Introduction to the Rigid Plastic Tubing Market
Rigid plastic tubing has become a cornerstone of modern industrial, medical, and consumer applications, offering unmatched durability, chemical resistance, and design flexibility. As sectors from automotive and aerospace to pharmaceuticals and food processing demand ever more robust fluid handling, rigid tubing provides a reliable conduit for liquids and gases under high pressure and temperature extremes. In recent years, manufacturers have invested heavily in advanced resin formulations and precision extrusion techniques to meet tougher safety standards and deliver lightweight, cost-effective solutions.
Amid rising global emphasis on circular economy principles, rigid plastic tubes now integrate recycled and bio-based polymers, redefining material efficiency without sacrificing performance. At the same time, digital manufacturing platforms and real-time quality monitoring enable custom dimensions and tighter tolerances, empowering end users to streamline assembly processes and reduce waste. As a critical component across hydraulic systems, intravenous medical devices, cable insulation, and packaging, rigid plastic tubing stands at the intersection of innovation and reliability.
This executive summary provides a strategic overview of transformative market shifts, regulatory dynamics, segmentation insights, regional performance, leading competitor strategies, and actionable recommendations designed to guide industry leaders through a rapidly evolving landscape.
Transformative Shifts Reshaping the Industry
Over the past decade, sustainability imperatives and technological breakthroughs have reshaped the rigid plastic tubing industry. Manufacturers increasingly shift toward bio-resins and advanced recycling methods, replacing traditional polyethylene and PVC with materials that reduce carbon footprints and support closed-loop systems. Parallel advances in extrusion blow molding and multi-cavity injection techniques have cut cycle times by up to 30% while improving dimensional accuracy, enabling high-speed production of complex tubing geometries.
Moreover, digital twins and in-line sensor systems now allow continuous quality verification, reducing scrap rates and accelerating time to market. Industry 4.0 integration not only enhances process transparency but also facilitates predictive maintenance, minimizing downtime and optimizing throughput. As a result, custom rigid tubing solutions have become more accessible to small and medium enterprises, fueling adoption across niche medical applications, smart packaging, and precision electronics.
Finally, supply chain resilience emerges as a critical priority. In response to past disruptions, leading operators diversify raw material sourcing, invest in regional manufacturing hubs, and form strategic alliances with resin producers. These shifts collectively underscore the industry’s commitment to agility, efficiency, and environmental stewardship.
Cumulative Impact of U.S. Tariffs in 2025
The introduction of new tariff schedules in 2025 has exerted significant pressure on import costs and supply chain structures. Increased duties on finished rigid tubing imports and key resin inputs such as PVC and high-density polyethylene have compelled distributors to reassess cost allocations, often passing higher expenses to downstream customers. Consequently, industrial end-users confront tighter budget constraints, prompting them to seek alternative suppliers and localized production options.
Furthermore, these tariff changes have accelerated investments in domestic resin manufacturing, as companies aim to mitigate exposure to cross-border levies. Regional processors have expanded capacity for homopolymer polypropylene and twin-screw extrusion to capture volume previously reliant on imports. Such capacity expansions, however, require substantial capital and carry lead times of 18 to 24 months, creating interim supply gaps that industry players address through strategic inventory builds.
As a result, product innovation has taken center stage: some firms redesign tubing profiles to optimize material usage and reduce kilo-gram cost exposure, while others explore polymer blends less affected by import duties. In parallel, collaborative agreements among resin suppliers, conduit fabricators, and end-users have emerged to share logistical risks and stabilize pricing. These adaptive measures underscore the industry’s resilience in navigating evolving trade policies and cost headwinds.
Key Segmentation Insights Across Six Dimensions
Rigorous segmentation analysis reveals distinct performance drivers across six dimensions. Based on material type, the market encompasses polyethylene-divided into high-density and low-density grades-polypropylene split between homopolymer and random copolymer, polystyrene offering general purpose and high impact variants, and polyvinyl chloride available in flexible and rigid formulations. When considering application, industrial uses such as hydraulic and pneumatic tubing compete alongside medical segments that include catheters, IV lines, and respiratory tubes, as well as packaging solutions for beverages and cosmetics.
End-use industries further clarify demand patterns: building and construction rely on conduit and plumbing tubes, electrical and electronics sectors adopt cable housing and encapsulation components, and healthcare institutions source tubing for diagnostic labs and hospital operations. Manufacturing methods add another layer of insight, covering extrusion blow molding via both extrusion and injection processes, single-screw and twin-screw extrusion, and specialized multi-cavity injection molding. Product form distinctions highlight corrugated tubing available in double-wall or single-wall variants, flexible elastomeric tubes, and rigid tubing offered in straight or shape-specific configurations. Finally, sales channels span direct routes through B2B representatives and manufacturers, alongside indirect distribution via distributors and retailers.
This comprehensive research report categorizes the Rigid Plastic Tubing market into clearly defined segments, providing a detailed analysis of emerging trends and precise revenue forecasts to support strategic decision-making.
- Material Type
- Application
- End-Use Industry
- Production Process
- Product Form
- Sales Channel
Key Regional Insights and Market Dynamics
Regional dynamics display pronounced differentiation in regulatory frameworks, raw material accessibility, and end-market priorities. The Americas lead with a mature industrial base and robust healthcare infrastructure, driving steady demand for high-performance tubing in oil and gas, automotive, and medical device applications. In contrast, Europe, Middle East & Africa emphasize stringent environmental regulations and recycling mandates, pushing suppliers to adopt certified recycled content and demonstrate circular-economy credentials.
Meanwhile, the Asia-Pacific region experiences rapid expansion driven by infrastructure development, burgeoning electronics manufacturing, and rising consumer packaging needs. Local players leverage cost-effective production and scalable extrusion capacity, often supported by government incentives aimed at boosting polymer processing industries. Transitioning across these regions, companies must tailor their value propositions-from sustainability claims in EMEA to cost competitiveness and rapid lead times in Asia-Pacific-while maintaining global quality standards.
This comprehensive research report examines key regions that drive the evolution of the Rigid Plastic Tubing market, offering deep insights into regional trends, growth factors, and industry developments that are influencing market performance.
- Americas
- Asia-Pacific
- Europe, Middle East & Africa
Key Company Strategies and Competitive Landscape
Competitive intensity stems from a diverse array of global and regional specialists. ALPLA Group and Amcor PLC alongside Bemis (merged into Amcor) have fortified their positions through portfolio diversification and vertical integration. Berry Global Inc. and RPC (now part of Berry) emphasize sustainable packaging solutions and recycled polymer content, while Constar International Inc. and Sealed Air Corporation focus on high-barrier properties for food and beverage applications.
German producers such as PACCOR International GmbH and Gerresheimer AG leverage advanced extrusion blow molding capabilities for pharmaceutical-grade tubing. Meanwhile, Greif Inc. and Huhtamaki PPL excel in industrial and consumer packaging formats, and Plastipak Packaging Inc. drives innovations in PET-based rigid tubes. Otto Environmental Systems North America and Silgan Holdings Inc. dedicate resources to circular processing technologies, and Sonoco Products Company invests in proprietary resin compounding to enhance mechanical strength. Collectively, these players deploy M&A, capacity expansions, and R&D to capture evolving demand.
This comprehensive research report delivers an in-depth overview of the principal market players in the Rigid Plastic Tubing market, evaluating their market share, strategic initiatives, and competitive positioning to illuminate the factors shaping the competitive landscape.
- ALPLA Group
- Amcor PLC
- Bemis Company Inc. (Merged with Amcor PLC)
- Berry Global Inc.
- Constar International Inc.
- Gerresheimer AG
- Greif Inc.
- Huhtamaki PPL
- Otto Environmental Systems North America Inc.
- PACCOR International GmbH
- Plastipak Packaging Inc.
- RPC Group PLC (Acquired by Berry Global)
- Sealed Air Corporation
- Silgan Holdings Inc.
- Sonoco Products Company
Actionable Recommendations for Industry Leaders
To thrive amid evolving regulations, tariff pressures, and sustainability expectations, industry leaders should prioritize four strategic imperatives. First, diversify resin sourcing by establishing multi-region supply agreements and investing in domestic polymer capacity, thereby insulating operations from tariff volatility and logistic disruptions. Second, accelerate adoption of recycled and bio-based polymers through partnerships with feedstock suppliers and certification bodies; by doing so, companies can secure access to growth segments in eco-conscious markets.
Third, integrate digital process controls and IoT-enabled monitoring across extrusion and molding lines, which will reduce production variance, lower scrap rates, and enable real-time traceability for quality assurance. Fourth, cultivate collaborative innovation by engaging end-users, research institutions, and resin producers in co-development initiatives focused on lightweighting, high-temperature performance, and antimicrobial properties for medical tubing. In addition, refining direct sales channels while optimizing distributor networks can enhance market responsiveness and improve margin structures. Embracing these recommendations will position industry leaders to capitalize on shifting demand and regulatory trends while reinforcing their competitive edge.
Explore AI-driven insights for the Rigid Plastic Tubing market with ResearchAI on our online platform, providing deeper, data-backed market analysis.
Ask ResearchAI anything
World's First Innovative Al for Market Research
Conclusion and Strategic Imperatives
In summary, the rigid plastic tubing market stands at a pivotal juncture shaped by sustainability mandates, technological innovation, and shifting trade policies. Transformative shifts in materials and manufacturing processes are redefining value propositions, while U.S. tariffs compel a strategic reassessment of supply chain configurations. A nuanced understanding of segmentation-spanning material types, applications, end-use industries, processes, product forms, and sales channels-is essential for identifying growth pockets and mitigating risk.
Regional insights underscore the need for tailored strategies: leveraging advanced capabilities and regulatory compliance in Europe, scaling cost-effective production in Asia-Pacific, and maintaining service excellence across the Americas. Concurrently, leading companies deploy mergers, capacity expansions, and R&D to solve emerging challenges in performance, recyclability, and traceability. By adopting recommended actions-diversifying supply, integrating recycled content, digitalizing manufacturing, and fostering co-innovation-stakeholders can secure long-term resilience and profitability.
This section provides a structured overview of the report, outlining key chapters and topics covered for easy reference in our Rigid Plastic Tubing market comprehensive research report.
- Preface
- Research Methodology
- Executive Summary
- Market Overview
- Market Dynamics
- Market Insights
- Cumulative Impact of United States Tariffs 2025
- Rigid Plastic Tubing Market, by Material Type
- Rigid Plastic Tubing Market, by Application
- Rigid Plastic Tubing Market, by End-Use Industry
- Rigid Plastic Tubing Market, by Production Process
- Rigid Plastic Tubing Market, by Product Form
- Rigid Plastic Tubing Market, by Sales Channel
- Americas Rigid Plastic Tubing Market
- Asia-Pacific Rigid Plastic Tubing Market
- Europe, Middle East & Africa Rigid Plastic Tubing Market
- Competitive Landscape
- ResearchAI
- ResearchStatistics
- ResearchContacts
- ResearchArticles
- Appendix
- List of Figures [Total: 28]
- List of Tables [Total: 1072 ]
Call to Action: Connect with Ketan Rohom for the Complete Report
For comprehensive analysis and deeper insights into market segmentation, regional strategies, tariff impacts, and competitive positioning, contact Ketan Rohom (Associate Director, Sales & Marketing) to purchase the full market research report. His expertise will ensure you access tailored guidance to navigate the dynamic rigid plastic tubing landscape effectively.
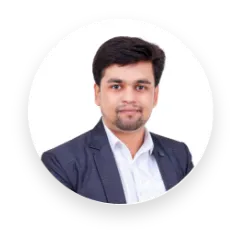
- When do I get the report?
- In what format does this report get delivered to me?
- How long has 360iResearch been around?
- What if I have a question about your reports?
- Can I share this report with my team?
- Can I use your research in my presentation?