The Semiconductor Inspection System Market size was estimated at USD 6.14 billion in 2024 and expected to reach USD 6.49 billion in 2025, at a CAGR 5.87% to reach USD 8.65 billion by 2030.

Unveiling the Crucial Role of Inspection in Semiconductor Production
The semiconductor industry stands at a pivotal crossroads where inspection systems have become critical enablers of manufacturing excellence. Every wafer processed must undergo rigorous scrutiny to meet stringent quality requirements and to ensure optimal yield at advanced technology nodes. Inspection technologies not only safeguard against catastrophic defects but also serve as early warning systems, informing process adjustments that can save millions in production costs.
Introduction to the semiconductor inspection landscape reveals its deep integration with emerging manufacturing trends. As device geometries shrink below single-digit nanometer scales, even the smallest particle or structural anomaly can compromise functionality. Therefore, inspection systems have evolved from simple defect capture instruments into sophisticated platforms that combine imaging, analytics, and machine learning. This evolution underscores the technology’s transition from a reactive quality control measure to a proactive process optimization tool.
Building on these foundations, this executive summary outlines the key drivers, challenges, and opportunities shaping the semiconductor inspection market. It synthesizes the transformative shifts in inspection modalities, examines the cumulative effects of upcoming U.S. tariffs in 2025, and distills critical segmentation and regional insights. Prepared for decision-makers and industry leaders, the following sections deliver a concise yet authoritative roadmap to navigate this complex and rapidly advancing domain.
Navigating a New Era of Advanced Inspection Technologies
The semiconductor inspection landscape has undergone transformative shifts driven by the convergence of precision requirements and digital technologies. Traditional optical inspection techniques have been complemented and, in many cases, superseded by high-resolution electron beam and X-ray inspection platforms that can detect sub-nanometer defects. Moreover, laser scanning inspection systems have risen to prominence by offering rapid, non-contact evaluation across large die areas, enabling manufacturers to maintain throughput without sacrificing accuracy.
Concurrently, integration of advanced analytics and machine learning has redefined defect classification and root-cause analysis. Inspection outputs no longer consist solely of static images; they feed real-time dashboards and predictive models that identify defect trends and correlate anomalies with upstream process parameters. This shift toward data-driven inspection transforms the technology into a strategic asset that informs process development and yields continual improvement across multiple fabs.
Looking ahead, the push for inline, high-speed inspection capabilities is reshaping production lines. Inline systems employ automated handling and synchronized data capture to minimize downtime, while on-equipment inspection bridges the gap between metrology and processing. Integrating inspection modules directly into lithography and etching tools reduces cycle time and amplifies feedback loops, empowering fabs to address defects at the source. Together, these transformative advances herald a new era of inspection that is more precise, predictive, and seamlessly woven into the semiconductor manufacturing tapestry.
Assessing the 2025 U.S. Tariff Impact on Inspection Ecosystems
As the United States prepares to implement additional tariffs on semiconductor equipment in 2025, inspection systems suppliers and chip manufacturers must brace for cascading effects. These tariff measures are expected to raise the cost of imported inspection machinery, compelling fabs to reevaluate procurement strategies and to explore localized sourcing or alternative vendors. Consequently, capital expenditure budgets may shift toward refurbishing existing platforms or adopting second-source equipment to mitigate financial strain.
The tariff landscape also introduces complexity into long-term partnerships between equipment vendors and end users. Suppliers face pressure to localize production, expand service centers, and adapt their supply chains to navigate trade barriers. In turn, fabs may accelerate investments in in-house service capabilities or seek collaborative arrangements with equipment manufacturers to secure preferential pricing and support. Such strategic realignments highlight the increasing importance of agile supply chain management in preserving production continuity.
Despite upward cost pressures, consistent demand for inspection precision and throughput remains unrelenting. Manufacturers will likely absorb some tariff-related expenses to maintain quality standards, but ongoing inflation in equipment costs could exacerbate lead times and project timelines. To counterbalance these headwinds, companies must intensify focus on yield optimization and operational efficiency, leveraging existing inspection assets more effectively and exploring software-driven enhancements to extend the lifecycle of capital investments.
Unlocking Insights Through Precise Market Segmentation
A nuanced understanding of market segmentation illuminates distinct growth trajectories across product types, components, and end users. Within the product dimension, electron beam inspection systems excel at high-resolution defect detection for advanced nodes, while laser scanning inspection systems efficiently survey large die areas at faster throughput. Optical inspection systems continue to hold relevance for mid-layer metrology and quick pass/fail analysis, and X-ray inspection systems reveal subsurface anomalies in complex 3D structures.
On the component front, hardware investments account for the bulk of system costs, with cameras, lasers, and microscopes serving as critical enablers of imaging fidelity and resolution. As feature sizes shrink, manufacturers demand cameras with increased pixel density and lasers with finer focus capabilities, while microscopes must deliver higher magnification with stable optics. Parallel to this, software components are gaining prominence as data analysis software and defect review software facilitate automated defect classification, trend analysis, and process feedback, transforming raw images into actionable insights.
End-user segmentation further clarifies application-specific drivers. In automotive electronics, where reliability under stringent safety standards is paramount, X-ray and laser scanning inspections are deployed to verify solder joint integrity and component placement. Consumer electronics manufacture prioritizes rapid optical inspection throughput to support high-volume assembly lines. Meanwhile, leading semiconductor foundries and IDM players integrate a mix of electron beam and optical systems in their 3-nanometer and below process nodes, underscoring the critical role of cutting-edge inspection technology in pushing Moore’s Law forward.
This comprehensive research report categorizes the Semiconductor Inspection System market into clearly defined segments, providing a detailed analysis of emerging trends and precise revenue forecasts to support strategic decision-making.
- Product Type
- Component
- End-User
Regional Dynamics Driving the Global Inspection Market
Regional nuances manifest in technology adoption rates, investment appetites, and regulatory frameworks across the Americas, Europe Middle East & Africa, and Asia-Pacific. In the Americas, a robust ecosystem of foundries, advanced packaging facilities, and research institutions has created fertile ground for electron beam and inline optical inspection platforms. Government incentives and collaborative public-private initiatives further accelerate deployment of next-generation inspection tools.
Within Europe Middle East & Africa, stringent quality and environmental regulations drive demand for energy-efficient inspection systems and comprehensive supply chain transparency. High-mix manufacturing in specialized automotive and industrial semiconductors fosters versatile inspection portfolios that combine laser scanning, X-ray, and hybrid optical-electron beam solutions. Strategic partnerships with local service providers bolster uptime and support compliance requirements.
Asia-Pacific remains the largest market by volume, fueled by leading-edge foundries in Taiwan, South Korea, and China. Rapid expansion of fabrication capacity and aggressive node migration plans create continuous demand for high-throughput inspection systems. Moreover, regional governments’ emphasis on domestic chip capabilities is catalyzing increased capital investment in localized manufacturing and equipment servicing, thus strengthening the inspection market’s growth trajectory.
This comprehensive research report examines key regions that drive the evolution of the Semiconductor Inspection System market, offering deep insights into regional trends, growth factors, and industry developments that are influencing market performance.
- Americas
- Europe, Middle East & Africa
- Asia-Pacific
Competitive Landscape and Leading Innovators in Inspection
A competitive cohort of inspection equipment providers defines the current landscape, with market leaders differentiated by technology portfolios, global service footprints, and strategic alliances. One prominent vendor has established dominance in optical and laser scanning inspection technologies by leveraging decades of process integration expertise within top-tier foundries. Another leading firm commands the electron beam inspection segment, continually innovating resolution and throughput to serve sub-3 nanometer process nodes.
Emerging challengers have carved niche positions through specialization in defect review software and real-time analytics platforms, enabling fabs to extract more value from existing hardware investments. Several players originated in adjacent metrology markets and have successfully transitioned into integrated inspection solutions by combining hardware modules with robust data analysis suites. Partnerships with semiconductor manufacturers have further accelerated these entrants’ credibility and market presence.
Strategic M&A activity and cross-industry collaborations are also reshaping competitive dynamics. Well-capitalized multinationals are acquiring software-focused startups to enhance their machine learning capabilities, while regional equipment suppliers form alliances with global service organizations to expand maintenance and calibration networks. Through these concerted efforts, companies are not only defending their core customer bases but also pursuing new application areas in advanced packaging and heterogeneous integration.
This comprehensive research report delivers an in-depth overview of the principal market players in the Semiconductor Inspection System market, evaluating their market share, strategic initiatives, and competitive positioning to illuminate the factors shaping the competitive landscape.
- Advantest Corporation
- Applied Materials, Inc.
- ASML Holding N.V.
- Camtek Ltd.
- Carl Zeiss AG
- Hitachi, Ltd.
- JEOL Ltd.
- Keysight Technologies, Inc.
- KLA Corporation
- Lasertec Corporation
- Lumetrics, Inc.
- Muetec GmbH
- Nanometrics Incorporated
- Nikon Metrology Inc.
- Onto Innovation Inc.
- Rigaku Corporation
- SCREEN Holdings Co., Ltd.
- Spirox Corporation
- Thermo Fisher Scientific, Inc.
- Toray Industries, Inc.
- UnitySC
- Veeco Instruments Inc.
Strategic Recommendations to Propel Inspection Excellence
Industry leaders should prioritize integration of artificial intelligence and machine learning to elevate defect detection and predictive maintenance capabilities. By embedding intelligent algorithms at the system level, organizations can shift inspection from a purely reactive quality gate to a proactive process control mechanism that anticipates yield bottlenecks and recommends corrective actions.
Supply chain resilience must also rank high on the strategic agenda. Diversifying equipment sourcing across multiple geographies and establishing local service hubs will mitigate risks associated with trade tensions and logistics disruptions. Equally important is cultivating collaborative relationships with equipment vendors, enabling joint roadmap planning and early access to emerging technologies.
Investing in workforce development and cross-functional expertise ensures that inspection teams can fully leverage advanced systems. Fostering a culture of continuous learning through specialized training programs and certifications will accelerate adoption of new inspection modalities and reinforce process traceability.
Finally, aligning inspection strategies with broader digital transformation initiatives amplifies value creation. Integrating inspection data with manufacturing execution systems and process control platforms enables holistic visibility across the production floor, paving the way for closed-loop feedback systems and dynamic optimization of fab operations.
Robust Research Methodology Underpinning Our Analysis
This research employs a rigorous mixed-methodology approach to ensure comprehensive and unbiased insights. Primary data collection included in-depth interviews with senior process engineers, equipment managers, and R&D heads across leading semiconductor manufacturers. These conversations provided qualitative understanding of inspection challenges, technology adoption drivers, and strategic priorities directly from industry stakeholders.
Secondary research drew from a wide array of sources including technical journals, patent filings, regulatory documents, and equipment datasheets. Cross-referencing historical financial reports and public disclosures enabled validation of market share estimates and competitive positioning. Quantitative analysis utilized production data, fab capacity expansions, and historical procurement trends to identify patterns in equipment demand and technology shifts.
Data triangulation techniques assured the integrity of findings, with independent expert validation conducted to reconcile any discrepancies. The synthesis of qualitative and quantitative inputs culminated in actionable insights that accurately reflect current market dynamics and anticipate emerging opportunities within the semiconductor inspection domain.
Explore AI-driven insights for the Semiconductor Inspection System market with ResearchAI on our online platform, providing deeper, data-backed market analysis.
Ask ResearchAI anything
World's First Innovative Al for Market Research
Summarizing Key Takeaways and Future Outlook
As the semiconductor industry continues its relentless march toward smaller geometries and more complex packages, inspection systems will play a defining role in enabling consistent yield and product reliability. The confluence of advanced imaging modalities, data analytics, and strategic supply chain realignment positions the market for sustained innovation and resilience.
Stakeholders equipped with the insights from this report will be better prepared to navigate trade-related headwinds, to optimize capital investments across hardware and software components, and to align regional expansion plans with evolving demand patterns. Ultimately, a proactive and integrated approach to inspection will be indispensable in delivering the next generation of semiconductor performance with uncompromising quality.
This section provides a structured overview of the report, outlining key chapters and topics covered for easy reference in our Semiconductor Inspection System market comprehensive research report.
- Preface
- Research Methodology
- Executive Summary
- Market Overview
- Market Dynamics
- Market Insights
- Cumulative Impact of United States Tariffs 2025
- Semiconductor Inspection System Market, by Product Type
- Semiconductor Inspection System Market, by Component
- Semiconductor Inspection System Market, by End-User
- Americas Semiconductor Inspection System Market
- Europe, Middle East & Africa Semiconductor Inspection System Market
- Asia-Pacific Semiconductor Inspection System Market
- Competitive Landscape
- ResearchAI
- ResearchStatistics
- ResearchContacts
- ResearchArticles
- Appendix
- List of Figures [Total: 22]
- List of Tables [Total: 235 ]
Secure Your Comprehensive Inspection Market Insights Today
To secure the full depth of analysis and actionable insights presented in this report, reach out to Ketan Rohom, Associate Director of Sales & Marketing. Engage directly to obtain tailored support and comprehensive access to the data, strategic recommendations, and competitive intelligence that will empower your organization’s decision-making process.
Don’t miss the opportunity to leverage the most up-to-date intelligence on semiconductor inspection systems. Contact Ketan Rohom today to purchase your copy of the market research report and begin transforming your operational strategy with authoritative industry guidance
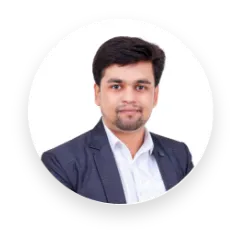
- How big is the Semiconductor Inspection System Market?
- What is the Semiconductor Inspection System Market growth?
- When do I get the report?
- In what format does this report get delivered to me?
- How long has 360iResearch been around?
- What if I have a question about your reports?
- Can I share this report with my team?
- Can I use your research in my presentation?