Introduction to RTD Wafer Temperature Measurement Systems
The realm of temperature measurement has undergone a profound evolution with the advent of resistive temperature detectors (RTDs) fabricated on wafer substrates. These wafer-based RTD systems deliver enhanced accuracy, rapid response times, and exceptional stability, meeting the stringent demands of aerospace, automotive, industrial, healthcare, and scientific research sectors. As global industries pursue higher precision and greater process reliability, RTD wafer solutions emerge as a cornerstone technology, enabling real-time monitoring and control in environments ranging from extreme high-temperature furnaces to delicate biomedical instrumentation.
This executive summary provides a concise yet comprehensive overview of the RTD wafer temperature measurement landscape. It highlights the transformative shifts driving innovation, examines the impact of emerging trade policies, distills key segmentation and regional dynamics, profiles leading companies, and delivers actionable strategies for decision-makers aiming to harness the full potential of wafer-based RTD systems. The insights presented herein are designed to empower executives and technical leaders to make informed choices, mitigate risk, and capitalize on growth opportunities in this rapidly advancing field.
Transformative Shifts Reshaping Temperature Measurement Landscape
The temperature measurement industry is experiencing several paradigm-shifting trends that are redefining how precision sensing solutions are designed, deployed, and integrated:
Digitization and IoT Integration: RTD wafer systems are increasingly embedded with digital interfaces and smart analytics capabilities, enabling remote monitoring, predictive maintenance, and seamless connectivity within Industrial Internet of Things (IIoT) frameworks.
Advanced Materials and Nanofabrication: The shift toward high-stability ceramic formulations, thin film compositions with enhanced thermal coefficients, and precision wire-wound architectures is unlocking new performance thresholds, extending sensor lifespans, and boosting reliability under extreme conditions.
Miniaturization and Form Factor Innovation: Wafer-scale manufacturing techniques allow for ultra-compact, high-density sensor arrays, supporting applications where space constraints and low thermal inertia are critical, such as in portable medical devices and compact aerospace instrumentation.
Sustainability and Energy Efficiency: Environmental regulations and corporate sustainability targets are driving demand for low-power, long-lifecycle RTD solutions. Manufacturers are focusing on reducing material waste, increasing recyclability, and optimizing energy consumption across the sensor lifecycle.
Convergence of Contact and Non-Contact Technologies: Hybrid systems incorporating both RTD wafer elements and infrared or thermal imaging modules are gaining traction, offering comprehensive temperature mapping capabilities for complex processes in semiconductor fabrication, power generation, and material analysis.
These transformative shifts underline the importance of continuous innovation, strategic partnerships, and agile supply chain management to maintain a competitive edge.
Cumulative Impact of United States Tariffs on RTD Wafer Systems in 2025
In 2025, newly imposed U.S. tariffs on select electronic components and precision sensors have exerted a multi-faceted impact on the wafer-based RTD ecosystem. Manufacturers sourcing raw sensor substrates and film deposition materials from overseas are navigating higher input costs, prompting adjustments to internal cost structures and price negotiation strategies with end users.
To mitigate exposure, many suppliers are expanding local fabrication capabilities in North America, diversifying procurement channels across allied regions, and entering collaborative manufacturing agreements to share tariff burdens. Meanwhile, system integrators are reevaluating build-to-order models, emphasizing modular, upgrade-friendly architectures that minimize the need for full sensor replacements and reduce total cost of ownership.
Regulatory compliance costs have increased, reinforcing the imperative for robust trade management processes and real-time duty monitoring. In response, businesses are investing in digital customs platforms and advanced risk analytics to forecast tariff implications and optimize their global logistics networks. Although the tariffs have introduced near-term pricing pressures, they are also accelerating innovation in untapped domestic production capabilities and strengthening supply chain resilience going forward.
Key Segmentation Insights Across Sensor, Material, Industry and Beyond
A nuanced understanding of market segmentation is essential to align product development and go-to-market strategies with specific customer needs. In terms of sensor type, general-purpose ceramic and high-stability ceramic sensors cater to applications demanding wide temperature ranges and long-term drift resistance; high-temperature and standard thin films offer low thermal mass solutions ideal for rapid response monitoring; and precision wire-wound, glass-coated wire-wound, and conventional wire-wound sensors deliver robust performance in industrial environments requiring mechanical durability.
Material selection is equally critical: copper alloys and foils provide cost-effective solutions for moderate environments; nickel variants such as Nickel 200 and Nickel 201 balance durability with broad-range sensitivity; and pure platinum and its alloys maintain unrivaled accuracy in high-precision settings albeit at a premium price point.
End-user applications vary significantly: commercial and military aviation systems demand extreme reliability and certification compliance; commercial and passenger vehicles require rugged, miniaturized sensors for engine control and battery monitoring; medical devices and pharmaceutical processes call for biocompatible, sterilizable sensors; and manufacturing equipment along with process instrumentation benefit from customizable sensor layouts and integration flexibility.
Output preferences split between analog alternatives-alternating current and direct current circuits favored for simplicity and legacy compatibility-and digital interfaces including parallel and serial communication protocols, which support advanced signal processing and networked control.
Key application domains encompass climate control systems (HVAC units and refrigeration), energy management (power plants and renewable energy installations), scientific research (laboratory experiments and material analysis rigs), and continuous temperature monitoring solutions such as battery storage supervision. installation methodologies range from embedded sensor nodes and transducer modules to surface-mounted permanent and temporary mounts, each addressing differing maintenance and accessibility requirements.
Finally, technology choices pivot between contact measurement using probes and immersion assemblies and non-contact approaches leveraging infrared detectors and thermal imaging cameras, while the targeted temperature range-from sub-minus-100°C to extreme environments above 1000°C-dictates material robustness and sensor calibration protocols.
This comprehensive research report categorizes the RTD Wafer Temperature Measurement Systems market into clearly defined segments, providing a detailed analysis of emerging trends and precise revenue forecasts to support strategic decision-making.
- Sensor Type
- Material Type
- End-User Industry
- Output Type
- Application
- Installation Type
- Technology
- Temperature Range
Key Regional Dynamics Driving Growth and Innovation
Regional dynamics are shaping RTD wafer system adoption and innovation trajectories. In the Americas, robust aerospace and automotive manufacturing hubs in the United States and Canada are driving demand for high-precision, certified sensor solutions, with strong government research funding supporting advanced materials and IIoT integration projects.
Europe, Middle East & Africa (EMEA) presents a diverse landscape where stringent regulatory frameworks and sustainability mandates propel the adoption of low-power, eco-friendly measurement systems. Leading economies in Germany and France emphasize renewable energy monitoring and industrial automation, while emerging markets in the Middle East prioritize oil & gas process control and infrastructure modernization.
Asia-Pacific leads in high-volume electronics manufacturing, with major sensor fabrication facilities in China, Japan, South Korea, and Taiwan. Demand is spurred by expansions in consumer electronics, renewable energy installations, and smart city initiatives. Regional governments are also investing heavily in local R&D to reduce reliance on imported sensor technologies, fostering an environment of competitive innovation and cost optimization.
This comprehensive research report examines key regions that drive the evolution of the RTD Wafer Temperature Measurement Systems market, offering deep insights into regional trends, growth factors, and industry developments that are influencing market performance.
- Americas
- Asia-Pacific
- Europe, Middle East & Africa
Competitive Landscape and Leading Players Analysis
The competitive terrain of RTD wafer temperature measurement is defined by both global conglomerates and specialized sensor pioneers. ABB Ltd. and Siemens AG leverage expansive automation portfolios and deep integration expertise to deliver turnkey monitoring solutions. AMETEK, Inc. and Fluke Corporation are renowned for their precision instrumentation and extensive calibration networks, ensuring compliance with rigorous industry standards.
Honeywell International Inc. and Sensata Technologies combine broad industrial IoT ecosystems with sensor manufacturing scale, while Endress+Hauser Group excels in process automation and customized sensor modules. Omega Engineering, Inc. and Dwyer Instruments, Inc. have built reputations for rapid prototyping, specialized application support, and educational resources that accelerate adoption in scientific and industrial research settings.
TE Connectivity and Temperature Sensors Ltd. offer modular architectures that simplify system upgrades, and Badger Meter, Inc. brings fluid control synergies to flow and temperature monitoring solutions. Watlow Electric Manufacturing Company and WIKA Instrument, LP stand out for their thermal process components and calibration services, whereas Yokogawa Electric Corporation integrates advanced data analytics with high-accuracy RTD wafer sensors to enable predictive maintenance and process optimization.
These leading players compete on product innovation, regional service presence, strategic partnerships, and the ability to deliver end-to-end solutions that reduce integration complexity and enhance long-term operational efficiency.
This comprehensive research report delivers an in-depth overview of the principal market players in the RTD Wafer Temperature Measurement Systems market, evaluating their market share, strategic initiatives, and competitive positioning to illuminate the factors shaping the competitive landscape.
- ABB Ltd.
- AMETEK, Inc.
- Badger Meter, Inc.
- Dwyer Instruments, Inc.
- Endress+Hauser Group
- Fluke Corporation
- Honeywell International Inc.
- Omega Engineering, Inc.
- Sensata Technologies
- Siemens AG
- TE Connectivity
- Temperature Sensors Ltd.
- Watlow Electric Manufacturing Company
- WIKA Instrument, LP
- Yokogawa Electric Corporation
Actionable Recommendations for Industry Leaders
Industry leaders should consider the following strategic imperatives to capitalize on emerging opportunities and strengthen market positioning:
• Prioritize advanced material development by collaborating with specialty ceramic and thin film suppliers to create sensors that withstand extreme temperatures and harsh process conditions.
• Diversify supply chains through dual-sourcing strategies and regional manufacturing partnerships to mitigate tariff exposure and reduce lead times for critical wafer substrates.
• Accelerate digital transformation initiatives by embedding smart sensor modules with edge analytics, secure IIoT connectivity, and over-the-air firmware updates to enhance system lifecycle value.
• Forge cross-sector alliances with renewable energy, medical device, and aerospace integrators to co-develop tailored sensor solutions and expand addressable market segments.
• Implement robust calibration and certification programs to ensure compliance with global standards, streamline customer qualification processes, and reinforce quality differentiation.
• Embed sustainability criteria into product road-maps by selecting recyclable materials, reducing energy consumption during fabrication, and offering sensor take-back or refurbishment services.
Explore AI-driven insights for the RTD Wafer Temperature Measurement Systems market with ResearchAI on our online platform, providing deeper, data-backed market analysis.
Ask ResearchAI anything
World's First Innovative Al for Market Research
Conclusion: Navigating the Future of RTD Wafer Systems
The RTD wafer temperature measurement sector is poised for sustained advancement as stakeholders weave together materials science breakthroughs, digital capabilities, and supply chain resilience. By staying attuned to shifting regulatory landscapes, geopolitical trade dynamics, and evolving application requirements, organizations can fine-tune their strategies to remain at the forefront of innovation.
Collaborative R&D partnerships, coupled with an unwavering focus on customer-centric customization and environmental stewardship, will determine which companies capture the highest value across complex end-user ecosystems. Ultimately, the most successful players will be those who leverage a holistic approach-integrating product excellence with agile operations and forward-looking service models-to deliver unparalleled performance and reliability in every temperature-critical application.
This section provides a structured overview of the report, outlining key chapters and topics covered for easy reference in our RTD Wafer Temperature Measurement Systems market comprehensive research report.
- Preface
- Research Methodology
- Executive Summary
- Market Overview
- Market Dynamics
- Market Insights
- Cumulative Impact of United States Tariffs 2025
- RTD Wafer Temperature Measurement Systems Market, by Sensor Type
- RTD Wafer Temperature Measurement Systems Market, by Material Type
- RTD Wafer Temperature Measurement Systems Market, by End-User Industry
- RTD Wafer Temperature Measurement Systems Market, by Output Type
- RTD Wafer Temperature Measurement Systems Market, by Application
- RTD Wafer Temperature Measurement Systems Market, by Installation Type
- RTD Wafer Temperature Measurement Systems Market, by Technology
- RTD Wafer Temperature Measurement Systems Market, by Temperature Range
- Americas RTD Wafer Temperature Measurement Systems Market
- Asia-Pacific RTD Wafer Temperature Measurement Systems Market
- Europe, Middle East & Africa RTD Wafer Temperature Measurement Systems Market
- Competitive Landscape
- ResearchAI
- ResearchStatistics
- ResearchContacts
- ResearchArticles
- Appendix
- List of Figures [Total: 32]
- List of Tables [Total: 1383 ]
Next Steps: Secure Your Comprehensive RTD Wafer Systems Insight
For a detailed exploration of the RTD wafer temperature measurement market-including in-depth industry analysis, comprehensive vendor profiles, and strategic roadmaps-reach out to Ketan Rohom, Associate Director, Sales & Marketing. Equip your organization with the insights and tools needed to make informed investment decisions, accelerate innovation, and secure a competitive advantage. Contact Ketan directly to obtain your full research report and begin charting your path to success.
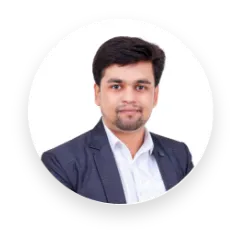
- When do I get the report?
- In what format does this report get delivered to me?
- How long has 360iResearch been around?
- What if I have a question about your reports?
- Can I share this report with my team?
- Can I use your research in my presentation?