Setting the Stage for Evolution in FPC Lamination
The roll to roll laminator has emerged as a pivotal enabler in the production of flexible printed circuits, addressing critical demands for high-speed processing, precision alignment, and material uniformity. In response to the burgeoning miniaturization of electronic components and the surging adoption of wearable and IoT devices, manufacturers are increasingly relying on advanced lamination solutions to maintain throughput and quality. This executive summary unpacks the multifaceted dynamics reshaping the industry, from evolving end-user requirements to the technological breakthroughs that redefine efficiency.
With global electronics supply chains under constant pressure to reduce cost, improve yield, and accelerate time-to-market, roll to roll laminators for FPC applications are no longer mere equipment investments-they are strategic assets. As circuit complexity intensifies, the ability to seamlessly integrate adhesive, thermal, and UV bonding methods alongside precise tension control becomes a decisive factor in product reliability. Against this backdrop, stakeholders must understand both the macroeconomic forces and the micro-level process optimizations that will determine competitive positioning in the years ahead.
Rewriting the Rules with Emerging Lamination Technologies
The lamination ecosystem is undergoing a profound transformation driven by converging technological innovations and shifting manufacturing paradigms. Advanced materials, digital process controls, and integrated vision systems are converging to push boundaries in resolution, speed, and defect detection. As manufacturers pursue Industry 4.0 aspirations, the integration of real-time sensor data and predictive maintenance algorithms into laminator platforms is creating unprecedented visibility into process performance, reducing downtime, and optimizing throughput.
Materials science breakthroughs are equally disruptive, with novel adhesive formulations and UV-curable polymers enabling thinner laminates and stronger interfacial bonds. Thermal lamination techniques have achieved new efficiencies through rapid heat exchange mechanisms and modular heating zones that cater to heterogeneous substrate properties. Furthermore, the rise of hybrid lamination lines that seamlessly switch between cold bonding for delicate substrates and high-temperature lamination for robust configurations is redefining production flexibility. These convergent shifts are fundamentally rewriting the rules of FPC assembly, enabling next-generation devices that demand ever-smaller form factors, higher reliability, and faster production cycles.
Navigating the Ripple Effects of US Tariff Changes in 2025
The imposition of augmented tariffs by the United States in 2025 has reverberated across global supply chains, compelling stakeholders to reevaluate sourcing strategies, cost allocations, and partnership models. Cumulative duties on critical lamination materials, including specialty adhesives and release liners sourced from key Asian markets, have increased landed costs and introduced volatility in margin structures. This environment has prompted both equipment providers and material suppliers to explore onshore manufacturing initiatives, strategic joint ventures, and tariff engineering techniques to mitigate exposure.
In the wake of these changes, many manufacturers have pursued dual-sourcing arrangements, combining regional production hubs with alternative material portfolios to preserve cost competitiveness. Some have accelerated the localization of adhesive compounding and pre-laminated substrate production, while others have negotiated long-term supply contracts to lock in favorable terms before further tariff escalations. The net result is a more fragmented yet resilient ecosystem, where agility in trade compliance, customs optimization, and cross-border logistics has become as critical to success as technical prowess in lamination.
Unlocking Market Dimensions through Critical Segmentation Analysis
Understanding the full breadth of the roll to roll laminator market requires a multi-dimensional segmentation lens that captures the nuanced ways in which end-users and applications are diverging. A technology-based perspective highlights the rise of adhesive lamination for lightweight wearable circuits, while cold lamination techniques are gaining traction for heat-sensitive substrates. Thermal lamination remains a mainstay for robust industrial electronics, and ultraviolet lamination is carving out a niche in applications demanding rapid cure cycles and minimal thermal stress.
Application-driven insights reveal that the automotive electronics sector is increasingly reliant on high-throughput laminators to meet stringent safety and reliability benchmarks, even as consumer electronics demand lines capable of handling complex flexible displays. The industrial electronics space values systems with modular roll-to-roll capability to accommodate varying substrate widths, while medical device manufacturers prioritize traceability features and cleanroom-compatible configurations. From an end-user standpoint, contract manufacturers are pushing for fully automatic lines to reduce labor variability, electronics manufacturers often retain semi-automatic cells for pilot runs, and EMS providers balance manual and automated units to optimize cost and flexibility.
Further refinement emerges when examining specific machine attributes. Rollers calibrated for substrate thicknesses between 200 and 400 microns must accommodate rapid speed changes for short runs, while laminators designed for films under 200 microns feature ultra-precise tension controls to avoid wrinkling. Equipment tailored to widths of 500 to 1000 millimeters addresses mainstream panel formats, contrasted with specialized systems for narrow webs below 500 millimeters and custom solutions exceeding 1000 millimeters for large-area circuits. Operating speed also defines the competitive landscape, with midrange lines running at 50 to 100 meters per minute forming the performance backbone, entry-level laminators focusing on speeds under 50 meters per minute for high-accuracy jobs, and high-speed units surpassing 100 meters per minute to meet volume-intensive requirements.
This comprehensive research report categorizes the Roll to Roll Laminator for FPC market into clearly defined segments, providing a detailed analysis of emerging trends and precise revenue forecasts to support strategic decision-making.
- Technology
- Application
- End User
- Automation Level
- Thickness
- Roll Width
- Operating Speed
Regional Dynamics Shaping the Global Lamination Arena
Geographic factors play a pivotal role in shaping demand trajectories and supply chain configurations for roll to roll laminators. In the Americas, rising onshore electronics manufacturing in the United States and Mexico has spurred investments in state-of-the-art lamination lines that reduce time-to-market and mitigate cross-border logistics risks. Regulatory incentives for domestic production of automotive and defense electronics are further catalyzing capital expenditures, while emerging opportunities in Brazil’s consumer electronics sector create secondary pockets of growth.
Shifts in the Europe, Middle East & Africa region reflect a blend of established industrial bases and nascent manufacturing clusters. Western European nations remain hubs for precision laminator innovation, backed by strong R&D ecosystems and robust service networks. Meanwhile, Middle Eastern initiatives aimed at diversifying away from oil revenues are prompting targeted incentives for electronics assembly, encouraging local integrators to partner with global equipment vendors. Eastern European countries are also attracting investment as high-volume contract manufacturers seek cost efficiencies and preferential access to EU markets.
The Asia-Pacific landscape continues to dominate production volume, driven by China’s sprawling electronics clusters and Southeast Asia’s growing role as a cost-competitive alternative. Japan and South Korea sustain leadership in advanced materials and process automation, while Taiwan’s EMS ecosystem fuels strong demand for versatile laminator configurations. Across the region, competition is intensifying as new players enter the market with localized service offerings and financing programs designed to lower the barrier to adoption for small and mid-sized manufacturers.
This comprehensive research report examines key regions that drive the evolution of the Roll to Roll Laminator for FPC market, offering deep insights into regional trends, growth factors, and industry developments that are influencing market performance.
- Americas
- Europe, Middle East & Africa
- Asia-Pacific
Profiling Market Leaders and Competitive Strategies
Competition within the roll to roll laminator market is defined by a handful of global technology leaders alongside agile regional specialists. Leading multinational vendors have secured their positions through continuous innovation in process controls, materials compatibility, and digital integration. They maintain extensive service networks, ensuring rapid field support and spare parts availability across major production hubs. These firms also partner with adhesive and film suppliers to offer turnkey solutions that streamline installation and minimize the learning curve for new customers.
At the same time, regional players are capitalizing on localized expertise, shorter lead times, and flexible financing options to challenge global incumbents in emerging markets. By customizing machine configurations to specific substrate characteristics and local regulatory requirements, these companies foster deeper relationships with contract manufacturers and EMS providers seeking tailored solutions. Strategic alliances between global and regional entities are increasingly common, blending technological prowess with market-specific know-how to capture share in both developed and developing markets.
This comprehensive research report delivers an in-depth overview of the principal market players in the Roll to Roll Laminator for FPC market, evaluating their market share, strategic initiatives, and competitive positioning to illuminate the factors shaping the competitive landscape.
- ULVAC, Inc.
- Toray Engineering Co., Ltd.
- SCREEN Semiconductor Solutions Co., Ltd.
- Hitachi High-Tech Corporation
- Canon Machinery Inc.
- Nordson Corporation
- Applied Materials, Inc.
- MKS Instruments, Inc.
- EVATEC AG
- VON ARDENNE GmbH
Strategic Imperatives for Future-Proofing Lamination Investments
Industry leaders must prioritize a systematic approach to investment that aligns lamination capabilities with evolving product roadmaps. Upgrading existing lines with modular heating and UV curing units can extend process flexibility without the expense of full equipment replacement. Establishing strong partnerships with adhesive and film suppliers ensures early access to next-generation materials that can unlock new application niches. It is also critical to integrate real-time analytics and predictive maintenance platforms, as these systems can dramatically reduce unplanned downtime and improve process yield.
Moreover, companies should develop multi-sourcing strategies that hedge against geopolitical risks and tariff volatility, leveraging regional production capacity for both equipment and consumables. Collaboration with contract manufacturers to pilot advanced laminator configurations can accelerate technology validation and build customer confidence. From an operational standpoint, cross-training maintenance teams on both mechanical and digital diagnostic tools will streamline troubleshooting and reinforce continuous improvement cycles. Lastly, investing in training programs for line operators ensures that human expertise keeps pace with automation advancements, safeguarding process consistency and quality.
Robust Research Framework Underpinning Market Insights
The research underpinning these insights combines extensive secondary analysis of industry publications, trade data, and regulatory filings with primary interviews conducted across the value chain. Key stakeholders, including equipment OEM executives, material science experts, and contract manufacturing leaders, contributed qualitative perspectives that deepened understanding of decision criteria and technology adoption timelines. Data points were triangulated against historical shipment records and customs databases to assess trade flow dynamics and tariff impacts.
Segmentation frameworks were developed through iterative validation workshops with domain specialists, ensuring that each category reflects practical distinctions in technology, application, end-user, and machine specifications. Rigorous quality checks and cross-referencing with publicly available financial statements enhanced data accuracy, while sensitivity analyses were employed to test the resilience of key findings under varying economic scenarios. This multi-layered methodology ensures a balanced, objective view of the roll to roll laminator market without reliance on proprietary forecasting models.
Explore AI-driven insights for the Roll to Roll Laminator for FPC market with ResearchAI on our online platform, providing deeper, data-backed market analysis.
Ask ResearchAI anything
World's First Innovative Al for Market Research
Integrating Findings to Propel Strategic Decisions
The roll to roll laminator market for flexible printed circuits stands at a critical inflection point, driven by advanced materials, digital process controls, and shifting trade dynamics. Stakeholders who understand the nuanced segmentation of technologies, applications, and end-users will be best positioned to capture emerging opportunities in automotive, medical, and consumer electronics. Meanwhile, regional dynamics and tariff-induced cost pressures underscore the need for agile sourcing and strategic partnerships.
Competition will intensify around the ability to deliver turnkey solutions that integrate lamination equipment, materials, and software analytics. Companies that proactively modernize their lines, diversify supply chains, and embrace data-driven process management will outpace rivals reliant on legacy platforms. As the industry advances toward higher speeds, tighter tolerances, and more complex substrates, the combination of human expertise and technological innovation will determine market leadership and long-term profitability.
This section provides a structured overview of the report, outlining key chapters and topics covered for easy reference in our Roll to Roll Laminator for FPC market comprehensive research report.
- Preface
- Research Methodology
- Executive Summary
- Market Overview
- Market Dynamics
- Market Insights
- Cumulative Impact of United States Tariffs 2025
- Roll to Roll Laminator for FPC Market, by Technology
- Roll to Roll Laminator for FPC Market, by Application
- Roll to Roll Laminator for FPC Market, by End User
- Roll to Roll Laminator for FPC Market, by Automation Level
- Roll to Roll Laminator for FPC Market, by Thickness
- Roll to Roll Laminator for FPC Market, by Roll Width
- Roll to Roll Laminator for FPC Market, by Operating Speed
- Americas Roll to Roll Laminator for FPC Market
- Europe, Middle East & Africa Roll to Roll Laminator for FPC Market
- Asia-Pacific Roll to Roll Laminator for FPC Market
- Competitive Landscape
- ResearchAI
- ResearchStatistics
- ResearchContacts
- ResearchArticles
- Appendix
- List of Figures [Total: 30]
- List of Tables [Total: 328 ]
Secure Strategic Insights with Our Comprehensive Market Report
Investors and decision-makers seeking a comprehensive understanding of the roll to roll laminator landscape are encouraged to reach out directly to Ketan Rohom, Associate Director, Sales & Marketing, to secure the full market research report. The report delivers in-depth analysis, actionable insights, and strategic forecasts that can inform critical investments and operational enhancements. Engaging with Ketan Rohom provides access to tailored data packages, interactive briefings, and exclusive executive summaries designed to catalyze market advantage. This direct channel ensures rapid response, customized support, and priority delivery of proprietary findings that will empower your organization to navigate evolving trade dynamics, technological shifts, and competitive pressures with confidence.
Purchase of the report unlocks detailed segmentation breakdowns, regional performance metrics, and vendor benchmarking that cannot be found elsewhere. By leveraging these insights, stakeholders can optimize supply chains, target high-growth niches, and align product roadmaps with emerging customer needs. Contacting Ketan Rohom secures personalized consultation on how to deploy the research outcomes effectively across strategic, operational, and financial planning cycles. Take this opportunity to secure your competitive edge and invest in intelligence that drives sustainable growth across the roll to roll laminator value chain
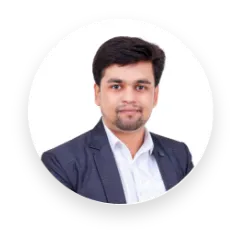
- When do I get the report?
- In what format does this report get delivered to me?
- How long has 360iResearch been around?
- What if I have a question about your reports?
- Can I share this report with my team?
- Can I use your research in my presentation?