Introduction: The Evolving Role of RFID Tag Production Equipment
The explosive growth of the Internet of Things, coupled with pressing demands for real-time visibility and automation, has thrust RFID tag production equipment into the spotlight. As industries from retail to healthcare embrace digital transformation, the machinery that writes, encodes and validates RFID tags has become a strategic asset rather than a mere manufacturing tool. In this rapidly evolving environment, manufacturers of encoding machines, printers and quality-assurance systems must adapt to a shifting technology landscape, tighter regulatory requirements and increasingly complex customer specifications.
Against this backdrop, executives and decision-makers require a clear view of the forces reshaping production workflows, cost structures and competitive dynamics. This executive summary offers a concise yet comprehensive overview of the market’s transformative shifts, the impact of new US tariffs, key segmentation and regional trends, leading players’ positioning and actionable recommendations for industry leaders charting their next growth phase.
Transformative Shifts Reshaping RFID Tag Production
Over the past five years, the RFID tag production landscape has undergone seismic changes. Automation levels have skyrocketed as advanced robotics and machine-vision systems deliver faster throughput and near-zero error rates. Concurrently, a wave of miniaturization has introduced ultra-compact encoding heads capable of handling high-density tag arrays in a single pass. These innovations have not only accelerated capacity but have also unlocked new use cases in sectors such as pharmaceuticals, where precision and traceability are paramount.
Meanwhile, converging digital technologies-cloud-based data management, edge computing and machine learning-are redefining production optimization. Predictive maintenance analytics now anticipate equipment failures before they occur, driving uptime above 98 percent. Real-time dashboards inform operators of yield metrics, cycle times and tag quality in a single integrated view. As a result, production equipment has evolved from standalone machines into interconnected nodes within an intelligent manufacturing ecosystem.
Looking ahead, the push for greener operations is driving machine builders to adopt energy-efficient motors, heat-recovery systems and modular designs that minimize waste. At the same time, growing concerns around data security are elevating the importance of hardware-level encryption capabilities. Together, these trends underscore a crucial truth: in today’s hyper-competitive market, differentiation increasingly hinges on equipment agility, intelligence and sustainability.
Cumulative Impact of United States Tariffs in 2025
The introduction of the United States’ 2025 tariff schedule has injected fresh complexity into the RFID tag production supply chain. Tariffs on key components-readers, antennas and specialized encoding chips-have driven material costs up by double digits for domestic manufacturers. As a result, many equipment suppliers face margin compression, prompting them to explore alternatives such as dual-sourcing and localized assembly to mitigate exposure.
In response, global vendors have reconfigured their supplier networks, shifting a portion of procurement to regions exempt from levies or benefiting from preferential trade agreements. At the same time, some manufacturers are reallocating production to low-tariff zones, balancing transportation costs against duty savings. This recalibration has ripple effects across lead times, inventory strategies and capital-expenditure planning.
Despite these headwinds, the tariff environment has also catalyzed innovation. Equipment OEMs are investing in in-house chip development and forging partnerships to secure long-term supply. Others are redesigning systems to support multiple component standards and plug-and-play modules that can be sourced from diverse vendors. Ultimately, while tariffs have disrupted cost baselines, they have accelerated the industry’s drive toward supply-chain resilience and technical self-sufficiency.
Key Segmentation Insights Driving Equipment Strategy
A granular understanding of market segments reveals where demand for production equipment will intensify and which areas merit targeted investment. When analyzed by product type, manufacturers of active RFID tags-a category favoring battery-powered, long-range applications-require high-precision laser etching and multi-frequency encoding modules, whereas producers of passive and semi-passive tags prioritize high-speed printing and batch verification systems to meet volume targets.
Examining frequency range shows that ultra-high frequency deployments demand inline calibration and advanced error-correction software, while low-frequency and high-frequency lines emphasize simplified coil winding stations and cost-effective antenna testing rigs. Component-level segmentation highlights a thriving market for embedded middleware platforms that orchestrate tag serialization, data encryption and cloud integration alongside traditional hardware like readers, antennas and tags.
Industry-specific insights underline the value of customization. In agriculture, equipment tailored for animal tracking and crop monitoring features ruggedized modulators and field-calibrated sensors. In healthcare, dedicated lines for medical devices and pharmaceuticals integrate tamper-evident encoding and regulatory-compliance workflows. Automotive and industrial machinery producers in manufacturing demand heavy-duty reel-to-reel systems with zero-defect detection, while retail operations-spanning apparel, electronics and food & beverages-leverage high-throughput thermal printers with batch-level serialization. Transportation and logistics players, including distribution centers, freight carriers and warehouse managers, seek end-to-end encoding solutions that seamlessly integrate with existing conveyors and RFID gateways.
The application layer further differentiates equipment needs: asset tracking systems for inventory control and supply chain management require synchronized multi-reader calibration, contactless payment terminals emphasize secure element programming, logistics and transport lines concentrate on mobile encoding carts, and security & access control deployments-encompassing employee ID cards and secure entry systems-focus on embedded biometric module support.
Advances in wireless standards such as Bluetooth Low Energy, Near-Field Communication and Ultra-Wideband are shaping equipment roadmaps, driving OEMs to offer configurable interfaces. Likewise, power-source segmentation-battery operated versus energy harvesting-dictates machine design priorities, from built-in charge stations to ultra-low-power wake-up circuits. Installation requirements split between fixed RFID systems housed in dedicated production cells and mobile RFID systems mounted on carts or vehicles. Finally, enterprise size and data management preferences-whether cloud-based, hybrid or on-premise-alongside functional components spanning hardware integration, managed services and software integration define diverse go-to-market opportunities.
This comprehensive research report categorizes the RFID Tag Production Equipment market into clearly defined segments, providing a detailed analysis of emerging trends and precise revenue forecasts to support strategic decision-making.
- Product Type
- Frequency Range
- Component
- End-Use Industry
- Application
- Technology
- Power Source
- Installation Type
- Enterprise Size
- Data Management Solutions
- Functional Component
Key Regional Insights Highlighting Growth Pockets
Regional dynamics continue to shape the competitive landscape for RFID tag production equipment. In the Americas, robust demand from retail, logistics and healthcare sectors sustains investments in high-throughput encoding lines and integrated quality management platforms. Local OEMs benefit from proximity to end-users and can offer rapid deployment services, yet they must navigate complex trade policies across North and South America.
Europe, the Middle East & Africa present a mosaic of opportunities: stringent data-privacy regulations in the EU drive demand for encryption-enabled machinery, while the Middle East’s large-scale logistics hubs invest heavily in advanced automation to support growing e-commerce volumes. In Africa, infrastructure upgrades and pilot programs in agriculture and healthcare spur interest in portable and rugged tag-printing devices.
In Asia-Pacific, a combination of mature markets-Japan, South Korea and Australia-and rapidly expanding economies-India and Southeast Asia-fuels both volume and innovation. High labor costs in developed APAC nations encourage the adoption of fully automated, lights-out production cells, whereas cost-sensitive markets favor modular, semi-automated solutions that can scale incrementally.
Across all regions, proximity to key component suppliers, local standards compliance, service network density and aftermarket support capabilities influence purchasing decisions. Equipment providers that tailor offerings to regional regulatory frameworks and language requirements gain a significant competitive edge.
This comprehensive research report examines key regions that drive the evolution of the RFID Tag Production Equipment market, offering deep insights into regional trends, growth factors, and industry developments that are influencing market performance.
- Americas
- Asia-Pacific
- Europe, Middle East & Africa
Key Company Insights Shaping Competitive Dynamics
The competitive ecosystem for RFID tag production equipment spans established conglomerates and specialized technology firms. Alien Technology Corporation and Avery Dennison Corporation leverage broad portfolios of tag materials and in-line printing systems, while CAEN RFID Srl and FEIG Electronic GmbH focus on high-precision encoding modules and reader-writer integration.
Confidex Ltd. and GAO RFID Inc. have carved niches with modular, field-serviceable platforms suited for rugged environments, whereas HID Global Corporation and Honeywell International Inc. bring decades of industrial automation and security expertise to turnkey production lines. Impinj, Inc. and Invengo Technology Corporation Ltd. drive innovation in chip-embedded encoding, collaborating closely with semiconductor providers like NXP Semiconductors N.V.
Microsensys GmbH and Rinas Gerätetechnik GmbH specialize in antenna testing rigs and calibration services, while SAG Securitag Assembly Group and Smartrac N.V. focus on high-volume reel-to-reel printing and embedding processes. Tageos SAS and ThingMagic, a Division of Novanta, Inc., offer flexible, software-driven encoding appliances that integrate seamlessly with cloud-based management platforms.
Voyantic Ltd. leads the market in quality-assurance systems with over-the-air tag performance analytics, and Zebra Technologies Corporation unites RFID hardware with comprehensive middleware suites. Each of these players differentiates through a combination of technical innovation, after-sales support and strategic partnerships with system integrators.
This comprehensive research report delivers an in-depth overview of the principal market players in the RFID Tag Production Equipment market, evaluating their market share, strategic initiatives, and competitive positioning to illuminate the factors shaping the competitive landscape.
- Alien Technology Corporation
- Avery Dennison Corporation
- CAEN RFID Srl
- Confidex Ltd.
- FEIG Electronic GmbH
- GAO RFID Inc.
- HID Global Corporation
- Honeywell International Inc.
- Impinj, Inc.
- Invengo Technology Corporation Ltd.
- Microsensys GmbH
- NXP Semiconductors N.V.
- Rinas Gerätetechnik GmbH
- SAG Securitag Assembly Group
- Smartrac N.V.
- Tageos SAS
- ThingMagic, a Division of Novanta, Inc.
- Voyantic Ltd.
- Zebra Technologies Corporation
Actionable Recommendations for Industry Leaders
To thrive in this dynamic environment, equipment manufacturers and end-users should prioritize three strategic imperatives. First, accelerate integration of digital-twin and AI-driven analytics to optimize machine performance and predict maintenance needs. By turning production data into actionable insights, leaders can drive yield improvements and reduce downtime.
Second, diversify supply chains and establish component-agnostic architectures. Embracing plug-and-play modules and multi-vendor interoperability safeguards operations against geopolitical disruptions and tariff volatility. Collaborative relationships with semiconductor foundries, connector suppliers and middleware developers enhance resilience and innovation velocity.
Third, adopt a solutions-oriented go-to-market approach. Rather than selling standalone machines, equipment providers should bundle hardware with managed services-such as remote diagnostics, firmware updates and operator training-and customizable software integration. This shift from capex-only transactions to recurring revenue models deepens customer relationships and boosts lifetime value.
Additionally, investing in green manufacturing practices-energy-efficient drives, recyclable materials and modular upgrades-addresses both regulatory pressures and corporate sustainability goals. Finally, fostering partnerships with standards bodies and industry consortia ensures early compliance with emerging protocols, positioning leading firms as trusted advisors in a fast-moving market.
Explore AI-driven insights for the RFID Tag Production Equipment market with ResearchAI on our online platform, providing deeper, data-backed market analysis.
Ask ResearchAI anything
World's First Innovative Al for Market Research
Conclusion: Positioning for the Next Wave of RFID Innovation
The RFID tag production equipment sector stands at the intersection of technological innovation, global trade dynamics and evolving customer requirements. As automation, data connectivity and sustainability take center stage, equipment OEMs and their customers must adopt agile strategies to maintain competitive advantage. By aligning machine design with application-specific needs, diversifying supply chains to counter tariff pressures and embedding intelligence across the production floor, industry participants can unlock new revenue streams and operational efficiencies.
Ultimately, success will go to those who view production equipment not as a standalone asset but as a core element of a fully connected, data-driven manufacturing ecosystem. Organizations that embrace this holistic perspective will lead the next wave of RFID adoption and create lasting value across the supply chain.
This section provides a structured overview of the report, outlining key chapters and topics covered for easy reference in our RFID Tag Production Equipment market comprehensive research report.
- Preface
- Research Methodology
- Executive Summary
- Market Overview
- Market Dynamics
- Market Insights
- Cumulative Impact of United States Tariffs 2025
- RFID Tag Production Equipment Market, by Product Type
- RFID Tag Production Equipment Market, by Frequency Range
- RFID Tag Production Equipment Market, by Component
- RFID Tag Production Equipment Market, by End-Use Industry
- RFID Tag Production Equipment Market, by Application
- RFID Tag Production Equipment Market, by Technology
- RFID Tag Production Equipment Market, by Power Source
- RFID Tag Production Equipment Market, by Installation Type
- RFID Tag Production Equipment Market, by Enterprise Size
- RFID Tag Production Equipment Market, by Data Management Solutions
- RFID Tag Production Equipment Market, by Functional Component
- Americas RFID Tag Production Equipment Market
- Asia-Pacific RFID Tag Production Equipment Market
- Europe, Middle East & Africa RFID Tag Production Equipment Market
- Competitive Landscape
- ResearchAI
- ResearchStatistics
- ResearchContacts
- ResearchArticles
- Appendix
- List of Figures [Total: 38]
- List of Tables [Total: 818 ]
Call-To-Action: Contact Ketan Rohom to Access the Full Market Research Report
To gain deeper insights and actionable data on RFID tag production equipment, connect with Ketan Rohom, Associate Director of Sales & Marketing. Ketan can guide you through the full market research report, tailored slices of data and bespoke consulting packages designed to support strategic decision-making. Reach out today to secure your copy and stay ahead in an era defined by automation and intelligent manufacturing.
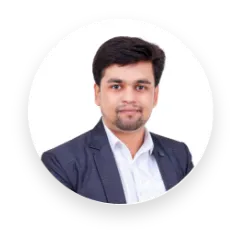
- When do I get the report?
- In what format does this report get delivered to me?
- How long has 360iResearch been around?
- What if I have a question about your reports?
- Can I share this report with my team?
- Can I use your research in my presentation?