Introduction to Precision Machining Diamond Tools
Precision machining diamond tools have become an indispensable component in high-performance manufacturing environments, enabling exceptional precision, durability, and efficiency. From monocrystalline cutting inserts to high-power laser-precision solutions, these tools support critical applications in aerospace, automotive, medical device manufacturing, and more. As industries demand ever-smaller tolerances and faster throughput, diamond-based tooling technologies continue to evolve, delivering microscopic accuracy, extended service life, and reduced maintenance costs. This executive summary provides a comprehensive overview of the market dynamics, transformative trends, and strategic insights that industry leaders must consider to remain competitive.
In recent years, accelerating digitalization, renewable energy investments, and rising demand for lightweight materials have reshaped tool requirements. Concurrently, geopolitical developments and evolving regulatory landscapes have influenced supply chains, pricing strategies, and regional competitiveness. The following sections explore these shifts, analyze segmentation nuances, assess tariff impacts, and highlight regional and competitive landscapes. Finally, actionable recommendations will guide decision-makers in capitalizing on emerging opportunities and mitigating risks in this fast-paced market.
Transformative Shifts Reshaping the Market Landscape
Over the past decade, the precision machining diamond tools market has undergone transformative shifts driven by advanced manufacturing techniques, sustainability imperatives, and digital integration. Additive and subtractive manufacturing processes now coexist, with hybrid 3D machining platforms leveraging diamond tooling to achieve complex geometries and ultra-fine finishes in a single setup. Meanwhile, laser-precision tools have gained prominence for non-contact material removal, enabling burr-free cuts in brittle substrates. This convergence of technologies has expanded the application envelope, facilitating the machining of composites, ceramics, and high-hardness metals with unprecedented speed and quality.
Simultaneously, end-use industries have elevated performance expectations. Aerospace manufacturers demand monocrystalline cutting tools for airframe rivets and engine components that withstand extreme temperatures and cyclic stresses. Automotive OEMs prioritize drilling tools optimized for carbon fiber-reinforced plastics and steel carbides to reduce vehicle weight and improve fuel efficiency. The medical device sector relies on submicron tools for implantable components and surgical instrumentation, requiring the utmost precision and biocompatibility. These evolving requirements have catalyzed material innovations, such as nanometric diamond coatings and submicron tool geometries, which further enhance service life and process stability.
Furthermore, digital twins and IoT-enabled tool monitoring now offer real-time performance data, enabling predictive maintenance and process optimization. As a result, manufacturers can minimize downtime, reduce scrap rates, and maximize throughput-driving both cost savings and competitive differentiation. These transformative dynamics underscore the imperative for tool providers and end-users to invest in R&D, forge strategic partnerships, and adopt agile manufacturing paradigms to thrive in this rapidly evolving landscape.
Analyzing the Cumulative Impact of U.S. Tariffs in 2025
In 2025, newly enacted tariffs in the United States will impose increased duties on diamond tool imports, reflecting broader trade policy shifts aimed at protecting domestic industries. These measures are likely to raise landed costs for monocrystalline and polycrystalline cutting tools imported from key suppliers, compelling end-users to reevaluate sourcing strategies. High-precision grinding wheels, especially cylindrical and surface variants sourced from global suppliers, will face heightened duty burdens, translating into price adjustments along the value chain.
Consequently, several downstream effects will emerge. Domestic manufacturers of chemical vapor deposition and physical vapor deposition tools may experience renewed demand as buyers seek to offset higher import costs with locally produced alternatives. At the same time, distributors and large enterprises will need to reassess inventory policies and negotiate long-term contracts to stabilize pricing. SMEs and small workshop operators could face affordability challenges, potentially slowing adoption rates for advanced diamond tooling solutions.
Moreover, the tariff environment may accelerate regional sourcing diversification, with importers turning to Asia-Pacific producers that benefit from free trade agreements. This shift will intensify competition among global tool manufacturers and could spur collaborative ventures to establish local production facilities in North America. In this way, the cumulative tariff impact will not only influence pricing and procurement decisions but also reshape the competitive landscape, supply chain resilience, and investment priorities through 2025 and beyond.
Key Segmentation Insights Across Multiple Dimensions
A granular examination of market segments reveals distinct growth drivers and innovation hotspots across tool types, material applications, end-use industries, technologies, customer categories, product functionalities, and production processes. In the cutting tools category, monocrystalline inserts continue to lead in high-wear applications while polycrystalline variants gain traction for cost-sensitive projects. Core drill bits and twist drill bits serve the drilling segment, addressing deep-hole and high-speed drilling requirements in hard metals and composites. Blank trimming and broaching tools support forming operations in reinforced concrete and implant manufacturing, whereas cylindrical and surface grinding wheels deliver fine finishes on ceramic and glass fiber components.
Material application diversity further shapes tooling needs. Composite machining demands diamond-coated tools optimized for carbon fiber and glass fiber laminates, while hard metals such as carbide and steel require tools with superior toughness. Non-metallic components, including ceramics and graphite, benefit from laser-precision ablation and submicron grinding. End-use industries manifest unique tool profiles: aerospace relies on airframe and engine component tooling, automotive focuses on engine manufacturing and transmission systems, construction and infrastructure prioritize reinforced concrete cutting and stone quarrying solutions, and medical device manufacturing emphasizes implant tools and surgical instruments with biocompatible coatings.
Technological segmentation highlights the rise of 3D machining platforms integrating additive and subtractive processes, alongside high-power and low-power laser-precision tools tailored for various material removal rates. Customer type distinctions reveal that large enterprises and SMEs drive industrial usage, while individual hobbyists and small workshop owners influence retail demand. Functionality-based differentiation underscores a clear split between high-precision microscopic and submicron tools versus standard-precision millimetric and nanometric options. Finally, production process advancements in chemical vapor deposition have unlocked thick and thin film applications, while physical vapor deposition tools employing electron beam and ion beam techniques deliver ultra-hard coatings for extended tool life.
This comprehensive research report categorizes the Precision Machining Diamond Tools market into clearly defined segments, providing a detailed analysis of emerging trends and precise revenue forecasts to support strategic decision-making.
- Type of Diamond Tools
- Material Application
- End-Use Industry
- Technology
- Customer Type
- Product Functionality
- Production Process
Key Regional Insights Driving Market Dynamics
Regional dynamics play a pivotal role in shaping supply chains, pricing strategies, and innovation ecosystems across the precision machining diamond tools market. In the Americas, strong aerospace and automotive hubs foster continuous investments in submicron and nanometric tools, supported by initiatives to localize production and reduce lead times. North American policies incentivize reshoring of high-tech manufacturing, encouraging partnerships between tool providers and OEMs to develop customized diamond-coated solutions for engine and structural components.
Across Europe, the Middle East & Africa, a mature machine tool base and stringent environmental regulations drive the adoption of sustainable machining practices, with growing demand for chemical vapor deposition tools that minimize waste. Germany, France, and Italy remain innovation centers for high-precision grinding wheels and advanced broaching solutions. In the Middle East, infrastructure megaprojects fuel stone quarrying and reinforced concrete cutting requirements, while Africa’s mining sector expands usage of core drill bits in mineral extraction.
The Asia-Pacific region exhibits the highest growth momentum, underpinned by rapid industrialization, urbanization, and manufacturing capacity expansions in China, India, Japan, and South Korea. Composite material machining for electric vehicle components and renewable energy systems propels demand for high-power laser-precision tools. Additionally, cost-competitive production capabilities in Southeast Asia attract outsourcing of physical vapor deposition and electron beam tool manufacturing. These regional nuances underscore the need for tailored go-to-market strategies and localized R&D efforts to address divergent customer requirements and regulatory landscapes.
This comprehensive research report examines key regions that drive the evolution of the Precision Machining Diamond Tools market, offering deep insights into regional trends, growth factors, and industry developments that are influencing market performance.
- Americas
- Asia-Pacific
- Europe, Middle East & Africa
Leading Companies and Their Strategic Positioning
Competition in the precision machining diamond tools market remains intense, with established and emerging players vying for market share through innovation, strategic alliances, and capacity expansion. Cerobear GmbH and DIANAMIC Abrasive Products Inc. have invested significantly in monocrystalline and polycrystalline cutting tool development, focusing on novel substrate formulations that enhance wear resistance. Ehwa Diamond Industrial Co., Ltd. and Element Six lead in advanced grinding wheel technologies, leveraging proprietary diamond coating processes to extend tool life in high-volume production.
Funik Ultrahard Material Co., Ltd. and Hunan Supreme Carbide Co., Ltd. have capitalized on China’s burgeoning manufacturing sector, scaling production of core drill bits, twist drill bits, and broaching tools for both domestic and export markets. Hyperion Materials & Technologies and Kennametal Inc. maintain strong global footprints, integrating laser-precision tooling solutions with IoT-enabled performance monitoring platforms. Kyocera Corporation and Mitsuhiro Tool Works, Ltd. continue to push boundaries in submicron and nanometric tool geometries for semiconductor and medical device applications.
Saint-Gobain S.A. and Sandvik AB harness cross-industry expertise to offer chemical vapor deposition and physical vapor deposition tools, while Shinhan Diamond Ind. Co., Ltd. and Sumitomo Electric Hardmetal Corp. focus on high-power laser and additive manufacturing tool adaptations. System 3R International AB and US Synthetic Corporation have differentiated themselves through precision workholding systems and synthetic diamond substrate innovations, respectively. These competitive strategies illustrate a landscape where R&D investment, regional partnerships, and digital service offerings define leadership positions.
This comprehensive research report delivers an in-depth overview of the principal market players in the Precision Machining Diamond Tools market, evaluating their market share, strategic initiatives, and competitive positioning to illuminate the factors shaping the competitive landscape.
- Cerobear GmbH
- DIANAMIC Abrasive Products Inc.
- Ehwa Diamond Industrial Co., Ltd.
- Element Six
- Funik Ultrahard Material Co., Ltd.
- Hunan Supreme Carbide Co., Ltd.
- Hyperion Materials & Technologies
- Kennametal Inc.
- Kyocera Corporation
- Mitsuhiro Tool Works, Ltd.
- Saint-Gobain S.A.
- Sandvik AB
- Shinhan Diamond Ind. Co. , Ltd.
- Sumitomo Electric Hardmetal Corp.
- System 3R International AB
- US Synthetic Corporation
Actionable Recommendations for Industry Leaders
To capitalize on the evolving market environment, industry leaders should adopt a multi-pronged strategy that blends technological innovation, supply chain resilience, and customer-centric service models. First, accelerating R&D in next-generation diamond materials-such as nanostructured coatings and hybrid composite substrates-will unlock performance gains in wear resistance and thermal stability. Leaders should collaborate with academic institutions and materials research centers to fast-track development cycles and validate tool performance under real-world operating conditions.
Second, diversifying manufacturing footprints across the Americas, EMEA, and Asia-Pacific will mitigate tariff exposure and supply disruptions. Establishing regional production hubs or strategic partnerships can reduce lead times and provide cost advantages. Simultaneously, implementing advanced planning systems and digital twin technologies will enhance demand forecasting and inventory optimization, enabling a more agile response to market fluctuations.
Third, embedding IoT-based tool monitoring and predictive maintenance services will deliver tangible value to customers by lowering downtime and improving yield. Packaging these offerings with performance-based contract models can foster long-term relationships and drive recurring revenue streams. Finally, investing in workforce upskilling programs-focused on CNC programming, laser tool operation, and data analytics-will empower internal teams and end-users to fully leverage advanced diamond tooling capabilities, ensuring sustained competitive differentiation.
Explore AI-driven insights for the Precision Machining Diamond Tools market with ResearchAI on our online platform, providing deeper, data-backed market analysis.
Ask ResearchAI anything
World's First Innovative Al for Market Research
Conclusion: Navigating a Dynamic Market Environment
The precision machining diamond tools market stands at a critical juncture, shaped by rapid technological advancements, shifting trade policies, and diverse regional demands. Companies that invest in material innovation, digital integration, and geographic diversification will emerge as frontrunners, delivering superior performance and cost efficiency to end-users across aerospace, automotive, construction, and medical sectors. By embracing predictive maintenance services, performance-based contracts, and targeted R&D partnerships, tool providers can build resilient ecosystems that adapt quickly to market changes.
Additionally, aligning go-to-market strategies with regional nuances-from reshoring initiatives in North America to sustainability mandates in Europe and capacity expansions in Asia-Pacific-will be essential. A customer-centric approach that blends high-precision tool offerings with comprehensive service packages will not only drive loyalty but also create barriers to entry for competitors. Ultimately, success will hinge on the ability to balance innovation with operational excellence, ensuring that advanced diamond tooling solutions deliver measurable productivity gains and sustainable value creation.
This section provides a structured overview of the report, outlining key chapters and topics covered for easy reference in our Precision Machining Diamond Tools market comprehensive research report.
- Preface
- Research Methodology
- Executive Summary
- Market Overview
- Market Dynamics
- Market Insights
- Cumulative Impact of United States Tariffs 2025
- Precision Machining Diamond Tools Market, by Type of Diamond Tools
- Precision Machining Diamond Tools Market, by Material Application
- Precision Machining Diamond Tools Market, by End-Use Industry
- Precision Machining Diamond Tools Market, by Technology
- Precision Machining Diamond Tools Market, by Customer Type
- Precision Machining Diamond Tools Market, by Product Functionality
- Precision Machining Diamond Tools Market, by Production Process
- Americas Precision Machining Diamond Tools Market
- Asia-Pacific Precision Machining Diamond Tools Market
- Europe, Middle East & Africa Precision Machining Diamond Tools Market
- Competitive Landscape
- ResearchAI
- ResearchStatistics
- ResearchContacts
- ResearchArticles
- Appendix
- List of Figures [Total: 30]
- List of Tables [Total: 1160 ]
Call to Action: Engage with Expert Insights Now
To explore detailed analyses, segmentation breakdowns, and strategic frameworks tailored to your organization’s needs, contact Ketan Rohom, Associate Director of Sales & Marketing, to secure your comprehensive market research report today. Leverage expert insights and actionable recommendations to stay ahead of the competition and drive growth in the precision machining diamond tools market.
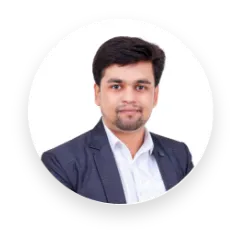
- When do I get the report?
- In what format does this report get delivered to me?
- How long has 360iResearch been around?
- What if I have a question about your reports?
- Can I share this report with my team?
- Can I use your research in my presentation?