Introduction to the Critical Role of Wafer Bonding Equipment
Semiconductor wafer bonding lies at the heart of advanced device fabrication, enabling the integration of dissimilar materials, the assembly of microelectromechanical systems, and the production of high-performance sensors. As device architectures grow increasingly complex, wafer bonding equipment has emerged as a critical enabler of next-generation electronics, driving innovation across automotive, consumer, and industrial applications. Over the past decade, manufacturers have pursued tighter alignment tolerances, enhanced throughput, and improved yield, compelling equipment suppliers to refine bonding techniques and process controls.
The rise of heterogeneous integration, miniaturization, and three-dimensional packaging has elevated bonding from a supporting operation to a strategic differentiator. Investment priorities now emphasize adaptive process stages-from pre-bond inspection and cleaning through post-bond testing-as companies seek to streamline production and reduce defect rates. This executive summary offers an in-depth look at the shifting dynamics of the wafer bonding landscape, examining technology evolution, tariff impacts, market segmentation, regional trends, and leading corporate strategies. Readers will gain actionable insights into how these forces collectively shape supplier decisions and guide capital investments.
Transformative Shifts Redefining the Wafer Bonding Landscape
The wafer bonding landscape is undergoing seismic change, driven by the convergence of automation, advanced process analytics, and material science breakthroughs. Rapid adoption of plasma-assisted and surface-activated bonding methods has enabled finer alignment at lower temperatures, shrinking cycle times and enhancing bond strength. Meanwhile, embedded sensors and real-time monitoring systems leverage machine learning to detect anomalies, adjust force application, and predict maintenance needs, effectively reducing downtime and boosting throughput.
Concurrently, equipment manufacturers are prioritizing modular architectures that accommodate evolving material stacks and heterogeneous substrates. The shift toward single-wafer bonding platforms optimized for automated handling reflects a broader industry push to tailor equipment footprints to fab capacity. As manufacturers embrace Industry 4.0 principles, the integration of digital twins and closed-loop controls transforms wafer bonding from an isolated step into an interconnected process. Stakeholders who harness these innovations position themselves to lead in an environment where precision, flexibility, and data-driven optimization are paramount.
Assessing the 2025 Tariff Impact on Wafer Bonding Supply Chains
The introduction of new tariffs in 2025 has exerted multifaceted pressures on the semiconductor wafer bonding ecosystem. Raw material surcharges have elevated the cost of specialty glasses and advanced polymers used in adhesive and anodic bonding processes. Equipment suppliers face margin compression as they absorb duties or pass increases on to customers, compelling them to revisit supply agreements and reassess component sourcing strategies.
Manufacturers have responded by exploring alternative materials and regional supply networks to counterbalance tariff burdens. Some industry leaders are relocating key assembly lines to mitigate duty exposure, while others negotiate long-term contracts to secure price stability. The cumulative effect has been a recalibration of procurement policies, with buyers prioritizing partners who demonstrate resilient logistics capabilities and transparent cost structures. As the tariff environment evolves, companies that proactively diversify their vendor base and optimize their global footprint will maintain competitiveness in wafer bonding operations.
Unveiling Critical Segmentation Perspectives for Wafer Bonding Success
A nuanced understanding of technology segmentation illuminates the competitive terrain of wafer bonding solutions. Within adhesive bonding, the choice between epoxy and polyimide compounds affects thermal stability and die shear strength, while anodic bonding with borosilicate glass and silicon optimizes electrostatic adhesion for sensor packages. Direct bonding implementations, ranging from plasma-assisted to surface-activated approaches, cater to low-temperature requirements in advanced photonic devices. Eutectic processes employing aluminum-silicon or gold-silicon alloys facilitate robust electrical interconnects, and solder bonding leveraging tin-lead or tin-silver formulations ensures reliable joints for power modules.
Equipment formats also vary significantly. Batch wafer furnaces-both horizontal and vertical-serve high-volume production demands, whereas single-wafer platforms, whether automated or manually operated, offer tighter process control for specialized applications. Across these equipment types, manufacturers tailor end-effectors and handling protocols to maintain contamination thresholds and alignment precision.
Applications span image sensors, where CCD and CMOS variants drive imaging performance, to MEMS devices such as accelerometers, gyroscopes, and pressure sensors. In power electronics, wafer bonding underpins IGBT and MOSFET fabrication, while RF amplifiers and filters benefit from high-fidelity package interfaces. End-user segments include foundries that demand scale, integrated device manufacturers seeking turnkey solutions, and original equipment manufacturers focused on customized assembly. Throughout the production lifecycle, process stages-from bond formation and force application through temperature cycling-intersect with cleaning operations, including chemical and plasma methods, and rigorous pre- and post-bond inspections such as alignment verification, surface topography analysis, leak testing, and shear testing. This multilayered segmentation framework highlights the interdependencies between technology, equipment, application, and process parameters that define bonding excellence.
This comprehensive research report categorizes the Semiconductor Wafer Bonding Equipment market into clearly defined segments, providing a detailed analysis of emerging trends and precise revenue forecasts to support strategic decision-making.
- Technology
- Equipment Type
- Application
- End User
- Process Stage
Decoding Regional Dynamics Influencing Wafer Bonding Demand
Regional dynamics shape the evolution of wafer bonding equipment demand and investment strategies. In the Americas, advanced packaging initiatives and automotive electrification drive demand for high-volume batch bonding systems, while a growing focus on MEMS fosters partnerships between equipment suppliers and automotive Tier 1 integrators. Europe, Middle East & Africa exhibits strong interest in heterogeneous integration and photonics, as research institutions and specialized foundries collaborate on compound semiconductor projects, prompting a surge in flexible single-wafer platforms. Asia-Pacific remains the epicenter of capacity expansion, where aggressive capital deployments by IDM players and foundries fuel orders for both horizontal furnace clusters and fully automated single-wafer lines.
Supply chain resilience has become a top priority across all regions, prompting cross-border alliances and localized service networks. As geopolitical considerations influence material flow and equipment delivery, regional stakeholders who secure strategic inventory buffers and cultivate local talent pools position themselves to adapt swiftly to shifting demand patterns.
This comprehensive research report examines key regions that drive the evolution of the Semiconductor Wafer Bonding Equipment market, offering deep insights into regional trends, growth factors, and industry developments that are influencing market performance.
- Americas
- Europe, Middle East & Africa
- Asia-Pacific
Insights into Leading Players Driving Equipment Innovation
Leading equipment suppliers have differentiated themselves through targeted technology roadmaps and strategic alliances. EV Group continues to advance wafer bonding optics with precision alignment modules and expanded cleanroom offerings, while SUSS MicroTec enhances its portfolio with plasma-based bonding solutions optimized for low-temperature substrates. Tokyo Electron leverages its semiconductor heritage to integrate bonding modules into broader cluster tools, and Kokusai Electric focuses on high-reliability systems for RF and power device assembly.
Other notable players are investing in artificial intelligence for predictive maintenance and yield enhancement, forging partnerships with materials experts to co-develop next-generation adhesives and eutectic alloys. These collaborations underscore a broader industry trend toward co-innovation, with equipment suppliers and end users working in concert to achieve superior bond quality, process repeatability, and throughput efficiencies.
This comprehensive research report delivers an in-depth overview of the principal market players in the Semiconductor Wafer Bonding Equipment market, evaluating their market share, strategic initiatives, and competitive positioning to illuminate the factors shaping the competitive landscape.
- EV Group Austria GmbH
- SUSS MicroTec AG
- Tokyo Electron Limited
- Applied Materials, Inc.
- ASM International N.V.
- Canon Inc.
- DISCO Corporation
- ULVAC, Inc.
- Meyer Burger Technology AG
- Palomar Technologies, Inc.
Strategic Actions for Maximizing Wafer Bonding Competitiveness
Industry leaders should prioritize the adoption of modular, upgradeable platforms that accommodate emerging materials and process variations. By integrating in-line metrology and real-time analytics, manufacturers can detect subtle deviations in bond integrity and implement corrective actions before throughput losses occur. Securing diversified raw material suppliers across multiple geographies will mitigate tariff exposure and supply chain disruptions.
Additionally, fostering collaborative R&D partnerships with semiconductor fabs, MEMS designers, and materials scientists will accelerate the validation of novel bonding chemistries and eutectic alloys. A focused investment in workforce training ensures operators can navigate increasingly automated, data-centric systems. Finally, aligning capital expenditure with market segments poised for high growth-such as photonic integration and advanced packaging-will optimize ROI and reinforce competitive advantages.
Methodical Research Approach Underpinning Market Insights
This analysis draws upon both primary interviews with equipment engineers, process architects, and fab managers, and secondary research encompassing industry white papers, technical journals, and financial reports. Data triangulation involved cross-referencing supplier shipment records, published patent filings, and tariff documentation to validate cost impacts and technology adoption rates.
Expert surveys provided insights into emerging material preferences, while on-site visits to leading fabs offered real-world observations of equipment performance and production workflows. The segmentation framework was refined through iterative feedback sessions, ensuring alignment with current manufacturing practices. Throughout the research process, quality control measures-such as peer reviews and data consistency checks-were applied to uphold methodological rigor and deliver actionable intelligence.
Explore AI-driven insights for the Semiconductor Wafer Bonding Equipment market with ResearchAI on our online platform, providing deeper, data-backed market analysis.
Ask ResearchAI anything
World's First Innovative Al for Market Research
Concluding Perspectives on the Future of Wafer Bonding Equipment
Semiconductor wafer bonding equipment occupies a pivotal position in the semiconductor value chain, enabling the assembly of increasingly complex devices that power modern electronics. The confluence of advanced bonding technologies, geopolitical influences, and regional investment strategies underscores a dynamic environment ripe with opportunity and challenge.
By synthesizing segmentation insights, tariff effects, and competitive strategies, this executive summary equips stakeholders with a comprehensive perspective on market drivers and technological imperatives. As the industry advances toward higher precision, greater integration, and resilient supply chains, the stakeholders best poised to lead will be those who embrace innovation, collaboration, and strategic foresight.
This section provides a structured overview of the report, outlining key chapters and topics covered for easy reference in our Semiconductor Wafer Bonding Equipment market comprehensive research report.
- Preface
- Research Methodology
- Executive Summary
- Market Overview
- Market Dynamics
- Market Insights
- Cumulative Impact of United States Tariffs 2025
- Semiconductor Wafer Bonding Equipment Market, by Technology
- Semiconductor Wafer Bonding Equipment Market, by Equipment Type
- Semiconductor Wafer Bonding Equipment Market, by Application
- Semiconductor Wafer Bonding Equipment Market, by End User
- Semiconductor Wafer Bonding Equipment Market, by Process Stage
- Americas Semiconductor Wafer Bonding Equipment Market
- Europe, Middle East & Africa Semiconductor Wafer Bonding Equipment Market
- Asia-Pacific Semiconductor Wafer Bonding Equipment Market
- Competitive Landscape
- ResearchAI
- ResearchStatistics
- ResearchContacts
- ResearchArticles
- Appendix
- List of Figures [Total: 26]
- List of Tables [Total: 900 ]
Contact Ketan Rohom to Secure Your Comprehensive Wafer Bonding Market Report
Discover how this comprehensive analysis can drive your strategic decisions in wafer bonding technology by engaging directly with Ketan Rohom, Associate Director, Sales & Marketing. Reach out to schedule a personalized consultation and explore tailored solutions that align with your business objectives. Secure access to the full market research report today and stay ahead of industry trends by connecting with the authoring specialist.
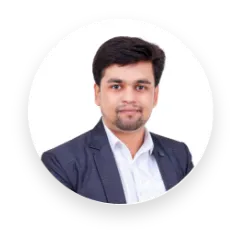
- When do I get the report?
- In what format does this report get delivered to me?
- How long has 360iResearch been around?
- What if I have a question about your reports?
- Can I share this report with my team?
- Can I use your research in my presentation?