Setting the Stage for Monocrystalline Silicon Wafer Market Evolution
Monocrystalline silicon wafers stand at the heart of modern electronics and renewable energy systems, providing the foundational substrate for integrated circuits and solar modules. Manufactured through a precise crystal growth process, these wafers deliver exceptional electrical properties and uniformity, enabling advanced device performance at scale. As semiconductor nodes shrink and solar efficiency targets rise, the demand for high-purity, defect-free silicon substrates has surged, driving innovation across supply chains and manufacturing equipment. This executive summary distills the critical trends, risks, and strategic inflection points shaping the monocrystalline silicon wafer sector today.
In this overview, we explore the technological drivers that are redefining wafer specifications, the policy shifts that influence global trade, and the competitive dynamics that uplift leading suppliers. Decision makers will find a concise yet thorough briefing of market segmentation patterns, regional growth differentials, and corporate strategies that inform investment and operational choices. Throughout the narrative, we integrate a balanced perspective that addresses both near-term challenges and long-term opportunities, ensuring readers can navigate the complexities of supply continuity, cost control, and innovation roadmaps with clarity and confidence.
Emerging Forces Reshaping Silicon Wafer Manufacturing Practices
The monocrystalline silicon wafer landscape is undergoing transformative shifts fueled by technological breakthroughs and evolving end-user requirements. Advanced lithography techniques demand wafers with tighter thickness tolerances and improved surface finishes, compelling manufacturers to refine their slicing and polishing processes. Simultaneously, the transition to smaller device geometries has amplified the relevance of 300 mm diameter substrates, as larger wafers support higher throughput and lower per-die cost.
Beyond engineering refinements, sustainability imperatives are reshaping production footprints. Water and energy consumption metrics now dictate capital allocation for new facilities, while closed-loop recycling of silicon kerf and slurry waste has become a strategic priority. In parallel, supply chain resilience is anchored by strategic partnerships with polysilicon producers and equipment vendors, ensuring continuity in feedstock quality and equipment uptime. These developments converge to redefine competitive advantage in wafer manufacturing.
Collectively, these shifts underscore a broader industrial pivot toward integrated value chains, marrying raw material innovation with process automation and environmental stewardship. As a result, both incumbent leaders and emerging disruptors are investing heavily in R&D, facility modernization, and cross-sector collaborations to stay ahead of accelerating performance benchmarks.
Assessing the Ripple Effects of 2025 US Tariff Escalations
In 2025, the United States implemented heightened tariffs on select silicon wafer imports in a move to bolster domestic production and protect critical supply chains. Companies reliant on international sources found themselves navigating increased unit costs and reconfigured procurement strategies. Suppliers in tariff-affected regions reprioritized their export corridors, diverting volumes toward markets with more favorable trade terms to mitigate margin erosion.
The immediate consequence was a recalibration of logistics networks. Manufacturers accelerated qualification of alternative vendors, investing in dual-sourcing arrangements to ensure continuity. Domestic capacity expansions that were once deferred now received renewed urgency, unlocking opportunities for local wafer fabricators to capture displaced demand. However, this transition introduced complexity in inventory planning, with buyers balancing higher in-house processing rates against the lead times associated with new equipment installations.
Looking ahead, the tariff regime acts as both a catalyst and a constraint. While it accelerates domestic investment and supply-chain localization, it also elevates cost pressures for device producers operating without scale economies. The net effect on innovation pipelines and downstream pricing will depend on how swiftly manufacturers can optimize capital deployment and streamline certification processes for emerging suppliers.
Unveiling Critical Segmentation Patterns Driving Market Dynamics
A granular examination of wafer segmentation reveals nuanced demand patterns that are critical for strategic positioning. When categorized by crystal orientation, the market divides into wafers with 100 planes and those with 111 planes, each offering distinct advantages in etch resistance and device integration. The selection of orientation often aligns with application complexity and tool compatibility.
From an application standpoint, integrated circuits command a significant share, driven by analog and power devices, logic devices, and memory devices. Within analog and power categories, linear ICs and power discretes deliver precision regulation and high-current switching, respectively. Logic device portfolios span microcontrollers that orchestrate embedded systems and microprocessors that handle compute-intensive tasks. Memory segments, encompassing DRAM and flash memory, demand substrates with exceptional defect density control to uphold data integrity. In parallel, solar cells rely on wafers engineered for light absorption efficiency and minimal crystal dislocations to maximize electrical conversion rates.
Doping type introduces another layer of complexity, with N-type and P-type wafers exhibiting divergent conductivity characteristics. N-type substrates, prized for lower initial degradation, are increasingly adopted in high-end solar modules, whereas P-type materials maintain stronghold in certain legacy device lines. Diameter considerations bifurcate the market into 200 mm and 300 mm wafers, the latter enabling higher equipment throughput and lower cost per die for advanced nodes.
Thickness profiles further refine value propositions: standard wafers balance rigidity and yield, thick variants address power device requirements, and thin wafers-available in standard thin and ultra thin-optimize thermal performance and minimize material usage. Finally, resistivity grades map to application sensitivity, with high resistivity supporting RF applications, low resistivity offered in adjacent low and very low tiers for power management, and medium resistivity segmented into medium high and medium low to suit general-purpose logic and analog circuits. Understanding these intersecting dimensions is vital for suppliers to tailor production capacities and for consumers to align procurement with performance and cost targets.
This comprehensive research report categorizes the Semiconductor Monocrystalline Silicon Wafer market into clearly defined segments, providing a detailed analysis of emerging trends and precise revenue forecasts to support strategic decision-making.
- Orientation
- Application
- Doping Type
- Diameter
- Thickness
- Resistivity
Regional Performance Highlights Across Key Geographies
Regional dynamics in the monocrystalline silicon wafer sector reflect a mosaic of technology maturity, policy environments, and consumption drivers. In the Americas, a confluence of automotive electrification and data center proliferation sustains robust wafer demand, while domestic fabrication initiatives benefit from supportive incentives. Supply chain integration with polysilicon producers and toolmakers reinforces the region’s position as a strategic hub for high-volume, advanced-node production.
Across Europe, the Middle East and Africa, collaborative research consortia and green energy mandates fuel wafer consumption for photovoltaic applications. Policies promoting carbon neutrality have catalyzed investments in next-generation solar cells, increasing demand for low-defect substrates. At the same time, semiconductor fabrication facilities in EMEA leverage strong engineering talent pools to pilot specialized wafers for niche high-performance computing and aerospace electronics.
In the Asia-Pacific realm, established manufacturing ecosystems in East Asia continue to dominate wafer output, underpinned by global polysilicon supply chains and cost-effective production capabilities. Emerging markets within South Asia and Southeast Asia are gradually scaling capacity to capture regional demand, particularly for solar cell integration and consumer electronics segments. Government support for ecosystem development and infrastructure modernization remains a key driver of capacity expansions across the region.
This comprehensive research report examines key regions that drive the evolution of the Semiconductor Monocrystalline Silicon Wafer market, offering deep insights into regional trends, growth factors, and industry developments that are influencing market performance.
- Americas
- Europe, Middle East & Africa
- Asia-Pacific
Competitive Landscape and Leading Company Strategies
Leading wafer suppliers have pursued differentiated strategies to solidify market leadership. Key players have invested in next-generation crystal growth technologies to improve yield and wafer uniformity, while forging long-term supply agreements with semiconductor foundries and solar module manufacturers. Capacity expansions in 300 mm facilities, coupled with modular cleanroom upgrades, have positioned these companies to tap into the demand for advanced-node devices without compromising agility.
R&D collaborations with equipment vendors and polysilicon refiners have delivered breakthroughs in impurity control and kerf loss reduction, directly enhancing operational efficiency. Some firms have adopted vertical integration models, acquiring or partnering with ingot-pulling entities to secure feedstock reliability and drive down total cost of ownership. Concurrently, digital transformation initiatives-spanning predictive maintenance, real-time process monitoring, and yield analytics-have emerged as key differentiators in plant performance and customer satisfaction.
As environmental, social and governance considerations converge with regulatory expectations, leading players are committing to renewable energy sourcing and closed-loop water management. These efforts resonate with device manufacturers who prioritize sustainable procurement, reinforcing supplier selection criteria beyond price and delivery metrics. Overall, the competitive landscape reflects a balanced emphasis on technological leadership, operational excellence, and corporate responsibility.
This comprehensive research report delivers an in-depth overview of the principal market players in the Semiconductor Monocrystalline Silicon Wafer market, evaluating their market share, strategic initiatives, and competitive positioning to illuminate the factors shaping the competitive landscape.
- Shin-Etsu Chemical Co., Ltd.
- SUMCO Corporation
- GlobalWafers Co., Ltd.
- Siltronic AG
- SK Siltron Co., Ltd.
- Zhonghuan Semiconductor Co., Ltd.
- Sino-American Silicon Products Inc.
- Wafer Works Corporation
Strategic Imperatives for Decision Makers to Capitalize on Opportunities
Industry leaders should initiate targeted investments in automated process control and advanced metrology to maintain wafer quality at sub-micron tolerances. Diversifying supplier networks through strategic alliances with emerging fabricators can mitigate tariff-induced cost volatility and ensure uninterrupted supply chains. Furthermore, prioritizing the development of ultra thin wafer lines offers a dual advantage of material cost savings and enhanced performance for power devices and advanced logic applications.
Commitment to sustainability will differentiate organizations in a crowded market. Establishing closed-loop water recycling and integrating solar or wind energy into production operations can reduce environmental impact while appealing to customers with rigorous ESG mandates. Simultaneously, embedding predictive analytics within manufacturing execution systems will drive proactive maintenance, minimize unplanned downtime and optimize throughput.
To capitalize on regional growth vectors, decision makers should tailor go-to-market strategies that align with local policy frameworks and ecosystem strengths. Collaborating with government bodies on incentive programs and workforce development can accelerate capacity expansions. Finally, continuous dialogue with end users-device makers and solar module manufacturers-will ensure that wafer specifications evolve in step with application requirements, securing long-term partnerships grounded in mutual innovation.
Robust Methodological Framework Underpinning the Analysis
The insights presented in this summary derive from a rigorous methodology that integrates primary and secondary research. Primary data was collected through in-depth interviews with key stakeholders across the wafer production value chain, including equipment vendors, polysilicon refiners, device manufacturers and industry experts. These qualitative perspectives were cross-verified with secondary sources, such as proprietary databases, trade association reports and peer-reviewed publications, ensuring comprehensive coverage of market trends and technical advancements.
Data triangulation techniques were employed to reconcile disparate inputs and validate findings, while quantitative analysis of production capacity, trade flows and technology adoption provided empirical grounding. Scenario mapping exercises explored potential outcomes of tariff shifts and policy interventions, offering strategic context without projecting explicit numerical forecasts. Finally, our editorial team subjected the compiled research to multiple rounds of peer review, ensuring accuracy, coherence and relevance for decision makers who demand both depth and clarity.
Explore AI-driven insights for the Semiconductor Monocrystalline Silicon Wafer market with ResearchAI on our online platform, providing deeper, data-backed market analysis.
Ask ResearchAI anything
World's First Innovative Al for Market Research
Consolidating Insights and Future Outlook
This executive summary consolidates critical insights on monocrystalline silicon wafers by examining technological advancements, trade policy impacts, segmentation depth, regional dynamics and competitive strategies. The narrative underscores how orientation choices, wafer diameters, thickness profiles and doping types intersect to define performance and cost parameters across integrated circuits and solar applications. Regional analyses illuminate the diverse forces shaping demand in the Americas, EMEA and Asia-Pacific, while corporate case studies reveal how leading suppliers are optimizing capacity, innovation and sustainability.
By mapping the cumulative effects of the 2025 US tariffs, we have highlighted how procurement strategies and supply chain diversification become key differentiators in a shifting trade environment. The methodological rigor ensures that these insights rest on a balanced fusion of expert interviews, data analysis and cross-market validation. Ultimately, informed strategic action-driven by the recommendations herein-will determine which players thrive in a competitive landscape marked by rapid technological change and evolving policy landscapes.
This section provides a structured overview of the report, outlining key chapters and topics covered for easy reference in our Semiconductor Monocrystalline Silicon Wafer market comprehensive research report.
- Preface
- Research Methodology
- Executive Summary
- Market Overview
- Market Dynamics
- Market Insights
- Cumulative Impact of United States Tariffs 2025
- Semiconductor Monocrystalline Silicon Wafer Market, by Orientation
- Semiconductor Monocrystalline Silicon Wafer Market, by Application
- Semiconductor Monocrystalline Silicon Wafer Market, by Doping Type
- Semiconductor Monocrystalline Silicon Wafer Market, by Diameter
- Semiconductor Monocrystalline Silicon Wafer Market, by Thickness
- Semiconductor Monocrystalline Silicon Wafer Market, by Resistivity
- Americas Semiconductor Monocrystalline Silicon Wafer Market
- Europe, Middle East & Africa Semiconductor Monocrystalline Silicon Wafer Market
- Asia-Pacific Semiconductor Monocrystalline Silicon Wafer Market
- Competitive Landscape
- ResearchAI
- ResearchStatistics
- ResearchContacts
- ResearchArticles
- Appendix
- List of Figures [Total: 28]
- List of Tables [Total: 586 ]
Secure Your Comprehensive Market Report from Our Senior Sales Executive
To deepen your strategic understanding and gain a competitive edge, engage with Ketan Rohom, Associate Director, Sales & Marketing at 360iResearch, to secure the full market research report. He will provide personalized insights tailored to your organization’s priorities and guide you through the granular data that underpins this summary. Don’t miss the opportunity to leverage comprehensive analysis, expert commentary, and actionable recommendations that will inform your next moves in the monocrystalline silicon wafer arena. Reach out today to unlock the complete suite of findings and position your team for sustained growth in a rapidly evolving landscape.
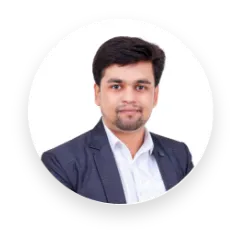
- When do I get the report?
- In what format does this report get delivered to me?
- How long has 360iResearch been around?
- What if I have a question about your reports?
- Can I share this report with my team?
- Can I use your research in my presentation?