The Railway Maintenance Machinery Market size was estimated at USD 4.76 billion in 2024 and expected to reach USD 5.06 billion in 2025, at a CAGR 5.99% to reach USD 6.75 billion by 2030.

Elevating Rail Safety and Efficiency Through Advanced Maintenance
Rail networks form the circulatory system of modern economies, and maintaining their operational integrity is paramount. As infrastructure ages and traffic density rises, the demand for advanced maintenance machinery grows ever more critical. Leading rail operators and contractors are transitioning from reactive to proactive strategies, deploying sophisticated machinery that ensures safety, minimizes downtime, and extends asset lifespan.
In recent years, integration of digital sensors, automation modules, and data analytics platforms has revolutionized the maintenance landscape. Traditional tamping, ballast cleaning, and grinding routines now coexist with real-time track inspection systems and condition-based workflows. Regulatory bodies are mandating tighter safety standards, compelling operators to invest in equipment that can deliver both precision and reliability under strict compliance requirements.
This executive summary surveys the transformative shifts redefining maintenance machinery, examines the implications of newly imposed United States tariffs, explores segmentation insights across machine types, maintenance regimes, end users, power sources, and operation modes, and highlights regional dynamics alongside leading industry participants. By synthesizing these dimensions, this overview equips decision-makers with the context and recommendations necessary to chart a forward-looking strategy in a fast-evolving sector.
Emerging Innovations Redefine the Railway Maintenance Landscape
Breakthroughs in automation and digital connectivity are reshaping every facet of railway maintenance. Autonomous tamping machines now navigate tracks with centimeter-level accuracy, while robotic rail grinding systems adapt their cutting profiles on the fly using embedded artificial intelligence. Coupled with cloud-based analytics, these solutions deliver predictive insights that preempt equipment failures and reduce unplanned interruptions.
Simultaneously, the proliferation of Internet of Things platforms has unlocked continuous condition monitoring. Sensor arrays capturing vibration, temperature, and acoustic signatures feed machine-learning algorithms that recognize early signs of wear. This shift toward predictive maintenance transforms service windows from scheduled intervals into dynamic, need-driven events, optimizing resource deployment and reducing lifecycle costs.
Environmental imperatives and sustainability targets are also influencing machine design. Hybrid power systems and low-emission engines are becoming standard, enabling operators to comply with stringent emissions regulations without sacrificing performance. Modular machinery architectures facilitate rapid deployment of upgrades, ensuring fleets can integrate new technologies without full replacements. Together, these advances signal a new era of responsive, data-driven maintenance poised to enhance safety, efficiency, and environmental stewardship.
Assessing the Ripple Effects of 2025 United States Tariffs on Machinery
The enactment of new United States tariffs effective 2025 introduces a complex matrix of cost pressures for global equipment manufacturers and end users alike. Machinery components ranging from high-precision sensors to heavy steel assemblies now face elevated import duties, driving up landed costs for critical maintenance vehicles and inspection tools. For suppliers, this necessitates a reevaluation of manufacturing footprints and sourcing strategies to mitigate margin erosion.
Operators reliant on imported machinery must contend with extended lead times and recalibrated procurement budgets. Some have begun exploring nearshoring options, shifting assembly operations closer to end markets to bypass punitive duties and stabilize supply chains. Others are renegotiating long-term service contracts, indexing pricing formulas to reflect tariff adjustments and currency fluctuations.
In parallel, domestic producers see an opportunity to capture market share by enhancing local manufacturing capabilities and accelerating product development cycles. Strategic partnerships between OEMs and regional fabricators are emerging, underscoring a broader trend toward onshore capacity building. While short-term disruptions are inevitable, these realignments may ultimately bolster resilience and foster innovation in North American railway maintenance ecosystems.
Deep Dive Into Market Segmentation Dynamics and Opportunities
Market segmentation reveals distinct demand drivers across machine type, maintenance philosophy, end-user profile, power source, and operation mode. Among machine types, ballast cleaning and rail grinding maintain a substantial share as core track renewal activities, yet track inspection solutions are experiencing the most rapid uptake. Within that domain, eddy current testing and laser profiling technologies are gaining traction for their ability to detect subsurface flaws and rail profile deviations with minimal service interruptions. Ultrasonic testing and visual inspection complement these methods, offering a layered approach to condition monitoring that enhances defect detection rates.
Maintenance types further stratify the market. Corrective maintenance continues to represent a significant baseline requirement, addressing failures after they occur. Preventive maintenance, anchored in time-based service schedules, provides routine care to limit degradation. However, predictive maintenance is redefining workload allocation, leveraging acoustic emission sensors, thermal imaging cameras, ultrasonic measurement devices, and vibration analysis tools to forecast component life and optimize intervention timing.
End users encompass a spectrum that ranges from government agencies enforcing public safety mandates to private contractors driven by project profitability metrics, as well as railway operators prioritizing network availability. Each group exhibits unique procurement criteria, from standardized contract specifications for public tenders to performance-based agreements in the private sector.
Power source selection remains a strategic consideration. Diesel-powered machines command established reliability across remote territories, while electric systems are favored on electrified corridors for zero-emission operation. Battery-powered solutions are emerging as flexible options for short-duration tasks and constrained environments, offering silent operation and rapid redeployment.
Operation mode preferences reflect a balance between human oversight and machine autonomy. Fully automatic platforms deliver consistent, high-precision performance in repetitive tasks, whereas manual modes afford operators nuanced control in complex scenarios. Semi-automatic systems blend both approaches, enabling automation of routine functions while preserving operator intervention for exceptions.
This comprehensive research report categorizes the Railway Maintenance Machinery market into clearly defined segments, providing a detailed analysis of emerging trends and precise revenue forecasts to support strategic decision-making.
- Machine Type
- Maintenance Type
- End User
- Power Source
- Operation Mode
Regional Nuances Driving Maintenance Machinery Adoption Globally
Regional analysis underscores divergent trajectories across global markets. In the Americas, investment in upgrading aging rail corridors and expanding intermodal freight capacity drives demand for heavy-duty tamping units and integrated inspection fleets. Funding initiatives at federal and state levels are channeling resources toward network resiliency and safety upgrades, while North American operators are increasingly exploring lease-based acquisitions to manage capital expenditures.
Across Europe, the Middle East and Africa, established high-speed lines in Western Europe coexist with burgeoning infrastructure programs in the Gulf region and refurbishment projects throughout Africa. European operators emphasize cross-border interoperability and digital standardization, fueling uptake of advanced IoT-enabled machinery. In the Middle East, rapid urbanization and high-profile rail network launches are accelerating procurement cycles, while African markets prioritize cost-effective maintenance processes that extend asset life with limited budgets.
In the Asia-Pacific zone, regional leaders such as China and India are deploying large-scale modernization programs, integrating high-speed corridors and urban metro expansions. Japan’s focus on ultra-precision grinding and continuous monitoring complements Australia’s push for remote operation capabilities in vast, low-density networks. These diverse needs foster a robust market for both high-capacity machinery and modular, scalable solutions that can adapt to varied climatic and topographical challenges.
This comprehensive research report examines key regions that drive the evolution of the Railway Maintenance Machinery market, offering deep insights into regional trends, growth factors, and industry developments that are influencing market performance.
- Americas
- Europe, Middle East & Africa
- Asia-Pacific
Leading Industry Players Steering Technological Advancements
The competitive landscape is shaped by established original equipment manufacturers alongside specialized innovators. Leading global players have fortified their positions through strategic collaborations with technology firms, integrating advanced sensor suites and data analytics platforms into traditional machinery portfolios. Several have launched hybrid diesel-electric tampers and battery-powered inspection trolleys, emphasizing modular upgrade paths that future-proof existing fleets.
Meanwhile, niche specialists are carving out market share by focusing exclusively on predictive maintenance solutions, developing portable acoustic emission devices and handheld thermal imaging cameras optimized for trackside diagnostics. These vendors often partner with software providers to offer end-to-end condition-monitoring ecosystems, encompassing hardware, data processing, and cloud-based reporting.
Some major conglomerates have pursued mergers and acquisitions to broaden their service offerings, acquiring firms with expertise in robotic track repair or advanced grinding technologies. Joint ventures are also prominent, particularly in regions where local content requirements favor domestic partnerships. Together, these moves underscore a dual strategy: scale up manufacturing capacity while embedding digital capabilities that meet the rising demand for smart maintenance operations.
This comprehensive research report delivers an in-depth overview of the principal market players in the Railway Maintenance Machinery market, evaluating their market share, strategic initiatives, and competitive positioning to illuminate the factors shaping the competitive landscape.
- Harsco Corporation
- Plasser & Theurer GmbH
- Progress Rail Services Corporation
- Pandrol Limited
- Loram Maintenance of Way, Inc.
- Speno International S.A.
- Windhoff Bahn- und Baumaschinen GmbH
- Sersa Group AG
- voestalpine Schieneninstandhaltung GmbH
- Robel Bahnbaumaschinen GmbH
Strategic Actions to Harness Growth in Railway Maintenance
Industry leaders should prioritize investment in scalable predictive maintenance platforms that integrate acoustic emission, thermal imaging, ultrasonic testing, and vibration analysis into a unified data lake. This will enable real-time condition monitoring and advanced analytics, reducing unscheduled downtime and improving maintenance precision. At the same time, diversifying manufacturing footprints by establishing assembly hubs in duty-free zones or nearshore locations can mitigate the impact of tariff fluctuations and shorten supply chains.
Collaborating with regulatory agencies to develop standardized digital reporting protocols will streamline tender processes and facilitate cross-border interoperability. Strategic alliances with software developers and sensor manufacturers can accelerate the rollout of modular upgrade kits, ensuring legacy machinery remains competitive. Operators should also explore flexible procurement models, such as performance-based contracts and equipment-as-a-service, to align expenditures with actual usage and performance outcomes.
Finally, upskilling maintenance teams to manage automated and semi-automatic platforms will be critical. Training programs that blend hands-on technical workshops with virtual simulations can build operator proficiency in robotics and data interpretation, maximizing the benefits of new machinery investments. By embracing these strategic actions, industry stakeholders can position themselves at the forefront of a rapidly evolving maintenance ecosystem.
Rigorous Framework Underpinning Our Research Approach
This study is grounded in a rigorous mixed-methods approach. Primary research comprised in-depth interviews with senior executives at leading rail operators, government procurement officials, and maintenance service providers. These qualitative insights were complemented by detailed surveys gathering quantitative data on fleet compositions, maintenance budgets, and technology adoption rates.
Secondary research drew from a comprehensive review of industry publications, trade association reports, regulatory filings, and patent databases. Publicly available financial statements and corporate presentations provided further context on corporate strategies and investment priorities. All data points were cross-verified through a triangulation process that reconciled discrepancies and validated emerging trends.
Analytical frameworks such as SWOT analysis, Porter’s Five Forces, and technology readiness assessments were employed to interpret competitive dynamics and adoption barriers. A dedicated expert panel of former railway engineers and market analysts reviewed preliminary findings, offering critical feedback that refined the final narrative. This methodology ensures a balanced, evidence-based perspective that supports strategic decision-making in the railway maintenance machinery sector.
Explore AI-driven insights for the Railway Maintenance Machinery market with ResearchAI on our online platform, providing deeper, data-backed market analysis.
Ask ResearchAI anything
World's First Innovative Al for Market Research
Synthesizing Insights to Chart the Future of Rail Maintenance
The railway maintenance machinery sector stands poised at the intersection of technological innovation, regulatory evolution, and shifting economic landscapes. Advanced automation and predictive analytics are redefining maintenance paradigms, while newly imposed tariffs are reshaping supply chains and cost structures. Segmentation analysis highlights emerging opportunities in track inspection and predictive services, and regional insights reveal differentiated growth drivers across the Americas, Europe, Middle East and Africa, and Asia-Pacific.
Leading companies are responding with hybrid product portfolios and strategic partnerships, underscoring the importance of agility and collaboration in an increasingly competitive environment. Industry stakeholders that adopt scalable maintenance platforms, diversify manufacturing bases, and engage in cross-sector standardization efforts will be best positioned to capitalize on growth opportunities.
As the sector evolves, proactive leadership and data-driven decision-making will be key to navigating tariff headwinds, harnessing digital transformation, and delivering safe, efficient, and sustainable rail operations. The insights presented here offer a comprehensive roadmap for stakeholders seeking to align their strategies with emerging market realities and secure a competitive advantage.
This section provides a structured overview of the report, outlining key chapters and topics covered for easy reference in our Railway Maintenance Machinery market comprehensive research report.
- Preface
- Research Methodology
- Executive Summary
- Market Overview
- Market Dynamics
- Market Insights
- Cumulative Impact of United States Tariffs 2025
- Railway Maintenance Machinery Market, by Machine Type
- Railway Maintenance Machinery Market, by Maintenance Type
- Railway Maintenance Machinery Market, by End User
- Railway Maintenance Machinery Market, by Power Source
- Railway Maintenance Machinery Market, by Operation Mode
- Americas Railway Maintenance Machinery Market
- Europe, Middle East & Africa Railway Maintenance Machinery Market
- Asia-Pacific Railway Maintenance Machinery Market
- Competitive Landscape
- ResearchAI
- ResearchStatistics
- ResearchContacts
- ResearchArticles
- Appendix
- List of Figures [Total: 26]
- List of Tables [Total: 331 ]
Connect with Ketan Rohom for Your Detailed Railway Maintenance Market Report
To unlock the full depth of this comprehensive railway maintenance machinery market research report, reach out directly to Ketan Rohom, Associate Director, Sales & Marketing. His expertise in tailoring insights to your strategic objectives ensures you secure the precise intelligence needed to navigate evolving industry dynamics and capitalize on emerging opportunities. Engage with an authoritative resource committed to delivering actionable data and trend analysis that will enhance decision-making, optimize procurement strategies, and drive competitive advantage.
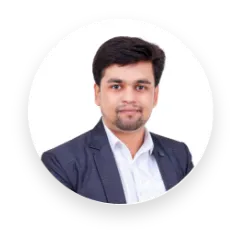
- How big is the Railway Maintenance Machinery Market?
- What is the Railway Maintenance Machinery Market growth?
- When do I get the report?
- In what format does this report get delivered to me?
- How long has 360iResearch been around?
- What if I have a question about your reports?
- Can I share this report with my team?
- Can I use your research in my presentation?