The Roller Compactor for Dry Granulation Market size was estimated at USD 1.51 billion in 2024 and expected to reach USD 1.62 billion in 2025, at a CAGR 7.51% to reach USD 2.33 billion by 2030.

Pioneering the Future of Dry Granulation Roller Compactors with Unmatched Efficiency and Versatility Transcending Traditional Boundaries
In recent years, the gravitation towards dry granulation methods has underscored roller compactors as pivotal assets in achieving consistent particle size distribution and superior granulate strength. Traditionally viewed as adjunct tools within broader manufacturing lines, these compactors have ascended to become central instruments for companies seeking reduced solvent usage and streamlined downstream processing. Against a backdrop of escalating regulatory scrutiny and growing emphasis on sustainable manufacturing, the roller compactor has emerged as an enabler of green process design devoid of excessive moisture or thermal stress. This document synthesizes critical insights into how this equipment underpins higher throughput and uniformity, positioning it as an indispensable component in pharmaceutical, food processing, and chemical production settings.
Transitioning from legacy approaches to digital-enabled operations, manufacturers are increasingly adopting connected sensors and data analytics for real-time monitoring of compaction force, roll speed, and material feed rates. This evolution is redefining quality assurance paradigms, ensuring that granules meet stringent end-use specifications while minimizing waste and downtime. As the industry accelerates towards continuous manufacturing, the roller compactor is no longer a peripheral implement but a core driver of efficiency gains and operational resilience. The subsequent sections dissect the transformative forces, segmentation nuances, and strategic imperatives that collectively shape the contemporary landscape of roller compaction technology.
Revolutionary Advancements in Granulation Technologies Catalyzing a Paradigm Shift in Roller Compactor Capabilities and Operational Workflows
The granulation landscape has witnessed seismic shifts propelled by breakthroughs in compaction dynamics and material science. Central to this transformation is the integration of advanced kneading and shear mechanisms in oscillating granulators, which now deliver homogenous densification across a spectrum of binder formulations. Concurrent progress in roller magnification techniques has enabled unprecedented control over material compression, facilitating tight tolerance management even at elevated production rates. Slit granulator attachments further augment flexibility, affording tailored particle profiles that align with specific downstream requirements without necessitating complete equipment overhauls.
These technological evolutions are complemented by a growing preference for continuous processing over batch-centric workflows. By eschewing intermittent stopping points, manufacturers are achieving smoother transitions between compaction and subsequent sieving stages, thereby minimizing feedstock segregation and elevating overall yield. The confluence of digital twin simulations and predictive maintenance algorithms has further accelerated lifecycle optimization, ensuring that maintenance windows are precisely calibrated to actual wear patterns rather than predetermined schedules. Such integrated innovations herald a paradigm where roller compactors not only process materials but also orchestrate holistic production intelligence.
Assessing the Ripple Effects of 2025 United States Tariff Policies on Roller Compactor Supply Chains and Cost Structures Across Key Industries
The imposition of updated United States tariff measures in 2025 introduced a recalibration of cost structures across the roller compactor ecosystem. Increased duties on imported wear parts and high-precision assemblies have prompted manufacturers to reevaluate sourcing strategies and deepen engagement with domestic supply networks. Raw material suppliers and component fabricators within North America have experienced heightened demand, driving reinvestment in local milling and machining capacities to offset elevated landed costs.
In response, equipment manufacturers have initiated design-for-manufacture programs that prioritize modular architectures and standardized subassemblies. This approach not only mitigates tariff-induced price escalations but also accelerates customization cycles and expedites service part availability. Concurrently, collaborative partnerships between OEMs and regional distributors have been forged to build buffer inventories that smooth procurement lead times and minimize exposure to tariff volatility. As a result, end-users benefit from more predictable pricing models and access to localized technical support, ensuring that production imperatives remain uninterrupted despite shifting trade landscapes.
Unveiling Critical Market Segmentation Dynamics to Decode Product Scale, Technology Innovations, Process Choices, Capacity Tiers, Functional Applications, and Industry Adoption Patterns
Delving into product type distinctions, the market spans from lab scale roller compactors-ideal for R&D and formulation trials-to pilot scale machines that bridge experimental proof of concept with larger production runs, and ultimately to production scale systems engineered for high-volume throughput. Each tier delivers specific advantages, whether optimizing resource use during early-stage development or guaranteeing robust performance under continuous operational regimens. The granulator’s underlying technology further refines these capabilities, with oscillating granulators excelling in uniform densification, roller magnification modules enhancing compression ratios, and slit granulators facilitating post-compaction granule shaping to meet varied downstream criteria.
Process type emerges as another critical lens. Batch processing configurations offer flexibility for small-batch specialty products, accommodating rapid changeover and niche formulation exploration. Continuous processing paradigms, on the other hand, deliver streamlined material flows and reduced safety margins, serving end users who prioritize uninterrupted production. Capacity considerations-ranging from small scale units for pilot initiatives to medium scale platforms supporting mid-tier output, and large scale installations underpinning major manufacturing hubs-underscore the importance of right-sizing equipment investments. Applicability extends across applications such as deaeration, which removes entrapped gases to improve compaction uniformity; dry granulation, a method prized for solvent reduction; and regranulation, which repurposes off-spec fines and rejects to maximize yield. Finally, end-user industry dynamics shape adoption curves. Chemical and petrochemical companies leverage robust compaction for specialty additives, food processing organizations incorporate granulators to enhance mixing and flow characteristics, and pharmaceutical companies deploy these machines to meet exacting dosage form consistency requirements.
This comprehensive research report categorizes the Roller Compactor for Dry Granulation market into clearly defined segments, providing a detailed analysis of emerging trends and precise revenue forecasts to support strategic decision-making.
- Product Type
- Technology Type
- Process Type
- Capacity
- Application
- End-User Industry
Mapping Regional Market Landscapes to Identify Growth Epicenters and Emerging Opportunities Across Americas, Europe Middle East and Africa, and Asia Pacific Territories
The Americas region continues to anchor the global roller compactor market, driven by a dense network of contract development and manufacturing enterprises, a strong pharmaceutical innovation ecosystem, and a growing appetite for food ingredient diversification. Investment in infrastructure modernization and regulatory alignment initiatives fosters a fertile environment for advanced compaction solutions, particularly in hubs located across North America.
In Europe, the Middle East, and Africa, technological adoption is propelled by stringent quality regulations and a preference for localized production capabilities. Western European manufacturing clusters integrate roller compactors into end-to-end continuous lines, while emerging economies in the EMEA band are increasingly investing in medium scale systems to serve burgeoning domestic markets. Cross-border collaboration frameworks and joint ventures are common strategies to overcome tariff sensitivities and to leverage regional R&D competencies.
The Asia-Pacific landscape exhibits a dual trajectory: established markets in Japan and South Korea upgrade production scale roller compactors with digitalization overlays, whereas Southeast Asian nations expand pilot and small scale installations to support contract pharma and agrochemical processing demands. This diversified approach underscores the region’s role as both a center for mature technological deployment and a cradle for nascent growth opportunities, fostered by favorable investment climates and expanding end-user sectors.
This comprehensive research report examines key regions that drive the evolution of the Roller Compactor for Dry Granulation market, offering deep insights into regional trends, growth factors, and industry developments that are influencing market performance.
- Americas
- Europe, Middle East & Africa
- Asia-Pacific
Profiling Leading Roller Compactor Manufacturers Shaping Industry Innovation through Product Evolution Strategic Alliances and After Sales Support Excellence
Key industry players are distinguishing themselves through an amalgam of product innovation, strategic partnerships, and after-sales support enhancements. Leading OEMs are expanding their service portfolios by integrating remote monitoring capabilities, predictive maintenance offerings, and modular upgrade paths that minimize operational disruptions. Cross-sector alliances are fostering co-development initiatives, aligning roller compactor design roadmaps with specialty chemical and pharmaceutical pilot facilities to validate next-generation material handling configurations.
Simultaneously, component suppliers specializing in high-tolerance rollers, advanced binder distribution systems, and proprietary wear-resistant coatings are forging closer ties with machine builders to ensure end-to-end performance optimization. Such collaboration has accelerated the introduction of plug-and-play enhancements that retrofit legacy assets, extending equipment lifecycles and delivering incremental value without necessitating full-scale capital investments. Through these collective efforts, market participants are cultivating value-driven ecosystems that emphasize sustainable operations, agility to regulatory shifts, and seamless scalability.
This comprehensive research report delivers an in-depth overview of the principal market players in the Roller Compactor for Dry Granulation market, evaluating their market share, strategic initiatives, and competitive positioning to illuminate the factors shaping the competitive landscape.
- Adare Pharma Solutions
- Alexanderwerk AG
- Beijing Longlitech Co., Ltd.
- Bepex International LLC
- Cadmach Machinery Co. Pvt. Ltd.
- Chamunda Pharma Machinery Pvt. Ltd.
- faytec ag
- Freund-Vector Corporation
- Gerteis Maschinen + Processengineering AG
- Hosokawa Micron Corporation
- IDEX MPT, Inc.
- Jiangyin Junzhuo Machinery Manufacturing Co., Ltd.
- Kevin Process Technologies Pvt. Ltd.
- L.B. Bohle Maschinen und Verfahren GmbH
- Natoli Engineering Company, Inc.
- Nicomac Srl
- Prism Pharma Machinery
- Yenchen Machinery Co., Ltd.
- Yichun Wonsen Intelligent Equipment Co., Ltd.
Strategic Imperatives for Industry Leaders to Navigate Trade Volatility Optimize Operational Resilience and Capitalize on Emerging Dry Granulation Innovations
Organizations seeking to excel in the dry granulation space should prioritize the establishment of cross-functional innovation labs that bring process engineers, material scientists, and data analysts together to co-create advanced compaction solutions. By fostering internal centers of excellence, companies can accelerate formulation optimization cycles and reduce time to commercial production. Additionally, investing in modular equipment architectures will empower rapid reconfiguration to address evolving product portfolios and regulatory demands, while minimizing capital outlay and downtime.
Forging strategic partnerships with regional parts fabricators and service providers can mitigate exposure to trade policy uncertainties and compress lead times for critical spares. Embedding digital twin and predictive maintenance platforms into existing installations will bolster operational resilience and reduce unscheduled stoppages. Finally, cultivating domain expertise through targeted training programs ensures that personnel remain adept at interpreting real-time process data, enabling swift corrective actions and continuous improvement in granulation quality metrics.
Robust Multistage Research Framework Integrating Primary Interviews Site Observations Data Triangulation and Peer Review to Ensure Analytical Rigor
This analysis leverages a dual-pronged methodology encompassing both qualitative and quantitative research phases. The qualitative component involved in-depth interviews with industry veterans, process engineers, and technology providers to surface firsthand perspectives on equipment performance, regulatory influences, and innovation roadmaps. Simultaneously, quantitative data was aggregated from corporate disclosures, trade associations, and platform-level instrumentation logs, then triangulated to validate observed trends and support narrative coherence.
Insights were further enriched through site visits to leading manufacturing facilities across the Americas, EMEA, and Asia-Pacific regions, enabling direct observation of roller compactor integration within live production lines. Secondary research included the review of scholarly publications, regulatory guidelines, and patent filings to capture emerging material formulations and patentable design advancements. Data triangulation and peer review processes were employed throughout to ensure analytical robustness and mitigate potential biases, culminating in a comprehensive narrative that addresses both strategic imperatives and operational realities.
Explore AI-driven insights for the Roller Compactor for Dry Granulation market with ResearchAI on our online platform, providing deeper, data-backed market analysis.
Ask ResearchAI anything
World's First Innovative Al for Market Research
Synthesis of Core Findings and Strategic Outlook Reinforcing the Transformative Role of Roller Compactors in Modern Granulation Ecosystems
The roller compactor market for dry granulation stands at an inflection point, where technological advancements and shifting regulatory landscapes are converging to redefine operational paradigms. Through modular design, digital integration, and localized manufacturing strategies, stakeholders can navigate trade headwinds, streamline production workflows, and enhance product quality. The segmentation insights underscore the importance of tailoring equipment scale and process type to application-specific imperatives, while regional analyses reveal diverse growth trajectories informed by geographic strengths and industrial maturity.
As the industry accelerates towards continuous manufacturing, value-driven partnerships and proactive investment in innovation ecosystems will delineate the market leaders from the followers. By synthesizing the technical, economic, and operational facets outlined in this summary, decision-makers are equipped to chart a course that aligns with both immediate imperatives and long-term enterprise objectives, thereby securing competitive advantage in an increasingly complex global landscape.
This section provides a structured overview of the report, outlining key chapters and topics covered for easy reference in our Roller Compactor for Dry Granulation market comprehensive research report.
- Preface
- Research Methodology
- Executive Summary
- Market Overview
- Market Dynamics
- Market Insights
- Cumulative Impact of United States Tariffs 2025
- Roller Compactor for Dry Granulation Market, by Product Type
- Roller Compactor for Dry Granulation Market, by Technology Type
- Roller Compactor for Dry Granulation Market, by Process Type
- Roller Compactor for Dry Granulation Market, by Capacity
- Roller Compactor for Dry Granulation Market, by Application
- Roller Compactor for Dry Granulation Market, by End-User Industry
- Americas Roller Compactor for Dry Granulation Market
- Europe, Middle East & Africa Roller Compactor for Dry Granulation Market
- Asia-Pacific Roller Compactor for Dry Granulation Market
- Competitive Landscape
- ResearchAI
- ResearchStatistics
- ResearchContacts
- ResearchArticles
- Appendix
- List of Figures [Total: 30]
- List of Tables [Total: 556 ]
Unlock Exclusive Granulation Market Intelligence and Transform Strategic Initiatives by Engaging Directly with the Expert Associate Director of Sales & Marketing
The exploration of this market’s nuances culminates in an opportunity for decisive action to reinforce competitive positioning, enhance operational excellence, and future-proof granulation strategies. Engaging directly with Ketan Rohom, Associate Director of Sales & Marketing, grants access to an extensive repository of insights and bespoke consultancy tailored to strategic growth initiatives. By partnering with this dedicated resource, stakeholders can secure clarity on emerging technological inflection points, regulatory shifts, and evolving customer demands that will influence investment priorities and product roadmaps. This consultative dialogue is designed to transform abstract market intelligence into actionable blueprints that drive sustainable value and accelerate time to market. Schedule a discussion to uncover how these findings translate into optimized capital allocation, supply chain resilience, and differentiated service offerings that align with your organization’s long-term vision.
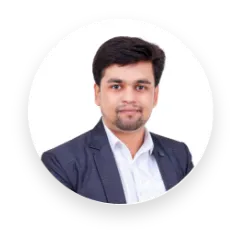
- How big is the Roller Compactor for Dry Granulation Market?
- What is the Roller Compactor for Dry Granulation Market growth?
- When do I get the report?
- In what format does this report get delivered to me?
- How long has 360iResearch been around?
- What if I have a question about your reports?
- Can I share this report with my team?
- Can I use your research in my presentation?