Revealing the Vital Role of CMP Polishing Pads in Advanced Semiconductor Fabrication
Chemical mechanical planarization (CMP) polishing pads have emerged as a cornerstone technology in modern semiconductor fabrication, delivering the nanometer-level planarity essential for advanced device scaling. As wafer geometries shrink and circuit densities climb, the role of polishing pads in achieving defect-free surfaces and uniform material removal has never been more critical. Innovations in pad topography and material composition enable manufacturers to meet exacting specifications, minimizing dishing, erosion, and micro-scratches that can compromise yield.
The strategic importance of CMP pads extends beyond basic planarization. They are pivotal in supporting aggressive node transitions, enabling greater transistor performance and power efficiency. With demand surging for high-performance computing, 5G, and artificial intelligence applications, fabs worldwide are under pressure to optimize every stage of the process flow. Against this backdrop, industry participants are racing to refine pad chemistries, enhance wafer-wafer consistency, and reduce environmental impact. This report provides a comprehensive exploration of how these forces converge to shape the CMP pad segment, setting the stage for deeper insight into the market dynamics at play.
Uncovering the Forces Redefining the CMP Polishing Pad Landscape
The semiconductor industry is undergoing a transformational shift driven by the relentless pursuit of Moore’s Law and the parallel rise of data-intensive applications. Leading-edge node transitions to 3nm and beyond impose exacting demands on CMP polishing pads, requiring novel fixed abrasive constructions to maintain uniform planarization at ever-finer geometries. At the same time, wafer manufacturers are exploring larger substrates to enhance throughput, prompting pad suppliers to engineer solutions capable of delivering consistent performance over expanded areas.
Environmental stewardship has also reshaped pad development priorities. Regulatory pressures on water consumption and slurry waste disposal are compelling suppliers to innovate low-consumption pad designs and recyclable materials. Concurrently, the proliferation of three-dimensional device architectures, such as FinFETs and 3D NAND, elevates the complexity of the planarization process, driving growth in specialized pad formulations that can address variable feature aspect ratios. These converging trends underscore the critical inflection point within the CMP pad landscape as industry participants race to address both technological and sustainability challenges.
Assessing the 2025 US Tariff Wave and Its ripple Effects on Pad Supply Chains
The introduction of new United States tariffs in 2025 targeting semiconductor manufacturing consumables has injected fresh urgency into supply chain strategies for CMP polishing pads. Import duties imposed on pad shipments and key raw materials such as copper and tungsten have led to notable cost inflation for wafer fabrication facilities. Manufacturers reliant on cross-border sourcing have responded by reevaluating contracts, consolidating supplier relationships, and exploring tariff exemption certifications where feasible.
These measures have produced a ripple effect across the value chain. Fabricators are redirecting order flows toward regional partners in North America, Europe, and select Asia-Pacific hubs to mitigate duty exposure. At the same time, pad producers are investing in localized manufacturing capacities to preserve competitive pricing and minimize lead times. For end users such as foundries and outsourcing assembly and test providers, the result has been a reframing of total cost of ownership analyses, with strategic stockpiling and just-in-time inventory strategies deployed to navigate heightened price volatility.
Decoding Market Dynamics Across Types, Materials, Applications, and End Users
A nuanced examination of market segmentation reveals distinct growth trajectories across pad types, material compositions, device applications, and end-user categories. Conventional pads continue to serve established logic and memory device processes, offering predictable removal rates and proven defect control. Meanwhile, fixed abrasive pads are gaining traction in advanced node applications where tighter uniformity and lower defect densities are paramount.
In parallel, material choices such as copper composites, oxide blends, and tungsten-reinforced formulations are tailored to address specific planarization challenges. Copper-focused pads excel in metal CMP steps for logic devices, while oxide pads drive superior performance in dielectric planarization. Tungsten-infused solutions often underpin barrier layer polishing, optimizing removal selectivity. On the application front, logic device manufacturers prioritize fine-tuned pad-sample interactions to support transistor scaling, whereas memory device fabs segment their CMP requirements between DRAM and NAND Flash architectures, each demanding unique pad profiles.
End-user segmentation further highlights divergent purchasing behaviors and technical priorities. High-volume foundries emphasize consistency and cost efficiency to serve a broad customer base. Integrated device manufacturers integrate polishing technologies into vertically managed process flows, seeking turnkey consumable packages. Outsourced assembly and test operations, by contrast, value rapid deployment and cross-node flexibility to accommodate multi-customer wafer inventories.
This comprehensive research report categorizes the Semiconductor CMP Polishing Pad market into clearly defined segments, providing a detailed analysis of emerging trends and precise revenue forecasts to support strategic decision-making.
- Type
- Material
- Application
- End User
Mapping Regional Growth Hotspots Across Americas, EMEA, and Asia-Pacific
Regional markets for CMP polishing pads display distinct growth drivers shaped by local semiconductor ecosystems. In the Americas, strong demand from advanced logic fabs and burgeoning markets for electric vehicle microcontrollers underpin steady pad consumption. Collaboration between pad suppliers and U.S.-based wafer foundries is fostering localized innovation in pad formulations, while environmental regulations in North America drive adoption of sustainable pad materials.
Europe, the Middle East, and Africa present a different set of dynamics. Automotive and industrial electronics applications form the backbone of Europe’s semiconductor consumption, necessitating pads that can maintain high yields under stringent quality standards. Incentives linked to the European Green Deal have catalyzed investment in water-efficient polishing systems, amplifying demand for pads engineered for reduced slurry usage and minimal waste generation.
Asia-Pacific remains the largest regional market, fueled by high-volume memory and logic production in China, Taiwan, South Korea, and Japan. Memory device expansion in DRAM and NAND Flash continues to drive significant pad replacement rates, while leading-edge fabs in South Korea and Taiwan push fixed abrasive solutions to meet shrinking node requirements. The region’s robust manufacturing footprint and rapid technology adoption ensure Asia-Pacific will remain a pivotal arena for CMP pad innovation.
This comprehensive research report examines key regions that drive the evolution of the Semiconductor CMP Polishing Pad market, offering deep insights into regional trends, growth factors, and industry developments that are influencing market performance.
- Americas
- Europe, Middle East & Africa
- Asia-Pacific
Spotlighting Industry Leaders and Their Strategic Moves in CMP Pad Innovation
Leading players in the CMP polishing pad domain are pursuing multifaceted strategies to secure competitive advantage and drive the next wave of innovation. Established firms with extensive chemical engineering capabilities are deepening investments in custom pad chemistries and advanced surface patterning techniques to deliver incremental performance gains. Simultaneously, several market entrants are forging partnerships with slurry suppliers and fab operators to co-develop integrated planarization solutions that optimize consumable compatibility and process control.
A parallel trend involves strategic capacity expansions in key manufacturing hubs. By adding localized production lines in North America and Europe, these companies aim to alleviate tariff pressures and shorten lead times for critical pad deliveries. In Asia-Pacific, alliances between pad suppliers and memory foundries are accelerating co-optimization programs, focusing on pad durability enhancements and defect reduction at the wafer edge. Across the board, R&D roadmaps are increasingly oriented toward eco-friendly raw materials, digital quality monitoring, and predictive maintenance platforms, reflecting a convergence of performance, cost, and sustainability imperatives.
This comprehensive research report delivers an in-depth overview of the principal market players in the Semiconductor CMP Polishing Pad market, evaluating their market share, strategic initiatives, and competitive positioning to illuminate the factors shaping the competitive landscape.
- Cabot Microelectronics Corporation
- Dow Inc.
- DuPont de Nemours, Inc.
- Fujibo Co., Ltd.
- Tokyo Ohka Kogyo Co., Ltd.
- Tosoh Corporation
- Entegris, Inc.
- Hitachi Chemical Co., Ltd.
Strategic Imperatives for Navigating the Evolving CMP Polishing Pad Market
Industry participants seeking to capitalize on emerging opportunities within the CMP polishing pad market should prioritize supply chain resilience through diversified sourcing and localized manufacturing footprints. By proactively collaborating with regional foundries and test operators, pad suppliers can secure first-mover advantages in co-development of next-generation formulations tailored to specific node transitions.
Another strategic imperative involves accelerating R&D in sustainable pad materials and low-waste process designs. Firms that integrate closed-loop water recycling and reusable pad components into their product lines will not only meet tightening environmental regulations but also achieve cost leadership through reduced slurry and disposal expenses. Moreover, embedding real-time sensors within pad support structures can enable predictive maintenance and in-situ quality assurance, unlocking new service revenue streams and enhancing overall equipment effectiveness.
Finally, maintaining vigilance toward global trade and tariff developments will be critical for mitigating cost volatility. Establishing cross-border tariff mitigation programs and pursuing duty drawback certifications can shield pricing strategies from abrupt policy shifts. By executing these recommendations in concert, industry leaders can reinforce their competitive positions, accelerate innovation, and deliver sustainable value across the CMP ecosystem.
Ensuring Rigor Through a Robust and Multifaceted Research Approach
This study employs a rigorous research approach grounded in both primary and secondary data sources, ensuring comprehensive coverage and analytical accuracy. Secondary insights were gathered from company reports, patent filings, trade publications, and regulatory documents to establish foundational market parameters. These were then validated through primary interviews with key stakeholders-including process engineers, purchasing managers, and R&D directors at leading wafer fabs and pad manufacturers.
Quantitative data collection involved detailed mapping of pad shipments, material consumption patterns, and pricing trends across major geographies. Statistical triangulation methods reconciled these inputs with public financial disclosures and proprietary databases to derive robust segmentation insights. Qualitative analysis further enriched the findings, as expert interviews illuminated emerging technology inflection points and strategic investment priorities.
Careful quality assurance protocols were applied throughout the research lifecycle, encompassing data validation workshops, peer reviews, and sensitivity analyses to ensure the reliability and relevance of the report’s conclusions. The resulting framework supports nuanced interpretation of market developments and equips decision-makers with actionable intelligence tailored to their strategic imperatives.
Explore AI-driven insights for the Semiconductor CMP Polishing Pad market with ResearchAI on our online platform, providing deeper, data-backed market analysis.
Ask ResearchAI anything
World's First Innovative Al for Market Research
Synthesizing Insights to Forge a Clear CMP Polishing Pad Outlook
The semiconductor CMP polishing pad landscape stands at a pivotal juncture, shaped by advanced node scaling, evolving materials science, and shifting trade policies. As manufacturers transition to finer geometries and three-dimensional device architectures, the demand for both conventional and fixed abrasive pad solutions will intensify. Regional dynamics-influenced by regulatory frameworks, fab expansions, and tariff landscapes-further underscore the need for agile supply chain and product development strategies.
Key segmentation insights reveal that distinct pad types and material compositions align closely with specific process steps and device architectures, while end-user priorities vary between high-volume foundries, integrated device manufacturers, and outsourcing providers. Leading players are capitalizing on these nuances through targeted R&D investments, localized manufacturing expansions, and collaborative co-development initiatives.
By synthesizing these insights, industry participants can anticipate where performance bottlenecks may arise, proactively adapt to cost pressures driven by tariffs, and harness regional growth opportunities. This comprehensive perspective lays the groundwork for informed decision-making and sustained competitive advantage in the dynamic realm of CMP polishing pads.
This section provides a structured overview of the report, outlining key chapters and topics covered for easy reference in our Semiconductor CMP Polishing Pad market comprehensive research report.
- Preface
- Research Methodology
- Executive Summary
- Market Overview
- Market Dynamics
- Market Insights
- Cumulative Impact of United States Tariffs 2025
- Semiconductor CMP Polishing Pad Market, by Type
- Semiconductor CMP Polishing Pad Market, by Material
- Semiconductor CMP Polishing Pad Market, by Application
- Semiconductor CMP Polishing Pad Market, by End User
- Americas Semiconductor CMP Polishing Pad Market
- Europe, Middle East & Africa Semiconductor CMP Polishing Pad Market
- Asia-Pacific Semiconductor CMP Polishing Pad Market
- Competitive Landscape
- ResearchAI
- ResearchStatistics
- ResearchContacts
- ResearchArticles
- Appendix
- List of Figures [Total: 24]
- List of Tables [Total: 233 ]
Unlock Deeper Insights by Engaging Ketan Rohom for the Full Market Report
Interested stakeholders seeking an in-depth understanding of the semiconductor CMP polishing pad market are encouraged to reach out directly to Ketan Rohom, Associate Director of Sales & Marketing, to secure the comprehensive market research report. His expertise ensures you receive tailored guidance on how emerging trends and tariff implications can shape your strategic roadmap. Contacting him will grant immediate access to detailed chapter analyses, proprietary data tables, and actionable insights designed to support critical decision-making and competitive positioning.
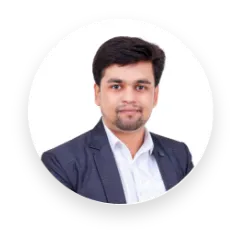
- When do I get the report?
- In what format does this report get delivered to me?
- How long has 360iResearch been around?
- What if I have a question about your reports?
- Can I share this report with my team?
- Can I use your research in my presentation?