Navigating the Future of Shipyard Welding with Robotic Precision
Robotic welding is rapidly transforming the shipbuilding sector by delivering unprecedented levels of precision, repeatability, and throughput. Traditional manual processes are being replaced by automated systems that leverage advanced robotics, sophisticated control algorithms, and integrated software platforms. These systems address longstanding challenges such as weld quality inconsistency, production bottlenecks, and workforce shortages. By embedding sensors and machine-learning models, modern robotic welding solutions continuously optimize weld parameters in real time, reducing defects while increasing yield.
The proliferation of automated welding in shipyards is driven by rising global demand for efficient, high-quality maritime vessels. As shipbuilders strive to meet tighter delivery schedules and adhere to stringent regulatory requirements, robotic welding provides a scalable approach that enhances safety, lowers operational costs, and accelerates build cycles. This report delves into the key forces reshaping the market, examines segmentation trends, evaluates regional dynamics, and surfaces strategic recommendations. Through rigorous primary and secondary research, it delivers the insights necessary for decision-makers to capitalize on technological innovations and navigate evolving tariff policies. Whether you are exploring system upgrades, evaluating new deployment models, or seeking to partner with leading vendors, the analysis presented here equips you with a comprehensive understanding of the competitive landscape and growth opportunities ahead.
How Advanced Robotics Are Redefining Shipbuilding Operations
The shipbuilding industry is undergoing a transformative shift as automotive-grade robotics, artificial intelligence, and digital twins converge on the shop floor. Collaborative robots are working alongside skilled welders to augment human capabilities, handling repetitive tasks while operators focus on critical path planning and quality control. Laser welding platforms equipped with fiber lasers deliver high-speed, low-distortion joins that were previously unattainable with traditional arc processes. Simultaneously, ultrasonic and resistance welding technologies are being integrated for specialized applications, enabling complex multi-material assemblies in confined spaces.
This convergence of technologies is fostering a new paradigm where the entire manufacturing process is orchestrated through real-time data analytics and adaptive control loops. Predictive maintenance algorithms anticipate equipment failures before they occur, reducing unplanned downtime and maximizing throughput rates. Simulation environments and virtual commissioning tools allow engineers to validate welding sequences digitally, minimizing physical prototyping cycles and ensuring seamless integration with hull assembly lines. As a result, shipbuilders can respond more agilely to shifting order books, customize vessels to precise specifications, and meet sustainability targets through optimized energy usage.
These transformative trends are not isolated. They represent a systemic redefinition of how ships are constructed, governed by interconnected processes that span design, procurement, production, and after-sales support. Early adopters of these advanced welding systems are already reporting improved cycle times by up to 30 percent, enhanced structural integrity, and significant reductions in manual rework. This section highlights the most impactful technological and operational shifts that are reshaping competitive dynamics across global shipyards.
Assessing the Ramifications of 2025 U.S. Tariffs on Welding Automation
The introduction of new United States tariffs on imported robotic welding equipment and critical subcomponents in 2025 is set to materially influence market dynamics. With duties imposed on both complete systems and specialized modules such as laser power sources and robotic arms, OEMs and tier-one suppliers are reassessing their global supply chains. Many manufacturers are evaluating nearshoring strategies to mitigate increased landed costs, while shipbuilders are negotiating warranty and service agreements to include more favorable terms on parts replacement and maintenance.
These tariffs have also catalyzed regional sourcing partnerships, enabling local integrators to develop customized solutions that comply with the revised trade framework. Although some end users may face temporary budgetary pressures as capital costs rise, the long-term effect is expected to incentivize investment in domestic manufacturing capabilities. Suppliers that pivot swiftly to establish localized production lines or secure tariff exemptions through trade agreements will gain a competitive advantage.
Moreover, the cost ripple extends beyond equipment pricing. Engineering consulting, installation services, and training programs tied to robot deployment may see adjusted fee structures as integrators factor in tariff-related overhead. Stakeholders must therefore adopt a holistic view of total cost of ownership, incorporating duty-driven fluctuations into their financial modeling. By proactively assessing alternative sourcing options and forging strategic alliances, shipyards can buffer against potential disruptions and maintain progress on automation roadmaps.
Unveiling Market Dynamics Through Comprehensive Segmentation Analysis
A nuanced examination of the market by welding type reveals that conventional arc methods, particularly metal inert gas welding, remain the backbone of large-scale hull construction, while plasma arc and tungsten inert gas approaches are carving out niches for precision applications. Laser technologies, divided between carbon dioxide and the more flexible fiber variants, are gaining traction in automated panel joining, where minimal heat-affected zones and high travel speeds yield superior cosmetic and structural results. Meanwhile, spot resistance welding continues to dominate high-volume joinery in superstructure modules, and high-frequency ultrasonic systems are emerging as enablers for lightweight composite mating operations.
When assessing applications, automated decks benefit from consistent weld penetration along large surface areas, whereas hull assembly lines leverage robotic cells to synchronize panel fit-up and longitudinal seams. Module fabrication centers deploy versatile robots for repeated pattern operations, and pipe welding solutions integrate tailored end effectors and path planning algorithms to navigate complex internal geometries. Across these use cases, the interplay between joint design, fixture automation, and software-driven process monitoring determines overall throughput and quality consistency.
Component segmentation underscores the critical role of hardware elements-the controller architectures, end effectors, power supplies, and robotic arms-that must operate in concert. Service offerings, from initial system installation to ongoing preventive maintenance and operator training, form the backbone of customer satisfaction and uptime optimization. Software investments in trajectory planning and real-time process monitoring deliver measurable improvements in weld repeatability and allow for rapid adaptation to new vessel designs.
Deployment models are bifurcated between collaborative robots, which include six-axis and SCARA variants suited for shared-workspace tasks, and dedicated cells designed as multi-station or single-station workhorses for high-volume operations. End-use sectors further delineate market priorities: commercial shipbuilders focus on cargo vessels, cruise liners, and offshore support craft, while defense contractors specify naval ships and submarines with exacting standards. Finally, analysis by ship type-from bulk carriers to container ships, passenger vessels, and tankers-reveals differentiated adoption rates, driven by hull geometry complexity, material thickness, and regulatory inspection regimes.
This comprehensive research report categorizes the Robotic Welding System for Shipbuilding market into clearly defined segments, providing a detailed analysis of emerging trends and precise revenue forecasts to support strategic decision-making.
- Type
- Application
- Component
- Deployment
- End Use
- Ship Type
Regional Market Forces Shaping Robotic Welding Adoption
Regional landscapes exhibit distinctive characteristics that influence the pace and scale of robotic welding adoption. In the Americas, robust demand from commercial shipyards building container ships and offshore support vessels coexists with increasing defense sector investments in naval frigates and submarines. Local system integrators and service providers have established mature networks, facilitating rapid deployment and localized support for controllers, end effectors, and power sources. Meanwhile, trade policy shifts are prompting stakeholders to explore alternative partnerships across North and South America to diversify supply chains.
Europe, the Middle East, and Africa present a heterogeneous mix of advanced manufacturing hubs and emerging shipbuilding markets. Western European nations are pioneering industry-grade digital twins and deploy high-precision laser welding cells for cruise ship modules and luxury yacht sections. Gulf economies are ramping up investments in offshore vessel assembly, prioritizing automation to offset labor cost inflation and meet sustainability targets. Additionally, African shipyards are exploring low-cost robotic cells to address local infrastructure needs and improve fleet maintenance capabilities.
Asia-Pacific remains the fastest-growing region, anchored by major shipyards in China, Japan, and South Korea. These facilities exploit scale advantages to integrate multi-station dedicated cells for bulk carriers and tankers, while rising OEMs in Australia and Southeast Asia are piloting collaborative robots for smaller passenger and offshore craft. Government incentives, export-oriented policies, and a deep pool of engineering talent are driving continuous innovation in path planning software and process monitoring systems. As a result, Asia-Pacific players are both significant consumers and leading developers of welding automation solutions.
This comprehensive research report examines key regions that drive the evolution of the Robotic Welding System for Shipbuilding market, offering deep insights into regional trends, growth factors, and industry developments that are influencing market performance.
- Americas
- Europe, Middle East & Africa
- Asia-Pacific
Dominant Players and Strategic Alliances Driving Innovation
The competitive landscape is defined by a cadre of global robotics specialists, power source innovators, and integrators. Leading robot manufacturers collaborate closely with welding equipment providers to co-develop turnkey solutions that marry core kinematics with domain-specific welding expertise. Laser power source companies partner with end-effector designers to expand the application envelope, offering modular cells that can be reconfigured across vessel classes. Software houses have emerged as pivotal enablers, delivering platform-agnostic tools for advanced trajectory planning and process analytics.
System integrators with deep shipyard experience maintain extensive service networks, offering installation, maintenance, and operator training packages that ensure consistent performance and rapid post-deployment optimization. Strategic alliances between component suppliers and shipbuilding conglomerates are accelerating the creation of localized manufacturing ecosystems, while joint ventures and acquisitions are consolidating competencies in robotics, welding, and digital manufacturing. These collaborations underscore the industry’s shift toward integrated solutions rather than point-product sales, positioning comprehensive automation platforms as the new baseline for competitiveness.
This comprehensive research report delivers an in-depth overview of the principal market players in the Robotic Welding System for Shipbuilding market, evaluating their market share, strategic initiatives, and competitive positioning to illuminate the factors shaping the competitive landscape.
- FANUC Corporation
- Yaskawa Electric Corporation
- ABB Ltd.
- KUKA AG
- Kawasaki Heavy Industries, Ltd.
- OTC Daihen Corporation
- Panasonic Corporation
- Comau S.p.A.
- Lincoln Electric Holdings, Inc.
- Fronius International GmbH
Strategic Imperatives to Capitalize on Robotic Welding Growth
To translate market insights into competitive advantage, shipyard executives should prioritize modular automation architectures that can evolve with production needs. Investing in flexible cells that support both collaborative and dedicated deployments enables rapid reallocation across deck, hull, and module operations. Engaging early with software specialists ensures that path planning and process monitoring tools are tailored to the unique joint geometries and material specifications of each vessel program.
Supply chain diversification must be paired with rigorous supplier qualification protocols to maintain component quality amid shifting tariffs. Establishing regional service hubs and training academies helps secure uptime commitments and develop a skilled workforce capable of overseeing advanced welding platforms. In parallel, pilot programs for predictive maintenance and digital twin integration will yield actionable data to refine operational workflows and reduce unplanned downtime.
Finally, forging research partnerships with academic institutions and technology consortia can accelerate the adoption of emerging welding modalities such as hybrid laser-arc and high-frequency ultrasonic processes. By aligning R&D investments with strategic imperatives-skilled labor augmentation, energy efficiency, and quality excellence-industry leaders will be well positioned to capture new market segments and set the benchmark for automated shipbuilding performance.
Rigorous Approach to Gathering and Analyzing Market Intelligence
This report is grounded in a robust research framework that integrates both primary and secondary sources. Industry data was collected through interviews with C-suite executives, operations managers, and research directors at leading shipyards, robotics suppliers, and system integrators. These insights were triangulated with publicly available financial reports, patent filings, and regulatory filings to validate trends and forecast implications.
Quantitative analysis was supported by proprietary databases that track equipment shipments, service contracts, and regional deployment statistics. Qualitative assessments stem from expert panels convened to evaluate technological maturity, adoption barriers, and market readiness. Each data point underwent rigorous cross-verification to ensure reliability and relevance.
Segmentation matrices were developed to reflect real-world use cases, incorporating variables such as welding type, application, component architecture, deployment model, end-use sector, and ship classification. Regional analyses considered economic indicators, trade policy frameworks, and investment incentives. The resulting methodology delivers a comprehensive, reproducible foundation for strategic decision-making.
Explore AI-driven insights for the Robotic Welding System for Shipbuilding market with ResearchAI on our online platform, providing deeper, data-backed market analysis.
Ask ResearchAI anything
World's First Innovative Al for Market Research
Synthesizing Insights to Chart the Path Forward
Robotic welding systems represent a pivotal enabler for shipbuilders seeking to enhance productivity, quality, and safety across vessel construction and maintenance. The intersection of advanced robotics, intelligent software, and evolving tariff considerations has created both challenges and opportunities. By dissecting market segmentation and regional dynamics, and profiling key industry players, this analysis provides a holistic view of the current state and future trajectory.
Leaders who embrace modular automation, cultivate strategic partnerships, and maintain agility in sourcing will unlock significant competitive advantages. As the industry moves toward greater digitization and collaborative human-machine ecosystems, the insights presented here will serve as a blueprint for informed investment and operational excellence. The time to act is now: deploying the right technologies and strategies will determine which shipyards steer the next wave of maritime innovation.
This section provides a structured overview of the report, outlining key chapters and topics covered for easy reference in our Robotic Welding System for Shipbuilding market comprehensive research report.
- Preface
- Research Methodology
- Executive Summary
- Market Overview
- Market Dynamics
- Market Insights
- Cumulative Impact of United States Tariffs 2025
- Robotic Welding System for Shipbuilding Market, by Type
- Robotic Welding System for Shipbuilding Market, by Application
- Robotic Welding System for Shipbuilding Market, by Component
- Robotic Welding System for Shipbuilding Market, by Deployment
- Robotic Welding System for Shipbuilding Market, by End Use
- Robotic Welding System for Shipbuilding Market, by Ship Type
- Americas Robotic Welding System for Shipbuilding Market
- Europe, Middle East & Africa Robotic Welding System for Shipbuilding Market
- Asia-Pacific Robotic Welding System for Shipbuilding Market
- Competitive Landscape
- ResearchAI
- ResearchStatistics
- ResearchContacts
- ResearchArticles
- Appendix
- List of Figures [Total: 28]
- List of Tables [Total: 769 ]
Secure Your In-Depth Robotic Welding System Report Today
To gain the strategic intelligence needed to lead in the evolving shipbuilding automation landscape, secure your comprehensive report on robotic welding systems today. Connect directly with Ketan Rohom, Associate Director of Sales & Marketing, for personalized insights and tailored guidance on harnessing these advancements. Elevate your decision-making with data-driven analysis, expert interviews, and actionable roadmaps that will inform investment, technology adoption, and competitive positioning. Reach out now to unlock the detailed findings, proprietary segmentation, regional breakdowns, and future-proof recommendations that will empower your organization to outperform rivals and capitalize on emerging market opportunities.
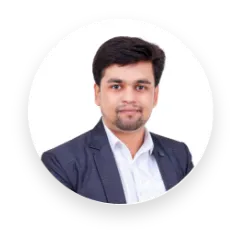
- When do I get the report?
- In what format does this report get delivered to me?
- How long has 360iResearch been around?
- What if I have a question about your reports?
- Can I share this report with my team?
- Can I use your research in my presentation?