The Rubber Twin-Screw Extrusion Equipment Market size was estimated at USD 345.67 million in 2024 and expected to reach USD 362.83 million in 2025, at a CAGR 4.87% to reach USD 460.00 million by 2030.

Unveiling the Dynamics of Rubber Twin-Screw Extrusion Technology
Rubber twin-screw extrusion stands at the forefront of material processing innovation, delivering unparalleled mixing precision and throughput stability. This technology enables manufacturers to blend elastomers with reinforcing agents and additives in a continuous process that optimizes product performance and reduces cycle times.
In this dynamic environment, decision-makers are navigating changing raw material compositions, regulatory pressures, and evolving customer expectations. As end-use applications expand from automotive seals to advanced packaging solutions, equipment providers must adapt designs that meet stringent quality standards while enhancing operational efficiency.
This executive summary distills the critical developments shaping the rubber twin-screw extrusion equipment landscape, offering insights into market drivers, segmentation trends, and strategic imperatives. It serves as a roadmap for executives seeking to align product portfolios with emerging industry requirements and to capitalize on opportunities for growth.
Navigating Paradigm Shifts Reshaping Equipment Demand
Over the past several years, the rubber extrusion landscape has undergone transformative shifts driven by the convergence of digitalization and sustainability imperatives. Advanced control architectures now enable real-time monitoring of shear rates, torque, and temperature profiles, empowering operators to optimize processing windows and reduce scrap rates. Integration of artificial intelligence and machine learning algorithms has further refined predictive maintenance capabilities, minimizing unplanned downtime and boosting overall equipment effectiveness.
Concurrently, increasing regulatory scrutiny on volatile organic compound emissions and energy consumption has prompted OEMs to engineer energy-efficient drive systems and closed-loop devolatilization modules. Manufacturers are experimenting with bio-based feedstocks and recycled elastomer formulations, pushing twin-screw platforms to accommodate novel material rheologies while maintaining consistent performance. This confluence of digital transformation and ecological responsibility is reshaping procurement criteria across end-user industries, compelling suppliers to deliver modular, scalable extrusion lines that support rapid changeovers and minimized environmental footprint.
As market participants navigate these paradigm shifts, they must balance capital investment cycles against the imperative to modernize processing assets. Forward-looking equipment providers that design systems for seamless software integration, remote diagnostics, and sustainable operation will unlock new tiers of value for customers and establish lasting competitive advantage.
Evaluating the Ripple Effects of U.S. Tariff Measures
The imposition of cumulative U.S. tariffs set for full effect in 2025 has introduced an additional layer of complexity for equipment manufacturers and end users alike. Duties on imported extrusion components and finished machinery have elevated total landed costs, prompting procurement teams to reassess global sourcing strategies. Suppliers reliant on overseas fabrication are exploring nearshoring options or partnerships with domestic fabricators to mitigate import levies and secure price stability.
The tariff environment has also driven consolidation of supply chains, as buyers seek to leverage volume agreements and integrated service offerings to offset elevated duty expenses. Localized manufacturing hubs have gained traction as OEMs invest in regional assembly facilities, reducing exposure to cross-border cost fluctuations while accelerating delivery timelines. This shift toward distributed production nodes is complemented by collaborative service networks that deliver installation, commissioning, and aftermarket support closer to the customer’s site.
Despite these headwinds, the tariff landscape is fostering innovation in contract structuring and financing models. Equipment vendors are introducing pay-per-use arrangements and extended leasing solutions that buffer capital outlays from duty impacts. By realigning go-to-market approaches and strengthening regional footprints, the industry is navigating duty pressures while preserving capacity to meet growing demand across key end-use segments.
Decoding Market Segmentation for Strategic Clarity
A nuanced understanding of equipment demand emerges when examining segmentation across machine type, application, end-user industry, material type, and screw configuration. In terms of machine architecture, co-rotating and counter-rotating platforms define the competitive landscape, with both variants available in electric and hydraulic drive options. Electric models deliver consistent torque and reduced maintenance intervals, whereas hydraulic systems offer high peak torque for specialized compounding tasks. End users select the configuration that aligns with throughput targets, energy efficiency goals, and serviceability requirements.
Application-based differentiation further delineates market opportunities. Hose production leverages Ethylene Propylene Diene Monomer Rubber and Nitrile Rubber compounds, demanding extrusion lines capable of precise pressure control and continuous vulcanization integration. Profile extrusion also relies on EPDM and NBR formulations, calling for equipment that ensures dimensional accuracy and surface finish. Sheet manufacturing of EPDM and Styrene Butadiene Rubber necessitates wide-die capabilities and robust degassing sections, while tire compounding, using Natural Rubber and SBR blends, requires high-shear screw elements and advanced homogenization zones.
End-user industries shape equipment specifications through unique requirements. Automotive components such as interior trims, seals, and tires impose tight tolerances, leading OEMs to prioritize systems with enhanced control loops and automated recipe management. In construction, gaskets and seals demand corrosion-resistant feeders and steady-state processing, whereas consumer goods segments focus on footwear and sporting goods, valuing gentle mixing and color consistency. The packaging sector’s flexible packaging and sleeves applications press for rapid material changeovers and minimal cross-contamination.
Material-centric segmentation underscores the interplay between elastomer chemistry and processing parameters. EPDM applications span hose, profile, and sheet production, highlighting the need for versatile screw designs. Natural Rubber, integral to sheet and tire manufacturing, introduces high viscosity challenges, necessitating reinforced barrel assemblies. Nitrile Rubber’s use in hose and seal extrusion calls for wear-resistant screw coatings, while SBR in sheet and tire lines requires precise temperature management to avoid scorch.
Screw configuration analysis reveals the strategic value of modular versus non-modular designs. Modular systems, featuring L/D ratios of 20:1, 24:1, and 30:1, offer flexibility to reconfigure processing sections, adapt to new formulations, and support capacity scaling. Non-modular platforms, available in L/D 20:1 and 28:1 variants, provide simplicity and lower capital expenditure for high-volume, dedicated production runs. Lifecycle costs, downtime implications, and product mix determine the optimal screw configuration for each application scenario.
This comprehensive research report categorizes the Rubber Twin-Screw Extrusion Equipment market into clearly defined segments, providing a detailed analysis of emerging trends and precise revenue forecasts to support strategic decision-making.
- Machine Type
- Application
- End-User Industry
- Material Type
- Screw Configuration
Uncovering Regional Drivers Across Key Geographies
The Americas region drives significant demand for rubber twin-screw extrusion lines, underpinned by robust automotive production in North America and expanding infrastructure projects in South America. Original equipment manufacturers and tier suppliers in the United States and Mexico are investing in localized manufacturing hubs to streamline supply chains and accelerate delivery to key markets. Brazil’s growing construction sector further stimulates equipment orders, while Canada’s emphasis on energy-efficient processing bolsters interest in advanced drive technologies.
Within Europe, Middle East and Africa, Western European markets leverage stringent environmental regulations to pilot next-generation extrusion systems integrating closed-loop devolatilization and carbon footprint monitoring. Germany, Italy, and France stand out for their precision engineering demands, driving innovation in high-torque, servo-driven platforms. The Middle East’s infrastructure boom, particularly in the Gulf Cooperation Council countries, fuels orders for seal and gasket extrusion lines, while South Africa’s consumer goods and packaging industries spur adoption of compact, versatile equipment.
Asia-Pacific remains a powerhouse for twin-screw extrusion growth, with China leading through sustained investment in automotive and industrial rubber processing. Indian market participants are modernizing aging machinery fleets, embracing electric drive solutions and remote monitoring capabilities. Japan and South Korea continue to push the envelope on high-speed, precision compounding systems, catering to electronics and medical device sectors. Southeast Asian emerging economies, buoyed by foreign direct investment, are rapidly scaling capacity for hose, sheet, and tire extrusion, driving a diverse mix of equipment configurations and service offerings.
This comprehensive research report examines key regions that drive the evolution of the Rubber Twin-Screw Extrusion Equipment market, offering deep insights into regional trends, growth factors, and industry developments that are influencing market performance.
- Americas
- Europe, Middle East & Africa
- Asia-Pacific
Profiling Industry Leaders and Strategic Imperatives
A handful of global and regional players dominate the rubber twin-screw extrusion equipment arena, each carving distinct competitive positions. One leading supplier has built its reputation on modular designs that enable rapid configuration changes, supported by an expansive service network for maintenance and spare parts. Another innovator specializes in high-performance screw metallurgy and barrel coatings, addressing wear challenges inherent to abrasive compound processing.
Strategic partnerships have become a cornerstone of differentiation. Several OEMs have allied with control system providers to embed digital twins and remote diagnostics into their platforms, offering real-time optimization and predictive maintenance capabilities. Recent acquisitions of local fabrication shops have expanded regional footprints, allowing prominent vendors to deliver faster lead times and tailored commissioning services in key markets.
Technology roadmaps reflect a sharp focus on energy efficiency and sustainability. Industry leaders are piloting extrusion lines equipped with regenerative drive systems and onboard devolatilization loops that capture and recycle process condensates. Service offerings have also evolved; proactive maintenance contracts, operator training programs, and upgrade kits for legacy equipment ensure continuous value delivery and strengthen customer relationships over the equipment lifecycle.
This comprehensive research report delivers an in-depth overview of the principal market players in the Rubber Twin-Screw Extrusion Equipment market, evaluating their market share, strategic initiatives, and competitive positioning to illuminate the factors shaping the competitive landscape.
- The Japan Steel Works, Ltd.
- KraussMaffei SE
- Coperion GmbH
- Leistritz Extrusion GmbH
- Davis-Standard, LLC
- Farrel Pomini S.p.A.
- Kobe Steel, Ltd.
- Milacron LLC
Actionable Strategies to Enhance Competitive Advantage
To thrive amid rising competition and evolving customer expectations, industry leaders must adopt a multifaceted approach. Prioritizing digital transformation across equipment portfolios enhances value propositions, reduces total cost of ownership, and unlocks new revenue streams via analytics-driven service models. Investing in modular platforms and open architecture controls enables rapid scalability and seamless integration of future upgrades.
Sustainability will remain a differentiator, driving demand for systems that support bio-based elastomers, recycled feedstocks, and energy-saving drive technologies. Collaborations with material suppliers and research institutes can accelerate the validation of novel elastomer formulations and processing techniques, shortening time-to-market for innovative products. Equally important is the cultivation of after-sales service capabilities; structured training programs, remote support channels, and performance-based maintenance agreements foster deeper customer loyalty and recurring revenue.
Finally, executives should explore strategic alliances and targeted acquisitions to broaden geographic reach and fill capability gaps. Whether through joint ventures in emerging economies or selective takeovers of specialized technology firms, expanding the ecosystem of partners and competencies will fortify market position and ensure resilience in the face of shifting trade and regulatory landscapes.
Methodological Rigor Ensuring Analytical Depth
This study synthesizes insights through a rigorous, two-pronged research methodology. Primary research involved in-depth interviews with key stakeholders, including equipment OEM executives, end-user technical managers, and channel partners. These discussions provided nuanced perspectives on emerging requirements, technology adoption roadblocks, and service expectations.
Secondary research drew on an extensive review of industry publications, patent databases, regulatory filings, and trade association reports. Financial statements and corporate announcements were analyzed to map strategic initiatives, technology investments, and partnership trajectories. Market data were validated through triangulation, cross-referencing multiple sources to ensure accuracy and reliability.
Quantitative analysis incorporated segmentation breakdowns by machine type, application, industry vertical, material type, and screw configuration. Regional demand projections and tariff impact assessments were developed through bottom-up modeling, based on equipment shipment data and end-user consumption trends. The study’s qualitative component captured competitive dynamics, go-to-market strategies, and customer satisfaction benchmarks.
To uphold methodological consistency, all findings underwent peer review by domain experts and were further refined during validation workshops with industry participants. This structured approach ensures that conclusions are grounded in empirical evidence and actionable for decision-makers.
Explore AI-driven insights for the Rubber Twin-Screw Extrusion Equipment market with ResearchAI on our online platform, providing deeper, data-backed market analysis.
Ask ResearchAI anything
World's First Innovative Al for Market Research
Synthesis of Insights Guiding Future Decisions
The convergence of digital capabilities, sustainability mandates, and geopolitical factors has reshaped the rubber twin-screw extrusion equipment market. Stakeholders must navigate an increasingly complex environment marked by shifting trade policies, evolving material science, and escalating performance expectations.
Strategic clarity emerges through granular segmentation analysis, revealing how machine architectures, application requirements, end-use industries, material properties, and screw designs interact to define equipment specifications. Regional insights highlight the divergent growth levers and regulatory frameworks that equipment suppliers must address to capture market share.
Leading companies differentiate through integrated service models, partnerships for technological advancement, and unwavering focus on energy efficiency and lifecycle support. Meanwhile, finance and procurement teams are recalibrating sourcing strategies in response to tariff regimes, underscoring the importance of flexible manufacturing footprints.
Coloring these trends are the actionable recommendations offered for digital transformation, modular design adoption, sustainability alignment, and strategic partnership formation. Taken together, these insights equip executives with the foresight to align capital investment, product development, and commercial strategies with the demands of tomorrow’s rubber processing landscape.
This section provides a structured overview of the report, outlining key chapters and topics covered for easy reference in our Rubber Twin-Screw Extrusion Equipment market comprehensive research report.
- Preface
- Research Methodology
- Executive Summary
- Market Overview
- Market Dynamics
- Market Insights
- Cumulative Impact of United States Tariffs 2025
- Rubber Twin-Screw Extrusion Equipment Market, by Machine Type
- Rubber Twin-Screw Extrusion Equipment Market, by Application
- Rubber Twin-Screw Extrusion Equipment Market, by End-User Industry
- Rubber Twin-Screw Extrusion Equipment Market, by Material Type
- Rubber Twin-Screw Extrusion Equipment Market, by Screw Configuration
- Americas Rubber Twin-Screw Extrusion Equipment Market
- Europe, Middle East & Africa Rubber Twin-Screw Extrusion Equipment Market
- Asia-Pacific Rubber Twin-Screw Extrusion Equipment Market
- Competitive Landscape
- ResearchAI
- ResearchStatistics
- ResearchContacts
- ResearchArticles
- Appendix
- List of Figures [Total: 26]
- List of Tables [Total: 944 ]
Secure Expert Intelligence to Drive Growth
To explore the full strategic insights and detailed analysis presented in this market research report, reach out to Ketan Rohom, Associate Director, Sales & Marketing. He can guide you through the scope of findings, elaborate on tailored opportunities for your organization, and arrange access to proprietary data sets. Engage directly with an experienced market advisor to ensure that you leverage these intelligence assets for competitive advantage. Secure your copy of the comprehensive report today and position your business to capitalize on emerging trends and disruptive forces within the rubber twin-screw extrusion equipment sector.
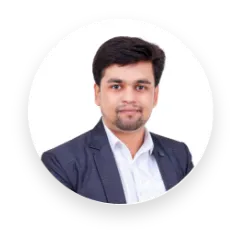
- How big is the Rubber Twin-Screw Extrusion Equipment Market?
- What is the Rubber Twin-Screw Extrusion Equipment Market growth?
- When do I get the report?
- In what format does this report get delivered to me?
- How long has 360iResearch been around?
- What if I have a question about your reports?
- Can I share this report with my team?
- Can I use your research in my presentation?