The Robotic Polishing System Market size was estimated at USD 256.08 million in 2024 and expected to reach USD 289.45 million in 2025, at a CAGR 13.33% to reach USD 542.80 million by 2030.

Unveiling the dynamic evolution and strategic significance of robotic polishing systems reshaping manufacturing precision and operational efficiency at scale
The robotic polishing system has emerged as an indispensable innovation reshaping high-precision manufacturing across diverse industries. At its core, this technology automates surface finishing processes that were once labor-intensive and inconsistent when performed manually. By integrating force-feedback sensors, advanced motion control, and adaptive tooling, modern robotic polishing solutions deliver uniform surface textures and mirror-grade finishes while substantially reducing defect rates and rework. Manufacturers transitioning from manual buffing to robotic polishing report up to a 40% increase in throughput alongside a 50% reduction in quality deviations, underscoring the system’s potential to elevate both efficiency and product excellence.
In recent years, the trajectory of robotic polishing has been fueled by advancements in 3D vision, artificial intelligence, and path-optimization techniques. High-resolution depth cameras now guide polishing arms in real time, enabling robots to tailor movement paths dynamically for each workpiece. Coupled with machine learning algorithms, these systems continually refine tool trajectories, predicting wear patterns and adjusting process parameters to minimize cycle times and material waste. This convergence of AI, vision, and sensor fusion is driving a new era of adaptive polishing that operates with unprecedented precision and repeatability.
As manufacturers contend with evolving product complexities, the robotic polishing system has proven especially valuable for handling intricate geometries. Industries such as aerospace, automotive, and medical devices demand micron-level surface tolerances on components ranging from turbine blades to orthopedic implants. Robotic polishing solutions meet these stringent requirements by delivering consistent force application and automated sensor-driven quality checks that guard against surface anomalies. Consequently, decision-makers are increasingly viewing automated polishing as a critical enabler for maintaining regulatory compliance, reducing cycle-time variability, and mitigating labor-related quality risks.
Exploring the sweeping technological breakthroughs and market shifts propelling robotic polishing systems into a new era of adaptability and precision
The landscape of robotic polishing is undergoing transformative shifts driven by rapid breakthroughs in automation and digitalization. One of the most notable changes is the transition from fixed-function polishing cells to modular, reconfigurable workstations. Manufacturers now deploy compact polishing units that can be easily relocated and repurposed for different tasks, enabling agile production lines capable of handling varied batch sizes. This trend toward flexible automation responds directly to market demands for customized products and tighter delivery schedules, positioning robotic polishing as a key contributor to smart, adaptive manufacturing ecosystems.
Equally significant is the rise of collaborative robot (cobot) integration in surface finishing applications. Cobots equipped with advanced force-torque sensors operate safely alongside human operators, combining robotic endurance and precision with human judgment for complex polishing tasks. This human-robot collaboration not only accelerates deployment cycles but also broadens access to automated polishing for small and medium-sized enterprises that may lack dedicated robotic programming expertise. By reducing the barriers to entry, cobots are democratizing high-precision finishing across a wider range of manufacturers.
Furthermore, the infusion of digital twins and simulation tools has revolutionized process planning for robotic polishing. Virtual replicas of robotic cells allow engineers to optimize tool paths, test new polishing strategies, and predict maintenance requirements in a simulated environment before executing on the shop floor. This simulation-driven approach minimizes trial-and-error, shortens commissioning times, and reduces downtime. When combined with cloud-based analytics, manufacturers can harness aggregated performance data to benchmark process improvements across global facilities, accelerating continuous innovation in polishing operations.
Finally, ongoing improvements in AI-driven quality inspection are redefining end-to-end polishing workflows. Automated vision systems now inspect each polished surface in real time, detecting minute defects and triggering corrective actions within the same cycle. This closed-loop quality control reduces reliance on manual inspection, lowers scrap rates, and ensures that finished components meet exacting industry standards. As a result, robotic polishing is cementing its role as an integral pillar of modern, data-driven manufacturing.
Analyzing the far-reaching consequences of the 2025 United States tariff measures on robotic polishing supply chains and manufacturer economics
Throughout 2025, the United States has maintained Section 301 tariff measures on Chinese-origin machinery, directly impacting robotic polishing systems classified under HTSUS chapters 84 and 85. These tariffs impose additional duties of up to 25% on imported industrial robots and ancillary equipment, effectively raising procurement costs for manufacturers reliant on Chinese-sourced components and complete robotic cells. Firms importing such systems between October 15, 2024, and March 31, 2025, could petition the USTR for exclusions; granted exemptions apply through May 31, 2025, providing a temporary reprieve from tariff burdens.
As a consequence of elevated duties, many manufacturers hesitated to finalize new automation projects amid heightened economic uncertainty. Small and medium-sized enterprises, in particular, found their capital expenditures constrained, delaying or scaling back robotic polishing integrations due to the increased cost of critical subcomponents. Additionally, the unpredictability of potential tariff extensions has complicated long-range planning for global operations and prompted stakeholders to reassess supply chain risk profiles.
Recognizing these challenges, some companies have strategically pursued tariff exclusion requests for specialized machinery categories. The exclusion process, open until March 31, 2025, has seen a surge of applications from manufacturers eager to mitigate a 25% duty on polishing robots, force sensors, and vision modules. While the rolling review mechanism offers short-term relief, enterprises must file early to maximize the benefit window, as approved exclusions expire on May 31, 2025.
In parallel, the tariff environment has accelerated a strategic pivot toward diversified sourcing and domestic production. Industry leaders are expanding investments in U.S.-based automation facilities and collaborating with local integrators to develop regionally manufactured polishing cells. This reshoring trend not only reduces exposure to tariff volatility but also strengthens supply chain resilience by shortening lead times and minimizing cross-border logistics risks. Several firms view this domestic shift as a long-term opportunity to drive higher automation adoption while shielding critical manufacturing from geopolitical headwinds.
Highlighting critical segmentation insights that uncover how module selection payload capacity and end-user application drive robotic polishing adoption
The segmentation of the robotic polishing market reveals distinct module categories, covering buffing, grinding, and polishing units, each designed to address specific surface finishing requirements and create tailored process flows. Within these modules, manufacturers must evaluate the nuanced capabilities and performance metrics of each type to align system design with their component geometries and material profiles.
Robot types further define competitive dynamics, spanning articulated arms, Cartesian configurations, and SCARA platforms. Articulated robots dominate in multi-axis flexibility for complex part contours, while Cartesian models excel in linear polishing paths due to their rigidity and ease of programming. SCARA robots offer a compelling blend of speed and precision for high-throughput planar polishing tasks, underscoring the importance of matching robot architecture with production speed targets and footprint constraints.
Payload capacity represents another critical layer of segmentation, with robots supporting less than 5 kg payloads catering to lightweight jewelry and electronics applications, 5–10 kg and 10–20 kg ranges addressing general industrial parts, and more than 20 kg platforms suitable for heavy‐duty aerospace and energy components. Selecting the correct payload class ensures optimal cycle stability and tool life under varying abrasive loads, influencing maintenance schedules and energy consumption considerations.
End-user sectors illustrate where robotic polishing deployment is most concentrated. Aerospace and defense demand precision polishing on high-value alloy components; automotive manufacturers leverage automated systems for high-volume wheel and trim finishing; construction and architecture firms adopt buffing modules for metal cladding; electronics and semiconductor producers require contamination-controlled polishing for connectors; and medical device companies enforce stringent surface integrity for implants. Understanding each sector’s regulatory and quality imperatives drives targeted solution development.
Finally, distribution channels-direct sales versus authorized distributors-shape customer engagement and aftermarket support. Direct manufacturer engagement often yields customized integration packages and end-to-end project management, while distributor networks offer local expertise, rapid spare parts fulfillment, and flexible financing models. Companies calibrate channel strategies to balance global reach with responsive service and minimize total cost of ownership over the equipment lifecycle.
This comprehensive research report categorizes the Robotic Polishing System market into clearly defined segments, providing a detailed analysis of emerging trends and precise revenue forecasts to support strategic decision-making.
- Module
- Robot Type
- Payload Capacity
- End-user
- Distribution Channel
Examining regional performance dynamics in the Americas EMEA and Asia-Pacific and their influence on robotic polishing deployment and service models
Regional dynamics shape the adoption trajectory of robotic polishing systems around the world. In the Americas, robust investments from the automotive and aerospace industries anchor demand, with U.S. manufacturers prioritizing advanced finishing for alloy wheel and turbine blade applications. The reshoring initiatives incentivized by government policies and workforce constraints are catalyzing onshore automation, as automotive OEMs and tier-one suppliers deploy flexible robotic cells to navigate mixed production lines and labor availability.
Across Europe, the Middle East, and Africa, established automotive OEMs and precision engineering firms continue to lead installations of multi-axis robotic polishing solutions. European automakers leverage stringent quality regulations and environmental mandates to justify automation spending, while medical device manufacturers in the region accelerate compliance-driven investments to maintain surface integrity standards. Additionally, the EMEA market benefits from strong service networks and robotics integration hubs that support rapid deployment and ongoing technical support, reinforcing the region’s leadership in precision finishing.
Asia-Pacific remains the fastest-growing region for robotic polishing adoption, driven by rapid industrialization in China, Japan, and South Korea. Electronics manufacturers are automating small-parts polishing at scale, while aerospace and energy sectors in India and Southeast Asia explore modular polishing platforms for export-oriented supply chains. According to the International Federation of Robotics, China accounted for 51% of new industrial robot installations worldwide in 2023, reflecting the region’s appetite for automation amid labor shortages and cost pressures.
This comprehensive research report examines key regions that drive the evolution of the Robotic Polishing System market, offering deep insights into regional trends, growth factors, and industry developments that are influencing market performance.
- Americas
- Europe, Middle East & Africa
- Asia-Pacific
Profiling leading innovators and competitive strategies of top-tier companies transforming robotic polishing technology integration and service excellence
Major industry players continue to define the competitive landscape and drive innovation in robotic polishing solutions. ABB has introduced new robot families optimized for polishing applications within its China-focused Lite+ and PoWa lines, emphasizing out-of-the-box usability and voice-driven programming. These robots can be operational within an hour and feature payload ranges suitable for electronics and metal finishing, underlining ABB’s commitment to mid-market customer accessibility and advanced sensor integration.
FANUC remains at the forefront with its dedicated robotic polishing platforms as outlined on its solutions webpage. The company offers customizable end-of-arm tooling and thermal compensation features for consistent finish quality. FANUC’s polishing robots integrate seamlessly with its ROBOGUIDE simulation software, enabling virtual commissioning and rapid process validation that minimize downtime and maximize throughput.
Yaskawa Electric Corporation has strategically invested $180 million in a new Wisconsin hub to localize robotic production and mitigate tariff exposure. This facility will integrate automation cell assembly, training, and R&D under one roof, streamlining delivery timelines for North American customers and enhancing service responsiveness. The move reflects Yaskawa’s focus on regional diversification and supply chain resilience amid evolving trade policies.
KUKA continues to navigate competitive pressures by expanding collaborative robot offerings and strengthening its global footprint. Despite stiff competition from Chinese suppliers, KUKA’s six-axis LBR series and strategic emphasis on autonomous mobile robots underscore its dedication to flexible, human-robot collaborative applications. The German-controlled brand leverages its engineering heritage to address high-precision requirements in aerospace and automotive finishing, positioning itself as a partner for complex polishing challenges.
This comprehensive research report delivers an in-depth overview of the principal market players in the Robotic Polishing System market, evaluating their market share, strategic initiatives, and competitive positioning to illuminate the factors shaping the competitive landscape.
- ABB Ltd.
- Acme Manufacturing
- Cohesive Robotics Inc.
- FANUC Corporation
- Grindmaster Pvt. Ltd
- Heinz Berger Maschinenfabrik GmbH & Co. KG
- Kingstone Robotics
- KUKA AG
- Nachi-Fujikoshi
- PushCorp, Inc.
- STRECON A/S
- Universal Robots
- VN Machines Pvt Ltd.
- Yamaha Fine Technologies Co., Ltd.
- Yaskawa Electric Corporation
- AV&R
- Tespa India Pvt Ltd.
- Mirka Ltd by KWH Group
- Changzhou Anchuang Intelligent Equipment Co., Ltd
- Mitsubishi Electric Corporation
Delivering actionable recommendations to empower industry leaders in optimizing robotic polishing investments processes and collaborative innovation pathways
To fully harness the potential of robotic polishing systems, industry leaders should prioritize a clear automation roadmap that aligns with strategic business objectives. Leaders must begin by conducting detailed process audits to identify high-impact polishing tasks, quantifying current cycle times, defect rates, and labor dependencies. From there, targeted pilot deployments at select workstations can validate performance metrics, enabling iterative scaling across production lines.
In parallel, executives should foster cross-functional collaboration between automation engineers, quality assurance teams, and supply chain stakeholders. Establishing a governance structure that includes regular performance reviews and risk assessments ensures that tariff considerations, maintenance logistics, and workforce training are proactively managed. This collaborative governance model promotes transparent decision-making and continuous improvement in polishing operations.
Investing in workforce upskilling is equally vital; robotics integrators should implement comprehensive training programs covering cobot programming, sensor calibration, and preventive maintenance practices. Empowering technicians with hands-on expertise accelerates automated polishing adoption while reducing reliance on external service providers. Furthermore, leveraging digital twin environments for virtual training can reinforce best practices without disrupting live production.
Finally, organizations should explore strategic partnerships with system integrators and original equipment manufacturers to co-develop specialized end-of-arm tooling and adaptive software modules. By cultivating an innovation ecosystem, leaders can stay ahead of emerging polishing requirements, enabling rapid adaptation to new materials and tighter finish tolerances. This proactive collaboration fosters long-term resilience and positions companies to capitalize on evolving market opportunities.
Outlining rigorous research methodology blending primary and secondary insights with triangulation for comprehensive analysis validity and strategic depth
The research methodology underpinning this analysis combined rigorous primary and secondary approaches to ensure comprehensive coverage and analytical validity. Primary insights were gathered through interviews with automation engineers, maintenance specialists, and procurement managers at leading manufacturing firms. These discussions provided real-world perspectives on system performance, integration challenges, and total cost considerations.
Secondary research incorporated a diverse range of credible sources, including industry-agnostic news outlets, technical whitepapers, and trade association data. Regulatory filings and USTR publications informed the assessment of tariff measures and exclusion processes. Corporate press releases and reputable robotics association reports supplemented the technology trend analysis, ensuring up-to-date coverage of sensor innovations, AI adoption, and collaborative robot developments.
Triangulation techniques were applied to validate findings across multiple data points, cross-referencing interview insights with publicly available market intelligence and independent studies. This multi-source verification approach strengthens the reliability of key observations and mitigates potential biases. Additionally, scenario mapping was utilized to model the impacts of tariff fluctuations, supply chain shifts, and emerging technology adoption rates on robotic polishing deployment.
Finally, iterative peer reviews and expert consultations were conducted to refine conclusions and recommendations. Feedback loops with subject matter experts and early-access report readers ensured that the final analysis balances technical depth with actionable relevance for decision-makers.
Explore AI-driven insights for the Robotic Polishing System market with ResearchAI on our online platform, providing deeper, data-backed market analysis.
Ask ResearchAI anything
World's First Innovative Al for Market Research
Synthesis of critical findings underscoring the transformative potential of robotic polishing systems for driving operational excellence and competitive advantage
In summary, robotic polishing systems have progressed from niche experimental cells to foundational components of modern manufacturing. The integration of advanced sensors, artificial intelligence, and collaborative robotics has expanded the technology’s applicability across sectors requiring high-precision surface finishes. Concurrently, the 2025 U.S. tariff environment has underscored the importance of supply chain agility, driving both temporary exclusion requests and long-term reshoring initiatives.
Segment-level analysis highlights how module selection, robot architecture, payload capacity, and end-user demands converge to shape system configurations. Regional insights reveal distinct market drivers, from the Americas’ reshoring momentum to EMEA’s service network strengths and Asia-Pacific’s rapid electronics and automotive automation growth. Major companies, including ABB, FANUC, Yaskawa, and KUKA, continue to innovate through local manufacturing investments, AI-enhanced solutions, and flexible deployment models.
As organizations plan their next wave of automation, a structured approach encompassing process audits, cross-functional governance, workforce upskilling, and partner collaboration will be essential. Through a robust research methodology underpinned by primary interviews and secondary data triangulation, this report delivers a holistic perspective on the strategic, operational, and technological imperatives shaping robotic polishing’s future.
Ultimately, this synthesis underscores that operators who embrace data-driven execution, resilient supply chains, and continuous innovation will capture the full value of robotic polishing, driving sustainable performance gains and maintaining competitive advantage in an increasingly automated world.
This section provides a structured overview of the report, outlining key chapters and topics covered for easy reference in our Robotic Polishing System market comprehensive research report.
- Preface
- Research Methodology
- Executive Summary
- Market Overview
- Market Dynamics
- Market Insights
- Cumulative Impact of United States Tariffs 2025
- Robotic Polishing System Market, by Module
- Robotic Polishing System Market, by Robot Type
- Robotic Polishing System Market, by Payload Capacity
- Robotic Polishing System Market, by End-user
- Robotic Polishing System Market, by Distribution Channel
- Americas Robotic Polishing System Market
- Europe, Middle East & Africa Robotic Polishing System Market
- Asia-Pacific Robotic Polishing System Market
- Competitive Landscape
- ResearchAI
- ResearchStatistics
- ResearchContacts
- ResearchArticles
- Appendix
- List of Figures [Total: 28]
- List of Tables [Total: 472 ]
Engage with Associate Director Ketan Rohom to secure your comprehensive research report and accelerate strategic decision making in robotic polishing initiatives
I invite you to connect with Associate Director, Sales & Marketing, Ketan Rohom, to gain exclusive access to our in-depth market research report on robotic polishing systems. This comprehensive resource provides the critical insights and strategic context you need to navigate the evolving landscape of automation with confidence. Reach out to Ketan to unlock tailored guidance, discuss how the findings align with your organization’s priorities, and secure a copy of the report that will empower your next-generation investment and operational decisions.
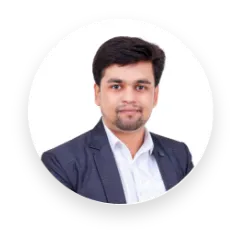
- How big is the Robotic Polishing System Market?
- What is the Robotic Polishing System Market growth?
- When do I get the report?
- In what format does this report get delivered to me?
- How long has 360iResearch been around?
- What if I have a question about your reports?
- Can I share this report with my team?
- Can I use your research in my presentation?