The Refinery Catalysts Market size was estimated at USD 6.04 billion in 2024 and expected to reach USD 6.33 billion in 2025, at a CAGR 4.94% to reach USD 8.07 billion by 2030.

Setting the Stage for Refinery Catalyst Innovation
Refinery catalysts lie at the heart of modern hydrocarbon processing, serving as indispensable enablers for converting crude feedstocks into high-value transportation fuels and chemical intermediates. As tightening environmental regulations and the global energy transition reshape demand profiles, the importance of these materials has never been greater. This executive summary delivers a concise yet comprehensive overview of the latest developments, core market drivers, and strategic considerations that will influence the industry’s trajectory over the coming years.
By exploring critical shifts in technology, policy, and competitive positioning, this narrative equips decision-makers with the context needed to navigate rapidly evolving dynamics. From shifts in feedstock quality and sustainability mandates to evolving supply chain structures, each facet is examined through a lens of practical insight. Readers will emerge with a clear view of the levers that catalyze performance, areas for strategic investment, and the implications of emerging trade frameworks.
Driving Forces Redefining the Catalyst Landscape
The refinery catalysts market is undergoing a profound transformation driven by converging forces across technology, regulation, and sustainability. Novel catalyst formulations are emerging that enable higher yields at lower operating temperatures, reducing both energy consumption and greenhouse gas emissions. Simultaneously, advancements in material science have yielded nanostructured compounds that exhibit superior selectivity for target reactions, translating into more efficient cracking, hydrocracking, and isomerization processes.
Moreover, tightening environmental standards are prompting refiners to upgrade existing units and install next-generation reactors. This regulatory momentum, particularly in regions committed to net-zero targets, is fueling demand for catalysts that can process lower-quality feedstocks and incorporate renewable inputs. Digitalization is also reshaping operating models, with predictive analytics and machine learning tools deployed to track catalyst health and optimize regeneration cycles. As a result, operations teams can anticipate performance degradation and schedule maintenance proactively, thereby maximizing uptime.
Collectively, these dynamic shifts are forging new pathways for competitive differentiation. Companies that integrate advanced catalyst platforms with data-driven process control can achieve tangible gains in yield, reliability, and cost efficiency. As this environment evolves, partnerships between catalyst developers, technology providers, and refineries will become critical to translating innovation into scalable outcomes.
Assessing the Effects of U.S. Tariffs on Catalyst Supply Chains
Recent adjustments to United States trade policy have introduced new tariff barriers that significantly affect the refinery catalyst supply chain. Materials such as certain precious and rare earth metals, often sourced from global suppliers, now face increased levies upon import. This development has raised procurement costs and prompted many catalyst producers and end-users to reassess their raw material strategies, looking for alternative sources or increased domestic capacity to offset additional expenses.
In response to these changes, stakeholders across the ecosystem are exploring more integrated supply chain models. Strategic stockpiling of critical inputs, long-term purchasing agreements, and collaborative sourcing consortia have emerged as viable approaches to mitigate tariff impacts. Additionally, some catalyst developers are accelerating investment in locally abundant base metals and siliceous materials, seeking formulations that deliver robust performance without reliance on high-tariff components. These adaptive measures not only address immediate cost pressures but also strengthen resilience against future policy fluctuations.
Unveiling Segmentation Patterns Guiding Market Strategies
The catalyst market’s complexity is underscored by the range of materials that address specific reaction pathways. In terms of composition, chemical compounds such as alumina and silica play foundational roles as support matrices, offering thermal stability and surface area. Metal-based catalysts draw on a spectrum of elements, from premium precious metals to more readily available transition and base metals, and even rare earth alloys tailored for specialized cracking or hydroprocessing functions. Natural and synthetic zeolites further extend functionality by providing microporous architectures that enhance selectivity in isomerization and molecular sieving applications.
Different reaction environments demand catalysts optimized for unique conditions. In alkylation, acidity and pore structure govern performance, whereas fluid catalytic cracking units rely on resilience under high temperature cycles to yield diesel and gasoline fractions. Hydrocracking catalysts must balance hydrogenation activity with stability to produce middle distillates and naphtha, while isomerization catalysts target branched alkanes through precise control of active sites, whether for butane or heavier C5/C6 streams.
End-user industries drive tailored catalyst solutions aligned with their processing objectives. Chemical manufacturing facilities prioritize catalysts that facilitate high-purity intermediates, whereas oil and gas refineries focus on throughput and conversion efficiency across the entire barrel spectrum. Within fuel additives, specialty agents such as anti-knocking compounds and octane enhancers depend on catalyst platforms that deliver high yields of molecularly precise hydrocarbons. Understanding these segmentation layers is critical for vendors to position offerings that resonate with the operational needs of each customer segment.
This comprehensive research report categorizes the Refinery Catalysts market into clearly defined segments, providing a detailed analysis of emerging trends and precise revenue forecasts to support strategic decision-making.
- Type
- Application
- End User Industry
Regional Dynamics Shaping Catalyst Adoption and Growth
Regional trends reveal significant variations in catalyst adoption and innovation agendas. In the Americas, mature refinery networks are embracing retrofit programs that bring older units into alignment with stricter emission controls and shifting product specifications. Investment is concentrated on upgrading cracking and hydroprocessing trains, with an emphasis on catalysts that enable dual-feed operations and improved hydrogen utilization.
In Europe, the Middle East and Africa, a blend of stringent environmental regulations and rapidly expanding refining capacity shapes strategic priorities. Western Europe is advancing renewable feedstock integration and circular economy initiatives, stimulating demand for catalysts that can process bio-based and waste-derived inputs. Gulf refining centers, in parallel, are driving scale expansions and pursuing high-throughput catalyst technologies to maximize conversion of heavy crudes and natural gas liquids, while North African facilities seek modular catalyst solutions that accommodate fluctuating feed qualities.
In Asia-Pacific, growth dynamics are defined by surging fuel demand and extensive capacity additions. Refinery operators in China and India are investing heavily to increase conversion complexities, deploying advanced catalysts for deep hydrocracking and clean fuel production. Southeast Asian markets are also scaling up, with new grassroots refineries specifying robust and low-maintenance catalyst systems to support remote and high-humidity environments. Collectively, these regional variations underscore the necessity for suppliers to tailor their portfolios and services to diverse regulatory, economic, and feedstock landscapes.
This comprehensive research report examines key regions that drive the evolution of the Refinery Catalysts market, offering deep insights into regional trends, growth factors, and industry developments that are influencing market performance.
- Americas
- Europe, Middle East & Africa
- Asia-Pacific
Profiling Industry Leaders and Emerging Innovators
Leading catalyst providers are capitalizing on technological leadership and strategic alliances to solidify market positions. Legacy chemical giants have leveraged decades of R&D to maintain a competitive edge in premium precious metal and zeolite offerings, while specialist developers focus on niche applications and rapid-cycle innovation. Joint ventures between catalyst manufacturers and process licensors have emerged as an effective model for co-creating turnkey solution packages that streamline integration and performance validation at commercial scale.
Meanwhile, emerging players are differentiating through agility in advanced material synthesis and digital service platforms. Remote monitoring tools that track catalyst deactivation in real time are gaining traction, enabling more responsive regeneration schedules and lower unplanned downtime. Some companies are also pioneering circular economy approaches by reclaiming spent catalysts and reprocessing them into secondary raw materials, thus addressing both cost pressures and environmental stewardship. Together, these strategies reflect a market where both established and nascent firms are striving to redefine value delivery across the entire catalyst lifecycle.
This comprehensive research report delivers an in-depth overview of the principal market players in the Refinery Catalysts market, evaluating their market share, strategic initiatives, and competitive positioning to illuminate the factors shaping the competitive landscape.
- Albemarle Corporation
- ANTEN CHEMICAL CO., LTD.
- Arkema S.A.
- Avantium N.V.
- Axens SA
- BASF SE
- Chempack
- Chevron Phillips Chemical Company LLC
- China Petroleum & Chemical Corporation
- Clariant AG
- Dorf Ketal Chemicals (I) Pvt. Ltd.
- Eurecat France SAS
- Evonik Industries AG
- Exxon Mobil Corporation
- Honeywell International Inc.
- JGC Holdings Corporation
- Johnson Matthey PLC
- KNT Group
- LyondellBasell Industries N.V.
- N.E. CHEMCAT Corporation
- Nippon Ketjen Co., Ltd.
- Royal Dutch Shell PLC
- Taiyo Koko Co., Ltd.
- Topsoe A/S
- W. R. Grace & Co.
- Zeolyst International
Strategic Imperatives for Leading Catalyst Enterprises
To thrive in this dynamic environment, industry leaders must pursue a dual strategy focused on technological differentiation and operational resilience. Advancing catalyst formulations to achieve both high activity and extended cycle life will be paramount, particularly as feedstock variability and sustainability mandates intensify. At the same time, companies should diversify their supply chain portfolios by forging alliances with geographically distributed raw material producers and exploring alternative base metal platforms that reduce exposure to tariff volatility.
In parallel, adopting digital solutions for catalyst performance monitoring and process optimization can unlock significant yield improvements and cost savings. Organizations should invest in analytics infrastructure that integrates on-site data with predictive models, thereby enabling proactive decisions about regeneration timing and replacement schedules. Finally, fostering collaborative research partnerships with academic and industry consortia will accelerate innovation while sharing development risks. By aligning technical excellence with collaborative ecosystems, leaders can reinforce their market positions and drive sustained growth.
Ensuring Rigor Through a Structured Research Framework
This research combines qualitative and quantitative inquiry methods to deliver a robust understanding of market dynamics. Primary interviews with refinery operators, catalyst developers, and regulatory experts were conducted to capture diverse perspectives on technological and economic drivers. These insights were cross-checked against secondary sources such as industry publications, patent filings, and public policy documents to ensure consistency and completeness.
Subsequent data analysis involved dissecting segment performance across material types, applications, and end-user industries. Comparative benchmarking highlighted best practices in catalyst management and service delivery. Geographic trends were mapped using production and capacity data, while supply chain resilience assessments drew upon trade statistics and corporate disclosures. Throughout the process, findings were validated with an expert advisory panel to align conclusions with real-world operational challenges and strategic priorities.
Explore AI-driven insights for the Refinery Catalysts market with ResearchAI on our online platform, providing deeper, data-backed market analysis.
Ask ResearchAI anything
World's First Innovative Al for Market Research
Synthesizing Insights to Navigate Market Complexities
The insights presented in this executive summary illuminate the multifaceted forces shaping the refinery catalysts market. From material innovation and policy shifts to regional demands and competitive tactics, each dimension underscores the complexity faced by stakeholders. By synthesizing segmentation analyses, tariff implications, and case studies of industry leaders, this narrative equips decision-makers with a nuanced perspective on where to channel investment and innovation efforts.
Ultimately, the path to leadership in this sector hinges on balancing technical excellence with adaptive strategies that address evolving feedstocks, regulatory expectations, and market volatility. Organizations that embrace advanced catalyst platforms, reinforce supply chain resilience, and leverage data-driven decision-making will be best positioned to capture emerging opportunities. This conclusion sets the stage for deeper exploration and tailored action planning in the comprehensive market research report.
This section provides a structured overview of the report, outlining key chapters and topics covered for easy reference in our Refinery Catalysts market comprehensive research report.
- Preface
- Research Methodology
- Executive Summary
- Market Overview
- Market Dynamics
- Market Insights
- Cumulative Impact of United States Tariffs 2025
- Refinery Catalysts Market, by Type
- Refinery Catalysts Market, by Application
- Refinery Catalysts Market, by End User Industry
- Americas Refinery Catalysts Market
- Europe, Middle East & Africa Refinery Catalysts Market
- Asia-Pacific Refinery Catalysts Market
- Competitive Landscape
- ResearchAI
- ResearchStatistics
- ResearchContacts
- ResearchArticles
- Appendix
- List of Figures [Total: 22]
- List of Tables [Total: 456 ]
Take the Next Step Toward Market Leadership
For organizations seeking a competitive edge in the refinery catalysts market, engaging directly with Ketan Rohom presents an invaluable opportunity. His deep understanding of market nuances and proven track record in guiding strategic decisions can help align your initiatives with emerging trends and regulatory dynamics. By partnering with him, firms can gain tailored insights that accelerate time-to-value and mitigate supply chain uncertainties.
To access the full breadth of our detailed market research report and benefit from customized consultations, reach out to Ketan Rohom, Associate Director of Sales & Marketing. His expertise will ensure your firm leverages actionable intelligence to drive sustainable growth and innovation. Don’t navigate these complex market shifts alone-connect with Ketan today to secure your roadmap to leadership in the refinery catalysts sector
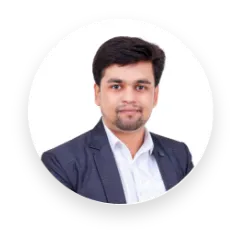
- How big is the Refinery Catalysts Market?
- What is the Refinery Catalysts Market growth?
- When do I get the report?
- In what format does this report get delivered to me?
- How long has 360iResearch been around?
- What if I have a question about your reports?
- Can I share this report with my team?
- Can I use your research in my presentation?