Introduction: The Evolution of Robotic Soldering in Modern Manufacturing
Robotic soldering machines have emerged as a cornerstone of precision assembly in electronics manufacturing, bridging the gap between manual craftsmanship and fully automated production. These systems integrate advanced robotics, vision technology, and intelligent control algorithms to deliver consistent solder joints at unprecedented speeds. As demand for miniaturized components and high-reliability assemblies grows across automotive, aerospace, medical devices, and consumer electronics sectors, the ability to maintain quality while scaling output becomes critical. Recent improvements in motion control, thermal profiling, and joint inspection have elevated these machines from niche tools to strategic assets. In parallel, mounting pressure to reduce labor costs and mitigate human error has accelerated adoption of fully robotic platforms alongside semi-automated and manual-assisted systems. This executive summary offers decision-makers a comprehensive overview of the current landscape, highlighting key market shifts, tariff influences, segmentation dynamics, regional trends, and competitive forces. It equips industry leaders with actionable insights to optimize capital investments, refine technology roadmaps, and align with evolving regulatory environments. Through a detailed examination of segmentation by machine variant, technology integration, soldering techniques, component applications, production capacity, end-use industries, and handling efficiency, this document reveals where opportunities converge and where strategic focus will drive the greatest returns.
Transformative Shifts Redefining the Robotic Soldering Landscape
The last decade has witnessed transformative shifts that are redefining what robotic soldering can achieve. Manufacturers are migrating from standalone soldering stations to integrated cells where automated soldering systems communicate seamlessly with upstream and downstream processes. Artificial intelligence–driven path planning now optimizes weld trajectories in real time, while vision system integration ensures each joint meets exacting tolerances. Cloud-connected operations and IoT-enabled monitoring feed predictive analytics engines that anticipate maintenance needs, reducing unplanned downtime. Machine learning algorithms continuously refine parameter settings to accommodate new component geometries, further shortening setup times. At the same time, the push for sustainability has fueled development of energy-efficient heating modules and reduced waste through precise solder paste deposition. Globally, supply chain resilience has become a strategic priority, prompting OEMs to favor equipment with modular architectures that can be reconfigured rapidly for shifting production volumes and emerging applications. Together, these shifts are elevating robotic soldering from a cost-savings tool into a critical enabler of agile, high-throughput manufacturing ecosystems.
Assessing the 2025 United States Tariffs and Their Cumulative Impact
The implementation of new United States tariffs in 2025, targeting key components including precision robotic arms and specialized soldering modules, has introduced additional cost pressures across the supply chain. Import duties ranging from modest levies on electronic vision systems to higher rates on fully assembled automated soldering units have prompted many OEMs and contract manufacturers to reassess sourcing strategies. Some Tier-1 suppliers have accelerated plans to relocate assembly lines closer to final markets, while others are negotiating longer-term contracts to lock in pricing before further adjustments. The tariffs have also spurred interest in domestic production of advanced soldering equipment, with local manufacturers ramping up capacity to meet demand. Although increased duties initially elevated capital expenditure by an estimated low-to-mid single-digit percentage, many adopters report that the long-term benefits of a more resilient, geographically diversified supply base outweigh short-term cost increases. Furthermore, negotiations at the bilateral level suggest future relief on select categories, making it imperative for industry leaders to monitor trade developments and adapt procurement schedules accordingly.
Key Segmentation Insights: Unpacking Market Categories and Drivers
Understanding how the market segments by machine variant reveals that automated soldering systems commanding robotic arm integration and vision system integration modules drive the highest level of innovation, while manual-assisted alternatives continue to serve niche applications where operator flexibility is paramount. Semi-automated systems bridge the gap, offering programmable repeatability without the footprint of a full robotic cell. From a technology integration standpoint, AI-driven platforms accelerate decision-making on solder joint parameters, cloud-connected operations facilitate centralized process management, IoT-enabled monitoring delivers predictive maintenance and real-time analytics for continuous uptime, and machine learning optimization refines cycle times and quality yields. In terms of soldering techniques, hotbar and reflow soldering remain staples for high-volume PCB assembly, selective soldering expands reach into mixed-component boards with its automated selective soldering variant, and wave soldering preserves its foothold for through-hole applications. Component application segmentation highlights growth in automotive electronics assemblies requiring precise thermal profiles, consumer electronics manufacturing evolving across portable devices and stationary devices, industrial control electronics with stringent reliability demands, and medical device electronics that mandate comprehensive traceability. Production volume capacity considerations favor high-volume production lines-both batch production lines and continuous production lines-for large-scale consumer and automotive work, while medium and low volume production address prototyping and specialized runs. End-use industry analysis underscores aerospace and automotive sectors’ rigorous quality standards, consumer goods deployments in home appliances and mobile devices driving rapid throughput, healthcare’s insistence on regulatory compliance, and industrial machinery’s demand for robust equipment. Finally, material handling efficiency, whether realized through conveyor-integrated systems or robotic pick and place under the automated material handling umbrella or through semi-automated handling, shapes end-to-end cycle times and floor-space requirements.
This comprehensive research report categorizes the Robotic Soldering Machines market into clearly defined segments, providing a detailed analysis of emerging trends and precise revenue forecasts to support strategic decision-making.
- Soldering Machine Variant
- Technology Integration Approach
- Soldering Technique Type
- Component Application
- Production Volume Capacity
- End Use Industry
- Material Handling Efficiency
Key Regional Insights: Geographies Shaping the Market Trajectory
Regionally, the Americas lead with robust demand in automotive hubs and medical device clusters, where sodium-free solder alloys and inline inspection capabilities are rapidly adopted. In North America, contract manufacturers anchor expansion around flexible manufacturing cells that integrate multi-axis robots with advanced thermal profiling. Europe, Middle East & Africa presents a diverse regulatory landscape: EU directives on electronic waste and stringent safety certifications in the Middle East drive investments in closed-loop quality control, while African markets explore lower-cost semi-automated solutions for localized assembly. Asia-Pacific remains the world’s largest adopter, with China’s consumer electronics giants, Japan’s precision-engineering heritage, South Korea’s memory chip fabricators, and rapidly growing Southeast Asian hubs each embracing different aspects of automation-from cost-effective entry-level systems to industry-leading AI-enhanced soldering cells.
This comprehensive research report examines key regions that drive the evolution of the Robotic Soldering Machines market, offering deep insights into regional trends, growth factors, and industry developments that are influencing market performance.
- Americas
- Asia-Pacific
- Europe, Middle East & Africa
Competitive Landscape: Leading Players Driving Innovation
The competitive landscape features established industrial robotics leaders alongside specialized automation innovators. ABB Ltd. leverages cross-platform integration from motion control to analytics, while Adept Technology, Inc. and Automated Soldering Solutions LLC pioneer compact desktop systems for rapid prototyping environments. CyberSolder Robotics Inc. focuses on vision-guided alignment, and Denso Robotics Co., Ltd. excels in high-speed, clean-room compatible cells suited for medical electronics. Elite Soldering Machines Inc. and ERSA GmbH + Co. KG offer modular lines tailored for wave and selective soldering, and FANUC Corporation extends its field-proven robot arms with dedicated soldering end-effectors. Future Robotics Assembly, LLC and InnoSolder Automation, Ltd. integrate AI diagnostics, while JUKI Corporation and Kawasaki Heavy Industries, Ltd. emphasize global service networks. KUKA AG and MetroRobotics Corporation invest heavily in collaborative robot research, and Mitsubishi Electric Corporation delivers hybrid systems that merge heating and soldering functions. Murata Machinery, Ltd. and Nordson Corporation introduce low-thermal-stress modules, Omron Corporation and Panasonic Corporation refine multi-axis trajectory planners, and Precision Soldering Systems, Inc. drives cost-effective retrofit solutions. Robosolder Technologies, Inc. and Robotronix Inc. refine closed-loop quality feedback, Seiko Epson Corporation (Epson Robots) and Siemens AG bolster digital twin capabilities, and SolderBot Inc. and Stäubli Robotics emphasize handheld-style collaborative cells. TechSolder Systems, Inc., Toshiba Machine Co., Ltd., Universal Robots A/S, Yamaha Motor Co., Ltd., and Yaskawa Electric Corporation each advance open-architecture platforms that simplify third-party integrations and reduce total cost of ownership.
This comprehensive research report delivers an in-depth overview of the principal market players in the Robotic Soldering Machines market, evaluating their market share, strategic initiatives, and competitive positioning to illuminate the factors shaping the competitive landscape.
- ABB Ltd.
- Adept Technology, Inc.
- Automated Soldering Solutions LLC
- CyberSolder Robotics Inc.
- Denso Robotics Co., Ltd.
- Elite Soldering Machines Inc.
- ERSA GmbH + Co. KG
- FANUC Corporation
- Future Robotics Assembly, LLC
- InnoSolder Automation, Ltd.
- JUKI Corporation
- Kawasaki Heavy Industries, Ltd.
- KUKA AG
- MetroRobotics Corporation
- Mitsubishi Electric Corporation
- Murata Machinery, Ltd.
- Nordson Corporation
- Omron Corporation
- Panasonic Corporation
- Precision Soldering Systems, Inc.
- Robosolder Technologies, Inc.
- Robotronix Inc.
- Seiko Epson Corporation (Epson Robots)
- Siemens AG
- SolderBot Inc.
- Stäubli Robotics
- TechSolder Systems, Inc.
- Toshiba Machine Co., Ltd.
- Universal Robots A/S
- Yamaha Motor Co., Ltd.
- Yaskawa Electric Corporation
Actionable Recommendations for Industry Leaders to Maximize Opportunities
To capitalize on emerging opportunities, industry leaders should prioritize modular robotic platforms that permit rapid reconfiguration for diverse soldering techniques. Integrate AI-based analytics from day one to reduce setup iterations and unlock predictive quality control. Establish cloud-connected data pipelines to link process KPIs with enterprise resource planning systems, enabling holistic visibility across production lines. Diversify supplier networks to buffer against tariff fluctuations and localize critical component production where feasible. Invest in workforce training programs emphasizing robot programming and maintenance skills to bridge talent gaps and maximize equipment ROI. Collaborate with machine vision specialists to tailor inspection routines for unique solder alloys and joint geometries. Pursue energy-efficient heating elements and adaptive cycle management to align with corporate sustainability objectives. Finally, pilot collaborative cobot cells for low-volume, high-mix environments to achieve the agility demanded by evolving product lifecycles.
Explore AI-driven insights for the Robotic Soldering Machines market with ResearchAI on our online platform, providing deeper, data-backed market analysis.
Ask ResearchAI anything
World's First Innovative Al for Market Research
Conclusion: Navigating the Future of Robotic Soldering Industry
Robotic soldering technology stands at a pivotal juncture, where advanced automation converges with intelligent control to deliver unparalleled quality and throughput. By understanding the impact of new tariffs, embracing segmentation-specific strategies, and evaluating regional nuances, executives can make informed investment decisions. The competitive landscape underscores the necessity of selecting partners who bring not only robust hardware but also software ecosystems that scale with future process innovations. As sustainability and supply-chain resilience take center stage, companies that harmonize technology adoption with operational agility will secure leadership positions. The insights presented here equip decision-makers to navigate complexities, mitigate risks, and seize emerging growth corridors across end-use industries.
This section provides a structured overview of the report, outlining key chapters and topics covered for easy reference in our Robotic Soldering Machines market comprehensive research report.
- Preface
- Research Methodology
- Executive Summary
- Market Overview
- Market Dynamics
- Market Insights
- Cumulative Impact of United States Tariffs 2025
- Robotic Soldering Machines Market, by Soldering Machine Variant
- Robotic Soldering Machines Market, by Technology Integration Approach
- Robotic Soldering Machines Market, by Soldering Technique Type
- Robotic Soldering Machines Market, by Component Application
- Robotic Soldering Machines Market, by Production Volume Capacity
- Robotic Soldering Machines Market, by End Use Industry
- Robotic Soldering Machines Market, by Material Handling Efficiency
- Americas Robotic Soldering Machines Market
- Asia-Pacific Robotic Soldering Machines Market
- Europe, Middle East & Africa Robotic Soldering Machines Market
- Competitive Landscape
- ResearchAI
- ResearchStatistics
- ResearchContacts
- ResearchArticles
- Appendix
- List of Figures [Total: 30]
- List of Tables [Total: 637 ]
Call to Action: Secure Comprehensive Market Insights with Ketan Rohom
For a comprehensive analysis and to align your strategic plans with market realities, contact Ketan Rohom, Associate Director, Sales & Marketing. Reach out by email or phone to secure your copy of the full market research report and gain tailored insights that will drive your competitive advantage.
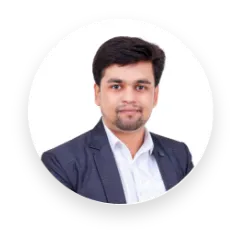
- When do I get the report?
- In what format does this report get delivered to me?
- How long has 360iResearch been around?
- What if I have a question about your reports?
- Can I share this report with my team?
- Can I use your research in my presentation?