Introduction: The Critical Role of Protective Coatings in Semiconductor Fabrication
The semiconductor industry faces an escalating demand for high-performance, reliable fabrication equipment, where protective coatings play a critical role in safeguarding sensitive surfaces, enhancing operational lifespan, and ensuring process purity. As chip architectures shrink and manufacturing processes evolve, the performance demands on coating materials have intensified. Next-generation devices require stringent control of contamination, electrostatic discharge, thermal stress, and mechanical wear, all of which can be mitigated through advanced protective layering.
Against this backdrop, stakeholders across the value chain-from equipment manufacturers and service providers to semiconductor foundries and integrated device manufacturers-are seeking coatings that deliver corrosion resistance, moisture barriers, and ESD protection without compromising precision or throughput. Emerging material innovations, tailored application techniques, and strategic partnerships are converging to redefine coating standards. Consequently, decision makers must grasp the underlying trends and drivers that shape this critical segment of semiconductor fabrication.
This executive summary outlines the transformative shifts altering the landscape, examines the cumulative impact of new U.S. tariffs in 2025, distills key segmentation and regional insights, profiles leading players, and delivers actionable recommendations. It serves as a concise yet comprehensive guide for executives, engineers, and procurement specialists aiming to navigate competitive pressures and technological complexity while optimizing coating strategies for next-generation fabrication equipment.
Transformative Shifts in the Protective Coatings Landscape
In recent years, the protective coatings market for semiconductor equipment has undergone significant metamorphosis driven by multiple parallel forces. First, material science breakthroughs have propelled hybrid and nano-engineered coatings from prototype to production stage. These advanced solutions combine organic-inorganic hybrids and nano metal formulations to deliver unprecedented barrier performance against corrosive process gases, particulate contamination, and thermal cycling. At the same time, waterborne polyurethanes and low-VOC silicones are rising to meet stringent environmental and workplace safety regulations, marking a departure from solvent-based chemistries that once dominated factory floors.
Second, digital transformation initiatives such as predictive maintenance and Industry 4.0 integration are reshaping how coatings are specified and monitored. Real-time sensor feedback on temperature, humidity, and coating integrity is enabling adaptive process controls that extend maintenance intervals and minimize unplanned downtime. This shift is paralleled by the adoption of smart packaging coatings embedded with sensors to track environmental exposure, signaling a future where coatings themselves become active data sources.
Finally, strategic alliances between coating formulators, equipment OEMs, and semiconductor manufacturers are accelerating co-development cycles. Joint research programs leverage shared risk and domain expertise to tailor formulations to specific etch, deposition, and lithography tools. This collaborative approach not only reduces time-to-market for next-gen coatings but also fosters standardized qualification protocols, improving interoperability and simplifying global sourcing strategies. Together, these transformative shifts underscore a landscape defined by innovation, sustainability, and cross-sector collaboration.
Cumulative Impact of U.S. Tariffs on Coating Materials in 2025
The introduction of new U.S. tariffs in 2025 on certain coating materials and precursor chemicals has introduced a complex layer of cost and supply-chain considerations for semiconductor equipment manufacturers. Tariffs targeting select solvent-borne acrylics, specialty silicones, and nano-metal additives have elevated landed costs in the Americas by an estimated mid-single digit percentage, exerting pressure on sourcing decisions and product margins.
In response, buyers are diversifying their supplier base, increasing procurement from Europe and Asia-Pacific regions where tariff exposure is lower. This rebalancing of trade flows has triggered capacity expansion among coating formulators in duty-advantaged jurisdictions, while stimulating local production initiatives in the U.S. to reduce reliance on imports.
Simultaneously, equipment OEMs are collaborating with formulator partners to reformulate key protective layers, prioritizing tariff-exempt chemistries such as waterborne epoxies and thermoplastic polyimides. By migrating to these alternatives, manufacturers can preserve performance characteristics-corrosion resistance, moisture barrier integrity, and ESD protection-while mitigating cost escalation.
Ultimately, the cumulative impact of 2025 tariffs has accelerated innovation in low-tariff formulations and reshaped global sourcing strategies, underscoring the importance of agile supply-chain planning and material flexibility in maintaining competitive advantage.
Key Segmentation Insights Across Materials, Applications, Channels, Technologies, and End Users
A comprehensive view of the coatings market reveals distinct performance and sourcing dynamics across five segmentation lenses. When dissecting material type, acrylics-both solvent-borne and waterborne-continue to serve as versatile, cost-effective barriers, while epoxies evolve from solvent-based to water-based systems that reduce VOC emissions. Polyimides, ranging from thermoplastic to thermoset grades, deliver robust thermal stability for high-temperature process modules. Polyurethanes, particularly acrylic and waterborne variants, offer balanced flexibility and chemical resistance, and silicones-especially anti-corrosive and low-VOC formulations-meet the dual demands of process purity and regulatory compliance.
Viewing the market through the prism of application, corrosion-resistant layers leverage ceramic and metal oxide coatings to protect against acid etch ambient, while ESD protection depends on conductive and dissipative coatings to prevent charge buildup. Moisture resistance is achieved with hydrophobic or superhydrophobic surfaces that repel cleaning fluids and deionized water, whereas thermal management calls for heat-dissipating and insulating coatings to maintain uniform temperature profiles. Wear resistance is provided by abrasion- and scratch-resistant formulations, safeguarding critical mechanical components from particle-induced damage.
Distribution channel analysis highlights the dual importance of direct and indirect sales. In-person interactions through specialized distributors and wholesalers remain vital for high-value equipment retrofits, complemented by online procurement via B2B platforms and company websites for standard maintenance kits. Indirect channels, including select retailers and third-party distributors, expand reach into aftermarket service networks.
Technology type segmentation distinguishes advanced coatings-such as biopolymer hybrids, nano polymer, and emerging smart-packaging solutions-from traditional dip and powder coating techniques. While dip coating and powder processes retain cost advantages for bulk applications, hybrid and nano coatings are increasingly specified for mission-critical assets.
Finally, end-user industry segmentation underscores the diverse demand drivers across equipment manufacturing, maintenance and repair services-including in-house and independent providers-and semiconductor manufacturers spanning foundries and integrated device manufacturers alike. Each segment exhibits unique material preferences and service expectations, necessitating tailored go-to-market strategies.
This comprehensive research report categorizes the Protective Coating for Semiconductor Fabrication Equipment market into clearly defined segments, providing a detailed analysis of emerging trends and precise revenue forecasts to support strategic decision-making.
- Material Type
- Application
- Distribution Channel
- Technology Type
- End-User Industry
Key Regional Insights in the Americas, EMEA, and Asia-Pacific
Regional dynamics shape coating adoption priorities and supply-chain strategies. In the Americas, a focus on near-shoring and sustainability has driven investments in waterborne and low-VOC chemistries, while the region’s wafer fab expansions amplify demand for moisture and corrosion-resistant solutions. Europe, Middle East & Africa (EMEA) emphasize regulatory compliance and environmental stewardship, accelerating uptake of solvent-free epoxies and advanced nano coatings. Sustainable manufacturing initiatives and circular economy policies in EMEA are fostering closed-loop formulation recycling and reclamation programs.
In Asia-Pacific, rapid fab construction in Taiwan, South Korea, China, and Japan sustains robust growth in protective coatings, with local formulator alliances ensuring supply-chain resilience. Manufacturers in the region are pioneering smart-packaging coatings embedded with IoT sensors to streamline MRO workflows. Collectively, these regional dynamics underscore the need for coating suppliers to align product portfolios and operational footprints with local regulatory frameworks, cost structures, and technology roadmaps.
This comprehensive research report examines key regions that drive the evolution of the Protective Coating for Semiconductor Fabrication Equipment market, offering deep insights into regional trends, growth factors, and industry developments that are influencing market performance.
- Americas
- Asia-Pacific
- Europe, Middle East & Africa
Key Company Insights from Global Protective Coatings Leaders
Leading global formulators are actively shaping the protective coatings market through innovation, strategic partnerships, and capacity enhancements. AkzoNobel N.V. continues to advance hybrid coating platforms by integrating biopolymer technologies with traditional solvent-based systems. Axalta Coating Systems, Ltd. has expanded its nano-metal additive portfolio to address emerging ESD and thermal management requirements. BASF SE leverages its petrochemical heritage to optimize waterborne epoxy chemistries for low-emission cleanrooms.
Hempel A/S is reinforcing its footprint in Asia-Pacific through joint ventures focused on localized silicone production, while Henkel AG & Co. KGaA’s research pipelines prioritize anti-corrosive and superhydrophobic formulations. Höganäs AB and Oerlikon Metco are collaborating on ceramic and metal oxide coatings to accelerate corrosion resistance for high-throughput etch tools. PPG Industries, Inc. and The Sherwin-Williams Company remain stalwart suppliers of powder and dip coating solutions, even as they pilot next-gen smart-packaging layers. Praxair Surface Technologies, Inc., Saint-Gobain S.A., and Sulzer Ltd. round out the competitive landscape with targeted innovations in wear-resistant and insulating coatings, each leveraging proprietary deposition technologies to enhance process reliability.
Together, these companies illustrate the diverse strategies-ranging from eco-friendly chemistries to cutting-edge nanotechnology-that are driving the market forward.
This comprehensive research report delivers an in-depth overview of the principal market players in the Protective Coating for Semiconductor Fabrication Equipment market, evaluating their market share, strategic initiatives, and competitive positioning to illuminate the factors shaping the competitive landscape.
- AkzoNobel N.V.
- Axalta Coating Systems, Ltd.
- BASF SE
- Hempel A/S
- Henkel AG & Co. KGaA
- Höganäs AB
- Oerlikon Metco
- PPG Industries, Inc.
- Praxair Surface Technologies, Inc.
- Saint-Gobain S.A.
- Sulzer Ltd.
- The Sherwin-Williams Company
Actionable Recommendations for Coating and Equipment Leaders
To capitalize on emerging opportunities and mitigate tariff-related risks, industry leaders should adopt a multifaceted approach. First, prioritize development and qualification of low-tariff, waterborne, and solvent-free coating formulations that maintain performance parity with legacy materials while aligning with evolving environmental regulations. This proactive reformulation roadmap will safeguard margins and support global market access.
Second, establish cross-functional teams that integrate R&D, supply-chain, and field service experts to co-develop customized coating solutions with strategic customers. Co-creation not only accelerates product validation cycles but also deepens customer partnerships, reducing the likelihood of competitive displacement.
Third, expand digital monitoring capabilities by embedding sensors and RFID markers within packaging and coating substrates to enable predictive maintenance analytics. Leveraging real-time data will optimize recoat intervals, streamline inventory management, and unlock new value-added services for equipment operators.
Finally, pursue selective geographic expansion through joint ventures or contract manufacturing in tariff-advantaged regions. Localized production will dampen the impact of future trade policy shifts and reinforce supply continuity, particularly in high-growth Asia-Pacific and Americas markets.
Explore AI-driven insights for the Protective Coating for Semiconductor Fabrication Equipment market with ResearchAI on our online platform, providing deeper, data-backed market analysis.
Ask ResearchAI anything
World's First Innovative Al for Market Research
Conclusion: Navigating the Future of Protective Coatings in Chip Manufacturing
The protective coatings sector for semiconductor fabrication equipment is at a pivotal juncture, driven by technological innovation, shifting regulatory landscapes, and evolving supply-chain dynamics. Advanced materials-ranging from nano coatings to solvent-free epoxies-are redefining performance benchmarks, while smart integration and digitalization elevate coatings from passive protectants to active contributors in maintenance workflows. At the same time, tariff pressures and environmental mandates underscore the need for agile formulation strategies and localized production footprints.
By synthesizing the latest market intelligence, segmentation analysis, and competitive profiling, stakeholders can craft informed strategies that balance performance, cost, and compliance. Embracing co-development partnerships, diversifying sourcing, and leveraging data-driven maintenance will be key differentiators in a rapidly evolving landscape. As the semiconductor industry continues its trajectory toward smaller nodes and higher wafer yields, the role of robust, intelligent, and sustainable protective coatings will only grow more essential.
This section provides a structured overview of the report, outlining key chapters and topics covered for easy reference in our Protective Coating for Semiconductor Fabrication Equipment market comprehensive research report.
- Preface
- Research Methodology
- Executive Summary
- Market Overview
- Market Dynamics
- Market Insights
- Cumulative Impact of United States Tariffs 2025
- Protective Coating for Semiconductor Fabrication Equipment Market, by Material Type
- Protective Coating for Semiconductor Fabrication Equipment Market, by Application
- Protective Coating for Semiconductor Fabrication Equipment Market, by Distribution Channel
- Protective Coating for Semiconductor Fabrication Equipment Market, by Technology Type
- Protective Coating for Semiconductor Fabrication Equipment Market, by End-User Industry
- Americas Protective Coating for Semiconductor Fabrication Equipment Market
- Asia-Pacific Protective Coating for Semiconductor Fabrication Equipment Market
- Europe, Middle East & Africa Protective Coating for Semiconductor Fabrication Equipment Market
- Competitive Landscape
- ResearchAI
- ResearchStatistics
- ResearchContacts
- ResearchArticles
- Appendix
- List of Figures [Total: 26]
- List of Tables [Total: 1118 ]
Call-To-Action: Engage with Ketan Rohom to Acquire the Full Market Research Report
To access detailed insights, technical specifications, and strategic guidance tailored to your organization’s needs, reach out to Ketan Rohom, Associate Director, Sales & Marketing. Elevate your coating strategies and secure competitive advantage with a comprehensive market research report designed for decision-makers in the semiconductor equipment ecosystem.
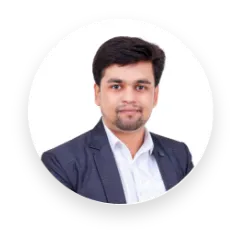
- When do I get the report?
- In what format does this report get delivered to me?
- How long has 360iResearch been around?
- What if I have a question about your reports?
- Can I share this report with my team?
- Can I use your research in my presentation?