation and The Nabertherm Group offer scalable solutions spanning benchtop to production-scale systems. Finally, Zircar Zirconia, Inc. differentiates itself through high-performance refractory components, supporting furnace longevity and consistent performance under harsh operating conditions.
This comprehensive research report delivers an in-depth overview of the principal market players in the Pre-sintering Furnace market, evaluating their market share, strategic initiatives, and competitive positioning to illuminate the factors shaping the competitive landscape.
- Carbolite Gero Ltd.
- CM Furnaces, Inc.
- Deltech Furnaces
- Harper International
- Harrop Industries, Inc.
- Heraeus Holding
- Ipsen USA
- Keith Company
- Linn High Therm GmbH
- Metech Inc.
- MTI Corporation
- Nabertherm GmbH
- Serena Engineering
- The Nabertherm Group
- Zircar Zirconia, Inc.
Actionable Recommendations for Industry Leaders
Acting decisively will secure competitive advantage amid evolving market conditions. Manufacturers should prioritize adoption of advanced heating technologies-such as induction and microwave systems-to improve cycle times and reduce energy consumption. Investing in digital twins and predictive maintenance platforms will further optimize throughput and minimize unplanned downtime.
Supply-chain resilience demands diversification of component sourcing, including partnerships with domestic fabricators to mitigate tariff-related cost pressures. Collaborations with materials research institutes can accelerate development of novel alloys and ceramics, enhancing furnace flexibility across emerging applications. Additionally, establishing modular furnace architectures will enable rapid reconfiguration for new materials or process parameters, supporting both high-volume production and low-volume customization.
From a regional perspective, aligning product roadmaps with local regulations-particularly in EMEA and North America-will facilitate market access, while tailored service models can strengthen customer relationships. Finally, integrating sustainability metrics into design and operations will not only reduce environmental impact but also resonate with end-users seeking greener manufacturing solutions.
Explore AI-driven insights for the Pre-sintering Furnace market with ResearchAI on our online platform, providing deeper, data-backed market analysis.
Ask ResearchAI anything
World's First Innovative Al for Market Research
Conclusion: Navigating Innovation and Resilience
In summary, the pre-sintering furnace market is poised for continued evolution, shaped by technological breakthroughs, shifting trade policies, and regional growth differentials. Stakeholders who embrace advanced heating mechanisms, invest in digital process controls, and diversify supply chains will be best positioned to capture new opportunities. Segmentation analysis underscores the importance of flexible furnace designs that address specific application requirements-from aerospace components to dental prosthetics-while regional insights highlight the need for tailored strategies in mature and emerging markets alike. By forging strategic partnerships in materials research and adopting energy-efficient architectures, furnace manufacturers and end users can achieve both performance excellence and sustainability goals. As the industrial landscape grows more competitive, proactive investment in innovation and resilience will determine market leadership moving forward.
This section provides a structured overview of the report, outlining key chapters and topics covered for easy reference in our Pre-sintering Furnace market comprehensive research report.
- Preface
- Research Methodology
- Executive Summary
- Market Overview
- Market Dynamics
- Market Insights
- Cumulative Impact of United States Tariffs 2025
- Pre-sintering Furnace Market, by Technology
- Pre-sintering Furnace Market, by Application
- Pre-sintering Furnace Market, by Material Type
- Pre-sintering Furnace Market, by Furnace Design
- Pre-sintering Furnace Market, by End-User Industry
- Pre-sintering Furnace Market, by Production Volume
- Pre-sintering Furnace Market, by Market Size
- Pre-sintering Furnace Market, by Energy Consumption
- Americas Pre-sintering Furnace Market
- Asia-Pacific Pre-sintering Furnace Market
- Europe, Middle East & Africa Pre-sintering Furnace Market
- Competitive Landscape
- ResearchAI
- ResearchStatistics
- ResearchContacts
- ResearchArticles
- Appendix
- List of Figures [Total: 32]
- List of Tables [Total: 1117 ]
Call to Action: Engage with Ketan Rohom for Full Market Insights
To explore comprehensive market insights and detailed analyses tailored for strategic decision-making, contact Ketan Rohom, Associate Director, Sales & Marketing, for further discussion and report access. Elevate your competitive edge with the full market research report today.
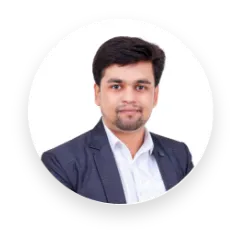
- When do I get the report?
- In what format does this report get delivered to me?
- How long has 360iResearch been around?
- What if I have a question about your reports?
- Can I share this report with my team?
- Can I use your research in my presentation?