Introduction to Rail Milling & Grinding Train Dynamics
Rail milling and grinding trains serve as critical instruments in maintaining and enhancing the safety, durability, and performance of rail networks. These specialized service trains travel along the tracks, removing irregularities and surface deformations that develop over time due to heavy loads, weathering, and daily wear. By precisely shaving off material and restoring the rail profile, they mitigate rolling resistance, reduce track-induced vibrations, and extend the life of both rails and rolling stock. With global rail operators under increasing pressure to optimize asset utilization, minimize downtime, and align with sustainability targets, the strategic deployment of advanced milling and grinding solutions has become an indispensable pillar of infrastructure management.
The rising emphasis on high-speed corridors, coupled with burgeoning commuter networks in urban centers, has intensified the demand for rail surface rehabilitation without compromising service availability. Meanwhile, technological innovations-ranging from automated material removal controls to condition-based monitoring systems-have elevated the effectiveness of milling and grinding trains, offering real-time feedback and adaptive grinding profiles that respond dynamically to rail conditions. As railway administrations navigate accelerated schedules, regulatory constraints, and evolving environmental mandates, a comprehensive understanding of the rail milling and grinding landscape is essential to unlock operational efficiencies and safeguard network integrity.
Transformative Shifts Redefining Rail Maintenance Landscape
Over the past decade, the rail milling and grinding sector has undergone transformative shifts driven by digital integration, modular design philosophies, and heightened environmental scrutiny. Advances in automation have empowered milling heads to adjust cutting depth and grinding pressure on the fly, informed by laser-based profile scanning and onboard analytics. Consequently, operators can achieve uniform railhead geometry with fewer passes, accelerating maintenance cycles and maximizing route availability.
Moreover, the transition toward modular platforms has redefined equipment flexibility. Manufacturers now offer plug-and-play modules that can be quickly configured for varied tasks-from heavy rail grinding on mainlines to fine-tuning track geometry in tight urban tunnels. This modularity not only streamlines logistics and service deployment but also lowers capital barriers for smaller network operators seeking customized solutions.
Simultaneously, sustainability mandates are reshaping propulsion choices. Electric-powered trains, once confined to electrified corridors, now integrate energy recovery systems that harvest regenerative braking energy, reducing carbon footprints and operating costs. Innovative filtration units capture particulate matter generated during grinding, aligning maintenance practices with stricter environmental regulations. As a result, this convergence of digital intelligence, modularity, and green technology is establishing a new paradigm for cost-effective, compliant, and high-performance rail surface management.
Assessing the Cumulative Impact of US Tariffs in 2025
The introduction of new tariffs by the United States in 2025 has reverberated across the global supply chain for rail maintenance equipment. Surcharges on imported steel and specialized components have inflated procurement costs for both domestic manufacturers and multinational suppliers. Consequently, original equipment manufacturers (OEMs) face pressure to localize production, re-evaluate supplier partnerships, and negotiate long-term contracts to hedge against further trade fluctuations.
At the same time, end users have responded by accelerating fleet modernization plans. Faced with higher unit prices, rail operators are demanding machines with extended service intervals and minimal consumable usage to offset upfront capital expenditures. This demand surge has favored high-performance machine offerings that promise lower total cost of ownership through longer wear part life and reduced energy consumption.
Furthermore, the tariff regime has spurred cross-border joint ventures and technology licensing agreements. European and Asia-Pacific equipment providers are forging strategic alliances with U.S.-based fabricators to circumvent import duties, ensuring continuity of spare parts availability and maintenance services. As rail networks endure accelerated traffic growth, this realignment of trade flows and partnership models will continue to shape procurement strategies and project timelines throughout 2025 and beyond.
Key Segmentation Insights Across Rail Milling & Grinding Markets
Market participants recognize distinct performance and application profiles across milling and grinding solutions. The divide between plain line milling and switch and crossing grinding underscores a fundamental types-based differentiation: plain line equipment excels at long-distance track resurfacing, while specialized switch and crossing machines navigate complex geometric intersections. These machines find their utility in both construction projects-where initial track laying demands precise rail profiles-and ongoing maintenance regimes that prioritize rail longevity and smooth ride quality.
Within the machinery capability spectrum, high-performance machines deliver robust power outputs and advanced cooling systems to tackle intensive grinding workloads, whereas standard machines address routine wear corrections with simpler configurations and lower energy requirements. Technology adoption further refines choice: automated systems provide real-time monitoring, adaptive grinding algorithms, and remote diagnostics to enhance process reliability, while manually operated units retain versatility for small-scale jobs and regions with limited digital infrastructure.
End users vary in their operational imperatives: private rail companies emphasize lifecycle cost optimization and network uptime, whereas public transport operators prioritize passenger safety, noise reduction, and adherence to urban regulatory frameworks. Operational mode selections-diesel-powered engines offering route flexibility and rapid deployment, contrasted with electric-powered platforms that align with net-zero objectives-reflect both infrastructure constraints and corporate sustainability pledges. Integration type completes the segmentation landscape: modular systems enable swift assembly of task-specific modules, while standalone units offer turnkey solutions that simplify fleet management and maintenance planning.
This comprehensive research report categorizes the Rail Milling & Grinding Train market into clearly defined segments, providing a detailed analysis of emerging trends and precise revenue forecasts to support strategic decision-making.
- Type
- Application
- Machinery Capability
- Technology
- End User
- Operational Mode
- Integration Type
Critical Regional Insights Shaping Market Trajectories
Regional dynamics shape both demand patterns and technology adoption curves. In the Americas, network age and extensive freight corridors drive urgent refurbishment initiatives, prompting operators to favor high-throughput grinding trains equipped for continuous heavy-haul service. Conversely, Europe, Middle East & Africa exhibit a dual narrative: legacy high-speed routes in Western Europe mandate precision grinding with stringent quality controls, while emerging markets in the Middle East and Africa pursue rapid capacity expansions, often integrating turnkey modular systems to accelerate project delivery.
Asia-Pacific stands out as a growth hotspot, fueled by massive investments in high-speed rail and urban metro networks. Here, local manufacturers and international OEMs compete to provide electric-powered grinding trains that meet both volume requirements and regional environmental standards. Additionally, the Asia-Pacific emphasis on digital twin simulations and predictive maintenance platforms demonstrates a forward-leaning approach to network asset management, setting benchmarks that influence best practices globally.
This comprehensive research report examines key regions that drive the evolution of the Rail Milling & Grinding Train market, offering deep insights into regional trends, growth factors, and industry developments that are influencing market performance.
- Americas
- Asia-Pacific
- Europe, Middle East & Africa
Leading Competitor Profiles and Strategic Insights
A handful of specialist companies command leading positions through differentiated offerings and strategic partnerships. Harsco Rail distinguishes itself with a global service network, coupling on-site support with advanced diagnostic tools to minimize downtime. Linmag GmbH focuses on high-precision tooling and engineering excellence, enabling faster grinding cycles on high-speed rail corridors. Linsinger Maschinenbau GmbH leverages modular machine architectures that allow operators to reconfigure equipment rapidly, optimizing capital utilization across diverse track conditions.
Plasser & Theurer excels in integrated automation, delivering intelligent control systems that provide live quality metrics and adaptive grinding profiles, enhancing both safety and efficiency. Vossloh AG drives innovation in electric-powered platforms, incorporating energy recovery systems and advanced filtration modules to meet stringent emissions criteria. Collectively, these companies set competitive benchmarks in machine performance, service quality, and environmental compliance.
This comprehensive research report delivers an in-depth overview of the principal market players in the Rail Milling & Grinding Train market, evaluating their market share, strategic initiatives, and competitive positioning to illuminate the factors shaping the competitive landscape.
- Harsco Rail
- Linmag GmbH
- Linsinger Maschinenbau GmbH
- Plasser & Theurer
- Vossloh AG
Actionable Recommendations for Industry Leaders
Industry leaders should accelerate the integration of digital platforms to harness real-time rail condition data, enabling predictive maintenance schedules that reduce unplanned outages. Prioritizing collaboration with local fabricators or forming joint ventures can mitigate tariff risks while ensuring agile supply chains for critical components. Investments in modular machine architectures should continue, empowering operators to scale capacity or pivot between construction and maintenance tasks with minimal downtime.
Furthermore, aligning equipment portfolios with sustainability mandates-through electric propulsion, regenerative braking, and particulate capture systems-will unlock access to green financing and government incentives. Developing service contracts that bundle performance guarantees, consumable management, and remote diagnostics will differentiate offerings in a competitive marketplace. Finally, nurturing partnerships with public transport authorities and private rail operators can yield co-developed solutions tailored to unique regulatory environments and network performance targets.
Explore AI-driven insights for the Rail Milling & Grinding Train market with ResearchAI on our online platform, providing deeper, data-backed market analysis.
Ask ResearchAI anything
World's First Innovative Al for Market Research
Conclusion: Seizing Opportunities in Rail Surface Solutions
Rail milling and grinding trains occupy a pivotal role in the ongoing modernization and expansion of global rail infrastructure. The convergence of digital intelligence, modular design, and environmental stewardship is reshaping both the capabilities and expectations of maintenance fleets. In this rapidly evolving context, equipment providers and rail operators must embrace agile strategies that address diverse segment requirements, regional dynamics, and shifting trade conditions.
By leveraging data-driven maintenance, sustainable propulsion systems, and adaptive machine configurations, stakeholders can deliver superior service quality while optimizing capital and operational expenditures. Those who anticipate regulatory changes, forge strategic alliances, and invest in next-generation technology will secure lasting competitive advantages and contribute meaningfully to safer, more reliable rail networks worldwide.
This section provides a structured overview of the report, outlining key chapters and topics covered for easy reference in our Rail Milling & Grinding Train market comprehensive research report.
- Preface
- Research Methodology
- Executive Summary
- Market Overview
- Market Dynamics
- Market Insights
- Cumulative Impact of United States Tariffs 2025
- Rail Milling & Grinding Train Market, by Type
- Rail Milling & Grinding Train Market, by Application
- Rail Milling & Grinding Train Market, by Machinery Capability
- Rail Milling & Grinding Train Market, by Technology
- Rail Milling & Grinding Train Market, by End User
- Rail Milling & Grinding Train Market, by Operational Mode
- Rail Milling & Grinding Train Market, by Integration Type
- Americas Rail Milling & Grinding Train Market
- Asia-Pacific Rail Milling & Grinding Train Market
- Europe, Middle East & Africa Rail Milling & Grinding Train Market
- Competitive Landscape
- ResearchAI
- ResearchStatistics
- ResearchContacts
- ResearchArticles
- Appendix
- List of Figures [Total: 30]
- List of Tables [Total: 319 ]
Call to Action: Engage Ketan Rohom for Comprehensive Market Intelligence
To gain in-depth insights and actionable data tailored to your strategic goals, connect with Ketan Rohom, Associate Director, Sales & Marketing. He can guide you through comprehensive intelligence packages designed to inform procurement, operational planning, and partnership initiatives. Engage today and equip your organization with the knowledge needed to stay ahead in the rail milling and grinding train market.
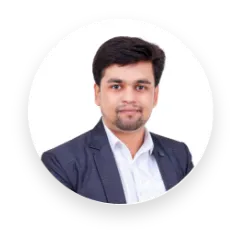
- When do I get the report?
- In what format does this report get delivered to me?
- How long has 360iResearch been around?
- What if I have a question about your reports?
- Can I share this report with my team?
- Can I use your research in my presentation?