Introduction to the Evolving Mixing Machine Landscape
The internal mixing machine remains at the core of rubber and plastic compounding, driving the performance and quality of final products across multiple industries. As manufacturers demand greater precision, consistency, and throughput, advances in machine design and process control have become critical differentiators. Over the past decade, mixing equipment has evolved from basic mechanical systems to sophisticated platforms featuring digital integration, adaptive control strategies, and enhanced safety protocols. This transition underscores the importance of investing in state-of-the-art machines that can accommodate a wide range of formulations while minimizing waste and downtime.
In today’s competitive environment, decision-makers must balance cost pressures with the need for innovation. Regulatory requirements and sustainability mandates are reshaping material formulations, placing new demands on mixers to handle energy-efficient processes and environmentally friendly compounds. Meanwhile, global supply chain complexities and evolving trade policies introduce additional challenges around part sourcing and logistics.
Against this backdrop, stakeholders require a concise yet comprehensive overview of the key forces influencing the internal mixing machine market. This executive summary consolidates recent developments, highlights emerging opportunities, and identifies strategic considerations to help leaders navigate the path ahead with confidence.
Transformative Shifts Redefining Mixing Equipment Performance
The mixing equipment ecosystem has witnessed several transformative shifts over the past few years. First, automation and digitalization have redefined operational benchmarks: robotic integration and smart monitoring now enable closed-loop control, predictive maintenance, and real-time quality assurance. As a result, throughput variability has declined while material characteristics remain tightly controlled.
Second, sustainability has emerged as a strategic imperative. Manufacturers are prioritizing energy-efficient systems that reduce carbon footprints; machines featuring advanced insulation, heat recovery, and servo-driven components now lead the pack. In parallel, environmental safety protocols are becoming increasingly stringent, driving demand for enclosed systems that minimize emissions and facilitate clean production.
Third, the rise of smart features-from IoT-enabled sensors to AI-driven analytics-has reshaped maintenance paradigms. Predictive maintenance algorithms can forecast component wear and schedule service proactively, reducing unplanned downtime. This technological shift not only enhances equipment reliability but also unlocks new opportunities for service-based revenue models.
Taken together, these trends are converging to establish a new performance frontier. As mixing platforms become smarter, leaner, and greener, the competitive landscape will reward suppliers who combine technological prowess with deep process expertise.
Cumulative Impact of United States Tariffs on Equipment Supply Chains
The implementation of new U.S. tariffs in 2025 has exerted a significant influence on equipment costs and supply chain strategies. Import duties on key components, including specialized alloys and precision drives, have prompted manufacturers to reevaluate sourcing and pricing structures. Many are exploring near-shoring options, engaging domestic machine builders to mitigate tariff exposure and streamline logistics.
Consequently, capital expenditure plans have shifted toward hybrid supply models that balance cost and risk. Organizations are negotiating long-term agreements with both international and local vendors to secure favorable terms and maintain production continuity. In some cases, companies are investing in modular machine designs that allow component substitution without major reengineering, thereby cushioning the impact of future trade policy changes.
Moreover, the tariff environment has accelerated consolidation in the supply chain. Smaller suppliers facing margin pressures are merging or forming strategic alliances to achieve economies of scale. At the same time, larger equipment manufacturers are leveraging their global footprints to distribute tariff burdens more evenly across regions.
Overall, the cumulative effect of the 2025 tariff adjustments has underscored the importance of agility, localized partnerships, and design flexibility in maintaining competitive advantage.
Key Segmentation Insights Across Materials, Methods and Technologies
Analysis by material type reveals distinct growth drivers: traditional elastomers continue to maintain baseline demand, while natural rubber holds firm in specialty applications. Synthetic rubber, including nitrile and styrene butadiene, captivates segments requiring chemical resistance and durability. Thermoplastics, with their versatile processing windows, further diversify machine utilization across industries.
When viewed through the lens of application industry, mixing machines experience heavy adoption in automotive manufacturing, especially for seals and tires that demand exacting compound homogeneity. Construction materials benefit from robust mixing platforms capable of handling high-viscosity blends, while consumer goods and medical applications increasingly rely on precise micro-mixing to ensure product safety and performance.
Processing method segmentation underscores the prevalence of batch processes-both large and small batch configurations-for custom compounders, contrasted with continuous processes favored by high-volume producers seeking minimal cycle interruptions and consistent quality.
Variations in technology level demonstrate a gradient of adoption: fully automatic systems featuring robotic integration and smart monitoring lead in high-throughput plants, whereas semi-automatic and manual operation units remain prevalent in smaller operations or niche production runs.
Evaluated by capacity range, high-capacity machines-especially heavy duty and industrial grade models-dominate large-scale manufacturing sites, while medium and low capacity units support more specialized or lower-volume requirements.
Finally, an innovation focus centered on energy efficiency and environmental safety drives investment in next-generation platforms, with IoT-enabled and predictive maintenance capabilities serving as pivotal differentiators.
This comprehensive research report categorizes the Rubber & Plastic Materials Internal Mixing Machine market into clearly defined segments, providing a detailed analysis of emerging trends and precise revenue forecasts to support strategic decision-making.
- Material Type
- Application Industry
- Processing Method
- Technology Level
- Capacity Range
- Innovation Focus
Key Regional Insights Shaping Equipment Deployment
In the Americas, robust demand for automotive and industrial rubber components spurs investment in cutting-edge mixing systems. Manufacturers in North and South America prioritize energy-efficient designs and local partnerships to mitigate recent trade and tariff uncertainties. The region’s well-developed aftermarket services network further enhances equipment uptime and total cost of ownership.
Within Europe, the Middle East and Africa, regulatory rigor around emissions and safety standards shapes purchasing decisions. European producers lead in adopting enclosed, low-emission mixers, while Middle Eastern and African markets are expanding capacity to support infrastructure growth. Cross-regional alliances blend European technological leadership with emerging-market manufacturing scale, creating diverse growth pockets.
Asia-Pacific remains the largest single market by volume, driven by automotive production in countries such as China and India and by the rise of consumer electronics in Southeast Asia. Rapid industrialization and government incentives for sustainable manufacturing accelerate the deployment of automation and smart monitoring solutions. Local machine builders are responding by offering tailored configurations that balance cost sensitivity with performance requirements.
This comprehensive research report examines key regions that drive the evolution of the Rubber & Plastic Materials Internal Mixing Machine market, offering deep insights into regional trends, growth factors, and industry developments that are influencing market performance.
- Americas
- Asia-Pacific
- Europe, Middle East & Africa
Key Company Insights and Competitive Dynamics
Leading original equipment manufacturers continue to drive innovation through strategic investments in research and development. In North America, Allied Mixing Solutions Ltd., Alpha Mixers Corporation, Beta Compound Engineering Ltd. and Premier Rubber Mixers Inc. are enhancing modular designs to support flexible capacity ranges. Dynamic Rubbers & Plastics Inc., RealMix Engineering Ltd. and Delta Mixers Group Inc. emphasize localized service networks that optimize uptime and lifecycle support.
European suppliers such as Brabender Technology GmbH, Bönnemann GmbH, Coperion GmbH, EuroMix Machinery GmbH, Lödige Process Technology GmbH and Schenck Process GmbH leverage advanced materials expertise and stringent safety certifications to lead growth in EMEA markets. They pair high-precision drives with smart monitoring modules that align with regional regulatory requirements.
In Asia-Pacific, Cubix Mixing Equipment Co., Fusion Technologies Inc. and NextGen Mixing Systems Inc. capitalize on high-volume automotive and consumer goods demand by delivering cost-effective continuous processing lines. Techno Mix Industries and Innovative Rubber Machinery Inc. are expanding local manufacturing footprints and service centers to address rapid industrialization.
Global Mix Solutions LLC, MasterMix Innovators LLC, Meridian Mixers Ltd., Integral Polymer Systems Ltd. and Kneader & Mixer Co. focus on niche segments such as smart features with IoT integration and predictive maintenance, forging partnerships with technology firms to accelerate digital transformation across all regions.
This comprehensive research report delivers an in-depth overview of the principal market players in the Rubber & Plastic Materials Internal Mixing Machine market, evaluating their market share, strategic initiatives, and competitive positioning to illuminate the factors shaping the competitive landscape.
- 360iResearch LLC
- Allied Mixing Solutions Ltd.
- Alpha Mixers Corporation
- Beta Compound Engineering Ltd.
- Brabender Technology GmbH
- Bönnemann GmbH
- Coperion GmbH
- Cubix Mixing Equipment Co.
- Delta Mixers Group Inc.
- Dynamic Rubbers & Plastics Inc.
- Entec Mixers Company Inc.
- EuroMix Machinery GmbH
- Fusion Technologies Inc.
- Global Mix Solutions LLC
- Horizon Mix Dynamics
- Innovative Rubber Machinery Inc.
- Integral Polymer Systems Ltd.
- Kneader & Mixer Co.
- Lödige Process Technology GmbH
- MasterMix Innovators LLC
- Meridian Mixers Ltd.
- NextGen Mixing Systems Inc.
- PlastComp Equipment Corp.
- PolyMix Technologies LLC
- Precision Polymer Mixers Inc.
- Premier Rubber Mixers Inc.
- RealMix Engineering Ltd.
- Ross Industries Inc
- Schenck Process GmbH
- Techno Mix Industries
Actionable Recommendations for Mixing Equipment Decision-Makers
Industry leaders must prioritize modularity and flexibility when specifying new mixing platforms. By selecting machines that support quick conversion between batch sizes and compounds, organizations can respond rapidly to changing customer requirements and regulatory shifts. Additionally, integrating predictive maintenance algorithms from the outset will reduce unexpected downtime and extend component lifecycles.
To counter supply chain volatility, executives should cultivate a balanced vendor portfolio that includes both global OEMs and regional specialists. Establishing consortia or cooperative agreements can further insulate operations from tariff fluctuations and raw material shortages.
Sustainability should serve as a guiding principle across capital investments. Companies can achieve significant energy savings by migrating to servo-driven drives and implementing heat recovery systems. Environmental safety goals can be met by adopting enclosed mixer designs equipped with high-efficiency particulate filters and solvent recovery modules.
Finally, embracing digital twins and advanced analytics will enable real-time insights into process performance. Cross-functional teams can leverage this data to optimize compound recipes, reduce waste, and accelerate time to market. Learning from early adopters in high-growth regions will help smaller operations scale these innovations effectively.
Explore AI-driven insights for the Rubber & Plastic Materials Internal Mixing Machine market with ResearchAI on our online platform, providing deeper, data-backed market analysis.
Ask ResearchAI anything
World's First Innovative Al for Market Research
Conclusion: Positioning for Long-Term Competitive Advantage
The internal mixing machine market stands at the intersection of technological advancement, regulatory evolution, and shifting trade dynamics. Throughout this summary, we have highlighted the major trends transforming equipment performance-from automation and smart features to the impacts of new tariffs and regional market drivers.
As the landscape continues to evolve, success will depend on adopting a holistic strategy that balances operational efficiency, sustainability, and resilience. Companies that invest in modular, energy-efficient machines equipped with digital monitoring capabilities will not only meet current production requirements but also position themselves to capitalize on future growth opportunities.
In an era defined by rapid innovation and global uncertainty, the ability to adapt quickly and leverage data-driven insights will be the ultimate competitive advantage. With a clear roadmap and actionable guidance, industry leaders can navigate these changes confidently and drive long-term value.
This section provides a structured overview of the report, outlining key chapters and topics covered for easy reference in our Rubber & Plastic Materials Internal Mixing Machine market comprehensive research report.
- Preface
- Research Methodology
- Executive Summary
- Market Overview
- Market Dynamics
- Market Insights
- Cumulative Impact of United States Tariffs 2025
- Rubber & Plastic Materials Internal Mixing Machine Market, by Material Type
- Rubber & Plastic Materials Internal Mixing Machine Market, by Application Industry
- Rubber & Plastic Materials Internal Mixing Machine Market, by Processing Method
- Rubber & Plastic Materials Internal Mixing Machine Market, by Technology Level
- Rubber & Plastic Materials Internal Mixing Machine Market, by Capacity Range
- Rubber & Plastic Materials Internal Mixing Machine Market, by Innovation Focus
- Americas Rubber & Plastic Materials Internal Mixing Machine Market
- Asia-Pacific Rubber & Plastic Materials Internal Mixing Machine Market
- Europe, Middle East & Africa Rubber & Plastic Materials Internal Mixing Machine Market
- Competitive Landscape
- ResearchAI
- ResearchStatistics
- ResearchContacts
- ResearchArticles
- Appendix
- List of Figures [Total: 28]
- List of Tables [Total: 546 ]
Call-to-Action: Partner with Our Expert to Access In-Depth Market Intelligence
Ready to gain deeper insights and drive strategic decisions with a comprehensive market research report? Contact Ketan Rohom, Associate Director, Sales & Marketing at 360iResearch, to learn how this detailed analysis can inform your next investment in internal mixing technologies. Secure your copy today and empower your organization to lead in the evolving mixing equipment landscape.
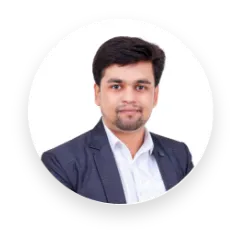
- When do I get the report?
- In what format does this report get delivered to me?
- How long has 360iResearch been around?
- What if I have a question about your reports?
- Can I share this report with my team?
- Can I use your research in my presentation?