Introduction to the Precision Metal Cold Forging Machinery Ecosystem
The precision metal cold forging machinery sector underpins high-value manufacturing processes across critical industries by enabling the efficient transformation of metal blanks into complex geometries without the need for melting. As global demand intensifies for lightweight, high-strength components in automotive, aerospace, medical and industrial segments, manufacturers are pursuing advanced cold forging solutions that deliver superior dimensional accuracy, material savings and shortened production cycles. Rising pressures to reduce carbon footprints and adhere to stringent sustainability standards have further accelerated adoption of cold forging, which minimizes energy consumption and scrap generation compared to traditional hot forging techniques.
Recent advancements in servo-driven presses, closed‐loop controls and sensor integration have elevated machine performance to unprecedented levels, supporting micro-forging applications for medical devices and high-volume production of engine components. Simultaneously, digital twins and predictive analytics are reshaping maintenance strategies, ensuring uninterrupted uptime and consistent quality. As supply chains evolve in complexity, end users are seeking partners offering turnkey cold forging systems, comprehensive support services and seamless integration with downstream assembly processes.
Against this backdrop of rapid technological innovation and shifting market dynamics, industry stakeholders must navigate an increasingly intricate landscape to capitalize on emerging opportunities and mitigate risks. This executive summary provides an in-depth exploration of the transformative trends, policy headwinds, segmentation drivers and regional dynamics that are redefining the future of cold forging machinery.
Transformative Shifts Reshaping the Cold Forging Machinery Landscape
The landscape of precision metal cold forging machinery is undergoing transformative shifts driven by digitalization, geopolitical realignments and sustainability mandates. First, the surge in Industry 4.0 adoption has catalyzed the deployment of smart forging cells equipped with real-time monitoring, closed‐loop feedback and automated material handling, resulting in dramatic gains in throughput and repeatability. Next, supply chain resilience initiatives are prompting nearshoring of critical forging operations, reducing lead times and mitigating exposure to cross-border disruptions.
Concurrently, the transition toward electrification in automotive and aerospace sectors has generated heightened demand for lightweight alloy components, spurring investments in high-tonnage presses capable of handling aluminum, titanium and specialty alloys. In parallel, regulatory frameworks aimed at carbon reduction are compelling manufacturers to re-evaluate energy-intensive hot forging processes in favor of cold forging, which boasts lower per-unit energy consumption and minimal post-process machining.
Moreover, a new wave of collaboration between machine tool builders, software developers and materials scientists is accelerating the commercialization of hybrid forging technologies that integrate hydraulic, electromagnetic and mechanical actuation to optimize force distribution and cycle times. Taken together, these developments are redefining machine tool design paradigms and reshaping competitive dynamics across the global cold forging ecosystem.
Cumulative Impact of U.S. Tariffs in 2025 on Cold Forging Operations
The imposition of new U.S. tariffs in 2025 has introduced a significant layer of complexity for suppliers and end users in the precision cold forging arena. Components sourced from regions subject to elevated duties are now up to 25 percent more costly, prompting manufacturers to reassess vendor portfolios and explore alternative supply corridors. In response, many forging equipment producers have accelerated the establishment of production hubs in duty-free zones or within the United States to preserve cost competitiveness and shorten delivery windows.
This tariff landscape has also encouraged deeper collaboration between forging machine builders and local fabricators, resulting in joint ventures that bypass traditional import channels. Additionally, OEMs are renegotiating contracts to include tariff-adjustment clauses, hedging against future policy changes. While these measures have successfully mitigated short-term price inflation, they have also diversified the supplier base and increased complexity in quality assurance and compliance processes.
Looking ahead, the enduring impact of these tariff measures will hinge on the ability of industry players to develop agile procurement frameworks, enhance transparency across multi-tier supply chains and leverage digital documentation systems for real-time duty management. Firms that adapt swiftly to this new trade environment will gain a strategic advantage through stabilized input costs and fortified supply resilience.
Key Segmentation Insights Across Product, Capacity, Application and Technology
The precision metal cold forging machinery market can be dissected across multiple dimensions, each revealing unique growth drivers and adoption barriers. Segmentation based on product type encompasses Double Disc Forging Machines, Horizontal Presses and Vertical Presses, with each category optimized for distinct force distribution and throughput requirements. When viewed through the lens of forging capacity, the spectrum ranges from small forging up to 20 ton to medium forging between 20 and 100 ton, and large forging above 100 ton, addressing everything from high-precision micro-components to structural parts.
Application-based segmentation highlights critical sectors such as Aerospace Components, Automotive Parts, Health & Medical Devices and Industrial Equipment. Within aerospace components, focus areas include aircraft engines and airframe subassemblies; automotive parts concentrate on engine components and transmission parts; medical devices prioritize surgical instruments; and industrial equipment spans agricultural machinery and heavy construction tools. End users are similarly distributed across Aerospace & Defense, Automotive, Heavy Engineering and the Medical Industry, with the automotive segment further categorized into commercial vehicles and passenger cars.
Material type plays a pivotal role in machine specification, with aluminum & alloys, carbon steel, copper alloys and titanium and specialty materials each presenting unique formability and lubrication challenges. Sales channels range from direct engagements with OEMs to partnerships with distributors & dealers and the expanding footprint of online platforms. Technological orientation divides the market into automatic and semi-automatic machinery, hydraulic forging technology and mechanical forging technology, each offering varying degrees of cycle efficiency. Temperature regimes differentiate cold forging from hot and warm forging processes, while automation level spans manual, semi-automated and fully automated systems. Finally, die type considerations-closed die, impression die and open die-dictate design complexity, tool sourcing and maintenance cycles.
This comprehensive research report categorizes the Precision Metal Cold Forging Machinery market into clearly defined segments, providing a detailed analysis of emerging trends and precise revenue forecasts to support strategic decision-making.
- Product Type
- Forging Capacity
- Application
- End-User Industry
- Material Type
- Sales Channel
- Technology
- Forging Temperature
- Automation Level
- Die Type
Key Regional Dynamics Shaping Precision Forging Demand
Regional dynamics in the precision cold forging machinery sector reveal distinct adoption patterns and competitive advantages. In the Americas, a mature automotive industry and robust aerospace programs drive demand for high-tonnage presses and integrated forging cells. National initiatives to bolster domestic manufacturing have further incentivized capital investment in advanced cold forging assets.
Shifting focus to Europe, Middle East & Africa, stringent emissions regulations and a resurgence of defense spending are fueling procurement of cold forging equipment capable of processing titanium and specialty alloys. Local machine tool builders are integrating green energy strategies and circular economy principles to align with regulatory mandates and consumer expectations.
Meanwhile, Asia-Pacific continues to exhibit rapid expansion powered by rising industrialization in emerging markets and large-scale infrastructure projects. Domestic forging equipment manufacturers are leveraging cost advantages to capture share, while established global suppliers partner with regional firms to enhance service networks and localize spare parts inventories. Across all regions, interoperability with downstream assembly lines and compliance with industry-specific standards remain core selection criteria.
This comprehensive research report examines key regions that drive the evolution of the Precision Metal Cold Forging Machinery market, offering deep insights into regional trends, growth factors, and industry developments that are influencing market performance.
- Americas
- Asia-Pacific
- Europe, Middle East & Africa
Competitive Intelligence: Profiles of Leading Forging Equipment Manufacturers
The competitive landscape of precision metal cold forging machinery features a blend of heritage machine tool builders and agile newcomers. AIDA Engineering, Ltd. and ANDRITZ Kaiser GmbH maintain strong footholds in specialized forging presses, leveraging decades of metallurgical expertise to deliver high-precision systems. Chin Fong Machine Industrial Co., Ltd. and Daisho Seiki Corporation capitalize on scalable production lines and customizable automation packages to serve high-volume automotive clients.
Japanese firms such as Enomoto Machine Co., Ltd. and Sakamura Machine Co., Ltd. drive innovation in micro-forging and multi-stage operations, while European stalwarts FAGOR ARRASATE S. Coop. and Schuler AG focus on large-tonnage presses and turnkey plant installations. German entities KNUTH Werkzeugmaschinen GmbH and SMS Group GmbH emphasize energy efficiency and advanced process control platforms, whereas Nidec Corporation and Komatsu Ltd. offer integrated mechatronic solutions that blend electric drives with hydraulic actuation.
At the same time, companies such as Hatebur Metalforming Equipment, Ltd., JIER Machine-Tool Group Co., Ltd. and WFL Millturn Technologies GmbH & Co. KG are expanding their global service footprints and digital offerings to meet the evolving needs of end users seeking predictive maintenance and remote diagnostics. This diverse array of competitors ensures a dynamic market environment, fostering continuous innovation and customer-centric enhancements.
This comprehensive research report delivers an in-depth overview of the principal market players in the Precision Metal Cold Forging Machinery market, evaluating their market share, strategic initiatives, and competitive positioning to illuminate the factors shaping the competitive landscape.
- AIDA Engineering, Ltd.
- ANDRITZ Kaiser GmbH
- Chin Fong Machine Industrial Co., Ltd.
- Daisho Seiki Corporation
- Enomoto Machine Co., Ltd.
- FAGOR ARRASATE S. Coop.
- Hatebur Metalforming Equipment, Ltd.
- JIER Machine-Tool Group Co., Ltd.
- KNUTH Werkzeugmaschinen GmbH
- Komatsu Ltd.
- Nidec Corporation
- Sakamura Machine Co., Ltd.
- Schuler AG
- SMS Group GmbH
- WFL Millturn Technologies GmbH & Co. KG
Actionable Strategies for Industry Leadership and Growth
Industry leaders can capitalize on emerging opportunities by implementing a set of targeted, actionable strategies. First, forging equipment providers should accelerate integration of digital twins and AI-driven predictive maintenance tools into new machine platforms, ensuring continuous performance optimization and minimal unplanned downtime. Second, manufacturers need to broaden their alloy processing capabilities by investing in multi-material tool libraries and advanced lubrication systems tailored to lightweight and specialty metals.
Third, establishing modular automation kits that can be retrofitted onto existing presses will create scalable upgrade paths for end users, extending equipment lifecycles and generating recurring revenue streams. Fourth, fostering strategic alliances with component suppliers and systems integrators in key regions will enhance supply chain agility and local service delivery, mitigating the impact of trade barriers and logistics disruptions.
Fifth, companies should formalize sustainability roadmaps, setting clear targets for energy consumption per cycle and scrap reduction. Transparent reporting on greenhouse gas emissions and resource utilization will strengthen ESG credentials and resonate with corporate procurement teams. Finally, sales and marketing functions must embrace consultative, solution-based engagement, showcasing end-to-end process insights and total cost of ownership analyses to shift the conversation from price competition to value creation.
Explore AI-driven insights for the Precision Metal Cold Forging Machinery market with ResearchAI on our online platform, providing deeper, data-backed market analysis.
Ask ResearchAI anything
World's First Innovative Al for Market Research
Conclusion: Navigating the Future of Cold Forging Machinery
In summary, the precision metal cold forging machinery market stands at the intersection of technological revolution, regulatory evolution and shifting trade dynamics. Smart automation, advanced material handling and strategic localization are emerging as critical success factors, while tariff-induced supply chain realignment underscores the need for procurement agility. By harnessing data-driven maintenance, modular automation solutions and sustainable manufacturing principles, equipment providers and end users can secure competitive advantage and achieve resilient, future-ready operations.
This section provides a structured overview of the report, outlining key chapters and topics covered for easy reference in our Precision Metal Cold Forging Machinery market comprehensive research report.
- Preface
- Research Methodology
- Executive Summary
- Market Overview
- Market Dynamics
- Market Insights
- Cumulative Impact of United States Tariffs 2025
- Precision Metal Cold Forging Machinery Market, by Product Type
- Precision Metal Cold Forging Machinery Market, by Forging Capacity
- Precision Metal Cold Forging Machinery Market, by Application
- Precision Metal Cold Forging Machinery Market, by End-User Industry
- Precision Metal Cold Forging Machinery Market, by Material Type
- Precision Metal Cold Forging Machinery Market, by Sales Channel
- Precision Metal Cold Forging Machinery Market, by Technology
- Precision Metal Cold Forging Machinery Market, by Forging Temperature
- Precision Metal Cold Forging Machinery Market, by Automation Level
- Precision Metal Cold Forging Machinery Market, by Die Type
- Americas Precision Metal Cold Forging Machinery Market
- Asia-Pacific Precision Metal Cold Forging Machinery Market
- Europe, Middle East & Africa Precision Metal Cold Forging Machinery Market
- Competitive Landscape
- ResearchAI
- ResearchStatistics
- ResearchContacts
- ResearchArticles
- Appendix
- List of Figures [Total: 36]
- List of Tables [Total: 683 ]
Call to Action: Engage with Ketan Rohom for In-Depth Market Insights
To explore this comprehensive market research report and gain deeper insights into emerging trends, competitive benchmarks and strategic imperatives, contact Ketan Rohom, Associate Director, Sales & Marketing. Engage now to unlock tailored solutions that will guide your organization’s growth in the precision cold forging arena.
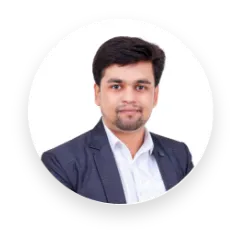
- When do I get the report?
- In what format does this report get delivered to me?
- How long has 360iResearch been around?
- What if I have a question about your reports?
- Can I share this report with my team?
- Can I use your research in my presentation?