Executive Summary: Introduction to Selective Laser Sintering Market Dynamics
Selective Laser Sintering (SLS) has redefined additive manufacturing by enabling intricate geometries, robust mechanical properties, and rapid production without the constraints of traditional tooling. By fusing powdered materials layer by layer under a focused laser beam, SLS empowers engineers and designers to iterate concepts in real time, accelerating development cycles and optimizing performance. Industries ranging from aerospace to medical devices have embraced this technology to produce lightweight structural components, customized surgical implants, and functional prototypes that mirror end-use conditions.
As the pace of innovation intensifies, SLS service providers are enhancing machine throughput, refining powder recyclability, and expanding material portfolios to include high-temperature polymers and specialized metal powders. Concurrent advancements in process automation and digital workflow integration have streamlined production from file to finished part, reducing manual intervention and quality variances. Decision-makers now evaluate SLS not merely as a prototyping tool but as a viable solution for short-run manufacturing and on-demand spare parts, unlocking new revenue streams and reshoring opportunities.
This report introduces the critical dynamics shaping the SLS 3D printing landscape, exploring how evolving material science, regulatory standards, and global trade policies converge to influence strategic investments. The subsequent sections deliver deep insights into market shifts, tariff impacts, segmentation nuances, regional hotspots, competitive benchmarks, and actionable strategies for industry leaders.
Emerging Technological and Market Shifts in SLS 3D Printing
The SLS 3D printing landscape is undergoing transformative shifts driven by technological breakthroughs and evolving customer expectations. Laser power enhancements and multi-laser configurations now deliver faster sintering speeds and larger build volumes, enabling complex assemblies and high throughput. Concurrently, the integration of artificial intelligence in process control has improved part consistency, predictive maintenance, and yield optimization, reducing scrap rates and operational costs.
In material development, novel composites and high-performance polymers have extended SLS applications into extreme environments requiring thermal resistance, chemical stability, and wear resistance. Metal powder sintering solutions have matured, supporting aerospace-grade aluminum, stainless steel, and titanium alloys that meet stringent certification requirements. Software platforms now offer simulation of powder flow, thermal gradients, and shrinkage, allowing engineers to refine designs virtually before committing material.
Sustainability considerations have catalyzed the use of recycled powder streams and energy-efficient lasers, while circular economy frameworks encourage cradle-to-cradle strategies for end-of-life parts. Partnerships between service providers, OEMs, and materials specialists are fostering co-development of application-specific alloys and polymer blends. At the same time, increased demand for customization and decentralized production is paving the way for cloud-based order management, on-demand manufacturing hubs, and agile supply networks that can respond to market volatility.
Assessing the Cumulative Impact of 2025 US Tariffs on SLS Supply Chains
The introduction of new US tariffs on SLS-related imports in 2025 has compounded cost pressures across the supply chain. Enhanced duty rates on high-performance polymers, composite powders, and precision laser systems have elevated raw material costs by up to 15 percent, prompting service providers to re-evaluate sourcing strategies. Metal powder manufacturers face similar constraints, leading to price adjustments for aluminum, stainless steel, and titanium feedstocks.
These measures have incentivized near-shoring initiatives, with several key component producers relocating or partnering with North American facilities to mitigate duty impacts and reduce lead times. Domestic powder recyclers are scaling operations to supply certified recycled material, while machine OEMs are localizing final assembly and service centers to preserve competitive pricing structures.
In response, many SLS service bureaus have implemented flexible pricing models, passing incremental costs to customers through tiered service packages that emphasize faster turnaround or enhanced post-processing. They are also negotiating volume-based agreements with raw material suppliers and exploring alternative polymer blends with lower duty classifications. Strategic alliances among equipment vendors, materials formulators, and research institutions are accelerating qualification of tariff-friendly feedstocks without compromising performance standards.
Key Market Segmentation Insights Across Applications, Materials, and More
Based on Industry Applications, the market is studied across Aerospace Parts, Automotive Components, Consumer Goods, Electronics Prototypes, Industrial Equipment, and Medical Devices, with the Medical Devices segment further explored through Dental, Orthopedics, and Surgical Implants to capture specialized regulatory and biocompatibility requirements. Based on Material Specifications, the study covers Composite Powders, High Performance Polymers, Metal Powders, and Thermoplastic Powders, reflecting the critical role of materials in defining mechanical strength, thermal resistance, and cost efficiency; Metal Powders are dissected into Aluminum Powders, Stainless Steel Powders, and Titanium Powders to address density, corrosion resistance, and certification nuances.
In terms of Production Scale, the research differentiates Mass Production, Prototyping, and Short Run Manufacturing, noting that Mass Production subdivides into Batch Processing and Volume Production to highlight automation levels and throughput needs. Based on Design Complexity, market analysis examines Customization Needs, Intricate Detailing, and Simple Geometry, with Customization Needs broken down further into Dimensional Accuracy and Surface Finish to emphasize quality tolerances and post-processing demands.
When evaluating Application Purpose, the framework includes End Use Production, Research And Development, and Spare Parts Manufacturing, drilling into End Use Production through Aesthetic Components and Functional Parts to distinguish cosmetic requirements from performance criteria. Based on Operational Efficiency, segments such as Cost Optimization, Process Automation, and Quick Turnaround are addressed, with Process Automation detailing Integration Solutions and Workflow Optimization that underpin digital thread implementation. Finally, Quality Standards are explored through Certification Processes, Quality Assurance, and Regulatory Compliant, dissecting Regulatory Compliant into FDA Clearance and ISO Compliance, while Material Performance segments-Electrical Conductivity, Mechanical Strength, Thermal Resistance, and Wear Resistance-are rounded out by an examination of Mechanical Strength’s Impact Resistance and Tensile Strength subcategories.
This comprehensive research report categorizes the Selective Laser Sintering 3D Printing Services market into clearly defined segments, providing a detailed analysis of emerging trends and precise revenue forecasts to support strategic decision-making.
- Industry Applications
- Material Specifications
- Production Scale
- Design Complexity
- Application Purpose
- Operational Efficiency
- Quality Standards
- Material Performance
Key Regional Insights on Demand Drivers and Infrastructure
In the Americas, established aerospace clusters in the United States and Canada drive demand for high-performance SLS components, while on-shoring trends bolster investments in domestic powder recycling and post-processing facilities. Brazil and Mexico are emerging as cost-effective hubs for short-run manufacturing, leveraging free-trade zones and proximity to automotive OEMs.
Europe, Middle East & Africa presents a diversified landscape where Germany, the UK, and France lead technological adoption for industrial equipment and medical device sintering, supported by robust regulatory frameworks. The Middle East is piloting additive factories for oil and gas maintenance parts, whereas South African service bureaus focus on rapid prototyping for mining and infrastructure applications.
Asia-Pacific stands out as a high-growth region propelled by China’s expanding aerospace and consumer electronics sectors, Japan’s advanced materials research, and South Korea’s electronics prototyping ecosystem. India and Southeast Asian nations are investing in skill development and partnerships to scale short-run production, targeting both local consumption and export markets.
This comprehensive research report examines key regions that drive the evolution of the Selective Laser Sintering 3D Printing Services market, offering deep insights into regional trends, growth factors, and industry developments that are influencing market performance.
- Americas
- Asia-Pacific
- Europe, Middle East & Africa
Key Company Profiles and Competitive Benchmarking in the SLS Space
The competitive landscape comprises specialized SLS service bureaus, machine OEMs, and materials innovators. Leading the charge are Advanced SLS Innovations Corp, Direct SLS Manufacturing LLC, EcoSinter Innovations Ltd, Elite Sintering Technologies Inc, Fusion Sinter 3D Services Inc, Fusion SLS Manufacturing Ltd, Integrated SLS Systems Corp, Laser Precision Sintering Ltd, Laser Sinter Manufacturing Corp, Laser Sinter Tech Inc, and Laser Sintered Solutions Inc, each distinguished by advanced automation, proprietary materials, or turnkey production hubs. Complementing this are Laser Sintering Experts Inc, LaserFab Technologies Inc, NexPrint SLS Solutions LLC, NextGen SLS Industries Inc, PhotonSinter Solutions LLC, Pioneer SLS Industries LLC, Precision Laser Sintering Corp, Precision Sintering Enterprises Ltd, Premier Laser Sinter Corp, ProSinter Dynamics LLC, Selective Sinter Solutions LLC, SinterCraft Solutions Ltd, SinterLine Technologies LLC, SinterSphere Solutions LLC, SinterTech Manufacturing LLC, SinterWave Technologies Inc, SLS Precision Manufacturing LLC, Summit SLS Technologies Ltd, and UltraSinter Manufacturing Corp, notable for regional footprints, customized service offerings, and collaborative R&D initiatives. These players are investing in capacity expansion, certification accreditations, and digital platforms to capture growing demand.
This comprehensive research report delivers an in-depth overview of the principal market players in the Selective Laser Sintering 3D Printing Services market, evaluating their market share, strategic initiatives, and competitive positioning to illuminate the factors shaping the competitive landscape.
- Advanced SLS Innovations Corp
- Direct SLS Manufacturing LLC
- EcoSinter Innovations Ltd
- Elite Sintering Technologies Inc
- Fusion Sinter 3D Services Inc
- Fusion SLS Manufacturing Ltd
- Integrated SLS Systems Corp
- Laser Precision Sintering Ltd
- Laser Sinter Manufacturing Corp
- Laser Sinter Tech Inc
- Laser Sintered Solutions Inc
- Laser Sintering Experts Inc
- LaserFab Technologies Inc
- NexPrint SLS Solutions LLC
- NextGen SLS Industries Inc
- PhotonSinter Solutions LLC
- Pioneer SLS Industries LLC
- Precision Laser Sintering Corp
- Precision Sintering Enterprises Ltd
- Premier Laser Sinter Corp
- ProSinter Dynamics LLC
- Selective Sinter Solutions LLC
- SinterCraft Solutions Ltd
- SinterLine Technologies LLC
- SinterSphere Solutions LLC
- SinterTech Manufacturing LLC
- SinterWave Technologies Inc
- SLS Precision Manufacturing LLC
- Summit SLS Technologies Ltd
- UltraSinter Manufacturing Corp
Actionable Recommendations for Industry Leaders to Navigate SLS Market Dynamics
To secure a leadership position, industry executives should prioritize diversifying material supply chains by qualifying multiple polymer and metal powder suppliers, thereby mitigating tariff-induced risks while sustaining innovation in material performance. Investing in process automation and digital twin technologies can further enhance throughput, traceability, and quality assurance, enabling real-time monitoring of sintering parameters and predictive maintenance.
Collaborative partnerships with research institutions and certification bodies will accelerate approval cycles for medical and aerospace applications, unlocking higher-margin opportunities. Implementing circular economy principles-such as certified powder recapture and closed-loop recycling-will reduce raw material expenditures and reinforce sustainability credentials.
Leaders should also adopt modular production footprints that combine centralized high-volume hubs with decentralized micro-factories, addressing regional lead-time demands and customized on-demand services. Finally, embracing advanced data analytics to forecast maintenance needs, optimize build orientation, and refine post-processing workflows will drive continuous improvement and cost competitiveness.
Explore AI-driven insights for the Selective Laser Sintering 3D Printing Services market with ResearchAI on our online platform, providing deeper, data-backed market analysis.
Ask ResearchAI anything
World's First Innovative Al for Market Research
Conclusion: Steering Future Success in SLS 3D Printing Sector
Selective Laser Sintering continues to redefine manufacturing paradigms by marrying design freedom with robust material properties and agile production models. As technology converges with digitalization, the sector is poised to expand beyond prototyping into mainstream serial manufacturing and on-demand supply networks. Navigating this evolution requires a strategic blend of material innovation, tariff-resilient sourcing, automation investments, and regulatory foresight.
By aligning operational capabilities with emerging application requirements-from aerospace and medical implants to electronics enclosures-organizations can capture premium segments and diversify revenue streams. The interplay of regional infrastructure, sustainability mandates, and collaborative ecosystems will shape the competitive battleground in the years ahead.
This section provides a structured overview of the report, outlining key chapters and topics covered for easy reference in our Selective Laser Sintering 3D Printing Services market comprehensive research report.
- Preface
- Research Methodology
- Executive Summary
- Market Overview
- Market Dynamics
- Market Insights
- Cumulative Impact of United States Tariffs 2025
- Selective Laser Sintering 3D Printing Services Market, by Industry Applications
- Selective Laser Sintering 3D Printing Services Market, by Material Specifications
- Selective Laser Sintering 3D Printing Services Market, by Production Scale
- Selective Laser Sintering 3D Printing Services Market, by Design Complexity
- Selective Laser Sintering 3D Printing Services Market, by Application Purpose
- Selective Laser Sintering 3D Printing Services Market, by Operational Efficiency
- Selective Laser Sintering 3D Printing Services Market, by Quality Standards
- Selective Laser Sintering 3D Printing Services Market, by Material Performance
- Americas Selective Laser Sintering 3D Printing Services Market
- Asia-Pacific Selective Laser Sintering 3D Printing Services Market
- Europe, Middle East & Africa Selective Laser Sintering 3D Printing Services Market
- Competitive Landscape
- ResearchAI
- ResearchStatistics
- ResearchContacts
- ResearchArticles
- Appendix
- List of Figures [Total: 32]
- List of Tables [Total: 730 ]
Purchase the Full Market Research Report with Ketan Rohom
To gain comprehensive insights and actionable data on the SLS 3D printing market, request your copy of the full report by contacting Ketan Rohom, Associate Director, Sales & Marketing. Ketan will guide you through tailored research offerings, answer specific inquiries, and facilitate immediate access to strategic intelligence designed to inform investment decisions and competitive strategies.
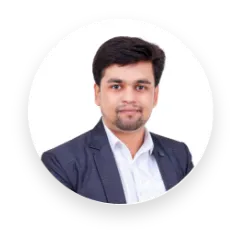
- When do I get the report?
- In what format does this report get delivered to me?
- How long has 360iResearch been around?
- What if I have a question about your reports?
- Can I share this report with my team?
- Can I use your research in my presentation?