Introduction to Reactor Spent Fuel Transport Containers
The safe transport of spent nuclear fuel remains a cornerstone of the global nuclear energy lifecycle, bridging the gap between onsite cooling and long-term storage or reprocessing facilities. As nuclear capacity expands to meet decarbonization goals, the integrity of transport containers dictates not only regulatory compliance but also public confidence. This executive summary highlights critical developments in container design, regulatory shifts, and supply chain dynamics that influence the conveyance of high-activity materials.
Modern transport solutions must balance mechanical robustness, radiation shielding, and thermal insulation while accommodating diverse handling modes-road, rail, and marine. Emerging composite materials, advanced manufacturing practices, and integrated monitoring systems are redefining performance benchmarks. At the same time, geopolitical pressures and trade policies are reshaping sourcing strategies and cost structures.
This overview distills transformative trends and strategic imperatives for stakeholders across the value chain, offering a concise yet comprehensive assessment of how container technologies and market forces converge to support the next generation of spent fuel logistics.
Transformative Shifts in Reactor Spent Fuel Logistics
Over the past decade, accelerated innovation and shifting policy frameworks have converged to redefine spent fuel transport logistics. Advances in fiber-reinforced composites and multi-material assemblies now deliver lighter, stronger containers with enhanced radiation attenuation. Meanwhile, digital transformation is driving remote condition monitoring through embedded sensors and real-time analytics, enabling proactive maintenance and operational transparency.
On the regulatory front, harmonization efforts by international bodies are streamlining cross-border approvals, while regional bodies tighten safety thresholds in response to heightened public scrutiny. Energy transition agendas have spurred collaboration between utilities, manufacturers, and research institutions to develop modular container platforms that address diverse reactor types and fuel enrichments.
Supply chain resilience has emerged as an equally transformative force. Manufacturers are localizing critical component production to mitigate tariff impacts and logistical disruptions. As a result, partnerships are expanding with specialty materials producers and engineering firms to integrate next-generation coatings and interlocking shielding layers. Collectively, these shifts create a more agile ecosystem capable of meeting rigorous safety, environmental, and performance standards.
How 2025 U.S. Tariffs Reshape Spent Fuel Transport Economics
In 2025, a new suite of U.S. trade measures targeting imported metals and advanced composites is reshaping cost dynamics for container producers and operators. Increased duties on steel and specialized composite reinforcements are prompting manufacturers to evaluate domestic sourcing and vertical integration models. Container designers are responding by optimizing material usage, favoring multi-material constructions that leverage locally produced alloys and polymeric liners.
Operators are reassessing total cost of ownership frameworks to accommodate tariff-driven price adjustments. This has fueled interest in lifecycle cost analyses that factor in maintenance, refurbishment, and potential recyclability of container components. At the same time, end-users are exploring joint procurement alliances to negotiate volume discounts and shared fabrication facilities.
International suppliers, facing steeper entry barriers, are strengthening strategic partnerships with U.S. firms to localize assembly and qualify materials under domestic content requirements. These collaborative approaches ensure compliance with trade regulations while preserving access to cutting-edge shielding technologies.
In-Depth Segmentation Insights for Transport Container Design
The spent fuel transport container market can be dissected through multiple lenses, each revealing distinct design and application demands. Type segmentation captures composite containers, which include carbon fiber reinforced, glass fiber reinforced, and hybrid composites; metal containers composed of copper and steel; and polymeric containers utilizing high-density polyethylene or polypropylene. Capacity tiers span the spectrum from units up to one metric ton to small-scale containers handling one to five metric tons, medium platforms rated for five to twenty metric tons and ten to twenty metric tons brackets, and large assemblies exceeding twenty metric tons. Application insights differentiate marine transport solutions-barges and cargo ships-from rail options on freight trains and high-speed rail, as well as road transport via long-distance and short-distance vehicles. Material type segmentation reveals multi-material configurations with multilayered construction and powdered compositional additives alongside single-material vessels built from traditional substrates. Design considerations cover cylindrical forms offering detachable lids or integrated closures and rectangular shapes available in non-stackable or stackable units. End-user categories span military and defense scenarios from air force trials to naval operations, nuclear power plants including breeder and conventional reactors, and research reactors in private and university settings. Finally, safety feature segmentation spotlights corrosion resistance achieved through coatings and internal linings, radiation shielding delivered via coated surfaces and interlocking layers, and thermal insulation provided by external shields and intermediate layers.
This comprehensive research report categorizes the Reactor Spent Fuel Transport Container market into clearly defined segments, providing a detailed analysis of emerging trends and precise revenue forecasts to support strategic decision-making.
- Type
- Capacity
- Application
- Material Type
- Design
- End-User
- Safety Features
Regional Nuances in Spent Fuel Transport Containers
Regional dynamics in the spent fuel transport container arena reflect varied energy strategies, regulatory climates, and infrastructure maturity. In the Americas, a combination of expanding nuclear fleets in North America and decommissioning projects in South America is driving demand for flexible container platforms. Stringent U.S. Department of Transportation standards and Canadian CNSC guidelines ensure rigorous qualification procedures, while Brazilian initiatives to modernize coastal transport infrastructure are creating niche opportunities for marine-grade solutions.
Europe, Middle East & Africa presents a mosaic of markets: Western European nations emphasize harmonized EN and IAEA certification regimes and encourage circular economy practices in container refurbishment. Gulf states are investing in research reactors to bolster medical isotope production, stimulating demand for shielded transport systems. In Africa, emerging nuclear programs in South Africa and Egypt are fostering partnerships with global vendors to establish localized assembly and training centers.
In Asia-Pacific, rapid nuclear expansion in China and India is matched by advanced safety enforcement in Japan and South Korea. Container manufacturers are exploring joint ventures to localize metallic and composite production, supporting regional content policies and reducing lead times. Southeast Asian plans for small modular reactors have further amplified interest in versatile, scalable container solutions adaptable to diverse port and rail infrastructures.
This comprehensive research report examines key regions that drive the evolution of the Reactor Spent Fuel Transport Container market, offering deep insights into regional trends, growth factors, and industry developments that are influencing market performance.
- Americas
- Asia-Pacific
- Europe, Middle East & Africa
Competitive Landscape: Leading Players in Transport Containers
The competitive landscape features several established and emerging players, each bringing unique strengths and capabilities. AREVA NC, now integrated within Orano, has leveraged composite expertise and licensing acumen to deliver customized transport casks. Babcock & Wilcox Company has long excelled in steel fabrication and modular assembly lines for high-activity containers. Cameco Corporation’s deep know-how in uranium logistics complements its growing portfolio of rail-certified transport vessels. China National Nuclear Corporation offers vertically integrated solutions, from fuel fabrication to container assembly, while Enresa’s proficiency in radioactive waste management informs its specialized container designs.
GNS Gesellschaft für Nuklear-Service mbH is recognized for its advanced engineering services and quality assurance protocols. Holtec International’s modular cask systems and digital monitoring packages have set new benchmarks for operational transparency. JSC TVEL and Kazatomprom leverage state-backed supply chains to deliver cost-effective raw materials, whereas NAC International Inc., also known as Nuclear Assurance Corporation, provides comprehensive licensing and safety analysis support. Rosatom State Atomic Energy Corporation combines global reach with in-house fabrication capabilities. Skoda JS a.s. contributes decades of heavy-machinery experience to its custom container offerings, and Westinghouse Electric Company integrates decades of reactor engineering insights into innovative shielding and thermal management solutions.
This comprehensive research report delivers an in-depth overview of the principal market players in the Reactor Spent Fuel Transport Container market, evaluating their market share, strategic initiatives, and competitive positioning to illuminate the factors shaping the competitive landscape.
- AREVA NC (now part of Orano)
- Babcock & Wilcox Company (B&W)
- Cameco Corporation
- China National Nuclear Corporation (CNNC)
- Enresa (Empresa Nacional de Residuos Radiactivos)
- GNS Gesellschaft für Nuklear-Service mbH
- Holtec International
- JSC TVEL
- Kazatomprom
- NAC International Inc.
- Nuclear Assurance Corporation (NAC)
- Rosatom State Atomic Energy Corporation
- Skoda JS a.s.
- Westinghouse Electric Company
Strategic Recommendations for Industry Stakeholders
Industry stakeholders should prioritize a multi-pronged strategy to thrive in the evolving transport container market. First, diversify material sourcing by partnering with specialty suppliers to reduce tariff exposure and support hybrid composite-metal assemblies that enhance performance. Second, invest in domestic manufacturing and localized assembly partnerships to align with regional content mandates and shorten supply chains. Third, adopt integrated digital monitoring platforms that track container health in real time, enabling predictive maintenance and reducing downtime.
Fourth, engage proactively with regulatory bodies to co-develop harmonized certification protocols, accelerating cross-border approvals and minimizing redesign cycles. Fifth, incorporate circular economy principles by designing containers for disassembly and recycling, addressing sustainability targets and lowering end-of-life costs. Sixth, establish collaborative procurement consortia to leverage volume discounts and share best practices across utilities, research institutions, and defense organizations. Finally, enhance stakeholder alignment by organizing joint training initiatives and simulation exercises that standardize handling procedures and reinforce safety culture.
Explore AI-driven insights for the Reactor Spent Fuel Transport Container market with ResearchAI on our online platform, providing deeper, data-backed market analysis.
Ask ResearchAI anything
World's First Innovative Al for Market Research
Concluding Perspectives on Spent Fuel Transport Innovations
The convergence of advanced materials, digital technologies, and evolving trade policies is ushering in a new era for spent fuel transport. Container designs are becoming lighter yet more robust, with integrated sensing and analytics delivering unprecedented visibility into in-transit conditions. At the same time, tightening regulatory frameworks and regional sourcing mandates are prompting a shift toward localized manufacturing and collaborative supply chains.
Success in this environment will hinge on harmonizing technical innovation with strategic partnerships across all segments-from composite producers and metal fabricators to rail operators and maritime carriers. By anticipating regulatory shifts, leveraging circular design principles, and embracing digital transformation, the industry can enhance safety, streamline logistics, and strengthen public trust. The insights provided here present a roadmap for aligning product development, procurement, and compliance efforts to support the safe, efficient, and sustainable transport of spent nuclear fuel.
This section provides a structured overview of the report, outlining key chapters and topics covered for easy reference in our Reactor Spent Fuel Transport Container market comprehensive research report.
- Preface
- Research Methodology
- Executive Summary
- Market Overview
- Market Dynamics
- Market Insights
- Cumulative Impact of United States Tariffs 2025
- Reactor Spent Fuel Transport Container Market, by Type
- Reactor Spent Fuel Transport Container Market, by Capacity
- Reactor Spent Fuel Transport Container Market, by Application
- Reactor Spent Fuel Transport Container Market, by Material Type
- Reactor Spent Fuel Transport Container Market, by Design
- Reactor Spent Fuel Transport Container Market, by End-User
- Reactor Spent Fuel Transport Container Market, by Safety Features
- Americas Reactor Spent Fuel Transport Container Market
- Asia-Pacific Reactor Spent Fuel Transport Container Market
- Europe, Middle East & Africa Reactor Spent Fuel Transport Container Market
- Competitive Landscape
- ResearchAI
- ResearchStatistics
- ResearchContacts
- ResearchArticles
- Appendix
- List of Figures [Total: 30]
- List of Tables [Total: 1159 ]
Connect with Ketan Rohom to Access the Full Report
To explore the full suite of insights on spent fuel transport container trends, regulatory impacts, and competitive dynamics, contact Ketan Rohom, Associate Director, Sales & Marketing. Reach out via email at [email protected] or call +1-555-123-4567 to secure access to the comprehensive market research report and empower your strategic planning.
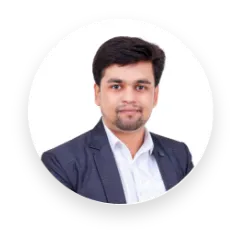
- When do I get the report?
- In what format does this report get delivered to me?
- How long has 360iResearch been around?
- What if I have a question about your reports?
- Can I share this report with my team?
- Can I use your research in my presentation?