The Reticulated Foam Market size was estimated at USD 608.11 million in 2024 and expected to reach USD 647.97 million in 2025, at a CAGR 6.50% to reach USD 887.40 million by 2030.

Recognizing How Reticulated Foam’s Unique Properties Are Driving Its Adoption Across Filtration, Cushioning, and Soundproofing Industries Globally
Reticulated foam, an open-cell material created through a precise reticulation process that removes cell membranes while preserving a robust skeleton, has emerged as an indispensable solution across high-performance applications. Its exceptional porosity and interconnected cellular architecture enable superior fluid and air permeability, positioning it distinctively in filtration and fluid-management systems. Beyond its filtration pedigree, reticulated foam’s resilience and shock-absorption qualities have led to rapid adoption in cushioning products, where uniform force distribution and long-term durability are prized.
This material’s versatility extends further into soundproofing, where its sound-damping capabilities address acoustic challenges in architectural and automotive interiors. The ability to tailor pore size and density through controlled manufacturing parameters grants designers and engineers a high degree of customization, from medical wound care dressings requiring ultra-fine pore connectivity to automotive seat cushions demanding both comfort and structural integrity.
As competitive pressures and performance demands intensify, manufacturers continue to refine both polymer chemistry and reticulation techniques, unlocking novel formulations and adding value through enhanced environmental friendliness. Regulatory trends toward energy efficiency and clean manufacturing processes are reinforcing reticulated foam’s appeal, as industry leaders explore bio-based feedstocks and closed-loop recycling methods. In this context, understanding the fundamentals of reticulated foam becomes essential for stakeholders aiming to capitalize on its rapid rise across filtration, cushioning, and noise-reduction markets.
Identifying the Pivotal Technological, Sustainability, and Manufacturing Innovations That Are Transforming the Reticulated Foam Market Landscape Worldwide
The reticulated foam industry is undergoing a profound metamorphosis driven by technological breakthroughs, heightened sustainability imperatives, and evolving manufacturing paradigms. Advances in digital manufacturing have enabled real-time process monitoring and tighter control over reticulation uniformity, yielding foams with consistent pore structures and enhanced performance predictability. Concurrently, the integration of Internet of Things sensors into production lines is facilitating predictive maintenance and reducing downtime, bolstering operational efficiency.
Sustainability has surged to the forefront of strategic priorities, with major foam producers investing in bio-based polyol research and exploring solvent-free reticulation techniques. Such initiatives not only align with global carbon-reduction commitments but also respond to end-users demanding greener materials and transparent supply chains. In parallel, the advent of additive manufacturing is expanding the design envelope of reticulated foam, enabling complex geometries previously unattainable with traditional cutting and bonding methods.
Market players are also harnessing data analytics to forecast maintenance cycles in filtration systems and quantify lifecycle benefits, thereby strengthening value propositions to industrial and municipal customers. This convergence of digitalization, bio-innovation, and lean manufacturing is forging a new paradigm in which reticulated foam solutions deliver both high performance and environmental credentials. As these transformative trends accelerate, stakeholders must adapt strategies to leverage advanced production technologies and sustainable materials in order to maintain competitive advantage.
Evaluating the Cumulative Impact of 2025 United States Tariffs on Reticulated Foam Supply Chains, Material Costs, and Industry Profitability Dynamics
In early 2025, United States trade policy introduced a series of layered tariffs on polyurethane raw materials and associated equipment, reshaping the reticulated foam supply chain and cost structure. Beginning March 4, 2025, an additional ad valorem tariff of 20% was imposed on all polyurethane feedstocks originating from China and Hong Kong, adding to existing anti-dumping and countervailing duties and intensifying cost pressures on converters and downstream product manufacturers. Shortly thereafter, the U.S. further escalated duties on Chinese goods, raising aggregate tariffs on key polyether polyols and diisocyanates to as high as 145% through successive increments in April 2025. These cumulative levies have dramatically altered the competitive landscape, favoring domestic and near-shore suppliers while amplifying global sourcing challenges.
Manufacturers reliant on imported resins and reticulation chambers have been forced to incorporate elevated raw-material costs into second-quarter pricing offers, with some opting to absorb part of the incremental expenses to mitigate customer pushback. The ripple effects extend to filtration equipment OEMs and automotive seating suppliers, where the surging base costs for toluene diisocyanate (TDI) and flexible polyether polyols are eroding margins and prompting extended lead times as procurement teams scramble to secure volume at viable rates.
To offset tariff-induced inflation, several foam converters are accelerating investments in localized polymer capacity and reticulation services, seeking to reshape their supply chains around lower-duty jurisdictions. At the same time, strategic stockpiling of critical feedstocks and renegotiation of long-term supply contracts are emerging as common tactics to stabilize input pricing. As these trade measures persist, the reticulated foam sector continues to navigate heightened uncertainty, balancing short-term cost containment with longer-term supply security and regulatory compliance.
Uncovering In-Depth Segment-Level Drivers and Dynamics Across Material Types, Forms, Applications, Industries, Pore Sizes, and Manufacturing Processes
The reticulated foam market exhibits a high degree of heterogeneity when dissected through multiple segmentation lenses, each revealing distinct growth drivers and performance priorities. Material type analysis uncovers a split between ceramic and metallic foams, valued for high-temperature and chemical resistance, and polymer-based counterparts such as polyethylene and polyurethane, prized for their lightweight and cushioning attributes. Within metals, aluminum and stainless steel foams cater to aerospace and structural applications, while high-density and low-density polyethylene grades balance rigidity and flexibility in filtration media. Polyurethane variants span from rigid structural boards to flexible cushioning pads, serving sectors from construction to furniture.
Examining form factors further highlights the industry’s customization capabilities. Solid blocks of reticulated foam accommodate large-scale fluid management systems, whereas sheets and filter cartridges are engineered for modular installation in HVAC and industrial filtration units. Rolls, available in both bulk and precisely slit widths, streamline automated cutting and sealing processes within appliance manufacturing lines.
Application segmentation underscores reticulated foam’s versatility: cushioning options address both packaging and seating comfort, while air and liquid filtration foams secure critical environments in pharmaceuticals, water treatment, and food processing. In soundproofing contexts, bespoke foam formulations attenuate noise across automotive cabins and recording studios, leveraging pore-size gradations to target specific frequency bands.
End-use industries range from automotive aftermarket and OEM seating systems to healthcare devices and HVAC equipment, with each vertical imposing unique specifications on foam porosity and resilience. Pore-size differentiation into high, medium, and low PPI tiers permits fine-tuning of flow resistance and particle capture efficiency, while manufacturing processes, whether chemical routes employing foaming agents and solvent extraction or physical methods like mechanical rupturing and melt expansion, dictate final foam morphology and performance.
This comprehensive research report categorizes the Reticulated Foam market into clearly defined segments, providing a detailed analysis of emerging trends and precise revenue forecasts to support strategic decision-making.
- Material Type
- Form
- Application
- End Use Industry
- Pore Size
- Manufacturing Process
Examining Regional Reticulated Foam Market Dynamics and Growth Opportunities Across the Americas, EMEA, and Asia-Pacific Regions
Across the Americas, reticulated foam demand is anchored by a strong domestic filtration equipment sector and a reinvigorated automotive industry seeking locally sourced components. Tariff policy shifts have spurred capital investments in U.S.-based polyol production and reticulation services, buttressed by government incentives aimed at strengthening homeland supply chains. This has led to new continuous foam lines in the Midwest and Southeast, targeting downstream markets in HVAC, water treatment, and specialty fluid management.
In Europe, Middle East & Africa, stringent environmental regulations and a focus on circular economy principles are driving innovation in sustainable feedstocks and recycling initiatives. European foam producers are collaborating with chemical manufacturers to introduce bio-based polyols and reclaim post-consumer foam through advanced depolymerization processes. Meanwhile, rapid growth in Middle Eastern petrochemical capacity is positioning the region as an emerging export hub for high-performance polyether and polyester resins destined for foam converters in Africa and Southern Europe.
Asia-Pacific remains the fastest expanding region, propelled by robust construction activity, rising urbanization in India and Southeast Asia, and significant capital projects in China’s filtration and water infrastructure sectors. Local foam manufacturers are scaling output of both polymer and metallic foams, leveraging cost-competitive feedstocks and leveraging automation to serve domestic and export markets. Moreover, partnerships between multinationals and regional converters are accelerating technology transfer, enabling tailored foam formulations for applications ranging from marine buoyancy modules to medical wound care dressings.
This comprehensive research report examines key regions that drive the evolution of the Reticulated Foam market, offering deep insights into regional trends, growth factors, and industry developments that are influencing market performance.
- Americas
- Europe, Middle East & Africa
- Asia-Pacific
Profiling Leading Reticulated Foam Manufacturers and Suppliers Highlighting Their Strategic Initiatives and Competitive Advantages
Leading reticulated foam manufacturers have adopted differentiated strategies to secure competitive advantages and address emerging market demands. Major chemical producers with vertically integrated operations are expanding polyol and isocyanate capacities adjacent to reticulation facilities, ensuring tighter cost control and supply stability. These players are also investing heavily in research centers to advance bio-based foam chemistries and develop next-generation additive packages that enhance flame retardance and antimicrobial performance.
Specialty foam converters are focusing on high-value niches, collaborating closely with OEM customers to co-develop bespoke filter cartridges and cushioning modules. By leveraging advanced digital design tools and rapid prototyping, they reduce time-to-market for customized foam solutions in critical industries such as healthcare, where sterile filtration and medical-grade biocompatibility are paramount. These converters are also forging alliances with equipment OEMs to integrate sensor-embedded foam components capable of real-time performance monitoring.
On the distribution front, global foam suppliers are broadening their logistics networks to offer just-in-time deliveries under flexible contractual models. This approach mitigates inventory carrying costs for end users and enhances response capabilities during demand surges, particularly in filtration and HVAC replacement cycles. Strategic acquisitions of regional converters and partnerships with local chemical distributors further strengthen market reach, highlighting a trend toward consolidation tempered by targeted investments in innovative foam platforms.
This comprehensive research report delivers an in-depth overview of the principal market players in the Reticulated Foam market, evaluating their market share, strategic initiatives, and competitive positioning to illuminate the factors shaping the competitive landscape.
- Recticel NV
- Zotefoams plc
- BASF SE
- FoamPartner AG
- Rogers Corporation
- The Carpenter Company
- Vita Group LLC
- Sekisui Alveo Co., Ltd.
- Foamex International Limited
- UFP Technologies, Inc.
Delivering Actionable Strategic Recommendations to Navigate Supply Chain Disruptions, Innovate Materials, and Capitalize on Market Shifts
To thrive amid tariff fluctuations and intensifying sustainability mandates, industry leaders should first diversify raw material sourcing by forging partnerships with non-Chinese polyol and diisocyanate suppliers and exploring near-shore production hubs. This approach will flatten supply chain volatility and reduce exposure to abrupt policy shifts. Next, accelerating investments in bio-based and recycled feedstocks will not only capture emerging eco-premium segments but also align with evolving regulatory landscapes and corporate decarbonization targets.
Embedding digitalization across the value chain is equally critical. Implementing IoT-enabled process controls and predictive analytics will elevate quality consistency, shorten production cycles, and lower operating costs. Leaders should also leverage additive manufacturing for rapid foam prototyping, enabling agile responses to customization demands from filtration and cushioning OEMs.
Collaborative innovation remains a cornerstone of competitive differentiation. Companies should co-invest with end users on performance testing and lifecycle validation, particularly in high-growth verticals such as medical devices and water treatment. Joint ventures with equipment manufacturers to integrate sensor-enabled foam components can unlock new service-based revenue streams tied to condition-based maintenance.
Finally, proactive monitoring of global trade policies and participation in industry associations will provide early warning signals on tariff escalations and regulatory shifts. By adopting a scenario-planning framework, companies can develop contingency plans and secure strategic reserves of critical feedstocks to ensure uninterrupted production and safeguard profit margins.
Outlining a Comprehensive Research Methodology Integrating Expert Interviews, Secondary Sources, and Robust Analytical Frameworks
This research combines a rigorous multi-stage methodology to deliver authoritative insights into the reticulated foam market. Secondary data collection encompassed comprehensive reviews of trade association publications, government customs databases, and technical literature on reticulation processes. Industry reports and patent filings were analyzed to map innovation trajectories and benchmark key material parameters.
Primary research involved structured interviews with senior executives at polymer manufacturers, foam converters, and filtration equipment OEMs across North America, Europe, and Asia-Pacific. These discussions provided qualitative depth on supply chain strategies, pricing mechanisms, and technology adoption. Validation workshops with industry experts were conducted to test preliminary findings and refine segmentation frameworks.
Quantitative analysis employed material mass-balance modeling to assess feedstock flows and tariff-induced cost impacts. Pore-size distribution and performance metrics were benchmarked through case studies in filtration and cushioning applications. A triangulation approach ensured data integrity, cross-verifying interview insights against secondary sources and proprietary databases.
The resulting research framework delivers both strategic intelligence and application-level detail, enabling stakeholders to make informed investment decisions, optimize product development roadmaps, and navigate complex international trade environments.
Explore AI-driven insights for the Reticulated Foam market with ResearchAI on our online platform, providing deeper, data-backed market analysis.
Ask ResearchAI anything
World's First Innovative Al for Market Research
Summarizing Key Insights and Strategic Considerations for Stakeholders Navigating the Evolving Reticulated Foam Landscape
The reticulated foam market stands at a pivotal juncture, shaped by rapid technological innovation, evolving sustainability expectations, and shifting trade dynamics. Stakeholders must navigate an intricate web of material variations-from metallic and ceramic foams to polyethylene and polyurethane grades-in tandem with form-factor customization that spans blocks, sheets, rolls, and ready-to-install cartridges. Strategic segmentation based on pore size and manufacturing process further underscores the sector’s complexity and opportunity.
Regionally, the Americas are witnessing a resurgence in domestic production driven by tariff-related localization incentives, while Europe, Middle East & Africa are pioneering bio-based and recycling initiatives under the banner of circular economy principles. Asia-Pacific continues to lead growth, buoyed by infrastructure expansion and rising demand in filtration and medical markets. Against this backdrop, leading manufacturers are pursuing integrated production models, digital transformation, and customer-centric co-innovation to secure competitive advantage.
As the landscape evolves, companies that proactively diversify supply chains, adopt sustainable feedstocks, and embed digital capabilities will outperform peers. Equally, those that leverage collaborative partnerships to accelerate tailored foam solutions for high-value applications will unlock new revenue streams. Ultimately, a strategic blend of operational resilience, technological foresight, and market intimacy is essential for capitalizing on the reticulated foam sector’s dynamic growth trajectory.
This section provides a structured overview of the report, outlining key chapters and topics covered for easy reference in our Reticulated Foam market comprehensive research report.
- Preface
- Research Methodology
- Executive Summary
- Market Overview
- Market Dynamics
- Market Insights
- Cumulative Impact of United States Tariffs 2025
- Reticulated Foam Market, by Material Type
- Reticulated Foam Market, by Form
- Reticulated Foam Market, by Application
- Reticulated Foam Market, by End Use Industry
- Reticulated Foam Market, by Pore Size
- Reticulated Foam Market, by Manufacturing Process
- Americas Reticulated Foam Market
- Europe, Middle East & Africa Reticulated Foam Market
- Asia-Pacific Reticulated Foam Market
- Competitive Landscape
- ResearchAI
- ResearchStatistics
- ResearchContacts
- ResearchArticles
- Appendix
- List of Figures [Total: 30]
- List of Tables [Total: 1360 ]
Engage with Ketan Rohom to Access the Detailed Reticulated Foam Market Research Report Tailored for Informed Strategic Decision-Making
To gain access to the full, in-depth reticulated foam market research report and unlock the strategic intelligence needed to navigate this evolving sector, reach out directly to Ketan Rohom, Associate Director of Sales & Marketing at 360iResearch. Ketan can provide tailored guidance on how the report’s insights align with your business priorities, share sample excerpts to illustrate the depth of analysis, and outline the flexible licensing options available for single users, corporate teams, or enterprise-wide deployments. Engaging with Ketan ensures you receive hands-on support in interpreting the data, identifying growth opportunities in filtration, cushioning, and beyond, and developing a competitive roadmap grounded in the latest market dynamics. Connect with Ketan today to secure your comprehensive reticulated foam market intelligence and gain a decisive advantage in planning product innovation, supply chain strategies, and regional market entry initiatives.
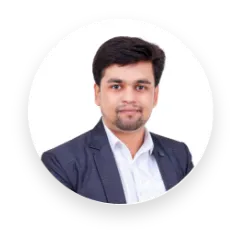
- How big is the Reticulated Foam Market?
- What is the Reticulated Foam Market growth?
- When do I get the report?
- In what format does this report get delivered to me?
- How long has 360iResearch been around?
- What if I have a question about your reports?
- Can I share this report with my team?
- Can I use your research in my presentation?