Introduction
The semiconductor industry’s relentless push toward higher performance, greater energy efficiency, and miniaturization has made crystal growth equipment an indispensable backbone of chip manufacturing. From the precise cultivation of silicon ingots to advanced gallium nitride substrates, the equipment that supports crystal growth dictates wafer quality, yield rates, and ultimately the competitiveness of fabs worldwide. As process nodes shrink into the single-digit nanometer regime and emerging materials such as silicon carbide and gallium nitride gain prominence, manufacturers demand more rigorous control over temperature, purity, and defect density. Navigating dynamic supply chains, evolving trade policies, and rapid technological change requires an informed, holistic perspective on this critical segment. This executive summary outlines the most transformative industry shifts, analyzes regulatory headwinds, dissects core market segments, and offers strategic guidance for leaders seeking to optimize their crystal growth capabilities in today’s complex environment.
Transformative Shifts in the Crystal Growth Landscape
Over the past decade, crystal growth equipment has undergone a fundamental evolution driven by the increasing complexity of semiconductor architectures and the imperative for lean, digitalized operations. Converging trends in advanced process control and data analytics have elevated real-time monitoring from a differentiator to a necessity, enabling firms to detect sub-micron anomalies, predict equipment maintenance needs, and minimize cycle time variation. Meanwhile, automation integration across wafer handling and consumable replenishment has streamlined throughput and reduced contamination risk.
Material innovation represents another seismic shift: gallium nitride and silicon carbide, once niche materials for power electronics, are now integral to electric vehicles and 5G infrastructure, prompting manufacturers to adapt crystal growth platforms to new chemistries and thermal profiles. Concurrently, the industry has embraced sustainability, with next-generation furnaces designed for lower energy consumption and reduced greenhouse gas emissions. Such transformative shifts have repositioned crystal growth equipment providers as partners in both performance optimization and corporate environmental responsibility.
Cumulative Impact of United States Tariffs 2025
In 2025, expanded U.S. tariffs on semiconductor manufacturing equipment have introduced layered complexities into global supply chains. Originally oriented toward photolithography and etch tools, the tariffs now explicitly cover specialized components used in crystal growth platforms, including high-purity gas delivery systems and optical monitoring modules. The immediate effect has been price inflation for imported furnaces and temperature control units, compelling North American and allied fabs to reevaluate sourcing strategies.
In response, many suppliers have accelerated local manufacturing partnerships and bolstered inventory buffers to mitigate lead-time volatility. Some crystal growth equipment vendors have pursued tariff engineering solutions, redesigning subsystems to reclassify duties or to substitute components from lower-tariff jurisdictions. Although these adaptations have partially absorbed cost pressures, manufacturers should anticipate continued regulatory flux and proactively engage in trade compliance planning to safeguard throughput and cost targets.
Key Segmentation Insights
An in-depth segmentation of the crystal growth equipment market reveals nuanced demand drivers aligned with specific operational priorities. When classified by application and use, production scale dominates capex budgets as high-volume fabs seek consistent yield yields, while prototype development and research and development facilities emphasize flexibility and modularity. Quality assurance deployments, particularly in advanced nodes, have spurred investment in optical monitoring devices and in-line defect inspection.
Examining crystal growth techniques underscores the sustained leadership of the Czochralski method, where both standard and modified processes accommodate a broad substrate range. Complementing this are Bridgman-Stockbarger systems for specialized ingots, float zone instrumentation prized for ultra-high-purity silicon, and zone melting platforms-both continuous and multiple zone variants-optimized for novel materials.
On the instrumentation front, furnace systems remain the foundational workhorses, with high-temperature and rapid thermal furnaces addressing divergent throughput and quality demands. Optical monitoring devices and advanced temperature control units have emerged as critical adjuncts, enabling precision down to single-degree variations.
Material and composition segmentation highlights the prominence of silicon-differentiated into doped and high-purity variants-as well as growing allocations for silicon carbide, gallium nitride, and germanium substrates. In parallel, the fabrication and process stage perspective emphasizes seamless integration across material preparation, surface treatment, core growth, seed crystal generation, annealing and cooling, and cutting and polishing, underscoring the need for end-to-end process cohesion.
Innovation-led toolsets, including advanced process control, automation integration, data analytics with predictive maintenance and process optimization modules, and real-time monitoring solutions, are driving next-generation performance. Capacity and scale distinctions reflect a bifurcation: large-scale manufacturing demands robust, high-throughput platforms, while mid and small scale production facilities prioritize configurability and rapid changeover.
Operational efficiency imperatives have fueled demand for cost optimization strategies, cycle time reduction techniques, and energy efficiency solutions. Quality and compliance segmentation further accentuates investments in automated and manual inspection systems, regulatory compliance frameworks, and international standards certification.
This comprehensive research report categorizes the Semiconductor Crystal Growth Equipment market into clearly defined segments, providing a detailed analysis of emerging trends and precise revenue forecasts to support strategic decision-making.
- Application And Use
- Crystal Growth Technique
- Equipment And Instrumentation
- Material And Composition
- Fabrication And Process Stage
- Innovation And Technology Development
- Capacity And Scale
- Operational Efficiency
- Quality And Compliance
Key Regional Insights
Geographic dynamics in the crystal growth equipment market underscore distinct regional trajectories. In the Americas, a resurgence of domestic semiconductor manufacturing driven by policy incentives has accelerated capital expenditures for advanced furnaces and process automation, while Canada’s research institutions continue to pioneer novel crystal growth methodologies. The Europe, Middle East & Africa region presents a mosaic of mature manufacturing hubs in Germany and the Netherlands, growing wafer fab ventures in Eastern Europe, and strategic investments in the Middle East aimed at diversifying local capacity. Asia-Pacific stands out as the largest and fastest-growing market, led by Taiwan’s and South Korea’s legacy foundries, Japan’s specialty crystal suppliers, and an expanding footprint in Southeast Asia. China’s dual emphasis on import substitution and local innovation has cultivated a competitive ecosystem of domestic equipment vendors and research consortia.
This comprehensive research report examines key regions that drive the evolution of the Semiconductor Crystal Growth Equipment market, offering deep insights into regional trends, growth factors, and industry developments that are influencing market performance.
- Americas
- Asia-Pacific
- Europe, Middle East & Africa
Key Companies Insights
Competition and collaboration among leading equipment providers are reshaping the industry’s innovation landscape. Advanced Crystal Manufacturing continues to expand its high-temperature furnace portfolio, while Advantest Corporation and Applied Materials, Inc. leverage their metrology and process strengths to offer integrated growth solutions. ASML Holding N.V. is exploring cross-technology synergies between lithography and crystal quality inspection, and Bridgelux Corporation has introduced hybrid modules addressing optical monitoring requirements. Canon Inc. and Corning Incorporated partner on specialty glass crucibles, whereas CrystalTech Industries, Inc. focuses on turnkey wafer handling systems.
Entegris, Inc. supplies high-purity materials and contamination control solutions critical to crystal integrity. FUJIFILM Corporation and Hitachi High-Technologies Corporation jointly drive innovations in rapid thermal processing. Innovative Growth Technologies Inc. champions flexible Czochralski platforms, while KLA Corporation advances automated defect detection. Lam Research Corporation and Lumentum Holdings Inc. are integrating laser-based annealing stages. MKS Instruments, Inc. and NanoCrystal Systems Ltd. emphasize gas delivery and impurity management, and Nikon Corporation complements optical inspection with advanced imaging sensors. Oxford Instruments PLC and Pioneer Semiconductor Solutions are forging partnerships on emerging materials, and Precision Semiconductor Equipment LLC delivers modular pre-growth conditioning units. Quantum Materials Corp. and SCREEN Holdings Co., Ltd. innovate at the intersection of materials science and automation. Semiconductor Equipment Corporation and Silicon Systems Engineering Inc. have expanded capacity for large-scale furnaces, while Sumitomo Electric Industries, Ltd. and Tokyo Electron Limited enhance full-fab integration. Veeco Instruments Inc. advances molecular beam epitaxy for compound semiconductors, and Vertex Crystal Equipment Corp. is pioneering multi-zone melting solutions.
This comprehensive research report delivers an in-depth overview of the principal market players in the Semiconductor Crystal Growth Equipment market, evaluating their market share, strategic initiatives, and competitive positioning to illuminate the factors shaping the competitive landscape.
- Advanced Crystal Manufacturing
- Advantest Corporation
- Applied Materials, Inc.
- ASML Holding N.V.
- Bridgelux Corporation
- Canon Inc.
- Corning Incorporated
- CrystalTech Industries, Inc.
- Entegris, Inc.
- FUJIFILM Corporation
- HighPurity Processing Technologies
- Hitachi High-Technologies Corporation
- Innovative Growth Technologies Inc.
- KLA Corporation
- Lam Research Corporation
- Lumentum Holdings Inc.
- MKS Instruments, Inc.
- NanoCrystal Systems Ltd.
- Nikon Corporation
- Oxford Instruments PLC
- Pioneer Semiconductor Solutions
- Precision Semiconductor Equipment LLC
- Quantum Materials Corp.
- SCREEN Holdings Co., Ltd.
- Semiconductor Equipment Corporation
- Silicon Systems Engineering Inc.
- Sumitomo Electric Industries, Ltd.
- Tokyo Electron Limited
- Veeco Instruments Inc.
- Vertex Crystal Equipment Corp.
Actionable Recommendations for Industry Leaders
To capitalize on evolving crystal growth demands, industry leaders should prioritize several strategic actions. First, deploying advanced process control systems integrated with real-time monitoring will drive yield improvements and reduce unplanned downtime. Second, diversifying supplier networks-especially in light of tariff volatility-can mitigate disruptions and optimize total cost of ownership. Third, investing in modular, flexible platforms capable of handling silicon carbide and gallium nitride will position manufacturers to capture growth in power electronics and 5G applications. Fourth, adopting digital twin simulations for process optimization can accelerate time-to-market and reduce experimentation costs. Fifth, strengthening quality and compliance frameworks, including automated inspection systems and international certification strategies, will build trust with fab customers. Finally, fostering strategic partnerships with material suppliers, research institutions, and equipment integrators will accelerate technology transfer and drive continuous innovation.
Explore AI-driven insights for the Semiconductor Crystal Growth Equipment market with ResearchAI on our online platform, providing deeper, data-backed market analysis.
Ask ResearchAI anything
World's First Innovative Al for Market Research
Conclusion
The confluence of advanced materials, stringent quality requirements, and geopolitical dynamics has placed crystal growth equipment at the heart of semiconductor innovation. As fabs push toward sub-three-nanometer nodes and broaden into heterogeneous integration, the ability to precisely control temperature profiles, impurity levels, and defect densities will define competitive advantage. Firms that navigate tariff pressures, embrace digitalization across process stages, and tailor equipment portfolios to emerging material demands will secure leadership in this critical segment. By leveraging data-driven insights, fostering collaborative ecosystems, and continuously refining operational efficiency, companies can unlock new performance thresholds and deliver the substrate quality that next-generation devices demand.
This section provides a structured overview of the report, outlining key chapters and topics covered for easy reference in our Semiconductor Crystal Growth Equipment market comprehensive research report.
- Preface
- Research Methodology
- Executive Summary
- Market Overview
- Market Dynamics
- Market Insights
- Cumulative Impact of United States Tariffs 2025
- Semiconductor Crystal Growth Equipment Market, by Application And Use
- Semiconductor Crystal Growth Equipment Market, by Crystal Growth Technique
- Semiconductor Crystal Growth Equipment Market, by Equipment And Instrumentation
- Semiconductor Crystal Growth Equipment Market, by Material And Composition
- Semiconductor Crystal Growth Equipment Market, by Fabrication And Process Stage
- Semiconductor Crystal Growth Equipment Market, by Innovation And Technology Development
- Semiconductor Crystal Growth Equipment Market, by Capacity And Scale
- Semiconductor Crystal Growth Equipment Market, by Operational Efficiency
- Semiconductor Crystal Growth Equipment Market, by Quality And Compliance
- Americas Semiconductor Crystal Growth Equipment Market
- Asia-Pacific Semiconductor Crystal Growth Equipment Market
- Europe, Middle East & Africa Semiconductor Crystal Growth Equipment Market
- Competitive Landscape
- ResearchAI
- ResearchStatistics
- ResearchContacts
- ResearchArticles
- Appendix
- List of Figures [Total: 34]
- List of Tables [Total: 816 ]
Call-To-Action: Secure Your Market Research Report Today
To obtain an in-depth analysis of market dynamics, comprehensive segmentation data, and strategic foresight tailored to your organization’s goals, contact Ketan Rohom, Associate Director, Sales & Marketing. His expertise will guide you through the research findings and help customize insights that drive informed decisions. Reach out today to access the full market research report and gain a competitive edge in semiconductor crystal growth equipment.
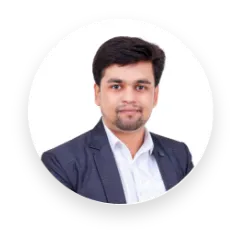
- When do I get the report?
- In what format does this report get delivered to me?
- How long has 360iResearch been around?
- What if I have a question about your reports?
- Can I share this report with my team?
- Can I use your research in my presentation?