Unveiling the Dynamics of Physical Vapor Deposition Equipment Shaping Precision Surface Engineering in Aerospace, Automotive, and Medical Industries
Physical vapor deposition (PVD) equipment represents a cornerstone of modern surface engineering, delivering high-precision coatings that extend functionality and performance across critical industries. Over recent years, PVD technologies have evolved from niche laboratory tools to high-throughput manufacturing systems, reflecting their growing importance in sectors demanding durability, corrosion resistance, and aesthetic enhancement. As the pace of product innovation accelerates, coating engineers and production leaders increasingly rely on PVD platforms to introduce novel material combinations, refine film thickness control, and optimize process repeatability. Consequently, understanding the nuances of PVD equipment capabilities has become essential for any organization seeking to maintain a competitive edge in an era defined by rapid technological advancement and stringent performance requirements.
This executive summary delves into the drivers, disruptors, and strategic considerations shaping the PVD equipment market, offering decision-makers a concise yet detailed overview of industry dynamics. Drawing on a rigorous research framework, it highlights transformative shifts, regulatory influences such as recent trade measures, and critical segmentation insights that illuminate key value pools. By synthesizing regional and competitive landscapes, the report equips stakeholders with a robust foundation for investment planning, technology adoption, and partnership development. The insights presented here set the stage for a deeper exploration of market opportunities and challenges, guiding executives through the complex ecosystem of material science, process engineering, and global supply chains.
Exploring the Technological Innovations and Market Disruptions Revolutionizing the Physical Vapor Deposition Equipment Industry in 2025
The PVD equipment landscape is in the midst of fundamental transformation, driven by converging forces of technological innovation, sustainability imperatives, and digitalization. On the technological front, advanced sputtering processes such as high-power impulse magnetron sputtering (HiPIMS) and cathodic arc deposition are enhancing film density and adhesion, enabling new coating functionalities tailored to demanding use cases. In parallel, the integration of in-situ monitoring tools, real-time process analytics, and closed-loop feedback systems supports tighter process control, reduces yield variability, and accelerates time to market. Consequently, adoption is shifting toward modular, digitally enabled cluster solutions capable of rapid reconfiguration to meet evolving product specifications.
Sustainability has emerged as a powerful catalyst for change, prompting equipment manufacturers to emphasize energy efficiency, resource conservation, and waste minimization. Developers are exploring lower-temperature deposition pathways and eco-friendly target materials to align with corporate environmental targets and regulatory standards. Meanwhile, the rise of Industry 4.0 has reinforced the importance of connected equipment, where IoT-enabled sensors, predictive maintenance algorithms, and cloud-based performance dashboards drive uptime improvements and cost savings. As a result, PVD platforms are being reimagined not only as coating tools but also as data engines, unlocking new value from historical process archives and cross-site benchmarking.
These transformative shifts underscore a broader market realignment, where customers prioritize flexible, intelligent solutions that address the twin challenges of product differentiation and operational resilience. Equipment vendors are responding with collaborative development models, offering service-oriented arrangements and software subscriptions that align with customers’ evolving needs. In this dynamic environment, organizations that harness digital ecosystems and embrace sustainable design principles will capture early-mover advantages, positioning themselves as leaders in a rapidly maturing market.
Assessing How 2025 U.S. Trade Tariffs Reshape Supply Chains and Cost Structures in the Physical Vapor Deposition Equipment Market
Recent trade policy developments in the United States have introduced a new layer of complexity for PVD equipment manufacturers and end-users, reshaping sourcing strategies and cost structures. In early 2025, additional tariffs of 25 percent on imports from Canada and Mexico, along with a 10 percent levy on select Chinese goods, were enacted to address broader trade and security objectives. Subsequently, a universal baseline tariff of ten percent on all imports was rolled out in the spring of 2025, further elevating landed equipment and spares costs. These measures have disrupted historically efficient supply chains, compelling stakeholders to reassess vendor partnerships and component origins to mitigate tariff exposure and maintain budgetary discipline.
In response, leading suppliers have initiated dual strategies: diversifying manufacturing footprints by establishing regional assembly hubs in tariff-neutral territories and renegotiating long-term agreements to lock in favorable material pricing. Meanwhile, equipment purchasers are scrutinizing total cost of ownership more closely, balancing upfront capital expenditures against projected operating expenses. Although the tariffs have introduced pricing pressure, they have also catalyzed renewed investment in domestic production capabilities, as stakeholders recognize the strategic benefits of supply chain resilience and reduced geopolitical risk. Over time, this realignment is anticipated to strengthen the domestic PVD ecosystem, fostering greater agility in responding to sudden policy shifts and international trade fluctuations.
Consequently, understanding the cumulative impact of these trade measures is critical. Organizations that proactively map tariff implications across product lines, redesign processes for tariff avoidance, and engage in scenario planning will emerge more resilient. In contrast, those that delay strategic responses risk margin erosion and supply bottlenecks. As the policy environment continues to evolve, maintaining clear visibility into tariff schedules and regulatory updates will be essential for securing competitive advantage in a challenging global market.
Gaining Strategic Insights Through Multi-Dimensional Segmentation of the Physical Vapor Deposition Equipment Market Across Industries and Materials
A granular examination of the PVD equipment market through multiple segmentation lenses reveals distinct opportunity pockets and strategic considerations. When viewed by end use industry, demand is particularly robust in aerospace and defense, where engine components, interior fixtures, and structural parts must endure extreme conditions. Automotive applications span exterior trim, functional mechanical parts, and interior decorative surfaces, each requiring tailored coating chemistries. In the electronics and semiconductor domain, high-throughput deposition tools are optimized for consumer electronics and wafer-fabrication processes, while the medical device sector leverages PVD for diagnostic equipment, implant coatings, and surgical instrument enhancements. Optical markets, including camera lenses, decorative optics, and specialty filters, rely on ultra-thin, uniform films to achieve precise optical properties.
Turning to equipment type, magnetron sputtering variants such as DC, radio frequency, and HiPIMS systems are selected when dense, high-purity films are paramount, whereas cathodic arc deposition-both filtered and unfiltered-addresses niche applications requiring advanced material phases. Electron beam evaporation, available in high-purity and standard platforms, remains a mainstay for metallic and compound coatings. Ion plating, whether beam-assisted or standard, and thermal evaporation techniques-induction or resistive-cater to varied material compatibility and production volume requirements.
Coating material choice further differentiates market segments, spanning carbides such as chromium and tungsten carbide, carbon materials including diamond-like carbon and graphite, and metal coatings like aluminum, chromium, and titanium. Nitride variants, notably chromium nitride and titanium nitride, deliver enhanced hardness, while oxide coatings-aluminum oxide and titanium oxide-ensure superior corrosion and wear resistance. Machine configurations, from load-lock and notch batch operations to conveyor and roll-to-roll inline systems, are selected based on throughput targets and substrate geometry. Finally, vacuum levels ranging from medium to ultra-high vacuum determine process stability and film quality, with specific applications demanding stringent vacuum control to achieve defect-free coatings.
Mapping these segmentation dimensions against customer priorities uncovers high-value intersections. For instance, combining HiPIMS technology with titanium nitride films for automotive functional components unlocks performance gains, while ultra-high vacuum DC sputtering of aluminum oxide satisfies rigorous optical clarity requirements. By aligning product roadmaps with such tailored segmentation insights, market participants can optimize R&D investments and accelerate time-to-revenue in their core industrial verticals.
This comprehensive research report categorizes the PVD Coating Equipment market into clearly defined segments, providing a detailed analysis of emerging trends and precise revenue forecasts to support strategic decision-making.
- End Use Industry
- Equipment Type
- Coating Material
- Application
- Machine Configuration
- Vacuum Type
Decoding Regional Dynamics Driving Adoption and Growth of Physical Vapor Deposition Equipment Across the Americas, EMEA, and Asia-Pacific
Regional dynamics exert a profound influence on PVD equipment adoption, shaped by varying economic drivers, regulatory landscapes, and end-market demand patterns. In the Americas, a resurgence in domestic manufacturing and a focus on reshoring critical supply chains have amplified investment in advanced surface-treatment capabilities. Aerospace primes, automotive OEMs, and medical device manufacturers are bolstering local production networks, augmenting demand for both standard and highly specialized PVD systems. Meanwhile, supportive government initiatives aim to enhance industrial competitiveness, signaling sustained growth potential for equipment vendors willing to partner on facility expansions and localized service models.
Across Europe, the Middle East, and Africa, stringent environmental regulations and ambitious decarbonization targets are guiding equipment purchasers toward energy-efficient deposition solutions. European coating specialists lead in developing low-temperature, solvent-free processes and integrating renewable energy sources into plant operations. In the Middle East, burgeoning aerospace and electronics hubs are prioritizing high-speed, high-volume sputtering technologies, while African markets are gradually embracing PVD for mining and heavy-industry applications where corrosion resistance is critical.
Asia-Pacific continues to dominate global PVD equipment installations, fueled by large-scale investments in consumer electronics, semiconductor fabrication, and automotive assembly. China’s semiconductor build-out, South Korea’s advanced display manufacturing, and Japan’s precision optics industry are collectively driving substantial uptake of cluster tool architectures and next-generation sputtering platforms. Additionally, Southeast Asian countries are emerging as attractive low-cost manufacturing bases, prompting equipment providers to develop mid-tier configurations that balance performance with capital affordability. Through region-specific alliances and agile deployment models, suppliers can capitalize on these diverse growth trajectories and reinforce their global footprint.
This comprehensive research report examines key regions that drive the evolution of the PVD Coating Equipment market, offering deep insights into regional trends, growth factors, and industry developments that are influencing market performance.
- Americas
- Europe, Middle East & Africa
- Asia-Pacific
Profiling Industry Leaders and Emerging Innovators Shaping the Competitive Landscape of Physical Vapor Deposition Equipment Manufacturing
The competitive landscape for PVD equipment is characterized by a blend of established multinational corporations and nimble specialized innovators. Global leaders have leveraged economies of scale and broad technology portfolios to deliver turnkey cluster systems that integrate multiple deposition and process modules. These incumbents excel in servicing high-volume semiconductor and electronics fabs, where uptime guarantees and preventive maintenance programs are critical. At the same time, a cadre of technology-focused firms is pushing the envelope with bespoke solutions for niche markets such as medical implants and luxury goods, offering agile development cycles and highly customized service agreements.
Recent partnerships between equipment vendors and materials technology providers underscore the importance of end-to-end process integration. Collaborative agreements enable seamless matching of target materials, deposition parameters, and post-process treatments, reducing the trial-and-error phase that traditionally extends qualification timelines. Furthermore, aftermarket services have emerged as a key differentiator, with leading companies offering remote diagnostics, predictive maintenance, and refurbishment services that enhance system longevity and customer satisfaction.
In this competitive milieu, market entrants are carving out differentiation through digital enablement and sustainability credentials. Several small and mid-sized players have introduced cloud-native process analytics platforms that provide customers with advanced process intelligence without the overhead of legacy hardware retrofits. Others have prioritized low-temperature processes and waste-minimization features, aligning product roadmaps with the growing emphasis on circular economy principles. By monitoring these evolving competitive strategies, stakeholders can identify best practices and potential alliance opportunities that align with their strategic objectives.
This comprehensive research report delivers an in-depth overview of the principal market players in the PVD Coating Equipment market, evaluating their market share, strategic initiatives, and competitive positioning to illuminate the factors shaping the competitive landscape.
- Applied Materials, Inc.
- Oerlikon Balzers Coating AG
- ULVAC, Inc.
- IHI Ionbond AG
- Bühler Leybold Optics GmbH
- Hauzer Techno Coating B.V.
- CemeCon AG
- Angstrom Engineering Inc.
- Denton Vacuum LLC
- PVD Products, Inc.
Formulating Tactical Strategies for Industry Leaders to Capitalize on Emerging Opportunities in Physical Vapor Deposition Equipment
Industry leaders should prioritize a balanced approach that marries technological innovation with strategic flexibility. First, establishing collaborative development partnerships with key end users and materials suppliers will enable co-creation of next-generation deposition processes, reducing time-to-market and ensuring alignment with emerging performance requirements. Simultaneously, investing in modular equipment architectures and software-based process control can provide the agility needed to pivot swiftly when product roadmaps or regulatory landscapes shift. As digital ecosystems become more entrenched, manufacturers should also deploy IoT-based asset management solutions to preemptively address downtime risks and optimize maintenance schedules.
From an operational standpoint, enterprises must undertake a thorough assessment of their global supply chains in light of recent tariff developments. Companies that revisit sourcing strategies, engage in dual-sourcing agreements, and evaluate localized manufacturing options will not only mitigate cost volatility but also cultivate supply resilience. Moreover, sustainability should be woven into both product design and factory operations. By adopting lower-temperature deposition processes, recovering and recycling sputtering byproducts, and integrating renewable energy sources, organizations can strengthen their environmental credentials and address stakeholder expectations.
Leadership teams should complement these strategic imperatives with capability-building initiatives. Upskilling process engineers in advanced deposition techniques, data science, and automation will foster a culture of continuous improvement. Lastly, maintaining a robust market intelligence function that tracks regional developments, technology roadmaps, and competitor moves will ensure decision makers remain ahead of inflection points. Collectively, these recommendations form a coherent blueprint for capturing untapped opportunities and reinforcing competitive advantage in the PVD equipment market.
Understanding the Rigorous Research Framework and Analytical Approaches Underpinning the Physical Vapor Deposition Equipment Market Study
This research leverages a multi-step methodology to ensure comprehensive coverage, validated data, and actionable insights. Primary research formed the foundation, involving in-depth interviews with domain experts, end-use industry executives, and equipment OEM representatives. These qualitative inputs were complemented by detailed surveys targeting process engineers, procurement leaders, and service partners to capture real-world usage patterns, technology adoption drivers, and unmet needs.
Secondary research entailed a systematic review of industry publications, regulatory filings, patent databases, and company reports. This included analyzing press releases, equipment specification sheets, and environmental compliance documentation to quantify technology trends and sustainability initiatives. Concurrently, a thorough examination of trade and tariff announcements, along with international trade data, provided visibility into cross-border equipment flows and policy impacts.
Data triangulation was employed to reconcile discrepancies between primary and secondary findings, ensuring robustness and accuracy. Advanced analytical tools, including cluster analysis and scenario modeling, were utilized to identify high-potential market segments and project technology diffusion pathways. Expert validation sessions with senior stakeholders across major supply chain nodes further refined the research outputs and confirmed the strategic relevance of key insights. This rigorous methodology underpins the credibility of the report’s conclusions and supports confident decision-making in a rapidly evolving market.
Explore AI-driven insights for the PVD Coating Equipment market with ResearchAI on our online platform, providing deeper, data-backed market analysis.
Ask ResearchAI anything
World's First Innovative Al for Market Research
Synthesizing Key Findings and Strategic Takeaways to Guide Stakeholders in the Physical Vapor Deposition Equipment Sector
The physical vapor deposition equipment market stands at an inflection point, shaped by rapid technological progress, shifting regulatory environments, and evolving supply chain dynamics. Advanced deposition processes and digital integration are redefining performance benchmarks, while sustainability and local manufacturing initiatives are redirecting investment flows. Moreover, recent trade measures underscore the importance of proactive risk management and diversified sourcing strategies. Against this backdrop, segmentation analysis reveals targeted growth pockets-where specific combinations of technology, material, and end use intersect to deliver outsized value. Regionally, the Americas, EMEA, and Asia-Pacific each present unique adoption drivers, from reshoring incentives to decarbonization mandates and high-volume electronics build-outs.
Competitive intensity is rising, as established OEMs and specialized newcomers alike pursue differentiation through collaboration, digital enablement, and service innovation. To thrive, stakeholders must adopt a holistic approach that integrates technology development, supply chain resilience, and sustainability into a unified strategy. By aligning organizational capabilities with market imperatives and leveraging robust data-driven insights, companies can navigate uncertainty and unlock long-term growth. Ultimately, this synthesis of findings equips decision makers with a clear roadmap to capitalize on transformative industry shifts and maintain leadership in the global PVD equipment landscape.
This section provides a structured overview of the report, outlining key chapters and topics covered for easy reference in our PVD Coating Equipment market comprehensive research report.
- Preface
- Research Methodology
- Executive Summary
- Market Overview
- Market Dynamics
- Market Insights
- Cumulative Impact of United States Tariffs 2025
- PVD Coating Equipment Market, by End Use Industry
- PVD Coating Equipment Market, by Equipment Type
- PVD Coating Equipment Market, by Coating Material
- PVD Coating Equipment Market, by Application
- PVD Coating Equipment Market, by Machine Configuration
- PVD Coating Equipment Market, by Vacuum Type
- Americas PVD Coating Equipment Market
- Europe, Middle East & Africa PVD Coating Equipment Market
- Asia-Pacific PVD Coating Equipment Market
- Competitive Landscape
- ResearchAI
- ResearchStatistics
- ResearchContacts
- ResearchArticles
- Appendix
- List of Figures [Total: 30]
- List of Tables [Total: 2438 ]
Connect with Ketan Rohom to Secure Comprehensive Physical Vapor Deposition Equipment Market Insights and Drive Strategic Decision-Making
To explore in-depth market insights, emerging trends, and strategic growth levers for physical vapor deposition equipment, reach out to Ketan Rohom, Associate Director of Sales & Marketing, to learn how this comprehensive research report can inform your next strategic move. Engage with tailored analyses, scenario assessments, and actionable data that empower your organization to navigate dynamic market forces with confidence. Connect with Ketan today and secure your copy of the full market research report to stay ahead in the competitive landscape and drive impactful outcomes.
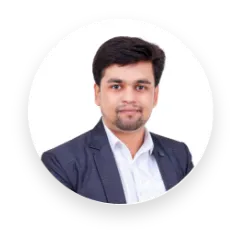
- When do I get the report?
- In what format does this report get delivered to me?
- How long has 360iResearch been around?
- What if I have a question about your reports?
- Can I share this report with my team?
- Can I use your research in my presentation?