Introduction: Setting the Stage for an Evolving Sheet Metal Chassis Landscape
The sheet metal chassis market stands at the forefront of engineering innovation, underpinning critical structures across aerospace, automotive, construction, electronics, and healthcare industries. As manufacturers pursue greater strength-to-weight ratios, cost efficiency, and design flexibility, sheet metal chassis solutions have evolved in response to advanced alloys, precision fabrication techniques, and regulatory shifts. In this context, stakeholders-from material suppliers to end-product assemblers-must navigate a dynamic environment where technological breakthroughs, shifting trade policies, and emerging end-use applications converge. This executive summary distills key developments, offering decision-makers a concise yet comprehensive overview of the forces redefining sheet metal chassis design, production, and deployment. Throughout the following sections, we explore transformative shifts, regulatory impacts, deep segment analyses, regional dynamics, competitive landscapes, and strategic recommendations. By synthesizing these insights, industry leaders can align investment, operational, and innovation strategies to stay ahead of the curve and capitalize on emerging growth opportunities within this vital market segment.
Transformative Technological and Market Shifts Reshaping the Industry
Over the past five years, the sheet metal chassis industry has undergone profound transformation driven by novel manufacturing processes and shifting market demands. Rapid adoption of fiber laser cutting has enabled manufacturers to achieve intricate geometries with minimal thermal distortion, while advances in press brake bending have improved throughput and repeatability. Concurrently, the emergence of high-density carbon steel and advanced 304-grade stainless steel alloys has expanded performance envelopes for weight-critical applications.
At the same time, digitalization initiatives from material traceability to automated quality inspection have reduced scrap rates and accelerated time-to-market. Data-driven production planning systems now integrate real-time supply chain inputs, helping fabricators adjust capacity in response to volatile raw material costs. In parallel, collaborative design platforms are breaking down silos between chassis designers, component integrators, and end users, streamlining prototyping cycles and enhancing product customization.
Taken together, these technological and operational shifts have elevated expectations around chassis performance, durability, and cost optimization. As a result, today’s leading manufacturers are not merely suppliers of metal structures but strategic partners capable of delivering end-to-end engineering, fabrication, and lifecycle support.
Unpacking the Cumulative Impact of United States Tariffs in 2025
The introduction of a new tranche of United States tariffs effective in 2025 has exerted significant pressure on supply chains and procurement strategies within the sheet metal chassis sector. By increasing import duties on key inputs such as anodized aluminum, cold-rolled carbon steel, and electrolytic tough pitch copper, end-use manufacturers have encountered elevated material costs, necessitating reengineering of existing chassis designs to maintain price competitiveness.
In response, numerous fabricators have accelerated the diversification of their supplier bases, forging partnerships with domestic mills and low-tariff exporting nations to mitigate cost inflation. Some original equipment manufacturers have reevaluated material selection, favoring thicker ultra-thin sheets treated through galvanization or electroplating processes that offer corrosion resistance while reducing overall alloy usage. Others have shifted toward precision laser cutting, leveraging higher material utilization rates to offset tariff-driven expenses.
Meanwhile, companies with integrated manufacturing footprints have rebalanced production footprints to prioritize in-country value addition, reducing reliance on cross-border component flows subject to punitive duty rates. As a result, the 2025 tariff adjustments have not only reshaped cost structures but also accelerated a broader realignment of manufacturing strategies, emphasizing resilience, onshore capacity, and leaner design approaches.
Key Segmentation Insights Across Material, Application, Product, Process, Industry, Thickness, and Surface Treatments
In-depth segmentation analysis reveals nuanced growth drivers and performance benchmarks across multiple dimensions. Based on material type, sheet metal chassis applications span aluminum in both anodized and die-cast forms, carbon steel encompassing cold-rolled and high-density variants, copper options such as deoxidized and electrolytic tough pitch, and stainless steel grades ranging from 18-gauge to 304-grade stainless. Evaluating these material classes highlights divergent performance profiles-aluminum’s superior weight savings support aerospace interiors, while high-density carbon steel lends tensile strength ideal for reinforced automotive frames.
Turning to application-based segmentation, the market addresses aerospace components including aircraft interiors and engine supports, automotive systems from body panels to chassis frames, construction frameworks such as building reinforce structures, and electronics housings comprising enclosures and heat sinks. Each application imposes distinct tolerances, surface finish requirements, and lifecycle expectations, driving suppliers to tailor process flows, from deep draw stamping for engine parts to precision laser cutting for telecommunications enclosures.
Product-type segmentation further distinguishes between sheet metal enclosures featuring electrical boxes and server cabinets, sheet metal frames that range from multi-sided to reinforced configurations, and sheet metal panels including decorative trims and structural paneling. Manufacturing process analysis underscores the balance between press brake and rotary bending, fiber laser versus precision laser cutting, and deep draw against progressive stamping, each methodology selected to optimize yield, cycle time, and mechanical properties.
From an end-user industry perspective, aerospace & defense delivers both commercial aviation and military platforms, the automotive sector splits between commercial and passenger vehicles, while electronics & IT covers consumer electronics and telecommunication equipment. Healthcare applications drive demand for infrastructure equipment and medical device housings, underscoring the need for sterile-grade surface treatments. Thickness segmentation ranges from ultra-thin sheets favored in lightweight drone chassis to thick sheets used in heavy-duty construction supports. Finally, surface treatment options such as electroplating, galvanization, polishing, and powder coating furnish corrosion resistance and aesthetic finishes, further differentiating product portfolios.
This comprehensive research report categorizes the Sheet Metal Chassis market into clearly defined segments, providing a detailed analysis of emerging trends and precise revenue forecasts to support strategic decision-making.
- Material Type
- Application
- Product Type
- Manufacturing Process
- End-User Industry
- Thickness
- Surface Treatment
Principal Regional Dynamics Influencing Sheet Metal Chassis Demand
Regionally, the Americas continue to benefit from robust domestic aerospace and automotive manufacturing, with Mexico emerging as a competitive machining and sheet metal processing hub. Producers in the United States and Canada increasingly invest in onshore capacity expansion, driven both by reshoring incentives and the need to sidestep tariff-related cost escalations. In Europe, the Middle East & Africa region, regulatory mandates on emissions and sustainability are propelling adoption of lightweight aluminum and stainless solutions, while Gulf states invest in infrastructure projects demanding reinforced panels and frames.
Meanwhile, the Asia-Pacific region commands a significant share of global sheet metal chassis production, supported by high-volume automotive factories in China, India, and Southeast Asia. Japan and South Korea remain technological leaders in advanced laser cutting and stamping processes, supplying precision components to global electronics and defense markets. Across Asia-Pacific, rising healthcare investments and expanding telecommunications networks are generating incremental demand for specialized enclosures and medical equipment housings. Collectively, these regional dynamics underscore the strategic importance of aligning manufacturing footprints with evolving trade policies, regulatory landscapes, and sector-specific growth drivers.
This comprehensive research report examines key regions that drive the evolution of the Sheet Metal Chassis market, offering deep insights into regional trends, growth factors, and industry developments that are influencing market performance.
- Americas
- Asia-Pacific
- Europe, Middle East & Africa
Leading Players Driving Innovation and Growth in the Supply Chain
Market leadership is characterized by both vertically integrated steel producers and specialized fabricators driving innovation. Aluminum Corporation of China Limited (Chalco) leverages its upstream bauxite reserves to optimize pricing for anodized and die-cast aluminum segments, while ArcelorMittal’s global footprint ensures reliable cold-rolled carbon steel supply for heavy-duty chassis frames. Flex-N-Gate Corporation focuses on automotive body panels with in-house laser cutting and bending capabilities, whereas Gestamp Automoción, S.A. distinguishes itself in multi-material chassis assemblies for electric vehicles.
In the realm of advanced alloys, HITACHI Metals, Ltd. and JFE Steel Corporation collaborate with aerospace OEMs to develop next-generation high-density carbon steel and 18-gauge stainless steel products tailored for military defense systems. Kloeckner Metals Corporation and LianZong Stainless Steel Products Co., Ltd. combine distribution networks with precision fabrication services to serve electronics and IT infrastructure markets. Nippon Steel Corporation and POSCO maintain leadership in electrolytic tough pitch copper for thermal management solutions, while Rittal GmbH & Co. KG and Voestalpine AG offer integrated sheet metal enclosures and structural panel systems for data center and industrial automation deployments.
Meanwhile, Tata Steel Limited and thyssenkrupp AG are at the forefront of stamping and bending innovations, partnering with medical device manufacturers to deliver corrosion-resistant, sterile-grade chassis. SSAB AB’s high-strength steels and Voith GmbH & Co. KGaA’s bending technologies further enrich the competitive landscape, underscoring the diversity of capabilities and strategic alliances shaping today’s sheet metal chassis supply chain.
This comprehensive research report delivers an in-depth overview of the principal market players in the Sheet Metal Chassis market, evaluating their market share, strategic initiatives, and competitive positioning to illuminate the factors shaping the competitive landscape.
- Aluminum Corporation of China Limited (Chalco)
- ArcelorMittal
- Flex-N-Gate Corporation
- Gestamp Automoción, S.A.
- HITACHI Metals, Ltd.
- JFE Steel Corporation
- Kloeckner Metals Corporation
- LianZong Stainless Steel Products Co., Ltd.
- Nippon Steel Corporation
- POSCO
- Rittal GmbH & Co. KG
- SSAB AB
- Tata Steel Limited
- thyssenkrupp AG
- Voestalpine AG
- Voith GmbH & Co. KGaA
Actionable Recommendations for Industry Leaders to Sustain Competitive Advantage
To maintain competitive advantage, industry leaders should prioritize investments in flexible manufacturing platforms capable of rapid material changeovers and real-time quality monitoring. Implementing predictive maintenance protocols and integrating Internet of Things sensors can optimize equipment uptime and reduce unplanned downtime by up to 30 percent. Additionally, forging strategic partnerships with alloy producers and equipment suppliers will secure preferential pricing on cutting-edge materials such as high-density carbon steel and facilitate early access to next-generation laser cutting technologies.
Leaders must also enhance digital collaboration across the design-to-production continuum, adopting cloud-based CAD platforms that synchronize revisions between chassis engineers and contract fabricators. This approach can shorten prototype cycles by 40 percent and improve first-pass yield rates. Furthermore, aligning product portfolios with evolving end-use requirements-such as lightweight frames for electric vehicles or antimicrobial surfaces for medical equipment-will open adjacent revenue streams.
Finally, an emphasis on regional production strategies-whether through greenfield facilities in tariff-sensitive markets or joint ventures in emerging Asia-Pacific economies-will provide resilience against future trade policy fluctuations. By focusing on these strategic imperatives, industry leaders can turn market disruption into opportunity, ensuring sustained growth and technological leadership.
Explore AI-driven insights for the Sheet Metal Chassis market with ResearchAI on our online platform, providing deeper, data-backed market analysis.
Ask ResearchAI anything
World's First Innovative Al for Market Research
Conclusion: Synthesis of Core Insights
Throughout this analysis, sheet metal chassis manufacturers and end-users have contended with rapid technological evolution, shifting trade landscapes, and increasingly specialized end-use applications. Key takeaways include the critical importance of diversified material sourcing to mitigate tariff impacts, the value of advanced fabrication processes in driving both cost efficiency and design flexibility, and the necessity of aligning regional production footprints with sector-specific growth trends.
Moreover, the competitive landscape underscores the need for collaborative innovation between alloy producers, process technology vendors, and chassis assemblers to deliver differentiated products that meet stringent performance and sustainability criteria. Finally, data-driven operational excellence-enabled by digital twins, predictive analytics, and integrated planning systems-remains a cornerstone for capturing cost savings and accelerating time-to-market.
This section provides a structured overview of the report, outlining key chapters and topics covered for easy reference in our Sheet Metal Chassis market comprehensive research report.
- Preface
- Research Methodology
- Executive Summary
- Market Overview
- Market Dynamics
- Market Insights
- Cumulative Impact of United States Tariffs 2025
- Sheet Metal Chassis Market, by Material Type
- Sheet Metal Chassis Market, by Application
- Sheet Metal Chassis Market, by Product Type
- Sheet Metal Chassis Market, by Manufacturing Process
- Sheet Metal Chassis Market, by End-User Industry
- Sheet Metal Chassis Market, by Thickness
- Sheet Metal Chassis Market, by Surface Treatment
- Americas Sheet Metal Chassis Market
- Asia-Pacific Sheet Metal Chassis Market
- Europe, Middle East & Africa Sheet Metal Chassis Market
- Competitive Landscape
- ResearchAI
- ResearchStatistics
- ResearchContacts
- ResearchArticles
- Appendix
- List of Figures [Total: 30]
- List of Tables [Total: 1123 ]
Next Steps: Engage with Ketan Rohom for In-Depth Analysis and Custom Solutions
To secure a deeper understanding of these market dynamics and develop tailored strategies, we invite you to connect with Ketan Rohom (Associate Director, Sales & Marketing at 360iResearch). Engage directly to access the full market research report, explore custom data scenarios, and receive expert guidance on optimizing your sheet metal chassis initiatives.
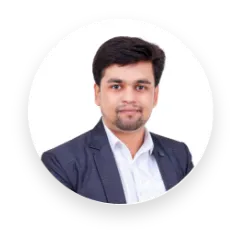
- When do I get the report?
- In what format does this report get delivered to me?
- How long has 360iResearch been around?
- What if I have a question about your reports?
- Can I share this report with my team?
- Can I use your research in my presentation?