Introduction to the Precision Welding Device Market
The precision welding device market stands at the forefront of industrial innovation, enabling seamless fusion of materials with unparalleled accuracy. Fueled by breakthroughs in automation, control systems, and advanced power sources, these devices are redefining manufacturing standards across sectors. As demand for high-quality, durable joints surges, businesses seek solutions that marry consistency with speed, driving investments into fully automatic, semi-automatic, and manual welding platforms.
This executive summary navigates the evolving technological landscape, examines regulatory and tariff influences shaping competitive dynamics, and distills critical segmentation, regional, and company-level insights. Leaders will uncover actionable strategies to harness emerging trends, mitigate risks, and capitalize on growth opportunities in aerospace, automotive, energy, shipbuilding, construction, healthcare, and broader manufacturing realms. By engaging with this concise yet comprehensive analysis, stakeholders can align their initiatives with market realities and position their organizations for sustained success.
Transformative Shifts Reshaping Welding Technologies
Industry paradigms are shifting as digital transformation, additive manufacturing, and Industry 4.0 frameworks penetrate traditional welding operations. Artificial intelligence–enabled control systems now orchestrate electron beam, laser, plasma arc, and ultrasonic welding processes, optimizing parameters in real time to reduce defects and scrap. Meanwhile, advancements in power sources-from conventional electric arc to hybrid configurations-are broadening material compatibility, accommodating aluminum, composite materials, steel variants, and titanium alloys with greater precision.
Moreover, the convergence of robotics and welding has accelerated cycle times, unlocking new possibilities in mass production and precision manufacturing alike. As smart factories proliferate, connectivity standards and IoT integration are elevating predictive maintenance, offering unprecedented visibility into equipment health. This transformative environment demands that providers and end users adopt agile strategies to keep pace with rapid technological obsolescence and evolving customer expectations.
Cumulative Impact of United States Tariffs 2025
Recent adjustments to United States tariff regimes have introduced complexity to cross-border supply chains, particularly for components and subassemblies integral to precision welding devices. Manufacturers sourcing critical parts-such as specialized laser generators or AI control units-from key international hubs now navigate elevated import duties, prompting a reassessment of sourcing strategies and inventory management.
Domestic producers face both headwinds and opportunities as tariff-related cost pressures incentivize onshore production of essential modules. In certain instances, localized manufacturing hubs have emerged to circumvent tariff burdens, stimulating innovation and reinforcing supply security. At the same time, corporations must remain vigilant to regulatory fluctuations, adopting flexible procurement frameworks and leveraging strategic partnerships to minimize disruption and maintain competitive pricing.
Key Segmentation Insights Across Product, Application, Material, and User
A granular understanding of market segmentation is essential for tailoring solutions and marketing approaches. Product type differentiation reveals that fully automatic welding devices lead adoption in high-throughput environments, while semi-automatic equipment bridges the gap between flexibility and efficiency, and manual units continue to serve small-scale workshops and maintenance teams. Application-driven insights show aerospace stakeholders demand both manufacturing-grade and maintenance-and-repair operations capabilities, whereas automotive players span from original equipment manufacturers to custom fabricators and aftermarket service providers. Energy sector requirements range from stringent nuclear compliance to oil and gas infrastructure welding and renewable energy component assembly, and shipyards allocate resources to commercial vessel construction and military-grade fabrication.
Material type diversity underscores the importance of aluminum and composite welding expertise for lightweight structures, with steel-both carbon and stainless variants-remaining ubiquitous in heavy-duty fabrication alongside emerging titanium applications. End-user industry analysis highlights that commercial construction and infrastructure projects leverage welding devices for structural steelwork, while medical device manufacturers and surgical instrument makers require micrometer-level precision. Consumer goods manufacturers and heavy machinery producers each prioritize reliability and throughput in their welding processes.
Technological segmentation demonstrates that electron beam and plasma arc welding cater to specialized, high-precision tasks, while laser welding-encompassing both CO2 and fiber laser modalities-balances speed and minimal heat-affected zones. Ultrasonic welding finds its niche in delicate assemblies and nonmetallic joins. The choice of power source-whether electric arc, gas-fueled, or hybrid-directly influences operational costs and environmental footprint. Control systems vary from AI-enabled platforms offering self-optimization, through analog setups valued for simplicity, to digital frameworks subdivided into microcontroller-based and PLC-controlled architectures. Purpose-driven deployment ranges from mass production lines with relentless cycle requirements to precision manufacturing of complex geometries and early-stage prototyping. Finally, user classification distinguishes between large corporations operating mass production facilities and R&D departments, and skilled professionals in small enterprises and workshops who require accessible, versatile solutions.
This comprehensive research report categorizes the Precision Welding Device market into clearly defined segments, providing a detailed analysis of emerging trends and precise revenue forecasts to support strategic decision-making.
- Product Type
- Application
- Material Type
- End-User Industry
- Technology Used
- Power Source
- Control System
- Purpose
- User-based Classification
Key Regional Insights Highlighting Global Market Dynamics
Regional dynamics shape investment priorities and competitive positioning. In the Americas, demand is propelled by a robust manufacturing base and accelerating adoption of automated welding cells in automotive and aerospace clusters. Tax incentives and regional trade agreements further stimulate domestic production of high-value modules. Within Europe, Middle East & Africa, emphasis lies on sustainability and energy-efficient welding technologies, driven by stringent emissions regulations and industrial modernization initiatives across the European Union and Gulf Cooperation Council states.
The Asia-Pacific region continues to lead in production volume, with emerging markets in Southeast Asia and India expanding their capacity for shipbuilding, construction, and renewables infrastructure. China remains a powerhouse for both device manufacturing and heavy industry applications, while Japan and South Korea focus on high-precision, laser-based solutions for electronics and medical device sectors. Across all regions, localized service networks and technical training programs are proving decisive for end-user adoption and long-term loyalty.
This comprehensive research report examines key regions that drive the evolution of the Precision Welding Device market, offering deep insights into regional trends, growth factors, and industry developments that are influencing market performance.
- Americas
- Asia-Pacific
- Europe, Middle East & Africa
Key Company Insights from Leading Device Providers
Competitive landscapes are defined by both multinational conglomerates and specialized innovators. Arcon Welding Equipment, LLC distinguishes itself through cost-effective manual and semi-automatic systems tailored to small enterprises. Colfax Corporation leverages its diversified portfolio to integrate additive manufacturing with advanced welding solutions. Daihen Corporation focuses on robotic welding automation and AI-driven process control, whereas Fronius International GmbH emphasizes energy-efficient power sources and seamless IoT connectivity.
Hobart Brothers Company has built a reputation on consumable and accessory synergies that enhance overall welding performance. Hypertherm, Inc. leads in high-precision plasma and laser cutting technologies that complement welding operations. Lincoln Electric Holdings, Inc. and Miller Electric Mfg. LLC maintain strong footholds in both arc welding equipment and digital control innovations. Panasonic Industry Europe GmbH delivers fiber laser expertise for microjoint fabrication, while The ESAB Group, Inc. capitalizes on global service networks and comprehensive training solutions to sustain customer engagement.
This comprehensive research report delivers an in-depth overview of the principal market players in the Precision Welding Device market, evaluating their market share, strategic initiatives, and competitive positioning to illuminate the factors shaping the competitive landscape.
- Arcon Welding Equipment, LLC
- Colfax Corporation
- Daihen Corporation
- Fronius International GmbH
- Hobart Brothers Company
- Hypertherm, Inc.
- Lincoln Electric Holdings, Inc.
- Miller Electric Mfg. LLC
- Panasonic Industry Europe GmbH
- The ESAB Group, Inc.
Actionable Recommendations for Industry Leaders
Industry leaders should prioritize investment in AI-enabled control systems to optimize weld quality and throughput. By collaborating with digital platform providers, organizations can establish predictive maintenance protocols that reduce unplanned downtime. In parallel, diversifying the supply chain through regional manufacturing partnerships can mitigate tariff-induced cost pressures and enhance resilience.
Moreover, integrating modular power sources-such as hybrid electric-gas configurations-can offer end users flexibility to adapt to fluctuating energy prices and regulatory demands. Strategic alliances with materials specialists will accelerate the development of welding parameters for advanced composites and titanium alloys. Finally, targeted workforce training programs are essential to cultivate the skilled talent required for operating sophisticated welding cells, ensuring that technological investments yield maximum ROI.
Explore AI-driven insights for the Precision Welding Device market with ResearchAI on our online platform, providing deeper, data-backed market analysis.
Ask ResearchAI anything
World's First Innovative Al for Market Research
Conclusion and Strategic Imperatives
As precision welding continues to evolve, stakeholders who embrace digitalization, automation, and agile sourcing will secure a competitive edge. A nuanced grasp of segmentation, regional variances, and vendor capabilities enables informed decision-making and fosters innovation. By aligning product roadmaps with emerging applications-from renewable energy assembly to advanced medical device fabrication-companies can capitalize on high-growth niches while reinforcing core capabilities.
Ultimately, success hinges on the ability to anticipate market needs, invest in robust control architectures, and cultivate partnerships that drive continuous improvement. Through proactive adaptation to regulatory shifts and technological breakthroughs, industry participants can maintain operational excellence and unlock new avenues for value creation.
This section provides a structured overview of the report, outlining key chapters and topics covered for easy reference in our Precision Welding Device market comprehensive research report.
- Preface
- Research Methodology
- Executive Summary
- Market Overview
- Market Dynamics
- Market Insights
- Cumulative Impact of United States Tariffs 2025
- Precision Welding Device Market, by Product Type
- Precision Welding Device Market, by Application
- Precision Welding Device Market, by Material Type
- Precision Welding Device Market, by End-User Industry
- Precision Welding Device Market, by Technology Used
- Precision Welding Device Market, by Power Source
- Precision Welding Device Market, by Control System
- Precision Welding Device Market, by Purpose
- Precision Welding Device Market, by User-based Classification
- Americas Precision Welding Device Market
- Asia-Pacific Precision Welding Device Market
- Europe, Middle East & Africa Precision Welding Device Market
- Competitive Landscape
- ResearchAI
- ResearchStatistics
- ResearchContacts
- ResearchArticles
- Appendix
- List of Figures [Total: 34]
- List of Tables [Total: 948 ]
Call to Action: Secure the Market Research Report with Ketan Rohom
To deepen your understanding of the precision welding device market and gain access to comprehensive data, analysis, and strategic guidance, reach out to Ketan Rohom (Associate Director, Sales & Marketing at 360iResearch). Secure your copy of the full market research report today and empower your organization with insights that drive growth and innovation.
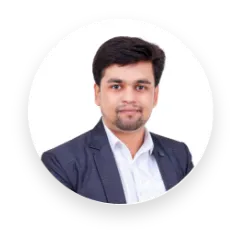
- When do I get the report?
- In what format does this report get delivered to me?
- How long has 360iResearch been around?
- What if I have a question about your reports?
- Can I share this report with my team?
- Can I use your research in my presentation?