Introduction to the Strategic Importance of Pultrusion Dies
Pultrusion dies serve as the critical component in shaping continuous profiles by guiding resin-impregnated fibers through heated tooling, ensuring structural integrity, dimensional accuracy, and surface finish. As industries increasingly seek lightweight, high-strength, and corrosion-resistant materials, the pultrusion die market has emerged as a focal point for manufacturers aiming to meet demanding performance criteria across transportation, construction, energy, and industrial applications. This executive summary explores the evolving environment of pultrusion dies, highlighting how innovation in tooling design and materials compatibility drives competitive advantage. By examining key transformations triggered by sustainability initiatives, digital integration, and shifting supply chains, this summary equips decision-makers with insights into how to adapt processes, optimize costs, and harness emerging opportunities without delving into granular quantitative projections. With the ongoing convergence of advanced composites and automation, dies are no longer passive molds but active enablers of higher throughput, tighter tolerances, and custom geometries. Understanding these dynamics and their implications will empower stakeholders to invest strategically in die technologies that align with performance goals, regulatory landscapes, and evolving customer demands.
Transformative Shifts Redefining Die Technology and Processes
Over the past decade, the pultrusion die landscape has undergone transformative shifts, propelled by three interlinked forces. First, sustainability imperatives have spurred material innovation beyond traditional glass fibers, ushering in carbon and aramid reinforcements that demand die materials with enhanced wear resistance and thermal conductivity. Second, the rise of Industry 4.0 practices has integrated sensors and real-time monitoring into die assemblies, enabling predictive maintenance and tighter quality control. Dies equipped with embedded temperature and pressure sensors now deliver consistent curing profiles, reducing scrap rates and unplanned downtime. Third, the globalization of supply chains-accelerated by digital procurement platforms-has broadened access to specialty die steels and coatings, fostering collaboration between tooling suppliers and composite processors. As a result, dies are becoming more modular and adaptable, capable of handling multiple resin systems and fiber architectures within a single setup. Together, these disruptive trends are redefining die performance benchmarks, shortening development cycles, and elevating the strategic role of tooling partners in meeting both technical and commercial objectives.
Navigating the Cumulative Impact of U.S. Tariffs in 2025
The implementation of new United States tariffs in 2025 on imported steel and aluminum variants has exerted significant pressure across the pultrusion die ecosystem. Increased duty burdens on high-quality alloy steel grades used for die blocks have driven tooling costs upward, prompting die manufacturers to explore alternative substrates and to negotiate long-term agreements with domestic steel mills. Meanwhile, tariffs on aluminum alloys such as 6061 and 7075 have translated into raw material surcharges, compelling some processors to redesign die geometries for greater material efficiency. On the resin side, cost escalations have led to selective reformulation of composite matrices, which in turn affects cure kinetics and die heating requirements. The cumulative effect has been a shift in supplier relationships, with many end users consolidating die orders to secure volume discounts and mitigate price volatility. To maintain competitive pricing, industry leaders are also investing in advanced coating technologies that extend die life, offsetting initial cost increases by reducing maintenance intervals and unplanned production halts.
Comprehensive Segmentation Insights Across Materials, Applications, and Processes
Material type segmentation reveals that aluminum variants (5052, 6061, 7075) remain favored for low-cost, moderate-strength tooling, yet composite materials including aramid, carbon, and glass fibers are gaining traction where corrosion resistance and lightweight characteristics are paramount. Steel variants-spanning alloy, carbon, and stainless grades-continue to dominate high-volume production runs requiring exceptional durability. Across application categories, the automotive sector’s demand for pultruded chassis and body components is driving dies optimized for rapid cycle times, while the construction industry’s focus on building facades and structural panels prioritizes die versatility to accommodate varying cross-sectional profiles. In the electrical and electronics segment, dies tailored for cable trays and transformer components emphasize tight dimensional tolerances. End-user types differ in tooling expectations: consumer products manufacturers seek cost-effective dies for furniture and appliances, energy sector operators require specialized tooling for solar panel frames and wind turbine blades, and heavy industrial players demand robust dies capable of withstanding abrasive resin blends. Product form analysis shows H-beams, I-beams, and T-rails in profile forms rapidly evolving in cross-sectional complexity, sheet forms like corrugated and perforated designs gaining traction in architectural applications, and tube forms addressing both structural and conduit needs. Manufacturing process insights underscore growing adoption of hybrid processes that combine hot and cold pultrusion to expand material compatibility, while distribution channels-from OEM bulk orders and aftermarket replacement parts to e-commerce direct sales-shape expectations around lead times, customization levels, and technical support.
This comprehensive research report categorizes the Pultrusion Dies market into clearly defined segments, providing a detailed analysis of emerging trends and precise revenue forecasts to support strategic decision-making.
- Material Type
- Application Category
- End-User Type
- Product Form
- Manufacturing Process
- Distribution Channel
Key Regional Dynamics Driving Die Demand and Technology Adoption
Regional dynamics in the Americas reflect strong uptake in infrastructure renewal projects across North America, where stringent regulatory standards for material safety and fire performance favor stainless steel and composite-reinforced die solutions. Latin American markets show opportunistic growth in construction and energy, with localized die manufacturing clusters emerging to reduce dependence on imports. In Europe, Middle East & Africa, environmental regulations in the EU have catalyzed the adoption of eco-friendly die coatings and extended tool life cycles, while Middle Eastern energy projects drive demand for dies suited to oil and gas infrastructure components. African markets, though nascent, present long-term potential as mining and transportation sectors invest in corrosion-resistant pultruded profiles. The Asia-Pacific region remains the largest consumer by volume, propelled by rapid urbanization in China and India and ongoing investment in renewable energy installations. Domestic die producers in this region are increasingly integrating digital quality assurance systems to meet both local and export specifications, creating a competitive landscape that emphasizes speed, cost efficiency, and adaptability to diverse composite matrices.
This comprehensive research report examines key regions that drive the evolution of the Pultrusion Dies market, offering deep insights into regional trends, growth factors, and industry developments that are influencing market performance.
- Americas
- Asia-Pacific
- Europe, Middle East & Africa
Profiling the Competitive Landscape and Leading Tooling Innovators
Among industry leaders, Bedford Reinforced Plastics has distinguished itself through proprietary die designs that enhance fiber alignment, while Composiflex, Inc. leverages rapid prototyping capabilities to shorten development cycles. Creative Pultrusions, Inc. focuses on turnkey die solutions, integrating heating elements and sensors for turnkey installations. Exel Composites balances global reach with localized support, customizing die coatings for varied environmental conditions. Fibergrate Composite Structures Inc. underscores product safety by adhering to stringent fire-retardant standards in its die tooling. Fiberline Composites A/S invests heavily in sustainable die materials and energy-efficient heat management. Gordon Composites prioritizes modular die platforms that facilitate on-site adjustments. National Composites, Inc. and Röchling Group both emphasize research partnerships to pioneer multi-material dies, while Strongwell Corporation’s extensive portfolio spans heavy-equipment profiles. Tecton Products delivers hybrid process expertise, and Washington Penn Plastic Co., Inc. combines steel and composite technologies to extend die life under abrasive applications. Collectively, these players are driving innovation through strategic collaborations, robust R&D investments, and a focus on lifecycle performance.
This comprehensive research report delivers an in-depth overview of the principal market players in the Pultrusion Dies market, evaluating their market share, strategic initiatives, and competitive positioning to illuminate the factors shaping the competitive landscape.
- Bedford Reinforced Plastics
- Composiflex, Inc.
- Creative Pultrusions, Inc.
- Exel Composites
- Fibergrate Composite Structures Inc.
- Fiberline Composites A/S
- Gordon Composites
- National Composites, Inc.
- Röchling Group
- Strongwell Corporation
- Tecton Products
- Washington Penn Plastic Co., Inc.
Actionable Recommendations for Tooling Manufacturers and End Users
Industry leaders should invest in next-generation sensor integration within die assemblies to enable real-time data analytics and condition-based maintenance strategies that reduce unplanned downtime. Adopting modular die architectures will facilitate rapid reconfiguration for diverse material systems and cross-sectional profiles, promoting agility in responding to customer specifications. Strategic partnerships with steel mills and coating specialists can secure stable raw material pricing and accelerate the development of corrosion- and wear-resistant surfaces. Collaborating with composite resin suppliers to co-develop formulations optimized for specific die thermal properties will streamline cure cycles and improve throughput. Furthermore, companies must scale digital training programs for operators, ensuring that new tooling technologies and quality monitoring systems are fully leveraged. Finally, exploring additive manufacturing techniques for rapid die prototyping can shorten lead times and facilitate design iterations, positioning tooling providers as value-added partners rather than mere component suppliers.
Explore AI-driven insights for the Pultrusion Dies market with ResearchAI on our online platform, providing deeper, data-backed market analysis.
Ask ResearchAI anything
World's First Innovative Al for Market Research
Conclusion: Positioning for Sustainable Growth and Competitive Advantage
As the pultrusion die sector advances, organizations that align design philosophies with sustainable materials, digital excellence, and resilient supply chains will outpace competitors. Embracing an integrated approach-where tooling, resin, and fiber systems are co-optimized-will ensure consistent part quality, lower total cost of ownership, and faster time to market. By monitoring tariff developments and maintaining flexible sourcing strategies, companies can mitigate cost pressures while maintaining high performance standards. Equally important is fostering collaborative ecosystems involving die designers, composite formulators, and end users to drive continuous improvement. Those who adopt predictive maintenance regimens and invest in operator training will unlock the full potential of smart tooling, translating technical advancements into measurable productivity gains. Ultimately, the capacity to deliver customized, high-precision profiles at competitive rates will define leadership in an increasingly complex pultrusion landscape.
This section provides a structured overview of the report, outlining key chapters and topics covered for easy reference in our Pultrusion Dies market comprehensive research report.
- Preface
- Research Methodology
- Executive Summary
- Market Overview
- Market Dynamics
- Market Insights
- Cumulative Impact of United States Tariffs 2025
- Pultrusion Dies Market, by Material Type
- Pultrusion Dies Market, by Application Category
- Pultrusion Dies Market, by End-User Type
- Pultrusion Dies Market, by Product Form
- Pultrusion Dies Market, by Manufacturing Process
- Pultrusion Dies Market, by Distribution Channel
- Americas Pultrusion Dies Market
- Asia-Pacific Pultrusion Dies Market
- Europe, Middle East & Africa Pultrusion Dies Market
- Competitive Landscape
- ResearchAI
- ResearchStatistics
- ResearchContacts
- ResearchArticles
- Appendix
- List of Figures [Total: 28]
- List of Tables [Total: 1085 ]
Call-To-Action: Connect with Ketan Rohom to Secure the Full Research Report
To gain a deeper understanding of die innovation strategies and benchmark your organization against industry best practices, contact Ketan Rohom (Associate Director, Sales & Marketing) to purchase the comprehensive market research report and propel your pultrusion initiatives forward.
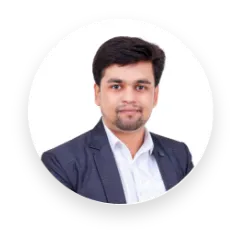
- When do I get the report?
- In what format does this report get delivered to me?
- How long has 360iResearch been around?
- What if I have a question about your reports?
- Can I share this report with my team?
- Can I use your research in my presentation?