Setting the Stage for Chamber Parts Cleaning and Coatings Excellence
The semiconductor industry’s relentless pursuit of smaller feature sizes and higher production yields hinges on the integrity of chamber parts cleaning and coatings. These critical processes ensure the longevity and performance of chambers used in deposition and etch equipment, safeguarding the production of advanced logic, memory, and power devices. As contamination control standards tighten and process windows narrow, manufacturers must adopt innovative cleaning chemistries and coating solutions to meet the demands of next-generation fabrication nodes.
This executive summary distills the latest market intelligence, examining the forces reshaping the landscape and highlighting the strategic levers that will define success. Through a rigorous analysis of technology shifts, regulatory influences, and competitive maneuvers, the summary offers a clear view of how chamber parts cleaning and coating providers can anticipate customer needs and capture growth. By focusing on key segmentation variables, regional dynamics, and the evolving tariff environment, decision-makers will gain a coherent framework to guide investment and operational priorities in the months ahead.
Revolutionary Trends Reshaping Semiconductor Cleaning and Coating
Rapid advancements in materials science have propelled new cleaning chemistries and coating formulations into the spotlight. As device architectures evolve toward three-dimensional structures and ultrathin films, traditional wet cleaning techniques face limitations in removing sub-nanometer residues. Consequently, plasma-based and hybrid dry-wet processes are gaining traction, delivering superior contamination control while minimizing damage to delicate chamber surfaces.
Concurrently, heightened environmental regulations have prompted equipment makers and service providers to adopt greener chemistries and closed-loop recycling systems. The industry’s commitment to sustainable practices has driven the development of low-toxicity cleaning agents and solvent recovery units, reducing both chemical waste and operational costs. This shift aligns with broader corporate sustainability goals, reinforcing the case for investments in eco-friendly process lines.
Moreover, digitalization and automation are transforming cleaning and coating workflows. Real-time monitoring powered by machine learning algorithms enables predictive maintenance of chamber components, while robotic handling ensures consistent application of anti-stiction and passivation coatings. These innovations not only enhance throughput but also reduce human error, bolstering yield and supporting the push toward fully autonomous fabs.
Navigating the Ripple Effects of 2025 US Tariff Policies
The introduction of expanded tariff brackets on electronic materials and equipment has created a complex operating environment for suppliers and fabricators. Producers reliant on imports of specialized cleaning compounds and coating precursors face elevated cost structures, forcing them to re-evaluate their sourcing strategies. In response, some providers have shifted production to domestic or alternative low-tariff jurisdictions to mitigate margin erosion.
These tariff measures have also accelerated efforts to diversify supply chains. OEMs and foundries are forging partnerships with regional chemical producers to secure uninterrupted access to critical materials. Such collaborations not only safeguard against trade disruptions but also foster co-development of tailored cleaning solutions that meet specific process requirements.
Furthermore, the increased cost pressure has prompted companies to optimize batch sizes and revisit inventory management practices. Consolidating orders and negotiating volume-based contracts have become essential tactics to absorb tariff impacts. At the same time, organizations are intensifying lobbying efforts and trade advocacy to influence policy revisions that support semiconductor manufacturing competitiveness.
Unveiling Critical Segments Driving Market Dynamics
A nuanced understanding of segment-level dynamics reveals divergent growth drivers across chamber types, cleaning methodologies, and coating applications. Within deposition and etch chambers, demand for advanced cleaning has intensified, particularly in processes employing chemical vapor deposition and physical vapor deposition techniques. The intricate geometries and layered materials in these chambers necessitate cleaning regimens that can penetrate micro-trenches while preserving surface integrity.
Different cleaning technologies address varied contamination challenges. Dry plasma methods excel in removing organic residues without introducing liquid byproducts, whereas wet chemistries remain indispensable for dissolving inorganic particulates. Between these extremes, hybrid processes combine plasma activation with engineered solvents to target mixed‐composition films, striking a balance between efficacy and equipment preservation.
Coating solutions have similarly diversified. Anti-stiction formulations prevent chamber components from adhering under vacuum, while passivation coatings shield surfaces from corrosive species during high-energy etch cycles. Meanwhile, thin film coatings tailored for metal or ceramic substrates deliver wear resistance and thermal stability, extending component life and reducing maintenance cycles.
Wafer size further influences cleaning and coating requirements. Transitioning from 200 mm to 300 mm platforms amplifies surface area and contamination risk, driving the adoption of scalable process modules designed for uniform coverage. End users exhibit distinct preferences as well. High-volume foundries prioritize throughput and repeatability, integrated device manufacturers seek turnkey process integration, and outsourced assembly and test centers emphasize cost-effective maintenance schedules.
Material composition impacts both cleaning efficacy and coating adhesion. Ceramic parts demand acid-resistant treatments, metal components require anti-oxidation layers, and quartz elements benefit from chemically inert thin films. Finally, the booming diversification of semiconductor applications-from logic and memory to optoelectronics and power devices-necessitates bespoke cleaning and coating strategies that align with device sensitivity and performance targets.
This comprehensive research report categorizes the Semiconductor Chamber Parts Cleaning & Coatings market into clearly defined segments, providing a detailed analysis of emerging trends and precise revenue forecasts to support strategic decision-making.
- Chamber Type
- Cleaning Type
- Coating Type
- Wafer Size
- End User
- Material Type
- Application
Regional Footprints: Insights Across Global Territories
The Americas region boasts a sophisticated ecosystem of semiconductor research and advanced fab operations. In this territory, leading foundries and IDM plants collaborate closely with local chemical manufacturers to co-innovate cleaning chemistries that comply with stringent environmental and safety regulations. The North American market’s focus on high-performance computing and automotive electronics underpins robust demand for specialized cleaning and coating solutions.
Europe, the Middle East & Africa present a mosaic of regulatory landscapes, where the enforcement of chemical usage standards varies by country. Despite this complexity, global equipment suppliers leverage regional research hubs to pilot novel processes before scaling them to high-volume production. The EMEA region also serves as an important crossroad for raw material distribution, making it a strategic base for inventory management in response to fluctuating trade policies.
Asia-Pacific remains the growth engine of semiconductor manufacturing, with a dense concentration of wafer fabrication facilities in East and Southeast Asia. Rapid expansion of memory and logic capacity in this region drives continuous investment in chamber parts maintenance and lifecycle extension programs. Local service providers partner with global coating specialists to customize anti-stiction and passivation treatments for high-throughput fabs, reflecting the sector’s commitment to cost-efficient yield optimization.
This comprehensive research report examines key regions that drive the evolution of the Semiconductor Chamber Parts Cleaning & Coatings market, offering deep insights into regional trends, growth factors, and industry developments that are influencing market performance.
- Americas
- Europe, Middle East & Africa
- Asia-Pacific
Spotlight on Leading Innovators Shaping the Sector
A handful of key players dominate the chamber parts cleaning and coatings arena, each leveraging unique technological strengths. Established chemical suppliers have broadened their portfolios through targeted acquisitions, integrating specialized solvent technologies and surface-engineering capabilities. Their scale and distribution networks enable rapid deployment of novel cleaning agents across global customer bases.
Equipment manufacturers have also deepened their involvement in consumable supplies, bundling maintenance services with coating packages designed to extend chamber uptime. These OEMs capitalize on proprietary process knowledge to formulate coatings that align with their tools’ specifications, thereby reinforcing ecosystem lock-in.
Niche specialists have emerged by focusing on high-value, low-volume applications. Leveraging advanced materials science, they deliver coating films with tailored properties for next-generation devices such as advanced logic nodes and compound semiconductor wafers. Their agility in process development allows rapid iteration in collaboration with early adopters of emerging technologies.
Collaborative alliances between chemical producers, tool vendors, and end users further shape the competitive landscape. Joint development agreements foster co-innovation of cleaning and coating solutions, while strategic partnerships facilitate geographic expansion and localized service capabilities. This collaborative model accelerates time to market and enhances customer responsiveness.
This comprehensive research report delivers an in-depth overview of the principal market players in the Semiconductor Chamber Parts Cleaning & Coatings market, evaluating their market share, strategic initiatives, and competitive positioning to illuminate the factors shaping the competitive landscape.
- Entegris, Inc.
- Merck KGaA
- DuPont de Nemours, Inc.
- MKS Instruments, Inc.
- JSR Corporation
- Shin-Etsu Chemical Co., Ltd.
- Sumitomo Chemical Co., Ltd.
- FUJIFILM Electronic Materials USA, Inc.
- Air Liquide Advanced Materials S.A.S.
- AZ Electronic Materials S.A.
Strategic Pathways for Industry Leadership Advancement
Industry leaders should prioritize the integration of digital monitoring systems into their cleaning and coating workflows. Embedding in-situ sensors and leveraging data analytics will enable predictive maintenance, reduce unplanned downtime, and optimize resource utilization. By harnessing these insights, companies can transition from reactive maintenance schedules to condition-based servicing models.
Strengthening regional manufacturing capabilities can mitigate tariff and supply chain risks. Establishing localized production lines for critical cleaning agents and coating precursors will reduce lead times and buffer against geopolitical uncertainties. Collaborative ventures with local chemical producers and tool suppliers can expedite technology transfer and regulatory approvals.
Sustainability must remain a core pillar of strategic planning. Investing in closed-loop solvent recovery systems and developing low-toxicity cleaning agents will not only ensure compliance with evolving environmental standards but also enhance cost competitiveness through resource efficiency. Transparent reporting of sustainability metrics will further resonate with customers and stakeholders.
Finally, fostering cross-functional alliances across R&D, operations, and supply chain teams will accelerate the commercialization of next-generation coatings. By aligning process engineers with material scientists and market strategists, organizations can deliver differentiated solutions tailored to emerging device architectures and application segments.
Rigorous Methodological Framework Underpinning the Study
This study combines primary research with extensive secondary analysis to deliver a comprehensive view of the chamber parts cleaning and coatings market. Primary data were gathered through in-depth interviews with senior executives at leading equipment manufacturers, chemical suppliers, and semiconductor fabs, ensuring firsthand perspectives on process challenges and solution requirements.
Secondary research encompassed a thorough review of industry publications, patent filings, regulatory documents, and company financial reports. This dual approach enabled cross-validation of insights and enhanced the reliability of findings. Market segmentation analysis was performed by synthesizing technology, end-user, and regional parameters, providing a granular understanding of demand drivers and competitive dynamics.
Data triangulation techniques ensured consistency among quantitative and qualitative inputs, while peer review by subject-matter experts enhanced the accuracy and objectivity of conclusions. The research framework prioritized transparency and reproducibility, with detailed documentation of data sources and analytical methodologies available for client review.
Explore AI-driven insights for the Semiconductor Chamber Parts Cleaning & Coatings market with ResearchAI on our online platform, providing deeper, data-backed market analysis.
Ask ResearchAI anything
World's First Innovative Al for Market Research
Synthesizing Insights to Forge a Clear Market Outlook
The semiconductor chamber parts cleaning and coatings market stands at a pivotal juncture, shaped by technological breakthroughs, regulatory pressures, and global trade dynamics. Stakeholders who embrace advanced cleaning processes, automated monitoring, and sustainable chemistries will gain a competitive edge, securing higher yields and reduced downtime.
Segmentation insights underscore the importance of tailoring solutions to specific chamber types, wafer sizes, and end-user needs, while regional analysis highlights varying regulatory landscapes and supply chain strategies. Key players continue to innovate through strategic alliances and differentiated product offerings, reinforcing the market’s collaborative ethos.
By following the strategic recommendations outlined, industry leaders can navigate tariff challenges, enhance operational resilience, and position themselves for growth in an increasingly complex environment. The path forward demands agility, technological acumen, and a steadfast commitment to sustainability.
This executive summary provides the foundations for informed decision-making, empowering stakeholders to align investments with emerging trends and capitalize on new opportunities in the chamber parts cleaning and coatings space.
This section provides a structured overview of the report, outlining key chapters and topics covered for easy reference in our Semiconductor Chamber Parts Cleaning & Coatings market comprehensive research report.
- Preface
- Research Methodology
- Executive Summary
- Market Overview
- Market Dynamics
- Market Insights
- Cumulative Impact of United States Tariffs 2025
- Semiconductor Chamber Parts Cleaning & Coatings Market, by Chamber Type
- Semiconductor Chamber Parts Cleaning & Coatings Market, by Cleaning Type
- Semiconductor Chamber Parts Cleaning & Coatings Market, by Coating Type
- Semiconductor Chamber Parts Cleaning & Coatings Market, by Wafer Size
- Semiconductor Chamber Parts Cleaning & Coatings Market, by End User
- Semiconductor Chamber Parts Cleaning & Coatings Market, by Material Type
- Semiconductor Chamber Parts Cleaning & Coatings Market, by Application
- Americas Semiconductor Chamber Parts Cleaning & Coatings Market
- Europe, Middle East & Africa Semiconductor Chamber Parts Cleaning & Coatings Market
- Asia-Pacific Semiconductor Chamber Parts Cleaning & Coatings Market
- Competitive Landscape
- ResearchAI
- ResearchStatistics
- ResearchContacts
- ResearchArticles
- Appendix
- List of Figures [Total: 30]
- List of Tables [Total: 369 ]
Connect with Ketan Rohom to Secure Your Strategic Advantage
To gain comprehensive visibility into the trends, opportunities, and strategic imperatives within the semiconductor chamber parts cleaning and coatings market, connect with Ketan Rohom, Associate Director of Sales & Marketing. His deep understanding of industry dynamics and customized solutions will ensure you extract maximum value from the full market research report. Reach out today to secure actionable insights, drive strategic decision-making, and position your organization at the forefront of innovation.
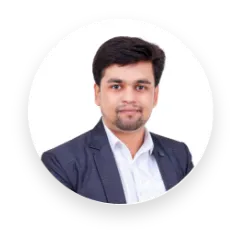
- When do I get the report?
- In what format does this report get delivered to me?
- How long has 360iResearch been around?
- What if I have a question about your reports?
- Can I share this report with my team?
- Can I use your research in my presentation?