Introduction to the Robotic Welding Arm Market
The convergence of precision engineering and automation has placed robotic welding arms at the forefront of modern manufacturing. As industries grapple with the dual pressures of rising labor costs and the demand for higher throughput, these sophisticated systems offer unparalleled consistency, speed, and quality. Beyond simple arc or spot welding, today’s robotic arms integrate advanced sensors, AI algorithms, and modular architectures that adapt to diverse materials and complex geometries. This executive summary delves into the critical developments reshaping the robotic welding arm market, examines external factors influencing adoption, and highlights strategic segmentation and regional trends. It aims to equip decision-makers with a clear understanding of the competitive landscape, emerging challenges, and key opportunities ahead.
Transformative Shifts Redefining the Robotic Welding Sector
Over the past decade, several seismic shifts have redefined how manufacturers approach welding operations. Rapid advances in laser and arc welding techniques have expanded the capabilities of robotic arms, enabling them to tackle both high-precision and heavy-duty tasks. AI-driven vision systems now guide welding trajectories in real time, reducing defects and minimizing rework. Meanwhile, the integration of the Internet of Things (IoT) has facilitated predictive maintenance, allowing operators to anticipate component wear and avoid costly downtime.
Transitioning from rigid, standalone units to highly flexible modular platforms, suppliers have responded to fluctuating production scales by offering customizable solutions that accommodate low, medium, and high-volume lines. The rise of sensor-driven feedback loops has further enhanced process control, ensuring repeatable weld quality even in demanding environments such as cleanrooms or outdoor facilities. Collectively, these developments are enabling manufacturers across aerospace, defense, automotive, energy, and shipbuilding to optimize throughput, reduce scrap rates, and accelerate time-to-market.
Cumulative Impact of US Tariffs in 2025 on Robotic Welding Arm Adoption
In 2025, newly imposed U.S. tariffs on imported robotic welding components and finished systems have triggered a notable ripple effect across supply chains. Manufacturers relying on overseas modules-especially those sourced from Asia-Pacific-face higher input costs, prompting many to reassess supplier contracts and explore domestic alternatives. Additionally, the steepening tariff curve has accelerated in-house manufacturing investments, as firms seek to insulate themselves from further duty escalations.
While some integrators have absorbed duties to maintain competitive pricing, others have renegotiated long-term agreements or adopted localization strategies, establishing final assembly lines on U.S. soil. This shift has fostered closer collaboration between system makers and Tier-1 OEMs, yet it has also introduced complexity in logistics, inventory management, and quality assurance. As a result, decision-makers must balance short-term cost pressures with long-term resilience, ensuring that tariff management aligns with broader operational objectives.
Key Insights from Market Segmentation
Insight into market segmentation reveals the nuanced drivers behind adoption patterns. Across aerospace and defense, the emphasis lies on high-precision laser and arc welding techniques tailored for exotic alloys and titanium welds. Automotive manufacturers, by contrast, gravitate toward gas metal arc welding and resistance spot welding for high-volume steel and aluminum chassis assembly. In energy and power generation, heavy machinery producers demand turnkey solutions that seamlessly integrate modular systems with IoT-enabled monitoring. Shipbuilding yards prioritize semi-automated arc welding modules capable of handling large sections in indoor and outdoor environments.
Production scale influences system choice: high-production lines favor fully automated setups with AI-assisted path planning, while low-volume shops leverage standalone units with manual override. Material type drives process selection, whether it involves welding steel, exotic alloys, or precision aluminum components. Similarly, integration models range from plug-and-play modular architectures to comprehensive turnkey systems, optimized for sensor-driven quality assurance. Technology integration, from IoT connectivity to sensor arrays, ensures real-time feedback across diverse application environments, including cleanroom settings for electronics assembly. Finally, innovation adoption and capital allocation shape purchasing decisions: early adopters invest in high-capital AI-assisted arms, whereas mainstream users balance moderate investment with proven semi-automated solutions.
This comprehensive research report categorizes the Robotic Welding Arm market into clearly defined segments, providing a detailed analysis of emerging trends and precise revenue forecasts to support strategic decision-making.
- Industry Application
- Welding Process
- Material Type
- Production Scale
- Integration Model
- Operational Mode
- Technology Integration
- Application Environment
- Innovation Adoption
- Scale Of Investment
Key Regional Dynamics Shaping the Robotic Welding Arm Market
Geographic dynamics play a pivotal role in shaping market trajectories. In the Americas, strong domestic manufacturing hubs in the U.S. and Mexico drive demand for high-production and turnkey welding solutions, with North American automakers and aerospace firms leading early adoption. Across Europe, Middle East & Africa, stringent quality standards and advanced regulatory frameworks have spurred uptake of sensor-driven and AI-assisted systems, particularly within Germany’s automotive sector and the U.K.’s offshore energy segment.
Asia-Pacific emerges as a high-growth arena, propelled by rapid industrialization in China, India, and Southeast Asia. Localized production scale ranges from low-volume precision workshops to sprawling heavy machinery plants, all seeking modular and IoT-enabled systems tailored to diverse environmental conditions. Regional incentives and investment in automation are accelerating the diffusion of fully automated and semi-automated arms across manufacturing clusters.
This comprehensive research report examines key regions that drive the evolution of the Robotic Welding Arm market, offering deep insights into regional trends, growth factors, and industry developments that are influencing market performance.
- Americas
- Asia-Pacific
- Europe, Middle East & Africa
Leading Companies Driving Innovation in Robotic Welding Arms
A constellation of global and niche players defines the competitive landscape. Established automation giants such as ABB Robotics AG, FANUC Robotics Corporation, KUKA Robotics GmbH, and Yaskawa Electric Corporation continue to set performance benchmarks, especially in high-precision industrial environments. Kawasaki Robotics Corporation and Mitsubishi Electric Automation Inc. maintain strong footholds in standardized manufacturing cells, while Universal Robots A/S and Staubli Robotics Ltd. pioneer collaborative, lightweight arms for flexible production lines.
Welding specialists like ESAB Corporation, Lincoln Electric Holdings, Inc., and Miller Electric Manufacturing Company extend their legacy through advanced robotic integrations, often in partnership with system integrators such as Comau S.p.A. and Precision Robotic Systems Inc. Emerging innovators-Fusion Robotics Inc., NextGen Welding Robotics LLC, and RoboWeld Solutions LLC-focus on AI-driven control and sensor fusion, targeting sectors that demand high accuracy on exotic alloys. Mid-tier integrators like ArcFusion Robotics Ltd., Dynamic WeldTech Ltd., and Omega Robotics Ltd. deliver modular, cost-efficient solutions, while turnkey providers including ProWeld Automation LLC, WeldTech Innovations Inc., and Vertex Welding Systems Corporation cater to comprehensive project needs from design through commissioning.
Meanwhile, specialized firms such as InnovaWeld Corporation, Impact Robotics Group Inc., and TechWeld Robotics Inc. carve out niches in unique application environments, whether cleanroom electronics assembly or outdoor heavy machinery construction. OTC Daihen Co., Ltd., Suzhou Aonest Automation Co., Ltd., and Yost Robotics Inc. further diversify the field with regionalized manufacturing and localized support networks, ensuring that end users receive tailored solutions aligned with capital investment strategies.
This comprehensive research report delivers an in-depth overview of the principal market players in the Robotic Welding Arm market, evaluating their market share, strategic initiatives, and competitive positioning to illuminate the factors shaping the competitive landscape.
- ABB Robotics AG
- ArcFusion Robotics Ltd.
- Comau S.p.A.
- Dynamic WeldTech Ltd.
- Elite Welding Technologies Corp.
- ESAB Corporation
- FANUC Robotics Corporation
- Fronius International GmbH
- Fusion Robotics Inc.
- Impact Robotics Group Inc.
- InnovaWeld Corporation
- Kawasaki Robotics Corporation
- KUKA Robotics GmbH
- Lincoln Electric Holdings, Inc.
- Miller Electric Manufacturing Company
- Mitsubishi Electric Automation Inc.
- NextGen Welding Robotics LLC
- Omega Robotics Ltd.
- OTC Daihen Co., Ltd.
- Precision Robotic Systems Inc.
- ProWeld Automation LLC
- RoboWeld Solutions LLC
- Staubli Robotics Ltd.
- Suzhou Aonest Automation Co., Ltd.
- TechWeld Robotics Inc.
- Universal Robots A/S
- Vertex Welding Systems Corporation
- WeldTech Innovations Inc.
- Yaskawa Electric Corporation
- Yost Robotics Inc.
Actionable Recommendations for Industry Leaders in Robotic Welding
To maintain a competitive edge, industry leaders should prioritize a multi-pronged strategy:
-
Strengthen Localized Manufacturing Ecosystems: Establish regional assembly or partner with local integrators to mitigate tariff impacts and reduce lead times.
-
Invest in Smart Integration: Leverage AI-assisted path optimization and IoT-enabled predictive maintenance to maximize uptime and weld consistency.
-
Tailor Solutions to End-User Needs: Develop modular platforms that can transition seamlessly between low-volume precision work and high-volume production, supporting both manual override and full automation.
-
Expand After-Sales Service Capabilities: Enhance training programs, remote diagnostics, and on-site support to build long-term customer loyalty and reduce lifecycle costs.
-
Foster Collaborative Innovation: Partner with material science experts and software developers to advance welding algorithms, especially for exotic alloys and multi-layer joints.
By implementing these recommendations, companies will not only navigate current trade challenges but also unlock new growth avenues across diverse market segments.
Explore AI-driven insights for the Robotic Welding Arm market with ResearchAI on our online platform, providing deeper, data-backed market analysis.
Ask ResearchAI anything
World's First Innovative Al for Market Research
Conclusion
The robotic welding arm market stands at an inflection point where technological maturity meets strategic complexity. As tariffs, evolving customer requirements, and regional dynamics converge, success will hinge on agility, innovation, and a deep understanding of segmented end-user needs. Those who invest in smart platforms, forge resilient supply chains, and cultivate strong local partnerships will be best positioned to capture value in both established and emerging markets. Ultimately, the most successful players will be those that deliver reliable performance today while anticipating the welding demands of tomorrow.
This section provides a structured overview of the report, outlining key chapters and topics covered for easy reference in our Robotic Welding Arm market comprehensive research report.
- Preface
- Research Methodology
- Executive Summary
- Market Overview
- Market Dynamics
- Market Insights
- Cumulative Impact of United States Tariffs 2025
- Robotic Welding Arm Market, by Industry Application
- Robotic Welding Arm Market, by Welding Process
- Robotic Welding Arm Market, by Material Type
- Robotic Welding Arm Market, by Production Scale
- Robotic Welding Arm Market, by Integration Model
- Robotic Welding Arm Market, by Operational Mode
- Robotic Welding Arm Market, by Technology Integration
- Robotic Welding Arm Market, by Application Environment
- Robotic Welding Arm Market, by Innovation Adoption
- Robotic Welding Arm Market, by Scale Of Investment
- Americas Robotic Welding Arm Market
- Asia-Pacific Robotic Welding Arm Market
- Europe, Middle East & Africa Robotic Welding Arm Market
- Competitive Landscape
- ResearchAI
- ResearchStatistics
- ResearchContacts
- ResearchArticles
- Appendix
- List of Figures [Total: 36]
- List of Tables [Total: 467 ]
Next Steps: Engage with Ketan Rohom to Access Full Research Report
To gain a comprehensive perspective on competitive benchmarks, tariff mitigation strategies, and detailed segment forecasts, reach out directly to Ketan Rohom, Associate Director, Sales & Marketing. Equip your organization with the insights needed to accelerate automation initiatives, enhance operational resilience, and drive sustainable growth in the rapidly evolving robotic welding arm market.
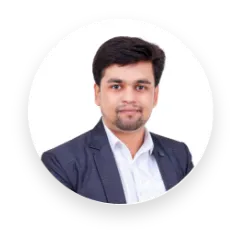
- When do I get the report?
- In what format does this report get delivered to me?
- How long has 360iResearch been around?
- What if I have a question about your reports?
- Can I share this report with my team?
- Can I use your research in my presentation?