The Robot Gears Market size was estimated at USD 141.39 million in 2024 and expected to reach USD 151.35 million in 2025, at a CAGR 6.71% to reach USD 208.88 million by 2030.

Navigating the Complex Terrain of Robot Gears
In an era defined by rapid automation and precision engineering, robot gears have emerged as critical enablers of next-generation machinery. From assembly lines that demand impeccable synchronization to aerospace systems that require flawless reliability under extreme conditions, these components underpin the performance and durability of complex robotic assemblies. As digital transformation intensifies, stakeholders across manufacturing, automotive, and energy sectors recognize the strategic value of advanced gearing solutions.
This executive summary distills the core drivers, emerging challenges, and competitive landscape shaping the robot gears market. We explore the technological breakthroughs that are redefining gear design, the regulatory and trade dynamics influencing supply chains, and the segmentation nuances that reveal high-potential niches. Our goal is to equip decision-makers with actionable intelligence, empowering them to identify growth pockets, optimize investments, and forge resilient supply networks.
By weaving together rigorous analysis and industry foresight, this document offers a clear view of the market’s evolution and the pathways to sustainable leadership. Whether you are a component supplier evaluating expansion strategies or an end user seeking robust turnkey solutions, the insights contained herein will illuminate the roadmap for success in the burgeoning robot gears arena.
Catalysts Propelling the Evolution of the Gear Market
The landscape of robot gears is undergoing transformative shifts propelled by a confluence of advanced materials, digitalization, and sustainability mandates. Recent advancements in additive manufacturing and high-precision machining have unlocked unprecedented design freedom, enabling intricate gear geometries that deliver higher torque density and reduced weight. Meanwhile, artificial intelligence–driven predictive maintenance platforms harness real-time sensor data to optimize gear performance, mitigate downtime risks, and extend service life.
Environmental regulations and corporate commitments to decarbonization are spurring the adoption of low-friction coatings and materials with enhanced wear resistance. These developments not only reduce energy consumption within gear assemblies but also minimize lubricant dependency, aligning gear suppliers with broader green manufacturing imperatives.
In parallel, collaborative robotics has broadened gear design requirements, demanding quieter operation and enhanced compliance. The integration of soft robotics technologies is fostering novel hybrid gearing systems that blend rigidity with controlled flexibility, unlocking new application domains across medical devices and precision handling tasks. Collectively, these transformative shifts are redefining the performance benchmarks and strategic imperatives for industry participants.
Assessing the Ripple Effects of 2025 US Tariffs
The imposition of revised United States tariffs in 2025 has introduced significant complexity into robot gear supply chains, compelling both domestic manufacturers and import-dependent users to recalibrate sourcing strategies. Tariff adjustments targeting specific imported gear categories have elevated acquisition costs, prompting a reexamination of supplier portfolios and cost structures.
In response, several U.S.-based producers have accelerated domestic capacity expansions, underpinned by incentives to localize high-precision machining and additive manufacturing capabilities. These investments not only mitigate tariff exposure but also enhance supply chain resilience amid geopolitical volatility. Concurrently, end users in automotive and aerospace sectors are negotiating strategic partnerships with regional manufacturers to secure preferential pricing and streamlined logistics.
Despite short-term cost pressures, the tariff landscape has catalyzed innovation as suppliers seek to differentiate through integrated value-added services such as on-site assembly support and digital maintenance platforms. By internalizing previously imported components and embedding advanced analytics within gear products, market participants are transforming a regulatory challenge into an opportunity for competitive advantage.
Unearthing Deep-Dive Insights Across Market Segments
A nuanced understanding of market segmentation reveals the diverse dynamics shaping demand across product configurations, end-use industries, materials, manufacturing techniques, and channels. When examined by product type, bevel gears account for specialized angular power transmission needs while helical gears dominate applications requiring smooth, quiet operation. Planetary gear assemblies have emerged as the solution of choice for high-torque, compact robotic systems, whereas spur gears continue to serve cost-sensitive mass-production contexts. Worm gears find their niche in scenarios demanding precise speed reduction with self-locking capability.
Shifting focus to end-user industries, aerospace demands aerospace-grade alloys and stringent quality protocols, while automotive applications bifurcate into commercial vehicles requiring heavy-duty gearing and passenger cars that prioritize weight optimization and NVH reduction. Industrial machinery markets include compressors, where efficiency gains drive gear design, gearboxes that underpin power transmission across sectors, and pumps that call for corrosion-resistant gearing solutions. The oil & gas sector, meanwhile, emphasizes durability under harsh conditions and regulatory compliance.
Material preferences further differentiate the landscape. Alloy steels-split between chrome and nickel variants-offer superior strength and fatigue resistance. Bronze remains indispensable for low-friction applications, carbon steels provide a cost-effective balance between performance and economy with high and low carbon options, and stainless steel addresses corrosion concerns in demanding environments.
Manufacturing processes also shape competitive positioning. Casting permits complex geometries at scale, forging delivers high structural integrity, machining achieves tight tolerances, and powder metallurgy enables near-net-shape production with minimal waste. Finally, distribution channels influence market reach: direct sales foster collaboration on custom solutions, distributors enable broad product availability, and online retail drives accessibility for smaller end users.
Together, these segmentation lenses illuminate pockets of robust growth potential, evolving performance requirements, and strategic entry points for both established players and new entrants seeking differentiated positioning.
This comprehensive research report categorizes the Robot Gears market into clearly defined segments, providing a detailed analysis of emerging trends and precise revenue forecasts to support strategic decision-making.
- Product Type
- End User Industry
- Material Type
- Manufacturing Process
- Distribution Channel
Decoding Regional Dynamics Shaping Global Demand
Regional dynamics play a pivotal role in charting the trajectory of the robot gears market, with each geographic cluster exhibiting distinct growth catalysts. In the Americas, robust automotive manufacturing hubs and a commitment to reshoring critical components have fueled investment in advanced gear production facilities. The region’s emphasis on nearshore sourcing and well-established aerospace supply chains underpin sustained demand for high-precision and heavy-duty gearing solutions.
Across Europe, the Middle East, and Africa, stringent emissions targets and an accelerating shift toward smart factories are major demand drivers. Germany’s advanced automation landscape has propelled innovation in quiet, high-efficiency gear systems, while the United Kingdom and France focus on aerospace-grade developments. The Middle East, buoyed by diversification strategies away from oil, shows growing interest in industrial machinery applications, and select African economies are investing in localized manufacturing capabilities to support infrastructure development.
In Asia-Pacific, the intersection of cost competitiveness and rapid industrialization has created a dynamic environment for gear manufacturers. China’s large-scale automotive production and expanding robotics sector demand a vast array of gear solutions, from cost-effective spur designs to sophisticated planetary systems. Japan’s enduring leadership in precision engineering continues to set benchmarks for gear quality, while emerging markets such as India and Southeast Asia offer new growth frontiers driven by infrastructure expansion and automation uptake.
This comprehensive research report examines key regions that drive the evolution of the Robot Gears market, offering deep insights into regional trends, growth factors, and industry developments that are influencing market performance.
- Americas
- Europe, Middle East & Africa
- Asia-Pacific
Profiling Leading Innovators Steering the Industry
Industry leaders are strategically differentiating through technology portfolios, global footprint, and collaborative ecosystems. Key players emphasize integrated service offerings that span custom design, end-to-end manufacturing, and digital maintenance platforms. Investments in research and development are heavily skewed toward materials science, additive manufacturing, and embedded sensor solutions that enable real-time performance monitoring.
Several companies have pursued joint ventures and partnerships to penetrate high-growth segments, leveraging local expertise to navigate regulatory landscapes and tailor products to regional specifications. Licensing agreements for proprietary gear coatings and lubrication technologies have emerged as critical enablers of ID growth in high-demand sectors such as aerospace and energy.
Supply chain diversification remains a top priority. Leading suppliers have established dual production hubs across continents, ensuring business continuity amid trade uncertainties. They also integrate vertically by acquiring specialized machining shops, forging facilities, and surface treatment providers, thereby streamlining quality control and reducing lead times.
In the distribution domain, top-tier firms are optimizing omnichannel strategies, blending direct sales teams for large OEM partnerships with digital platforms that cater to aftermarket and small-to-medium enterprise customers. This duality enhances market responsiveness while preserving the agility to adapt to evolving customer requirements.
This comprehensive research report delivers an in-depth overview of the principal market players in the Robot Gears market, evaluating their market share, strategic initiatives, and competitive positioning to illuminate the factors shaping the competitive landscape.
- Harmonic Drive Systems Inc.
- Nabtesco Corporation
- Sumitomo Heavy Industries, Ltd.
- WITTENSTEIN SE
- Neugart GmbH
- SEW-EURODRIVE GmbH & Co KG
- Bonfiglioli Riduttori S.p.A.
- Parker Hannifin Corporation
- Bosch Rexroth AG
- Oriental Motor Co., Ltd.
Strategic Roadmap for Sustained Market Leadership
To thrive amid intensifying competition and shifting trade dynamics, industry leaders must adopt a multi-faceted strategic approach. First, prioritizing collaborative research initiatives with materials science institutes and automation laboratories will accelerate the development of next-generation high-strength, lightweight gear alloys. Embedding sensor arrays directly into gear surfaces will enable predictive maintenance solutions that reduce operational downtime and improve total cost of ownership for end users.
Second, diversifying manufacturing footprints through a blend of localized micro-factories and scalable centralized hubs will balance cost efficiency with supply chain resilience. These micro-factories should focus on high-mix, low-volume specialized gears, while centralized facilities drive economies of scale for standard products.
Third, forging strategic partnerships with digital platform providers will create seamless integration between hardware and software, offering end-to-end lifecycle management solutions. A subscription-based service model for maintenance analytics can establish recurring revenue streams and deepen customer relationships.
Finally, cultivating an agile organizational culture that embraces continuous improvement, cross-functional teamwork, and rapid prototyping methodologies will empower companies to respond swiftly to emerging opportunities. By aligning talent development programs with technological roadmaps, leaders can ensure sustained innovation and long-term competitiveness.
Rigorous Framework Underpinning Our Analytical Approach
Our analysis combines primary interviews with senior executives, technical experts, and end users alongside secondary research covering peer-reviewed journals, industry publications, and regulatory filings. We employ a triangulated data validation approach in which insights from field interviews are cross-referenced against publicly available financial disclosures and patent databases.
In addition, proprietary algorithms filter through trade data to identify shifting import-export patterns, while sentiment analysis of technical forums and conference proceedings highlights emergent themes in gear design and manufacturing. This mixed-method framework ensures a comprehensive perspective on both quantitative metrics and qualitative trends.
To delineate segmentation nuances, we leverage a scenario-based modeling technique that evaluates performance, cost, and adoption factors across distinct product types, material categories, and end-use applications. Geographic analyses integrate macroeconomic indicators, infrastructure investment plans, and regional trade agreements to contextualize demand trajectories.
Rigorous peer-review checkpoints and validation workshops with domain specialists further fortify the credibility of our findings. Throughout the process, adherence to established research ethics and data integrity standards underpins the reliability and actionable value of the resulting insights.
Explore AI-driven insights for the Robot Gears market with ResearchAI on our online platform, providing deeper, data-backed market analysis.
Ask ResearchAI anything
World's First Innovative Al for Market Research
Synthesizing Key Takeaways for Informed Decision-Making
The insights presented underscore the critical inflection points shaping the robot gears market, from technological breakthroughs in materials and manufacturing to the strategic responses necessitated by shifting trade policies. High-precision industries such as aerospace and automotive will continue to demand tailored solutions, while emerging applications in medical robotics and renewable energy systems open new frontiers for gear innovation.
A clearly articulated segmentation strategy reveals where value creation potential is greatest, and regional analyses highlight the importance of adaptive supply chains and localized capabilities. Competitive profiling underscores the need for integrated platform solutions, as market leadership increasingly hinges on seamless hardware-software convergence.
For decision-makers, the path forward involves balancing near-term operational resilience with long-term investment in research, digitalization, and collaborative ecosystems. By embracing these imperatives, stakeholders can transform regulatory challenges into strategic advantages and position themselves at the forefront of the evolving robot gears landscape.
This conclusion serves as both a synthesis of key findings and a catalyst for informed action, guiding stakeholders toward sustainable growth and continued innovation.
This section provides a structured overview of the report, outlining key chapters and topics covered for easy reference in our Robot Gears market comprehensive research report.
- Preface
- Research Methodology
- Executive Summary
- Market Overview
- Market Dynamics
- Market Insights
- Cumulative Impact of United States Tariffs 2025
- Robot Gears Market, by Product Type
- Robot Gears Market, by End User Industry
- Robot Gears Market, by Material Type
- Robot Gears Market, by Manufacturing Process
- Robot Gears Market, by Distribution Channel
- Americas Robot Gears Market
- Europe, Middle East & Africa Robot Gears Market
- Asia-Pacific Robot Gears Market
- Competitive Landscape
- ResearchAI
- ResearchStatistics
- ResearchContacts
- ResearchArticles
- Appendix
- List of Figures [Total: 26]
- List of Tables [Total: 418 ]
Secure Your Comprehensive Robot Gears Market Report Today
Embark on a journey toward market mastery by securing the definitive Robot Gears Market Research Report. Connect directly with Ketan Rohom, Associate Director of Sales & Marketing, to unlock tailored insights that will propel your strategic initiatives forward and ensure your organization stays ahead of emerging trends.
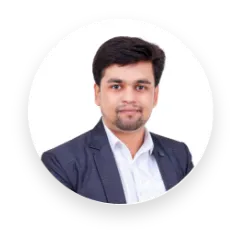
- How big is the Robot Gears Market?
- What is the Robot Gears Market growth?
- When do I get the report?
- In what format does this report get delivered to me?
- How long has 360iResearch been around?
- What if I have a question about your reports?
- Can I share this report with my team?
- Can I use your research in my presentation?