Introduction to Residual Heat Recovery Systems
Residual heat recovery systems represent a pivotal advancement in industrial energy management, capturing and reutilizing thermal energy that would otherwise dissipate into the environment. Industries ranging from petrochemical and power generation to food processing and steel production are increasingly under pressure to enhance operational efficiency while meeting stringent environmental and regulatory standards. By integrating technologies such as plate-fin exchangers, shell-and-tube units, and compact heat exchangers, businesses can unlock significant cost savings, reduce greenhouse gas emissions, and strengthen their sustainability credentials.
Today’s executive summary provides an in-depth exploration of how residual heat recovery is transforming industrial operations. We begin with a broad overview of current drivers and trends, then examine the implications of evolving trade policies, segment-specific dynamics, geographical considerations, and the competitive landscape. This analysis is designed to equip decision-makers with actionable intelligence as they navigate an energy-intensive future.
Through clear insights and a forward-looking perspective, this introduction sets the stage for stakeholders to understand the full potential of residual heat recovery systems in driving efficiency, resilience, and value creation.
Transformative Shifts in the Heat Recovery Landscape
Over the past decade, the landscape of residual heat recovery has shifted dramatically, driven by decarbonization mandates, rising energy costs, and rapid advances in materials and control strategies. Once viewed as niche enhancements, heat recovery units are now central to energy strategies across major industrial sectors. New materials, such as composite alloys with high-temperature shields, enable equipment to operate at unprecedented thermal ratings, while adaptive regulation and predictive optimization algorithms ensure real-time performance tuning and minimal maintenance downtime.
Parallel to these technological leaps, digital transformation has ushered in smart integration, leveraging IoT-enabled sensors for automated monitoring. This fusion of hardware and software has unlocked deeper insights into plant-level heat flows, enabling engineers to capture even low-grade waste heat for secondary power generation through Organic Rankine Cycle systems or convert it directly into cooling via absorption units. As predictive analytics mature, operators gain the ability to anticipate thermal inefficiencies before they escalate, fostering continuous performance improvements.
Furthermore, growing commitments to circular economy principles have spurred cross-industry collaboration. Cement manufacturers repurpose exhaust heat to preheat kilns, while steel producers circulate high-temperature flue gases through custom engineered modular designs. This convergence of materials science, digital controls, and circularity is redefining value chains, moving heat recovery from supportive to strategic.
Cumulative Impact of United States Tariffs in 2025
In 2025, tariffs imposed by the United States on imported heat exchange components and materials have had a multifaceted impact. Equipment suppliers have confronted higher input costs for shell-and-tube units made from stainless steel and composite materials, prompting many to localize production or source alternative alloys domestically. As a result, manufacturers of carbon steel exchangers have experienced increased demand, while providers relying on advanced coatings with corrosion-resistant or high-temperature shield properties have absorbed cost pressures.
Simultaneously, recovery technology specialists focusing on Thermoelectric modules have navigated raw material surcharges by refining supply chains and negotiating long-term contracts. Companies delivering Organic Rankine Cycle equipment have strategically partnered with local integrators to bypass certain tariff barriers, maintaining competitive pricing. Despite initial disruptions, these adjustments have accelerated innovation in adaptive regulation platforms, as advanced control providers prioritize software-driven performance gains over hardware-intensive upgrades.
The cumulative effect of these policy shifts has been a recalibration of pricing models, with retrofits gaining traction as organizations seek to avoid import duties on new installations. Energy-intensive industries such as petrochemical and paper and pulp have increasingly turned to in-house engineering divisions to custom engineer modular heat recovery solutions, mitigating external cost volatility and securing long-term efficiency improvements.
Key Market Segmentation Insights
Analyzing the market through multiple segmentation lenses reveals nuanced growth drivers and potential bottlenecks. When assessed by system type, air preheaters and plate-fin exchangers dominate installations where compact footprint and high heat transfer rates are critical, whereas shell-and-tube solutions maintain prominence in large-scale power generation sites. Custom engineered designs, particularly those leveraging modular design principles, cater to facilities requiring rapid scalability and tailored thermal profiles.
From the perspective of recovery technology, absorption units remain attractive for low-grade heat applications, while thermoelectric modules find niche use in remote or off-grid operations due to their solid-state reliability. Organic Rankine Cycle systems strike a balance, converting mid-temperature waste streams into electricity, and advanced control technologies-enabled by both adaptive regulation and predictive optimization-drive incremental efficiency gains and reduce unplanned downtime.
Shifting to industrial applications, power generation and refinery operations account for substantial demand, leveraging waste heat to preheat feed streams and generate supplementary power. Steel production and cement manufacture use integrated heat exchangers to lower fuel consumption, whereas food processing and paper and pulp facilities prioritize compact heat recovery units to maintain hygiene standards and minimize footprint. Within installation types, new installations feature smart integration with IoT-enabled sensors and automated monitoring, while retrofit installation remains a cost-effective choice for brownfield sites.
Finally, examining material construction uncovers a trend toward alloy-based exchangers in high-corrosion environments, complemented by carbon steel units for general applications. Composite materials and stainless steel deliver longevity under extreme temperatures, and advanced coatings-both corrosion-resistant and high-temperature shield variations-extend equipment life and reduce lifecycle costs.
This comprehensive research report categorizes the Residual Heat Recovery System market into clearly defined segments, providing a detailed analysis of emerging trends and precise revenue forecasts to support strategic decision-making.
- System Type
- Recovery Technology
- Industrial Application
- Installation Type
- Material Construction
Key Regional Insights
Regional dynamics reveal distinct adoption patterns. In the Americas, strong incentive programs and energy cost pressures have driven significant uptake of smart integration solutions, with retrofit projects in petrochemical hubs and steel plants delivering quick payback. Latin America, meanwhile, shows emerging interest in organic Rankine cycle deployments to support expanding power generation capacity.
The Europe, Middle East & Africa region exhibits a broad commitment to circular economy targets, spurring investments in modular custom engineered heat recovery across cement, food processing, and refining sectors. Automated monitoring platforms, integrated with advanced control systems, have become prerequisites for achieving net-zero ambitions in European industrial corridors.
Asia-Pacific leads in greenfield installations, with new infrastructure projects in China and India prioritizing compact heat exchangers and shell-and-tube systems. The rapid industrialization of Southeast Asia has triggered demand for turnkey solutions, blending alloy-based construction with IoT-enabled performance tracking. Across this region, partnerships between local EPC firms and global technology providers are accelerating market penetration.
This comprehensive research report examines key regions that drive the evolution of the Residual Heat Recovery System market, offering deep insights into regional trends, growth factors, and industry developments that are influencing market performance.
- Americas
- Asia-Pacific
- Europe, Middle East & Africa
Key Competitive Company Insights
The competitive landscape comprises both established heavy-equipment manufacturers and agile technology innovators. From EcoHeat Integration Inc to Waste Not Thermal Solutions Inc, the roster includes EcoReclaim Thermal Inc, EcoThermal Solutions LLC, EffiHeat Technologies Inc, FluxHeat Recovery Systems Inc, Green Energy Recoveries Corp, Heat Recovery Innovations Inc, HeatCycle Technologies Ltd, HeatGuard Recovery Corp, HeatLink Recovery Corp, HeatSustain Innovations Inc, HeatWise Recovery Technologies LLC, HeatX Change Systems Corp, Reclaim Energy Corp, Reclaim Thermal Systems LLC, Regen Thermal Dynamics Corp, ReHeat Technologies Inc, Residual Dynamics Solutions Inc, Residual Power Recovery Inc, Residue Energy Systems Inc, Sunergy Residual Tech Inc, TempSave Energy Systems Ltd, ThermalFlux Innovations LLC, ThermalRevamp Systems Corp, ThermalWave Solutions LLC, ThermoEconomics Solutions LLC, ThermoRevive Industries Inc, ThermoSmart Designs LLC, Waste Heat Minimizers Corp, and Waste Not Thermal Solutions Inc. Within this diverse group, companies specializing in adaptive regulation and predictive optimization are carving out leadership positions, offering advanced control platforms that complement both absorption and Organic Rankine Cycle deployments.
Manufacturers of modular custom engineered units have built strong relationships with EPC contractors, delivering scalable pre-fabricated solutions that minimize on-site assembly time. Conversely, players focused on composite materials and high-temperature shield coatings are differentiating through enhanced durability and lower maintenance requirements. As IoT-enabled smart integration becomes standard, technology providers offering end-to-end digital monitoring and analytics platforms are gaining traction, forging strategic alliances with industrial conglomerates to bundle hardware, software, and service agreements.
This comprehensive research report delivers an in-depth overview of the principal market players in the Residual Heat Recovery System market, evaluating their market share, strategic initiatives, and competitive positioning to illuminate the factors shaping the competitive landscape.
- EcoHeat Integration Inc
- EcoReclaim Thermal Inc
- EcoThermal Solutions LLC
- EffiHeat Technologies Inc
- FluxHeat Recovery Systems Inc
- Green Energy Recoveries Corp
- Heat Recovery Innovations Inc
- HeatCycle Technologies Ltd
- HeatGuard Recovery Corp
- HeatLink Recovery Corp
- HeatSustain Innovations Inc
- HeatWise Recovery Technologies LLC
- HeatX Change Systems Corp
- Reclaim Energy Corp
- Reclaim Thermal Systems LLC
- Regen Thermal Dynamics Corp
- ReHeat Technologies Inc
- Residual Dynamics Solutions Inc
- Residual Power Recovery Inc
- Residue Energy Systems Inc
- Sunergy Residual Tech Inc
- TempSave Energy Systems Ltd
- ThermalFlux Innovations LLC
- ThermalRevamp Systems Corp
- ThermalWave Solutions LLC
- ThermoEconomics Solutions LLC
- ThermoRevive Industries Inc
- ThermoSmart Designs LLC
- Waste Heat Minimizers Corp
- Waste Not Thermal Solutions Inc
Actionable Recommendations for Industry Leaders
Industry leaders should prioritize a holistic approach that marries advanced technology with strategic partnerships. By investing in adaptive regulation and predictive optimization capabilities, operators can unlock incremental efficiency gains without extensive hardware overhauls. Collaborating with suppliers of high-performance materials-such as composite alloys and advanced coatings-will also reinforce long-term reliability and reduce total cost of ownership.
Simultaneously, executives must evaluate the merits of new installations versus retrofit strategies in light of evolving tariff frameworks. Engaging engineering firms capable of delivering modular custom engineered solutions can accelerate deployment and mitigate tariff exposure, while targeting retrofit projects in high-heat-loss applications will drive rapid ROI. In regions with mature incentive regimes, firms should structure projects to capitalize on grants and carbon credit programs, integrating smart IoT-enabled monitoring to validate performance and secure ongoing rebates.
Finally, forging alliances between digital control specialists and traditional equipment manufacturers will be critical. By embedding automated monitoring and analytics into core heat recovery offerings, companies can create differentiated service models, shifting from one-time sales to subscription-based performance solutions. This collaborative mindset will enable stakeholders to navigate policy headwinds, accelerate decarbonization, and sustain competitive advantage.
Explore AI-driven insights for the Residual Heat Recovery System market with ResearchAI on our online platform, providing deeper, data-backed market analysis.
Ask ResearchAI anything
World's First Innovative Al for Market Research
Conclusion: Harnessing Waste Heat for Strategic Advantage
Residual heat recovery systems stand at the intersection of efficiency, sustainability, and digital innovation. By understanding the transformative shifts in materials, controls, and policy environments, stakeholders can harness heat that once went to waste, turning it into a strategic asset. The cumulative impact of trade measures, segmentation dynamics, regional variations, and competitive positioning underscores the need for a cohesive strategy that blends technology adoption, partnership development, and proactive policy navigation.
As industrial operations intensify global energy demands, residual heat recovery will be a cornerstone of efforts to reduce emissions, lower operating costs, and achieve net-zero targets. The insights presented here empower decision-makers to move beyond isolated projects toward integrated energy strategies, where every degree of thermal energy is captured, optimized, and valorized.
This section provides a structured overview of the report, outlining key chapters and topics covered for easy reference in our Residual Heat Recovery System market comprehensive research report.
- Preface
- Research Methodology
- Executive Summary
- Market Overview
- Market Dynamics
- Market Insights
- Cumulative Impact of United States Tariffs 2025
- Residual Heat Recovery System Market, by System Type
- Residual Heat Recovery System Market, by Recovery Technology
- Residual Heat Recovery System Market, by Industrial Application
- Residual Heat Recovery System Market, by Installation Type
- Residual Heat Recovery System Market, by Material Construction
- Americas Residual Heat Recovery System Market
- Asia-Pacific Residual Heat Recovery System Market
- Europe, Middle East & Africa Residual Heat Recovery System Market
- Competitive Landscape
- ResearchAI
- ResearchStatistics
- ResearchContacts
- ResearchArticles
- Appendix
- List of Figures [Total: 26]
- List of Tables [Total: 420 ]
Call to Action: Secure Your Detailed Market Research Report with Ketan Rohom
To explore these insights in greater depth and obtain a detailed roadmap tailored to your organization’s needs, contact Ketan Rohom, Associate Director, Sales & Marketing. Unlock the full potential of residual heat recovery by securing the comprehensive market research report today.
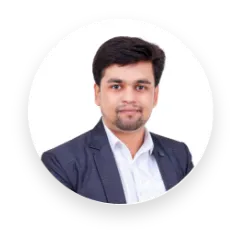
- When do I get the report?
- In what format does this report get delivered to me?
- How long has 360iResearch been around?
- What if I have a question about your reports?
- Can I share this report with my team?
- Can I use your research in my presentation?